Power tools are essential in any DIY setup. When a tool starts acting up, knowing how to fix it can save you time, money, and hassle. If you’ve heard that “the carbon brushes might be worn out,” this might initially sound like a minor issue, but it’s actually quite central to the health and power of your gear. Let’s look at how these carbon brushes in power tools work and why they’re essential for keeping your equipment in top shape.
What are Carbon Brushes in Power Tools and Why are They Important?
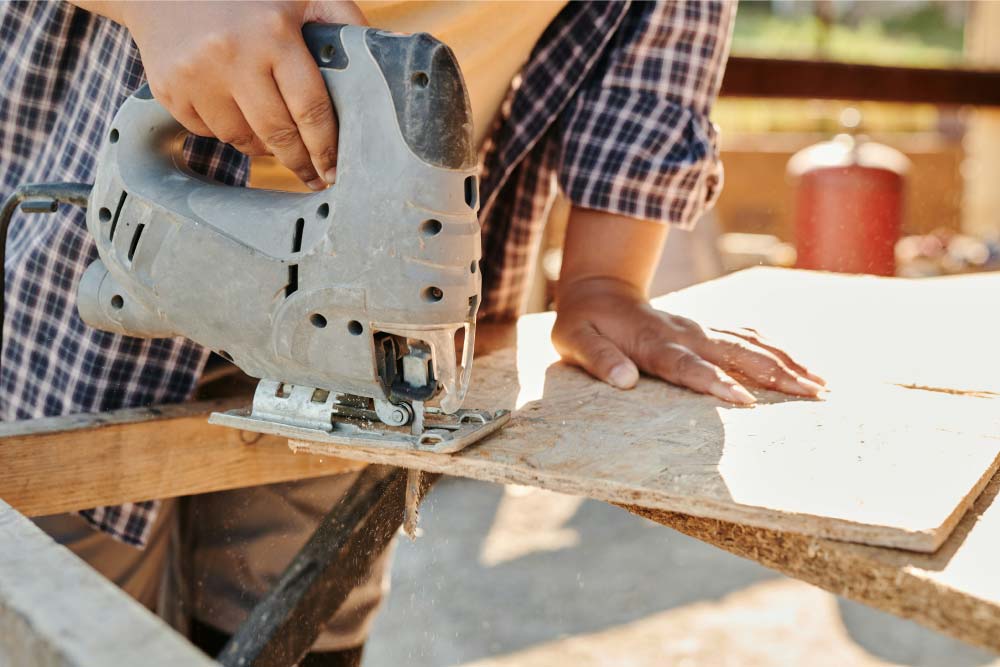
Carbon brushes might be small, but they’re essential in transferring the electricity needed to keep your tools working at peak power.
These components, made of a carbon and graphite blend, allow for consistent wear over time without damaging other motor parts.
Unlike harder materials such as metal, which could grind down essential motor parts, carbon wears gradually, preserving the motor’s integrity.
How Carbon Brushes in Power Tools Work?
Carbon brushes conduct electricity by maintaining constant contact with a rotating motor part called the commutator. As the motor spins, these brushes continuously press against the commutator, allowing a steady flow of electrical current. Without a solid connection, that power flow stutters, which translates to reduced speed, lower torque, or even a complete power loss. Think of carbon brushes as essential “transmitters” that keep energy flowing smoothly to maintain performance.
Pro Tip: Because carbon is a relatively soft material, it’s helpful to periodically check both the brushes and the commutator. Look for signs of wear or buildup on the commutator, which can be gently cleaned to improve performance further.
Takeaway: Carbon brushes enable consistent electrical flow by maintaining a steady connection with the motor’s moving parts, vital for uninterrupted power and performance.
Need more info? Top Deals Online are the experts on carbon brushes; click here to visit their site.
How do Carbon Brushes Wear Out, and How Can You Make Them Last Longer?

Friction between the brush and the commutator is what eventually wears down carbon brushes.
While wear is inevitable, its rate depends on factors like tool type, frequency of use, and even the pressure applied during use.
High-speed equipment like angle grinders or powerful drills generates a lot of heat, which speeds up brush wear. Using a tool continuously without breaks compounds this issue, leading to faster degradation.
Extending Brush Life: Practical Tips
- Allow for Rest Periods: Giving your tool occasional breaks helps manage heat, which can extend the life of the brushes.
- Limit High-Speed Operation: Avoid unnecessary high-speed operation; match the tool speed to the job’s requirements.
- Control Speed Settings: In tools with adjustable speed, try to avoid running at maximum speed constantly, this decreases friction, minimizes heat buildup, and reduces overall wear on the brushes.
Pro Tip: For frequently used power tools, it’s smart to schedule regular checks every three to six months. Remove and inspect the brushes to gauge wear levels. Some carbon brushes even have “wear lines” or indicators to show when it’s time for a replacement (source).
Takeaway: Simple adjustments to usage habits, such as limiting high-speed runs and taking breaks, can help prolong the life of your brushes and reduce the frequency of replacements.
Recognizing the Signs of Worn Carbon Brushes and How to Diagnose Issues with Confidence
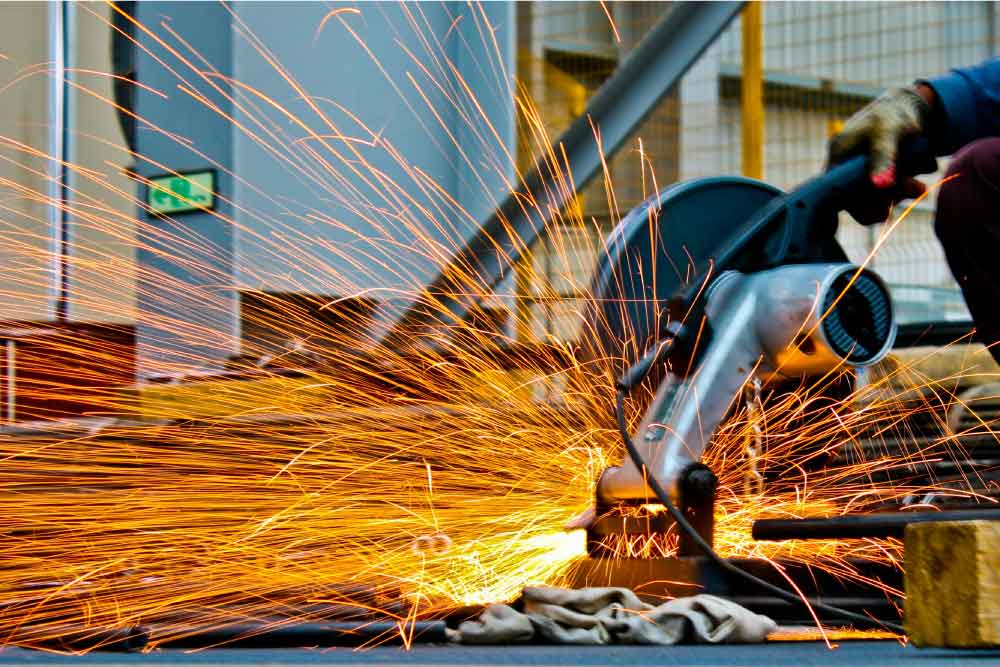
When your tool starts to misbehave, it’s easy to assume age is the cause or that it’s time for a replacement.
However, worn brushes are a common culprit, and recognizing the signs can save you from buying a whole new tool.
Reduced power output, overheating, and unusual noises often signal that the brushes may be failing. But how do you diagnose this confidently?
Expert Diagnosis Techniques
- Listen Closely to the Tool: Worn brushes can create a distinct, irregular “sputtering” sound as they struggle to maintain contact with the commutator. This noise, paired with frequent “power drops” (where the tool cuts in and out), is a clear indicator of brush wear.
- Check for Overheating: Overheating also points to worn brushes. If the tool feels hot after short use, this could mean the motor is straining due to poor electrical connectivity.
- Visually Inspect the Brushes: If possible, disassemble the tool’s housing to inspect the brushes. If the brush has worn down to a stub, that’s a clear sign it needs replacement. Brushes in poor condition may look rough, uneven, or even burnt (source).
- Inspect the Commutator: Don’t overlook the commutator; signs of burnt or scorched spots suggest poor contact and may require cleaning to restore a solid connection.
Pro Tip: Keep an ear out for any loud sparking sounds or visible sparking inside the motor housing. Occasional small sparks are normal, but consistent, bright sparks can indicate severely worn brushes that need immediate attention.
Takeaway: Observing changes in sound, power, and heat can help you diagnose worn brushes before they completely fail, allowing for timely replacements.
Why Carbon Brush Quality Matters More Than You Think?
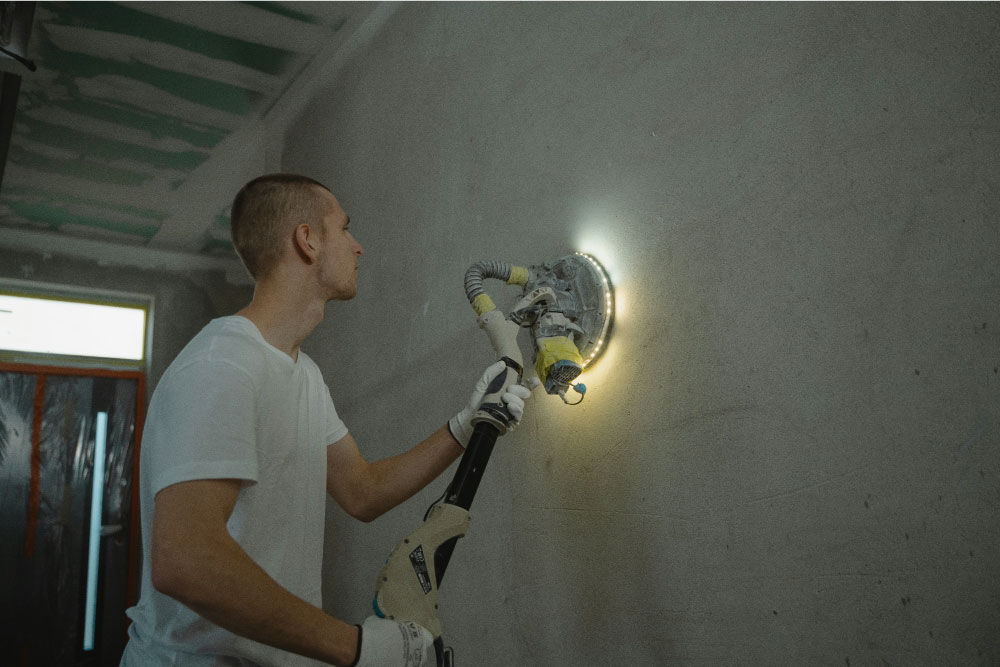
Not all brushes are created equal. Investing in high-quality carbon brushes can make a difference in both performance and longevity.
Brushes are available in different grades – soft, hard, or medium.
Softer brushes wear down more quickly but reduce wear on the commutator, while harder ones last longer but can be tougher on motor parts.
Choosing the Right Carbon Brush for Your Tool
- High-Density Carbon: For high-powered or frequently used tools, opt for premium brushes made from high-density carbon. These brushes will last longer and create less “arcing,” or visible sparking, which can prevent unnecessary wear on other motor components.
- OEM Options: Many tool manufacturers even sell OEM (original equipment manufacturer) brushes for specific models, which are often the best choice as they’re engineered for optimal compatibility (source).
Pro Tip: Always match the replacement brush to your tool’s specific motor type. Using brushes that are too hard or the wrong shape can create excessive wear on the commutator, shortening the motor’s lifespan.
Takeaway: Quality brushes suited to your tool’s needs can enhance performance and extend the life of both the brush and the motor.
Replacing Carbon Brushes: A Practical Guide to Boosting Tool Performance
Replacing worn brushes may sound intimidating, but it’s a task many DIYers can handle.
Most power tools have easily accessible brush compartments, usually under small plastic covers on the side of the motor housing.
Before you begin, make sure the tool is unplugged or has the battery removed to avoid any electrical risks.
Step-by-Step Replacement Tips
- Open the Brush Compartment: Use a screwdriver to access the compartment and remove the old brush.
- Examine the Spring Attachment: Brushes have springs attached to hold them against the commutator. When inserting a new brush, make sure the spring aligns correctly to keep the brush securely pressed against the motor.
- Close the Compartment: After the brush is in place, close the compartment securely.
- Break-In the New Brushes: Run the tool at a lower speed for a few minutes to let the new brushes “seat” or conform to the commutator’s shape. This break-in process is crucial for achieving smooth, consistent contact.
Pro Tip: After installing new brushes, avoid high-speed or heavy-duty operation for the first 15-20 minutes to allow for an even “seat” against the commutator. This improves the brush’s contact surface, ensuring it lasts longer.
Takeaway: Replacing brushes is a straightforward repair that can significantly enhance your tool’s performance, restoring power and prolonging lifespan.
How to Replace Carbon Brushes and Pro Tips for Ongoing Maintenance
Knowing when to replace brushes isn’t always straightforward, especially if your tool’s usage varies.
Carbon brushes typically last 50 to 150 hours of operation, depending on factors like motor speed and tool workload. Heavy-duty tools may need replacements sooner, while occasional-use tools might last much longer.
Proactive Carbon Brush Maintenance Plan
- Set a Routine: To keep your tools reliable, establish a maintenance routine that includes brush inspections, especially if you frequently use tools for extended projects.
- Stock Spare Brushes: Keeping extra brushes for heavily used tools can prevent downtime in the middle of a job. A small kit with common sizes is a wise investment, especially if you have multiple tools from the same brand.
Pro Tip: If you’re unsure about brush wear, a good rule is to check them after every 50 hours of use, which could be tracked by counting hours per project. A simple log can help you anticipate replacements, preventing unexpected interruptions.
Takeaway: Regular inspections and spare brushes help keep your tools ready for action, avoiding disruptions to your projects.
Also Read: Elevate Your Workshop: Must-Have Power Tools for Granite Projects