When it comes to metalworking, precision and strength are crucial for ensuring the durability and stability of the final product. One of the most effective tools in achieving this is the self-tapping screw. These screws are engineered to form their threads as they are driven into the metal, making them a go-to choice for a wide range of applications. This guide on self-tapping screws for metal aims to provide a comprehensive understanding of self-tapping screws, offering insights into their types, benefits, and best practices for use.
Understanding Self-Tapping Screws
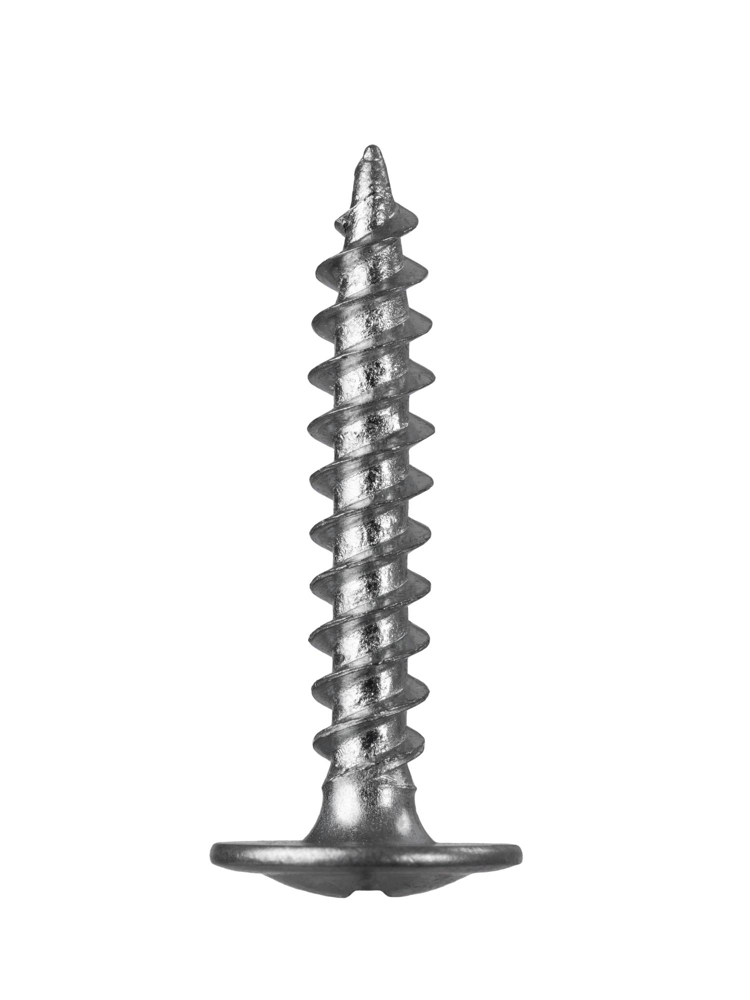
Self-tapping screws are a unique type of fastener designed to create threads as they are screwed into a substrate, typically metal. Unlike traditional screws, which require a pre-tapped hole, self-tapping screws can be driven directly into the material, cutting their threads in the process. This capability makes them especially useful in metalworking, where creating precise, threaded holes can be challenging and time-consuming. There are several types of self-tapping screws, each suited to specific applications. Thread-forming screws are ideal for softer metals, as they displace material to create the thread without removing any of it. This ensures a tight fit and strong connection. Thread-cutting screws, on the other hand, are designed for harder metals. They remove material to create the thread, reducing the risk of cracking or splitting in the substrate. Self-drilling screws combine the features of a drill bit and a self-tapping screw, making them perfect for applications where a pilot hole is not necessary. These self-tapping screws for metal are often used in construction and roofing, where speed and efficiency are paramount.
Advantages of Using Self-Tapping Screws for Metal
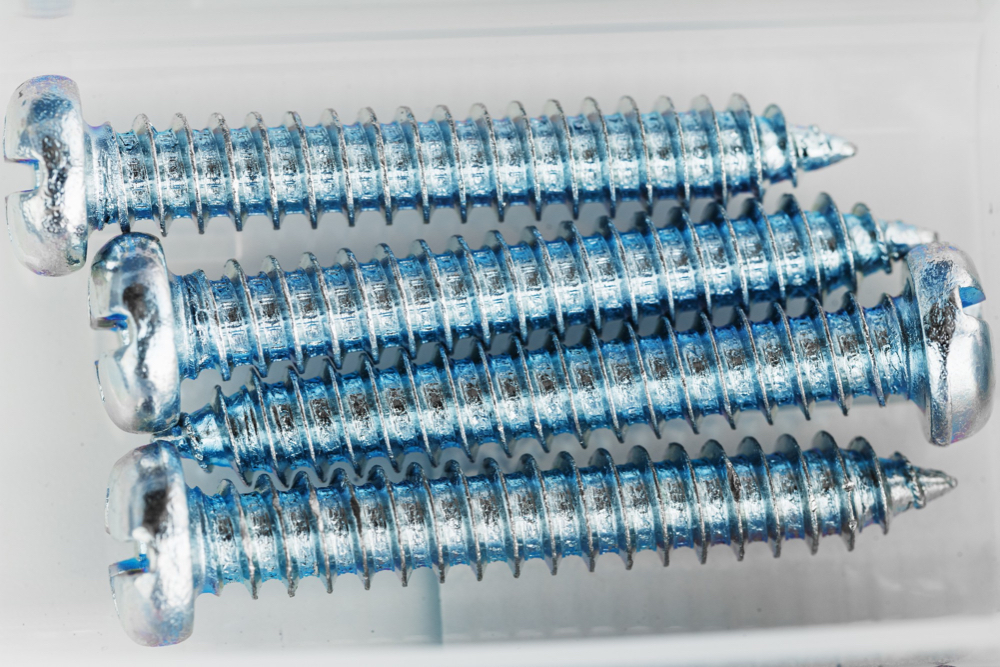
Self-tapping screws offer several advantages that make them an excellent choice for metal fastening. One of the primary benefits is the precision and strength they provide. Because these screws create their threads, they ensure a tight, secure fit that can withstand significant stress and load. This makes them ideal for applications where strength and durability are critical, such as in the automotive and construction industries.
Another advantage of self-tapping screws is their time efficiency. Since they do not require a pre-tapped hole, they reduce the need for additional steps in the installation process. This can save considerable time and effort, particularly in large-scale projects. The versatility of self-tapping screws is also worth noting. They can be used in a variety of metalworking projects, from light-duty tasks like securing electrical components to heavy-duty applications such as metal framing and roofing.
How to Choose the Right Self-Tapping Screws for Metal
Choosing the right self-tapping screw for your project is essential to ensure optimal performance and longevity. The first consideration is the type of metal you are working with and its thickness. Softer metals, such as aluminium, typically require thread-forming screws, while harder metals, like steel, are better suited to thread-cutting or self-drilling screws. The thickness of the metal will also determine the screw size, as longer screws are needed for thicker materials to ensure a secure hold.
It is also important to assess the load and stress factors that the screw will need to withstand. For applications where the screw will bear a significant load, such as in structural components, a stronger screw material like carbon steel may be necessary. The environmental conditions in which the screw will be used should also be considered. For outdoor applications or environments where the screw will be exposed to moisture or corrosive substances, stainless steel or a corrosion-resistant coating is recommended.
Best Practices for Installing Self-Tapping Screws
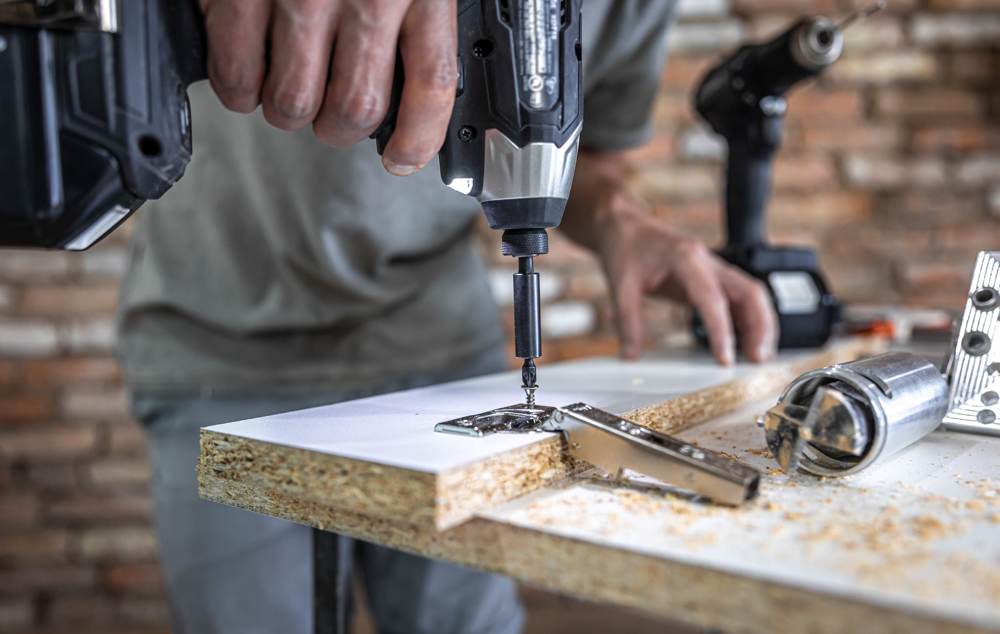
Proper installation of self-tapping screws is crucial for ensuring a strong, secure connection. The first step is to prepare the metal surface by cleaning it thoroughly. Any debris, grease, or rust can interfere with the screw’s ability to form threads and may lead to a weaker connection. If the metal is particularly hard or thick, drilling a pilot hole can help guide the screw and reduce the risk of breakage.
Selecting the right tools for installation is also important. For most self-tapping screws, a standard screwdriver or power drill with the appropriate bit will suffice. However, for larger or harder screws, a more powerful drill or an impact driver may be necessary to provide the required torque. When driving the screw, it is essential to apply steady pressure and avoid over-tightening. Over-tightening can strip the threads or even break the screw, compromising the connection.
Drilling and fastening techniques also play a role in achieving a secure installation. Start by positioning the screw perpendicular to the metal surface to ensure it enters straight. Apply consistent pressure as you drive the screw in, allowing it to cut its threads without forcing it. If you encounter resistance, back the screw out slightly and then continues driving it in to avoid stripping the threads. Once the screw is fully seated, check that it is flush with the metal surface and secure.
Conclusion
Self-tapping screws are a versatile and effective solution for fastening metal with precision and strength. By understanding the different types of self-tapping screws, their advantages, and best practices for installation, you can ensure a strong, secure connection in your metalworking projects. Whether you’re working on a large-scale construction project or a simple home improvement task, self-tapping screws offer the durability, efficiency, and cost-effectiveness needed to get the job done right.
You may also like to read the following article: