In this article, we discuss corrosion monitoring in reinforced concrete structures, its importance, advantages, and monitoring methods etc.
Do you know why ancient structures, such as forts and temples, stand firm to date compared to structures built over the past 30 to 50 years?
Have you ever given it a thought?
There are many factors, but the significant difference is that ancient structures were made of natural stones, lime etc., which did not require or only required minimal reinforcement. On the other hand, steel, widely used in buildings over the last decades, has become one of the major reasons why recently built structures do not last long.
Yes, you heard it right. Steel, or reinforcing, is one of the main reasons structures or buildings fail nowadays, and the reason is its corrosion. Hence, it’s crucial to know corrosion monitoring. The followings are the content details –
- Need for Corrosion Monitoring of Reinforced Concrete Structures.
- What Is Corrosion Monitoring?
- Why Is Corrosion Monitoring Important?
- Advantages of Corrosion Monitoring.
- Corrosion Monitoring Methods.
Let’s have a detailed look –
Need for Corrosion Monitoring of Reinforced Concrete Structures
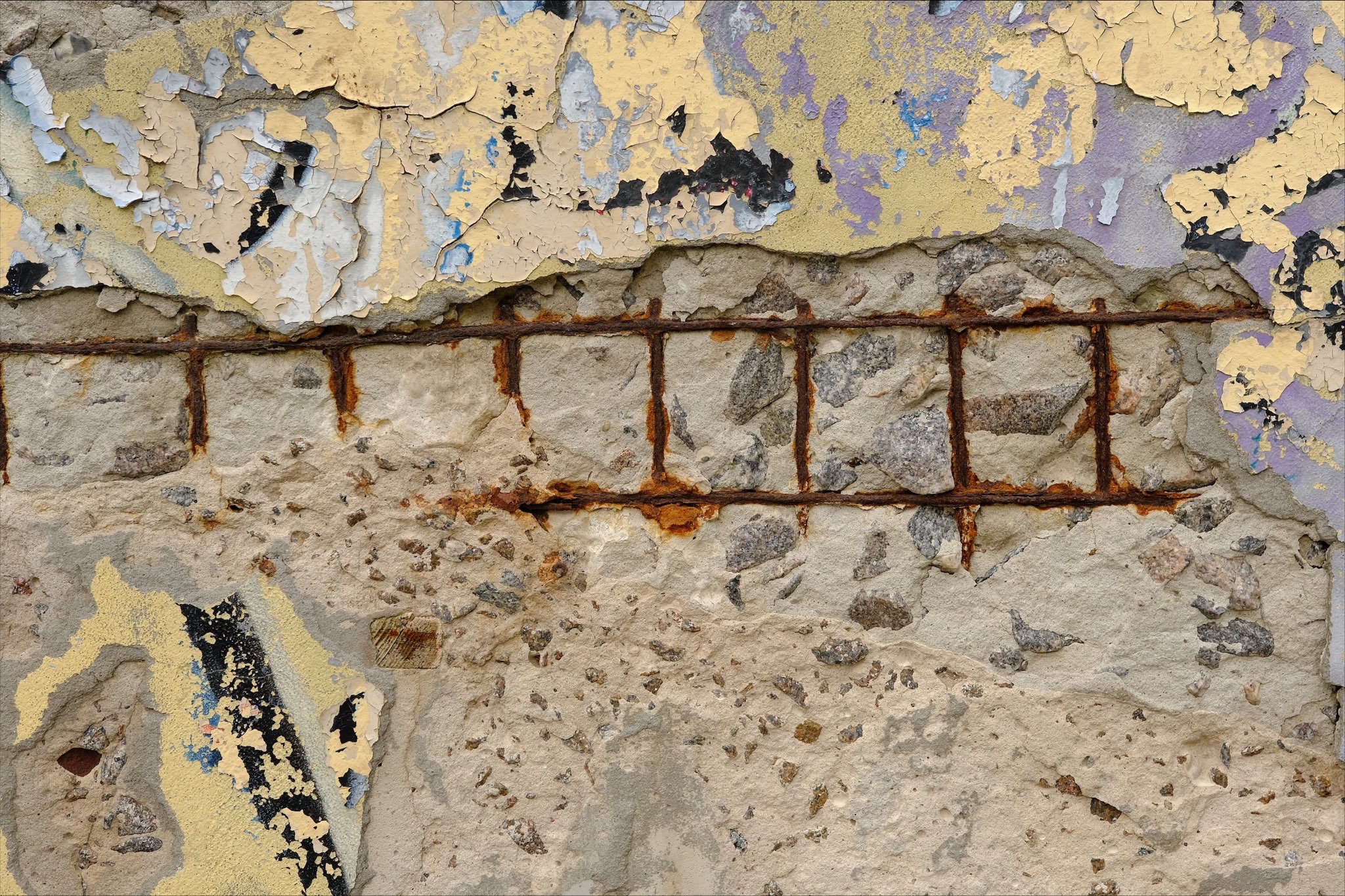
Concrete is strong in compression but weak in tension. Hence, we embed steel reinforcement in concrete to get adequate tensile strength. The concrete embedded with reinforcing steel is called Reinforced Cement Concrete (RCC). However, this reinforcement inside the Reinforced Concrete Structure is susceptible to corrosion damage. There are various causes of corrosion of reinforcement steel in concrete. Even if a structure is stable, corrosion can make it hazardous, uncomfortable and unusable.
Corrosion is a typical process we see in our daily lives. It may seem elementary, but it contributes to the small-scale deterioration of metals, such as those found in the grill of doors and windows in houses or in old cars, bikes, etc. On a larger scale, it significantly impacts the destruction of industrial pipes, RCC and steel structures, boilers in factories, steel chimneys, cooling towers etc. Corrosion has wasted a lot of resources and money, and today’s expenditure on infrastructure, industries etc., includes a sizable portion of repair costs.
Did you not comprehend? Let me give a typical example.
In the human body, skin can be compared to plaster and paint; muscles can be compared to concrete, and bones can be compared to reinforcement steel.
When our bones are damaged, we cannot function normally. The same is true of reinforcement steel in concrete structures, which can cause one part of the building or the entire building to fail.
Want to know more about the reasons for building failure due to the corrosion of steel bars? Go through the blog below –
Therefore, non-destructive inspections and monitoring techniques that can detect corrosion are required for quality control, planning and maintenance to ensure the longevity of these structures. Non-destructive concrete tests are also crucial for verifying structural strength and detecting corrosion. To do this, we must fully comprehend the corrosion monitoring system concept.
What Is Corrosion Monitoring?
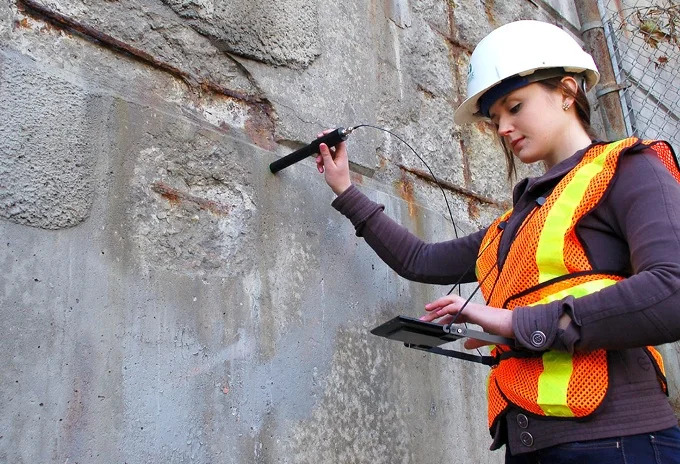
Many structural engineers ask about the best practices in corrosion monitoring and investigation. However, several issues on this subject still need to be solved, beginning with how to conduct a reliable investigation. Many people are also concerned about the outcomes of current testing procedures as well as their accuracy and precision.
Corrosion monitoring of reinforced concrete structures is challenging because corrosion happens slowly. Therefore, it is hard to detect early-stage corrosion. On the other hand, it is almost too late when we start to see the signs of surface corrosion. Detection and monitoring corrosion require appropriate knowledge, proper inspection tools, and experience.
Definition of Corrosion Monitoring
Corrosion monitoring is the process that evaluates and monitors the equipment, components, and structures and looks for signs of corrosion. It is a quantitative method that produces results regarding the extent of damage caused by corrosion. Additionally, it offers suggestions for improvement and ways to take preventative action.
The condition of structures can be monitored by visual inspection and other methods. According to it, remedies can be given. Therefore, periodically conduct surveys and keep track of the collected data to monitor the structure’s condition, beginning with the construction phase. According to the corrosion monitoring system data, one can make an informed decision about the structure’s remaining life, other life extension techniques and cost-effective measures to resolve corrosion problems.
Important Data & Steps of Corrosion Monitoring
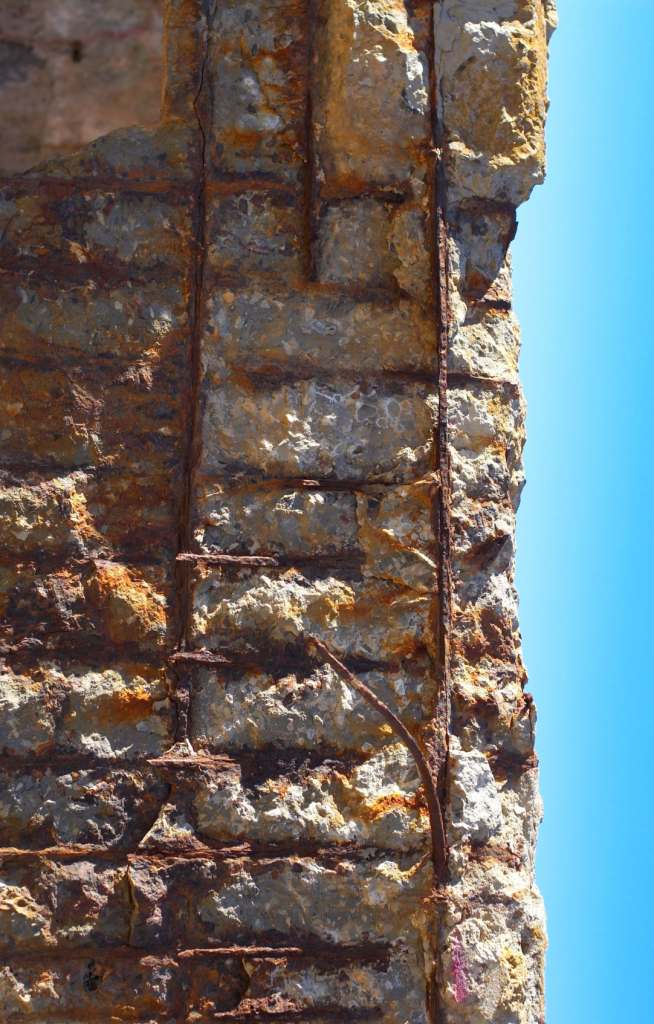
Important Data to Collect for Corrosion Monitoring
The important information and data to collect during corrosion monitoring of reinforced concrete structures are:
- The location and extent of the corroded areas
- The corrosion rate (i.e. how quickly it has spread over time)
- The root causes of the corrosion.
Important Steps of Corrosion Monitoring of Reinforced Concrete Structures
The following are the important steps involved in the corrosion monitoring of reinforced concrete structures:
- A visual inspection is done, and areas damaged due to corrosion are seen with the eyes.
- A suitable method and instrument are selected based on damage due to corrosion.
- The experiment is performed on the structure.
- Results are prepared in chart form, and thorough reports are made.
- Remedies are suggested as per the evaluation of the results.
Why Is Corrosion Monitoring Important?
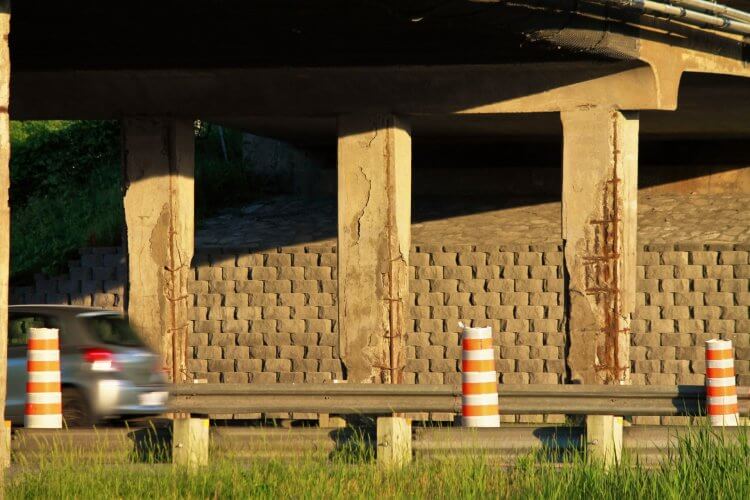
The main reasons for corrosion monitoring are as follows:
- Safety Perspective
- Reduction in Cost
- Better Efficiency
1. Safety Perspective
Corrosion monitoring of reinforced concrete is an important aspect of safety and as time passes, concrete components become more and more susceptible to corrosion. Thus, reducing life can make concrete components less useful, and if corrosion exceeds more, a component’s failure can occur, leading to an accident. Therefore studying corrosion monitoring can help in providing safety.
2. Reduction In Cost
Corrosion is causing damage to a lot of components, rendering them useless. Thus, regular monitoring can both protect the component and provide remedies that can be employed to reduce the renovation cost.
3. Better Efficiency
In addition to helping prevent accidents and cut costs, corrosion monitoring can improve the efficiency of industrial operations by extending component usage in better and more efficient ways.
Advantages of Corrosion Monitoring
- Corrosion monitoring gives an early warning when a destructive process of corrosion sets in.
- It also demonstrates the effectiveness of specific corrosion control techniques.
- Corrosion monitoring provides management information about the plant or equipment’s current health status and upkeep requirements if any.
- It can pinpoint a specific corrosion issue as well as its root causes and relevant control variables.
Corrosion Monitoring Methods
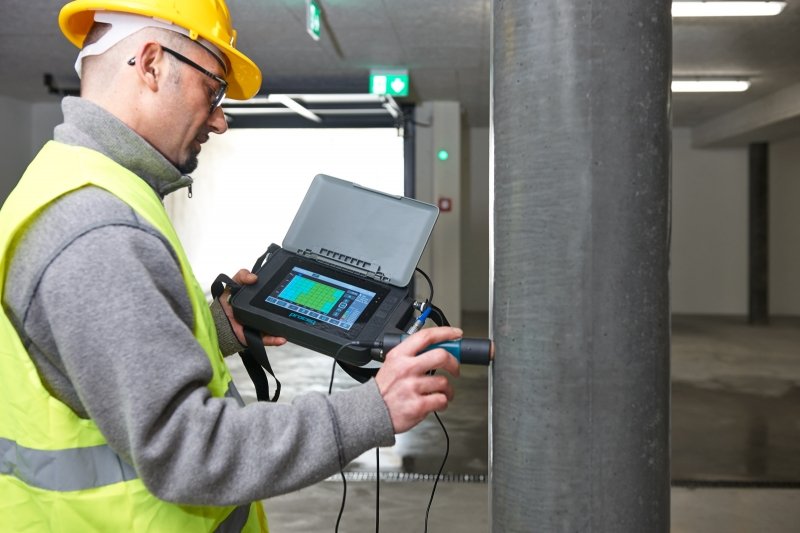
Various non-destructive methods, based on electrochemical and electromechanical techniques, have been used to identify the risk of steel corrosion in concrete structures, detect the damage caused by corrosion at an early stage, predict residual lives, and decide what preventive or repair systems are to be applied.
The following non-destructive and destructive methods are listed:
- Visual inspection
- Half-cell potential measurement
- Concrete Electrical resistivity measurement
- Linear Polarization Resistance (LPR) measurement
- Electrochemical Impendence Spectroscopy (EIS)
- Electrochemical Noise Analysis
- Vibrating wire and electrical strain gauges
- Cover thickness measurement
- Gravimetric weight loss methods
These are the standard t methods to determine corrosion. Certain measures to control the corrosion of steel reinforcement are –
- Coating of Reinforcement: Cement coating, epoxy or sealing coating is done on reinforcement.
- Coating of Concrete: A surface coating on concrete members increases their life and improves the appearance of the structure.
- Metallurgical Method: The structure of reinforcement is altered during its metallurgical process.
- Corrosion Inhibitors: By using chemicals such as calcium nitrate, phosphate, and benzoates, corrosion can be prevented or delayed.
- Cathodic Protection: One of the most effective methods used in the field.
On a final note, it is to be said that corrosion of structures is a harmful phenomenon which brings down the structure’s life. Therefore, it is crucial to monitor and study the propagation of corrosion in Reinforced Concrete Structures to adopt appropriate remedial measures. This shall help in prolong the life of the reinforced concrete structure.
Gharpedia has also written on concrete durability and various testing on Building materials. You might also be interested to know that Gharpedia has a special Gharpedia exclusive material testing category, where you can find all your answers to why – what – How regarding building material testing.
Image Courtesy – Image 1, Image 3, Image 5, Image 6
Author Bio
Mihir Solanki –