Corrosion of steel reinforcement in concrete is the most common occurring phenomenon in reinforced concrete structures. In this blog, gharpedia explains the process of corrosion of reinforcing bars in concrete, as well as suggests preventative measures.
What is Corrosion?
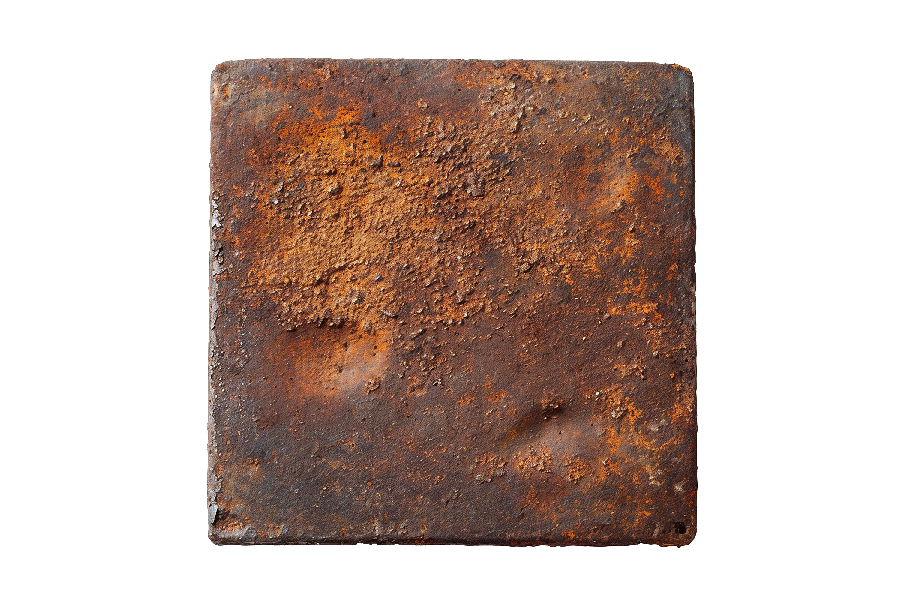
Corrosion is a natural deteriorating mechanism. In general, through the process of corrosion, metals are converted into metal oxide, metal sulphide, etc. Corrosion of steel reinforcement leads to orange or reddish-brown rust deposits surrounding the reinforcing steel bars. When subjected to rusting, steel reinforcement becomes brittle and flaky and slowly loses its mechanical strength and elasticity.
Feature blog box Corrosion Monitoring Methods for Reinforced Concrete Structures
Corrosion of Reinforcing Steel Bars in Concrete
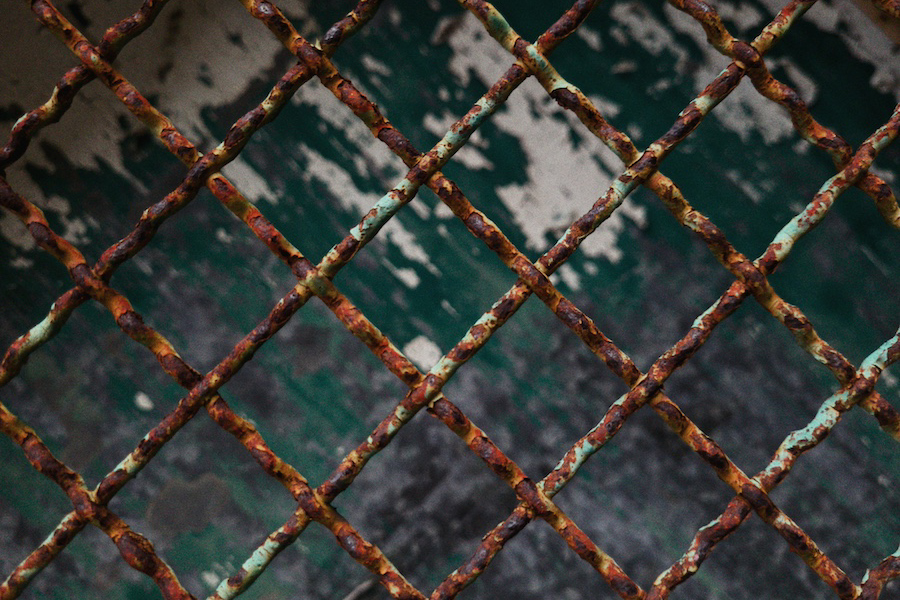
In general, concrete provides corrosion protection for the embedded steel reinforcement. This protection is a result of the high alkaline nature of concrete. A well-designed concrete, with a low water-to-cement ratio that is compacted adequately usually possesses a low level of permeability to prevent the ingress of corrosion inducing agents from the atmosphere. Even so, corrosion of embedded steel in concrete happens over time for various additional causes like long exposure to water or chloride. Below image shows how corrosion of steel bar in concrete takes place.
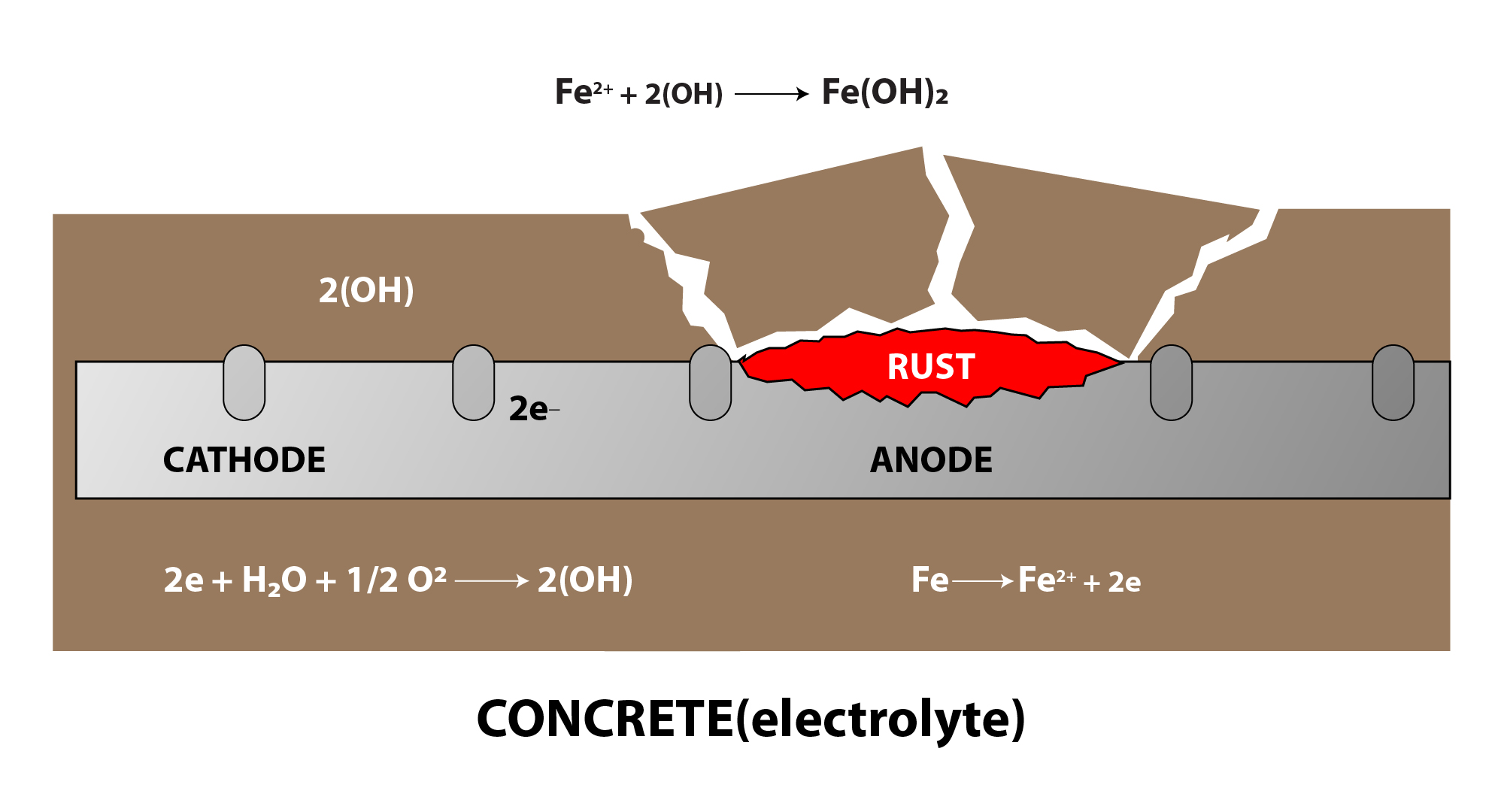
The bar acts like an electrolyte at the anodes, where iron atoms lose electrons and enter the concrete as ferrous ions. The anodic reaction, often known as a half-cell oxidation reaction, is one such process. Corrosion of reinforcement steel increases the volume of steel reinforcement in concrete due to rust formation, which creates tensile strength in the surrounding concrete, resulting in cracking, delamination, and spalling of the concrete. The presence of chlorides greatly exacerbates the corrosion attack.
A concrete structure may eventually collapse due to the corrosion of steel reinforcement if it is not repaired and maintained properly. Corrosion in RCC structures like bridges, parking structures, and off-shore structures such as piers, dams, docks, and port structures are destroyed by chloride-initiated reinforcement corrosion.
Know more about building failure due to corrosion here: Reasons of Building Failure due to Corrosion of Steel Bars
How Does Corrosion of Steel Reinforced Concrete Structures Take Place?
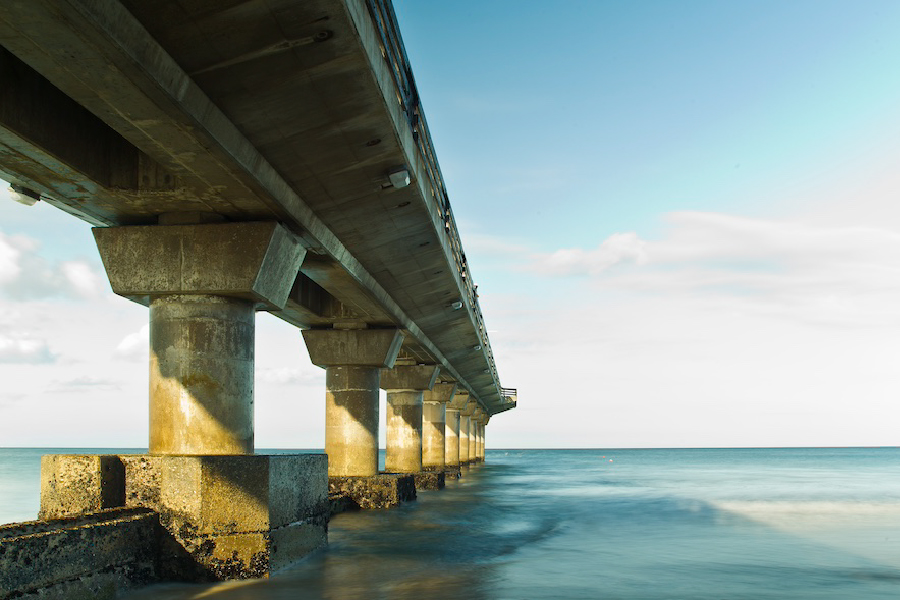
The chloride ions present in the water provide the right recipe for the corrosion of reinforcing bars in concrete. The chloride concentration is found in sea water and in waste water coming out of manufacturing units. Now the mute question is: how do chloride ions find their way into concrete that leads to the corrosion of rebar? Chloride ions present in concrete are usually acquired from different sources.
- Aggregates used in concrete making,
- Mixing water used in concrete making,
- Admixtures used in concrete making,
- Coastal saline environment, and
- De-icing salt is used on roads in cold countries.
Chloride is water-soluble, and in the case of hardened concrete, corrosion of steel in concrete structures takes place when chloride enters the concrete due to capillary action, which in this case means the flowing of water in the pores of the concrete. The cyclic freezing and thawing processes may also increase the chloride content of the concrete pore water.
The mechanism of corrosion promoted by chloride is not clearly understood to date. The popular theory is that chloride ions easily penetrate the protective oxide film over the embedded steel reinforcement, leaving the steel reinforcement vulnerable to corrosion.
We also have a detailed article on the causes of corrosion. Check it out here: Causes of Corrosion of Reinforcement Steel in Concrete
Prevention of Corrosion of Steel in Reinforced Concrete
Steel corrosion can be prevented in the following ways:
I. Use of Cement-Polymer Composite Coated Steel Reinforcement:
Cement polymer, when coated over steel reinforcement, creates an alkaline medium surrounding the steel reinforcement. This alkaline medium prevents corrosion.
II. Use of Fusion Bonded Epoxy-Coated Steel Reinforcement:
In this process, steel reinforcement is provided with a coating of epoxy powder. This coating over steel reinforcement prevents the occurrence of electro-chemical reactions. When the electro-chemical reaction is prevented, the corrosion is also prevented.
III. Use of Corrosion Resistant Reinforcment Steel:
Corrosion resistant Steel reinforcement possesses in-built corrosion resistance. This characteristic of steel reinforcement is achieved due to the chemical composition adopted during the manufacturing process.
IV. Use of Well-designed Concrete and Use of Proper Concrete Cover:
Control of the water-cement ratio in the production of concrete is key to the production of dense concrete. Concrete becomes porous if more water is used in the manufacturing process. Further, adequate concrete cover should also be provided for steel reinforcement embedded in concrete.
V. Testing of Concrete Ingredients:
Some ingredients, like water, aggregate, and admixtures, used in the production of concrete may contain chloride; hence, these ingredients should be tested for the presence of concrete before use. Materials with chloride contents should not be used in the production of concrete.
- The use of cementitious materials like slag and pozzolana makes the concrete dense, reducing the chance of water penetration and thereby reducing corrosion in steel reinforcement.
- Wire brushing the reinforcement to remove the rust scales before pouring concrete on the surface can help in prevention.
- Maintain a high degree of workmanship in concrete production, placement, compaction, and curing processes.
Corrosion Resistant Reinforcing Options
Studies on alternatives to steel reinforcement have been going on a continuous basis. Fiber-Reinforced Polymer (FRP) bars are one replacement that emerges as a perfect alternative to steel. In addition to being resistant to chloride ions, fiber-reinforced polymers (FRPs) also have unique mechanical qualities. There are four materials used in the production of fibre with civil engineering applications:
- Carbon is used in the production of Carbon Fibre Reinforced Polymers (CFRP)
- Glass is used in the production of Glass Fibre Reinforced Polymers (GFRP)
- Aramid is used in the production of Aramid Fibre Reinforced Polymers (AFRP)
- Basalt is used in the production of Basalt Fibre Reinforced Polymers (BFRP)
Though the use of FRP holds promise as a future alternative to steel reinforcement, its uses have been mostly restricted to strengthening, repairing, and retrofitting. For example, CFRP is extensively used in India in retrofitting work.
Also Read, Repairing of Corrosion Damaged Concrete
FRP in General has the Following Limitations
1) FRP has insufficient rigidity and gets easily deformed.
2) The long-term temperature resistance of FRP is poor.
3) FRP shows degradation in performance under the action of ultraviolet radiation, wind, snow, and chemical media.
4) It has low interlaminar shear strength, meaning bonding between layers is weak.
Conclusion
Corrosion in general is considered one of the most significant problems across the globe. The National Association of Corrosion Engineers conducted a global study on the cost of corrosion and preventive strategy in 2013. As per that study, the estimated global cost of corrosion was 3.4% of GDP, and for India, that figure was 4.2%. It can be safely presumed that the corrosion of steel reinforcement in concrete is substantial, hence the need for alternatives to steel reinforcement, and FRP holds promise in this regard.
Author Bio
Nafisa Nazneen Choudhury – Nafisa Nazneen Choudhury is a Civil Engineer (completed B.E. from Assam Engineering College) and is currently pursuing M.Tech in Structural Engineering at National Institute of Technology, Silchar. She is a Technical Content Writer, having over 3 years of experience and has wrote many articles related to Civil Engineering. She is also a Book Author (Authored – “Dream Tales of NNC: Revenge By Murder”) and her book can be found on Amazon. She is also a Guest Author at Gharpedia. Moreover, she is a certified member at Institution of Civil Engineers (ICE) and National Society of Professional Engineers (NSPE). She writes her blogs at her website – nnc2017.wordpress.com. She can be reached on LinkedIn.