The weathering of volcanic ash results in the formation of the clay substance known as bentonite, a key material extensively used in construction, especially in Bentonite Slurry in Pile Foundations. They are taken out of the quarry and ground into a fine powder. Bentonite is the name given to a variety of clays that, when combined with water, can swell and gel. When bentonite and water are combined, it forms a gel under static conditions but returns to its fluid state when disturbed or upset.
When bentonite and water are combined, it forms a gel under static conditions but returns to its fluid state when disturbed or upset. A slurry is a fluid mixture of crushed material with water that is used frequently as a practical method of managing particles in bulk. It can be thin, sloppy, made out of cement or mud. This combination is typically used to create a sturdy ground barrier for protection. This is also used for building specific foundations comprising of Bored Piles and digging diaphragm walls. Utilizing bentonite allows self-hardening mixtures, which are then used to construct cut-off walls, grouting mortars, and grouting. The waterproofing capabilities of bentonite are best utilized in environmental engineering to line landfill bases and seal off soil infiltrations. Bentonite is a naturally occurring mineral known as sodium montmorillonite, demonstrating thixotropic qualities. Sodium bentonite, Calcium bentonite, and Potassium bentonite are the three different varieties of bentonite. Sodium bentonite is utilized in Pile foundation work in the building sector.
Use of Bentonite Slurry in Pile Foundation
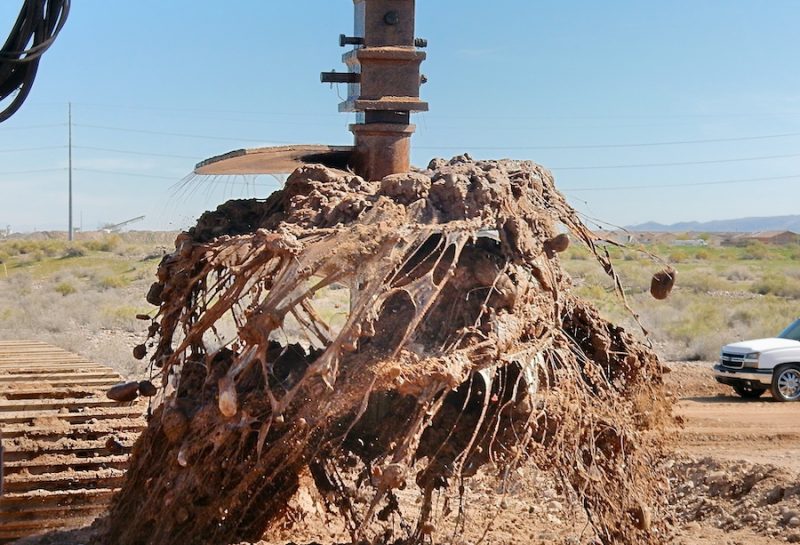
Bentonite has a great capacity to absorb water. After absorbing water, it expands significantly, approximately eight times its original volume.
The thixotropic characteristic of sodium bentonite makes it appropriate for soil stabilization activities. Because of the electrically charged ions in the bentonite slurry’s cations (Na+), the boring soil surface is stabilized. Therefore, bentonite slurry is utilized to a greater extent to prevent the collapse of the dirt in the pile bore.
Bentonite slurry is used in pile foundations and diaphragm walling, where it is referred to as drilling mud, lining tube, or excavation supporting slurry. These terms refer to the same material because of their similarity. In the case of bored cast in-situ piles, fine-grained soil that cannot stand on its own until a temporary steel tube liner is placed down the finished hole, a necessary requirement for the successful piling procedure.
However, bentonite slurry is to be employed as a stabilizing suspension or drilling mud in the case of granular soil or to make excavation more affordable by avoiding the excessive usage of steel liners.
Properties of Bentonite Slurry
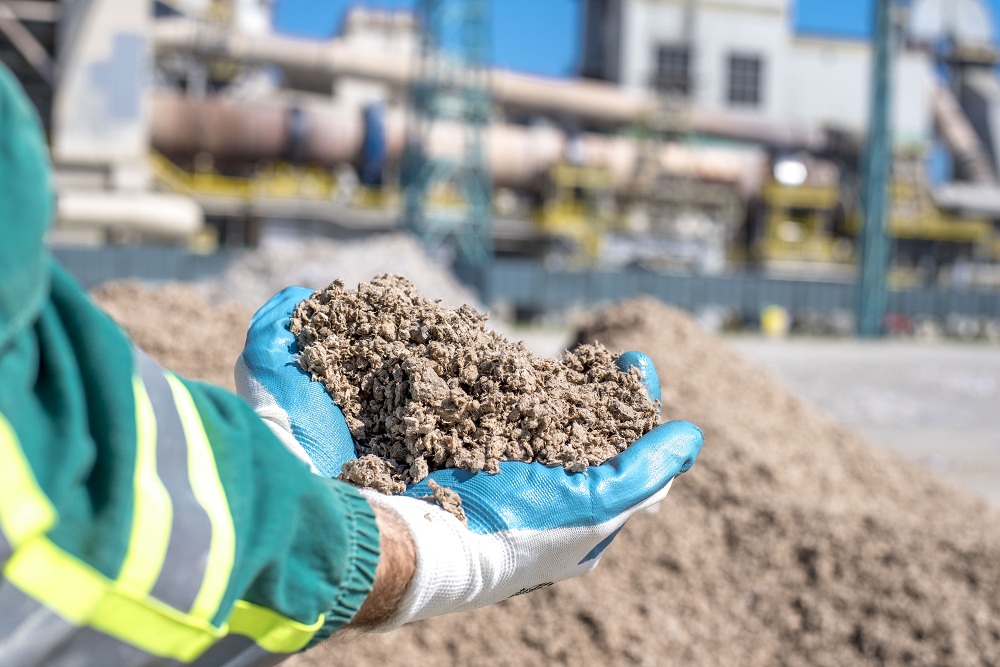
Since the goal of bentonite slurry development is to achieve maximal bentonite hydration, the powder must be added to the water mixture gradually. To ensure that all of the particles get irrigated and do not collect into partially hydrated balls. To achieve the greatest results, only freshwater of potable grade should be utilized during the mixing process. If there is any uncertainty, a chemical study should be performed to determine the water’s compatibility. The water is given a chemical treatment if necessary before being used. Some properties of bentonite slurry are:
- It maintains the excavation by applying hydrostatic pressure to the walls of the excavation, preventing collapse or holding a portion in place.
- When it doesn’t significantly flow into the soil and stays in the excavation, it acts as a sealant.
- It holds back trash and stops sluggish layers from accumulating near the excavation’s bottom.
- Maintaining its non-reactive state through clean displacement by the concrete, with minimal disturbance to the link between the reinforcement and the hardened concrete.
- In order to prepare for reuse, cleaning is done to remove suspended debris by running through screens and hydro cyclones.
- It must be simple to pump bentonite slurry.
Specifications of Bentonite Slurry
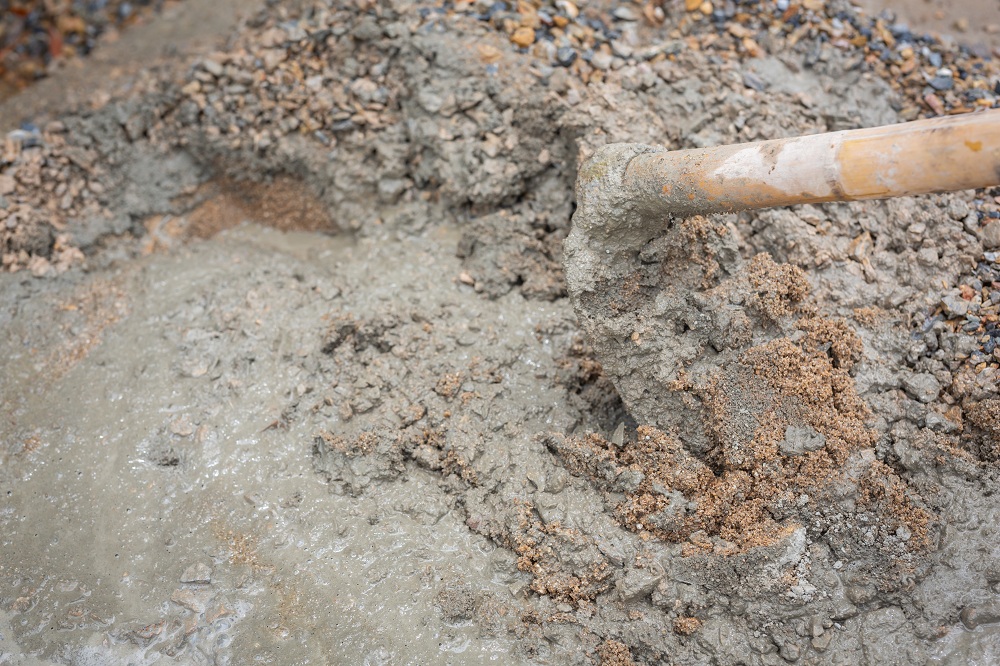
Lab Tests
- Swelling Index: 100% or higher during the course of 12 hours.
- Liquid Limit: Greater than 300% but less than 450%
- Sand content: Less than 7%
- Silt content: Less than 1%
Field Tests
- Marsh viscosity: ranges from 30 to 40 seconds.
- The pH: ranges from 9 to 12.
- Slurry density: 1.05-1.12 gm/cc.
Preparation of Bentonite Slurry
The goal when creating a bentonite slurry is to hydrate the bentonite to its fullest potential. To get the greatest results, only use fresh water of potable grade that is drawn from a mains supply. The manufacture of bentonite slurry shouldn’t utilize salt water because there isn’t a straightforward chemical process to get rid of sodium chloride. Although it is relatively easy to chemically remove calcium and magnesium before using the water, their presence in freshwater will prevent the bentonite powder from dispersing. Soda ash, or sodium carbonate, can be used to remove calcium by precipitating it out as calcium carbonate.
Depending on the equipment being utilized, bentonite slurry can be produced either in batches or continuously. To ensure that all the particles are wetted and do not clump into partially hydrated balls, the bentonite powder must be added to the mixing water gradually. Normally, the bentonite powder is put into a high-shear mixer or by a straight forward venturi hopper. To guarantee that all of the individual bentonite particles are distributed throughout the mixing water, the mixing apparatus must produce an adequate amount of shear. The quality of the bentonite and the necessary slurry viscosity will determine how much bentonite powder should be added to the mixing water. Concentrations between 4% and 6% by weight are typical for most applications.
Bentonite Slurry Usage Arrangements For Pile Foundation
01. Bentonite Pit
A temporary bentonite pit of the right size is dug beside the pile bore, and a vertical pump is installed in it.
02. Bentonite Feed Tank
The storage of new and recovered bentonite slurry is allowed in a bentonite feed tank that is situated close to the pit.
03. Temporary Channel
Numerous soil-filled sacks or sandbags are joined to build a temporary wall and channel around the pile bore in the shape of a tiny cofferdam. This barrier will route the bentonite and mud combination that emerges from the bore during the piling operation toward the bentonite pit. The slurry of mud and bentonite would be pumped to the recovery tank for any necessary desilting using the vertical pump in the bentonite pit.
04. Recovery Tank
Both the bentonite pit and the bentonite feed storage tank are connected to this tank. When bentonite needs to be designed for reuse, it is pumped from the bentonite pit to the recovery tank, where it is recovered and then moved to the bentonite storage tank.
To eliminate soil fragments, the slurry-soil combination that is discharged from the borehole is allowed to settle in lagoons or tanks.
05. Location of Tank
The placement of the bentonite storage and recovery tanks was chosen with consideration for its frequent and effective use. It is advised that tanks be positioned so that they can support a minimum of four pile foundation placements on either side.
06. Supply of Bentonite During Drilling
When drilling pile boreholes through sands and gravels to reach deeper into hard, fine-grained soils, bentonite slurry is employed in a straight forward manner together with rotary auger equipment.
Without assistance, a hole must be augered through the sands and gravels before the casing can be lowered.
07. Flushing
The bentonite is flushed concurrently with drilling operations to keep the suspension’s specific gravity within the range of 1.05 and 1.12. The borehole is thoroughly cleansed to get rid of all the contaminants when the auger or chisel is removed.
08. Reinforcement and Concrete
A reinforcing cage is then swiftly lowered while keeping an eye on the pile borehole’s centerline and verticality.
Concrete is ultimately poured using the tremie method. Since upper part of pile concrete get easily mixed with bentonite, it is considered weak in strength and therefore, it is chipped off till the cut-off level of the pile.
Conclusion
In conclusion, Bentonite Slurry plays a crucial role in pile foundation construction, providing soil stabilization, excavation support, and a reliable barrier against collapse. Its ability to absorb water and swell, coupled with proper preparation and management, ensures the stability and durability of pile foundations. Bentonite slurry is an invaluable tool in the construction industry, contributing to the successful completion of strong and long-lasting structures.
Also check out interesting blog on Foundation Method:
All about Underpinning Foundation Method
Image Courtesy: Image 2
Author Bio
Sabina –