Table of Contents
Construction projects fail at an alarming rate of 85% worldwide. Budget overruns and missed deadlines are the main culprits behind these failures. These numbers paint a stark picture of what construction professionals face every day.
Sussex’s building construction companies grapple with these challenges. Their problems span from sudden cost spikes to weather delays. Each project tests a manager’s skills and flexibility to adapt. Here is the common challenges in construction projects and how to solve them.
Major Budget Control Issues
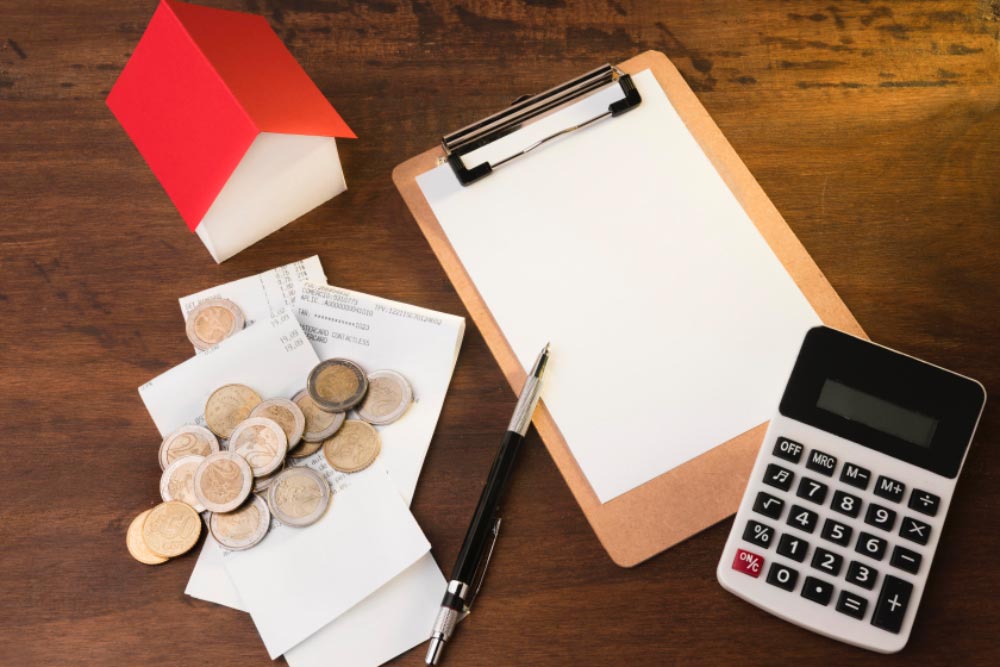
Budget control remains one of the biggest challenges in construction projects. Recent data shows that large projects can exceed their budget by up to 80%. This extra cost affects project timelines and the quality of final delivery.
Hidden Cost Factors in Construction
Construction projects face unexpected expenses that can throw off even well-planned budgets. These hidden costs usually include:
- Site preparation and excavation charges
- Permit and clearance fees
- Equipment repairs and replacements
- Weather-related delays
- Design modifications during construction
The quickest way to handle this involves keeping 10-15% of the total budget as contingency funds. Many building construction companies in Sussex use this approach to protect their projects from financial surprises.
Impact of Material Price Fluctuations
Material costs have become highly unpredictable over the last several years. Construction input prices rose by 22.3% year-over-year, while nonresidential construction materials jumped by 23.2%. Supply chain disruptions, market demand changes, and global economic conditions cause these fluctuations.
Steel prices, to name just one example, saw a 90.3% increase in 2021. Ready-mix concrete prices also climbed substantially, with an 11.2% increase in 2023 after a 10.3% rise in 2022.
Labor Cost Management Strategies
Labor expenses make up 50-60% of total construction costs for certain project types. These costs go beyond simple wages and include:
- Training and onboarding expenses
- Benefits and payroll taxes
- Overtime compensation
- Safety training programs
Construction managers can keep these costs under control through smart scheduling and resource allocation. Digital tracking systems help them monitor labor hours and spot areas that need improvement. Companies that use proper labor management strategies see lower overtime expenses and better productivity.
Project Timeline Bottlenecks
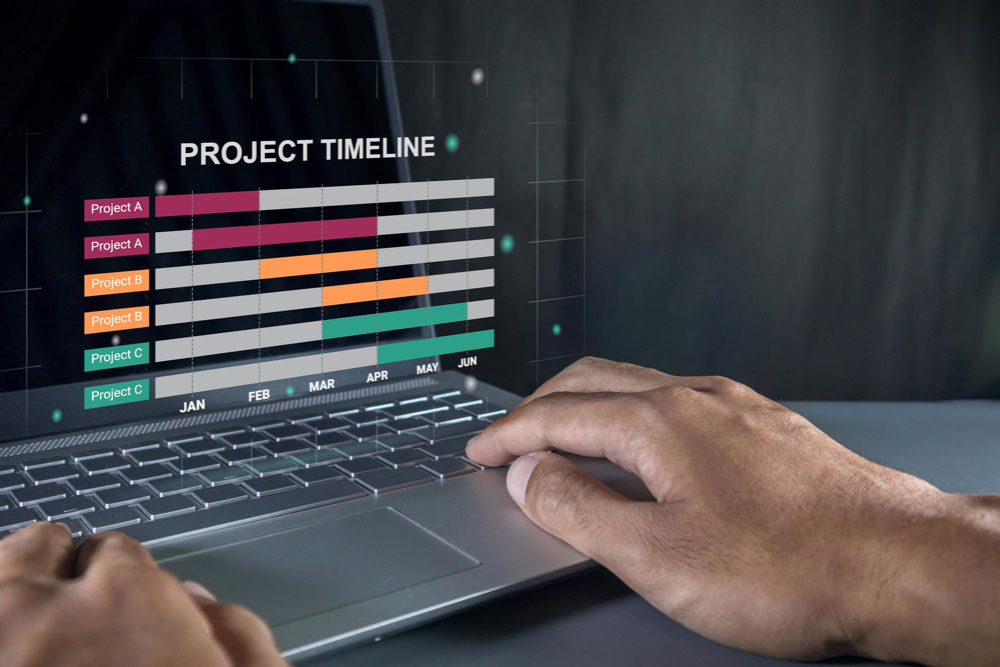
Construction projects struggle with time management. Studies show that projects run late by an average of 20 months. These delays create a domino effect throughout the project timeline.
Common Causes of Construction Delays
Several obstacles slow down construction projects repeatedly:
- Documentation and permit delays
- Labor shortages and skill gaps
- Equipment breakdowns
- Material delivery delays
- Subcontractor coordination problems
A single lost day of work on a $200 million construction project can drain up to $250,000 in labor, equipment, and contractual penalties. This hits building construction companies in Sussex hard and eats into their profit margins.
Resource Allocation Problems
Projects with multiple activities happening at once face tough resource management challenges. Research shows that 87% of construction projects run late because they can’t allocate resources properly. Project managers need to balance equipment use, worker schedules, and material deliveries carefully.
Digital tools help construction managers track how resources are used and spot potential problems early. These systems let managers adjust their plans and move resources around based on live data.
Weather-related Setbacks
Bad weather costs the construction industry billions each year in delays. Projects run into trouble when:
- Temperatures drop below 25 degrees or climbs above 95 degrees
- Daily rainfall tops 1.5 inches
- Wind speeds stay above 20 MPH
Modern construction management systems now come with weather forecasting features. These tools help managers plan around conditions that could stop concrete work, crane operations, or digging. Teams can plan ahead instead of scrambling to deal with weather problems.
Communication Breakdown Points
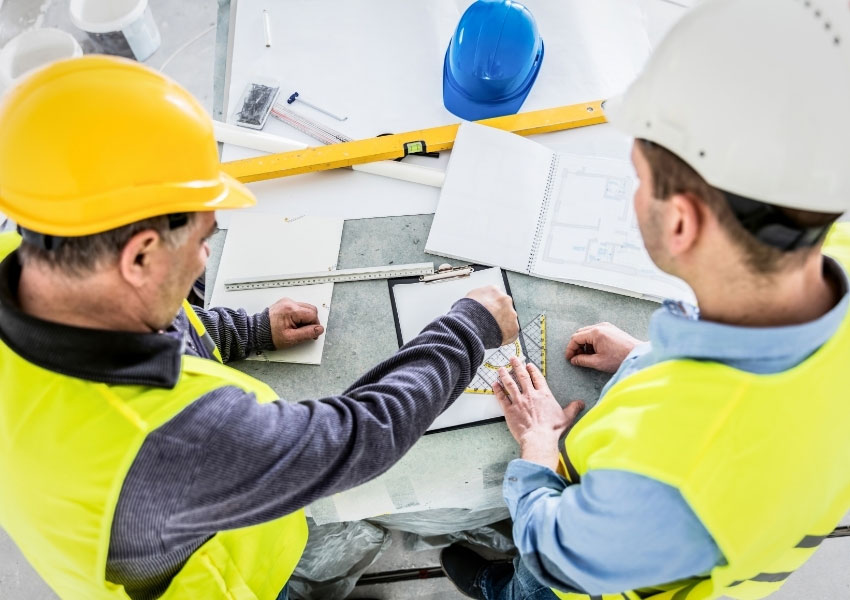
Construction companies in the United States lose over $177 billion each year due to poor communication. Fortus Construction, a building construction company in Sussex, knows that good communication forms the foundations of delivering successful projects.
Stakeholder Coordination Gaps
Construction projects bring together multiple stakeholders who have different priorities and goals. These differences cause budget overruns and delay projects. Construction workers now spend 35% of their time doing non-productive work and waste 5.5 hours every week just looking for project information.
Documentation Issues
Project teams face several critical documentation challenges:
- Plans and specifications become outdated
- Teams can’t access important documents easily
- Document organization lacks consistency
- Approval processes take too long
- Records go missing or remain incomplete
Teams waste 14 hours per person weekly to fix documentation problems and resolve conflicts. Digital document systems help reduce these inefficiencies.
Information Flow Barriers
Project bottlenecks create problems that affect everything downstream. Workers lose 3.9 hours weekly fixing mistakes caused by poor information sharing. Teams that depend on disconnected technology and manual processes make this problem worse.
Project success depends on construction managers, who track progress through updates and shared tools. Modern construction tools give teams immediate access to project details. Companies see fewer errors and better results when they use proper documentation systems.
Quality Control Challenges
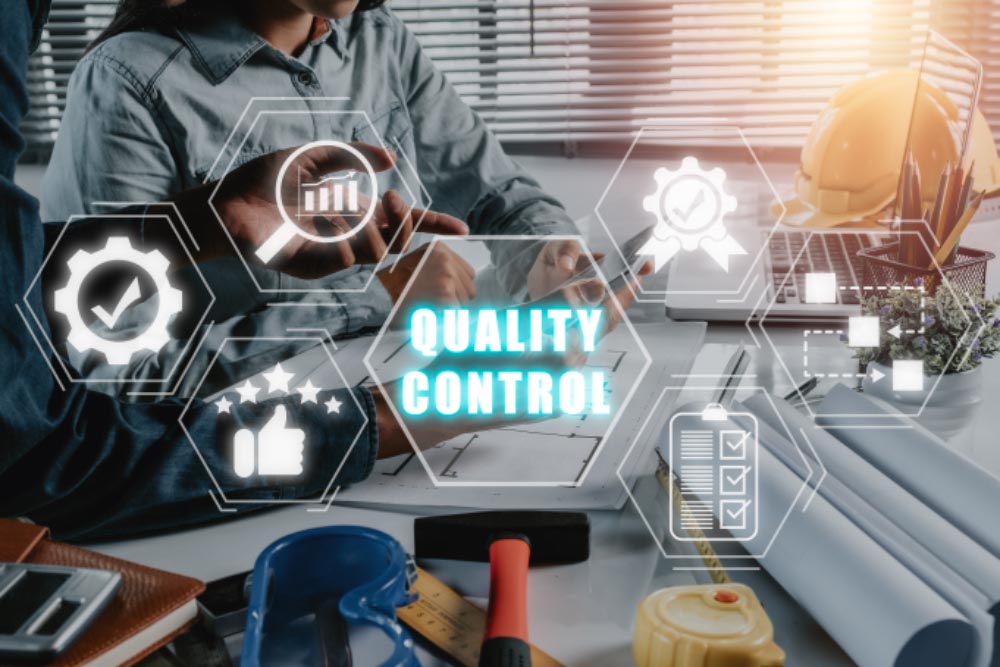
Quality control is the life-blood of successful construction projects. Defects and failures can lead to major financial effects. Studies show that even minor defects create the need for reconstruction and disrupt operations.
Material Quality Issues
Construction firms face their most important challenges when they maintain material quality standards. Poor-quality materials drive up long-term costs through repairs, replacements, and warranty claims. A recent industry analysis showed construction firms lose millions annually because of substandard materials.
Quality control measures should have:
- Regular material testing and verification
- Strict supplier qualification processes
- Documentation of material specifications
- Sample testing before bulk orders
- Storage and handling protocols
Workmanship Standards
The construction sector has seen a surge in workmanship-related regulations in the last fifty years. Fortus Construction, a building construction company in Sussex, knows that high workmanship standards are vital to project success. Studies show that poor workmanship becomes obvious, especially when you have soundproofing, insulation performance, and air-tightness issues.
Construction teams must follow contract specifications while meeting industry standards. Data shows construction staff spends 65% of their time on project-related activities and 35% on non-project tasks, including quality control documentation.
Inspection and Compliance Problems
Construction quality control needs systematic inspection processes. Research shows projects worth more than £20 million often need a resident site inspector to monitor construction progress. These inspectors provide independent assessments without taking responsibility for the work itself.
Digital construction management tools have transformed inspection processes. Modern systems help track compliance requirements and automate documentation. Statistics show construction companies waste 14 hours per person weekly on documentation-related problems.
Total quality control systems want to achieve zero defects throughout the construction process. This approach needs commitment from all organizational levels and has regular design reviews, quality circles, and detailed testing protocols.
Conclusion
Construction projects face many hurdles – budget overruns and quality control problems top the list. Smart management and modern tools help teams tackle these challenges head-on. Digital systems make it easier to track resources, handle paperwork, and keep teams connected.
Success in projects comes down to solid planning and execution. Teams can reduce risks by setting up emergency funds, watching weather patterns, and following strict quality checks. Building construction companies in Sussex that use these methods deliver better results with fewer delays.
Project leaders who welcome digital tools set their teams up to win. These solutions cut down paperwork time and help teams manage resources better while staying on budget. Project tracking systems boost quality control through automated checks and live updates.
Also Read: Effective Strategies for Managing a Construction Project from Beginning to End