Causes of Leakage in Buildings:
It is very difficult to pin-point exact cause as well as the sources of leakage of water in the building. Water passes through labyrinth of porosity channels of capillary as well as air voids which are invisible and which are difficult to track down to their routes. The water might enter from one point and become visible at some other point. Hence the possible causes of leakages should be analyzed and understood as described here under before taking up remedial measures:
Ingress of Water in Structures can be:
From below (subsoil water), through Soil and Masonry by Capillary action.
From above i.e. external sources are such as rain/storm. Rain water and/or Water pressure exerted on structural members and their inability to withstand the same.
From inside the building owning to improper water supply, sewerage and drainage installations. Internal water sources such as leaking pipes/ improper fittings, joints incl joints which have opened.
If attention is not paid to their prevention at every stage of planning, execution and maintenance it is likely to result in discomfort to occupants and unsightly appearances discomfort of living, unhygienic conditions and at times diseases incl repairs beyond reach and possibility.
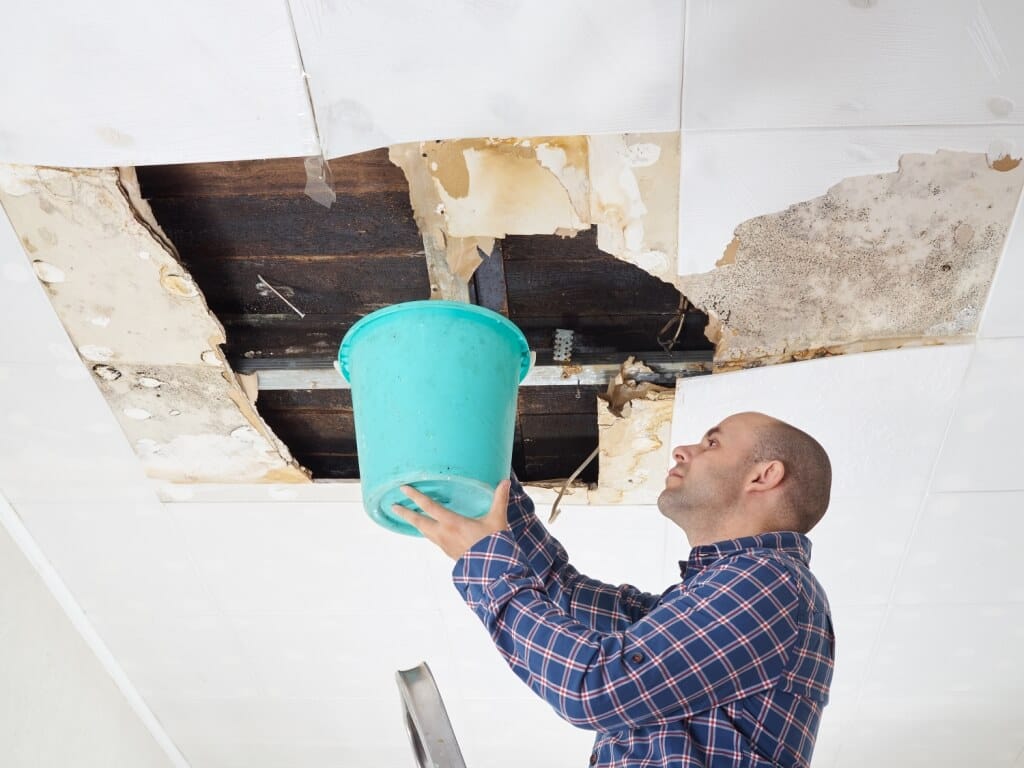
The major causes of leakage are:
(A) Structural Causes:
01. Cracks on the top surface of slab, due to various reasons including inadequate design of the slab.
02. Cracks on the bottom of slab due to excess deflection of slab, due to overloading or improper design.
03. Cracks at column supports.
- Poor workmanship and poor quality of materials particularly of RCC structures resulting in excess porosity in the slab, bad quality of concrete etc.
- Honeycombing: Honeycombing in concrete is due to improper proportion of aggregates, poor mixing or improper compaction or all of them together.
- Implications of use of higher water cement ratio: If the water cement ratio exceeds 0.6 to 0.7, then the pores in the concrete do not get segmented even with proper curing. Among other reasons, poor quality of construction makes the concrete pervious to water. Water enters into the porous concrete due to capillary attraction.
04. Expansion Joints in the Building:
Ineffective Sealing of Joints:
- Leaks through ineffectively sealed expansion joints, construction joints and other active cracks. For filling such joints, sealants like polysulphide are recommended. While providing expansion joint the engineer must remember that he is a civil engineer first and structural engineer later.
05. Leakage Due to Cracks:
Water follows the line of least resistance for entering into any material. Cracks in concrete or masonry walls provide paths of least resistance for the water to penetrate. Identify the type of crack. If it is a static crack, use of non-shrink modified polymer mortars or micro-concrete or any other sealant may be used.
- Cracks due to differential settlement of foundations of a building.
- Cracks formed in the RCC slab, beam, walls due to poor design, deficiency, over loading or poor workmanship resulting in honey combing etc
- Cracks due to thermal extremes, expansion- contraction, shrinkage, creep incl aggressive climatic conditions and lack of joints.
- Cracks due to vegetation growth.
- Cracks due to absence of structural elements like lintels, sill etc
- Cracks between two different materials particularly with different co-efficient of thermal expansion.
06. Spalling of concrete due to corrosion in the slab leading to cracks.
07. Leakage Due to Cold Joints:
One of the potential sources of leakage undoubtedly is thorough cold joint formed at the time of casting of concrete. It is difficult to identify such joints after completion of work. The location of these joints could be guessed only at the time of leakage.
08. Poor construction joints in both underground as well as overhead water tanks.
(B) Non-Structural Causes:
01. Poor Workmanship:
a) Slope not Proper – Defective Gradient of Terrace:
Improper gradient or slope of terraces leaves scope for water stagnation. One of the chief culprits of water leakage of roof slabs is improper gradient, improper drainage and rainwater collection arrangement. The gradient sloping towards khurras therefore should be proper.
The gradient or slope on terrace for rainwater to drain effectively must be not less than 1 in 48. Flooding of areas and improper or inadequate drainage is the main cause for leakage. Proper drainage of water solves most of the leakage problems.
Sometimes defective grading in brick bat lime Koba would result into absorbing water and seeping the same through weak spots or joints throughout the year instead of arresting the leakage.
It is also better to get rid of such sub-standard lime Koba grading.
It is also advisable not to adopt concealed rainwater disposal arrangements.
b) Defective Waterproofing:
Defects in Coping/Vatta:
- Lack of proper coping/ vatta at the junction between terrace and parapet walls is a major cause. If coping is not properly done and not properly tucked into the parapet wall and roof slab, the coping done would prove to be ineffective in arresting leakage of water through the cleavage developed between coping and parapet wall and between coping and terrace. Therefore coping provided must be effective and it must be done under close supervision.
Failure to Make Khurras:
- Khurras are other potential leaking points. Care must be taken to properly seal the khurras from seepage into walls and roof slab. The water collecting depression of rainwater must be made impervious.
c) Extreme Weather Conditions:
Dampness due to Development of Negative Pressure Inside the Structure:
- When the interior of the building develops low pressure when compared with that of the external pressure, due to suction effect, during high humid conditions, the air carrying external moisture may intrude inside the structure causing damp conditions.
02. Sub Standard Work Practices:
a) Holes in Masonry Made for Scaffolding:
During erection of scaffolding particularly for external plaster, holes are made for supporting one end of horizontal member of scaffold in walls. These holes are filled up negligently while removing scaffolding. Such holes are never filled with care. And again it is difficult to cure such isolated patches. Hence all such holes become source of water into walls and appear as damp patches later on in walls.
b) Breakage of Walls for Installation of Air Conditioners:
Similarly while installing Air conditioner particularly split units, holes are made in walls for gas / exhaust pipes. Such holes too are never filled with care that it needs.
c) Mechanical installations like cooling towers, AC units etc., on the terrace.
03. Poor Quality of Materials:
a) Poor Quality of Bricks and Plaster:
Masonry with poor quality bricks (having water absorption > 20%) and or with poor cement mortar joints (CM poorer than 1:6 and poor external plaster (CM poorer than 1:4) or inadequately cured masonry or plaster will always leak. Not only that, it will be very difficult and almost impossible to repair such poor workmanship.
b) Use of Porous Finishes and Brickwork on Exterior Walls:
Any other porous finish or even porous masonry will cause leakage.
c) Tiles on Terrace:
Because of lack of funds, many people still lay ordinary mosaic tiles made of cement concrete on terrace. Like ordinary cement concrete, mosaic tiles are also never waterproof. They are even more porous. Tiles will never solve your problem. What you need is good terrace waterproofing.
d) Trapped Water Problems:
- It is often found that the moisture trapped between the matrix of concrete and the surface finishing such as exterior emulsion paints do not allow the moisture to escape or migrate to other places, thereby causing damping problems and the attendant deterioration of substrate of the finishing layer. We must therefore ensure that the paint used is of vapor permeable type.
04. Poor Detailing:
a) No Waterproofing in Sunken Slabs of Toilets:
Very good waterproofing on bottom as well as sides of sunken slab for toilets is must.
No dismantling, breaking walls / slabs for pipe laying or any nature of hammering to any wall or plastered waterproofed surface in toilets should be allowed once water proofing is done. Hammering will create micro cracks causing leakage and which will be difficult to cure.
b) No Coping on Parapet Wall:
Defective Treatment of the Top of the Parapet:
- Failure to make the top of the parapet waterproofs.
- Normally after casting terrace slab, with a view to start immediate plastering work, parapet walls are constructed first. Thus the slab directly below parapet remains without waterproofing. Hence if adequate coping is not done, water will enter through top of parapet wall and enter in terrace slab. Further even if coping is done, water may enter through sides of parapet wall. Even a good coping (vatta) at junction will not prevent this.
c) Only Chemical waterproofing on Terrace:
Many people, who get motivated due to the advertisements of chemicals and chemical waterproofing, may provide only chemical waterproofing on terrace. This will not survive. Because most of the chemicals don’t have that stability against ultra violet radiation of the Sun. Further the film of chemical will start peeling off, once there is damage due to mechanical failure, like punch or a pin hole formed due to impact of heavy objects falling on it. This happen because the thickness of chemical waterproofing is in microns.
d) Balcony Without Waterproofing:
In most of the balconies or open terraces, no waterproofing is done on slab. While being open, water does get splashed and eventually accumulates there. Sometimes drains pipes from balconies are also not provided. The tiles or any flooring however good will not be able to prevent the leakage.
e) Absence of Throtting or Drip Course on Chajjas:
The chajja/weather sheds must be provided with throtting or drip mould so that water does not trickle down and it gets cut off and drops thereby stopping leakage.
f) No Vatta at the Joint Between Top of Chajja/Weather Shed and Wall:
Normally after casting chajja/weather shed, vatta or coping is needed at the joint between wall and chajja/weather shed so that water does not enter through joint.
g) Cut out in the Structure for the Branch Pipe:
No random cut outs or holes should be made in RCC members or even walls. The joint between the two is never going to be water tight.
h) Joints Between Flooring Tiles:
The joints between flooring tiles will allow water to percolate through slab causing leakage.
i) No Plinth Protection:
The water getting accumulated around the house will seep into the ground below. This will travel below the plinth or enter through external walls which have no coping.
Lack of adequate precaution in protecting the structure due to watering the adjoining gardens or lawns will also lead to such conditions.
j) Damp Proof Course not Provided or If Provided not Effective:
Most of the times DPC is not provided. If provided they are not adequate and may be at wrong locations.
k) Leakage of Water from Water Storage Tanks:
Failure to Make the Terrace Slab Waterproof on which Water Storage Tank is Installed:
It is often seen that when inlet water pressure is very high or when sub-standard float valves are used, the area below the water storage tank gets flooded and the situation gets worsened when there is water stagnation below the tank and the area has not been made thoroughly waterproof. Sometimes a short spout is provided for overflow of water and as a result of it, the overflow water gets collected around the tank itself.
l) No Heat Insulation on Terrace Slab:
Most of the times the RCC slab does not leak during initial years but starts leaking after few years of construction. This is because the slab originally was water tight. But because of extreme heat the due to expansion-contraction cracks develop in slab which ultimately provides outlet for water. It is for reason you also need to protect your slab from extreme heat and it is only because of this reason Brick Bat Lime Koba has been found effective and popular.
05. Poor Plumbing:
- Inadequate rain water pipes, improper drainage, no khurras
- Laying soil pipe / G.I. pipe below the floor.
- Minimum depth of water seal in various types of traps not maintained.
- Improper joints of water supply lines, water supply fittings etc.
- Incorrect placement of overflow pipe in overhead tanks.
- Improper slopes in floors and sanitary pipes and lack of adequate drainage pipes.
- Huge pressure in running water may cause leakage through joints if not done properly.
- No rain water outlets in balconies, open terraces etc.
06. Poor Maintenance:
a) Jalis/Perforated Cover on Rain Water Pipes on Terrace Getting Choked with Vegetation, Plastics:
This happens during first rain. No one really cleans outlets/ tops of rain water down take pipes. If there are trees near the house, the leaves including other wastes like plastics get accumulated on jalis/perforated cover and block water. The blocked water will find other routes or will get accumulated on terrace resulting in leakage.
b) Chocked Pipes:
The choking will naturally block passage of water. Water will try to come out through some other source or weak point, surface / joint.
c) Broken Pipes:
GI or other pipes, if not of good quality, when concealed will corrode or sometimes break. This will lead to leakage.
d) Throwing of Solid Wastes in WC’s.
e) Lack of Periodic Checks and Cleaning Arrangements:
- All the causes narrated above needs preventive maintenance and if neglected will invite water from one or other way.
It is therefore a common observation that most of the building elements are provided in the structure without the required detailing and thought for weather protection. Observations and results are imminent in their manifestation. One does not monitor the structures which one creates with love and passion.
Any one of above or together is the sure cause of leakage. This cause will allow water to enter and it will leak at some far away different point which is coherently weak. It therefore needs great care while designing, detailing, construction and of course while maintaining. To understand more about it and to identify the sources of water and remedial measures thereof, Read Sources of leakage.