When constructing a garage floor, the thickness of the concrete slab is crucial for ensuring durability and strength. You may have thought “How Thick Should a Garage Floor Be?” Read our brief information on garage floor thickness in this blog.
For most standard garages, a slab thickness of four inches is generally recommended. This thickness typically provides sufficient support for standard vehicles and light trucks. In situations where heavier vehicles or additional loads are expected, a thicker slab might be necessary. Six inches or more can offer added strength and prevent potential cracking. Properly preparing the subgrade and considering reinforcement options, such as rebar or wire mesh, can also increase the longevity of the garage floor.
Taking these factors into account, homeowners can make informed decisions about the appropriate thickness for their garage floor. Ensuring the right slab thickness helps in achieving a long-lasting and sturdy foundation.
Determining the Optimal Thickness for Your Garage Floor
The ideal thickness of a garage floor largely depends on how the garage will be used and the strength of the concrete mix used. Specific guidelines can help ensure a durable and long-lasting slab.
01. Evaluating Use and Load Requirements for Garage Floor
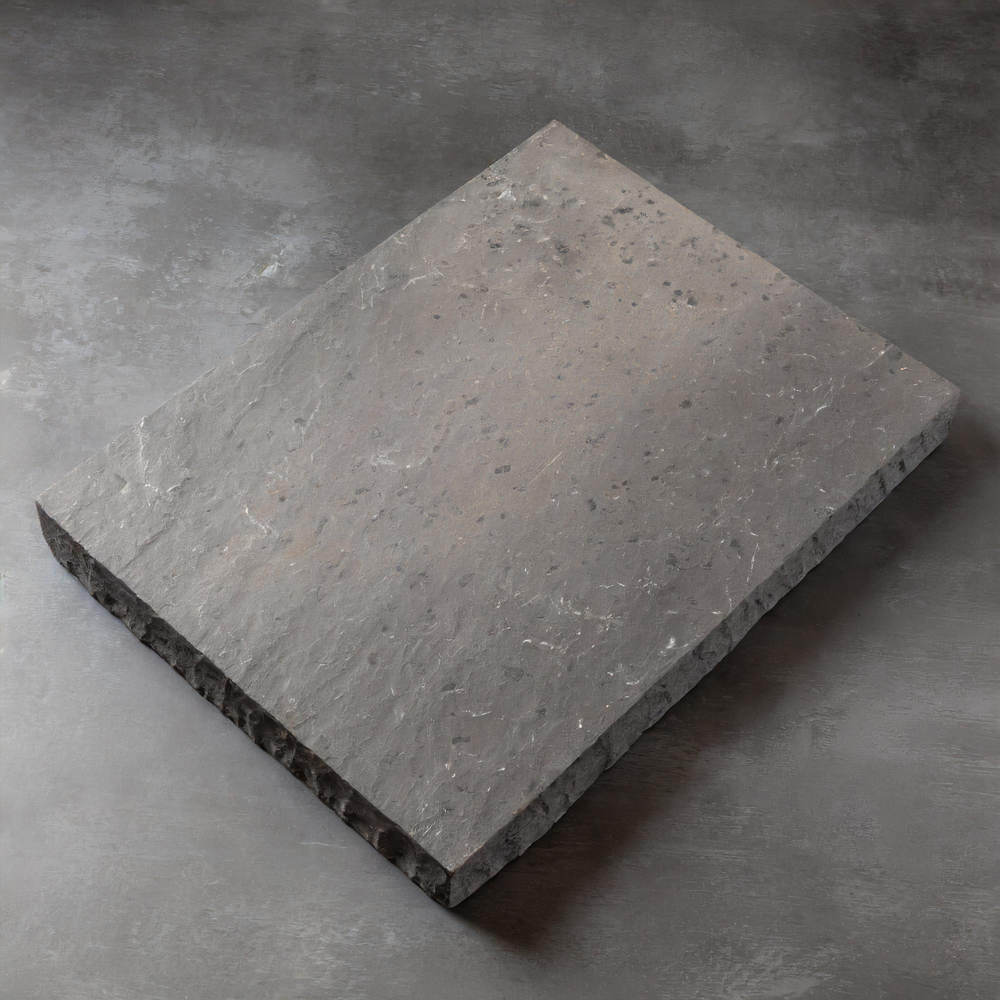
The first step is to assess the intended use of the garage. Metal garages and heavy-duty garages often require thicker slabs due to increased load demands. For standard residential garages, a thickness of 4 inches is typically sufficient.
For garages that will house heavy vehicles like trucks or boats, 6 inches is generally recommended. This extra thickness provides additional support and reduces the risk of cracking.
US Patriot Steel buildings or commercial garages might require even thicker slabs, possibly ranging from 6 to 8 inches. It’s vital to consider the cumulative weight of all stored items and vehicles when determining thickness.
02. Understanding Concrete Strength and Composition
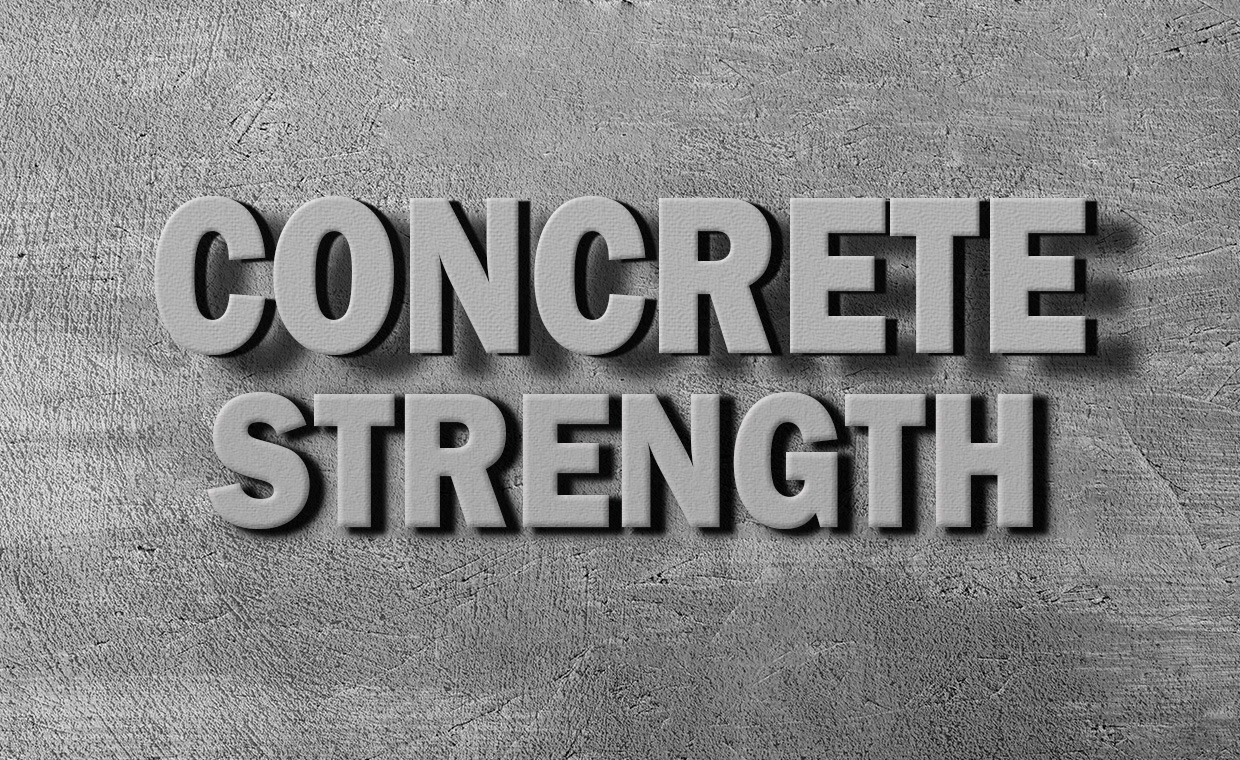
Concrete strength is another critical factor in determining slab thickness. A typical concrete mix for residential garages has a compressive strength of 3,000 to 4,000 PSI (pounds per square inch). This range is usually adequate for most applications.
For areas prone to severe weather or heavy usage, higher-strength concrete mixes may be warranted. Reinforcing the slab with rebar or steel mesh can also enhance its durability.
Using air-entrained concrete can improve the slab’s resistance to freeze-thaw cycles, making it a good option for colder climates. This reduces the likelihood of cracks forming over time.
Proper curing practices also play a role in achieving optimal strength, so ensure the slab is adequately cured before use.
Constructing a Resilient and Long-lasting Garage Slab
Constructing a resilient garage floor slab involves properly preparing the subgrade, employing best practices for concrete pouring and curing, and using reinforcements like rebar and wire mesh.
01. Proper Preparation of the Subgrade
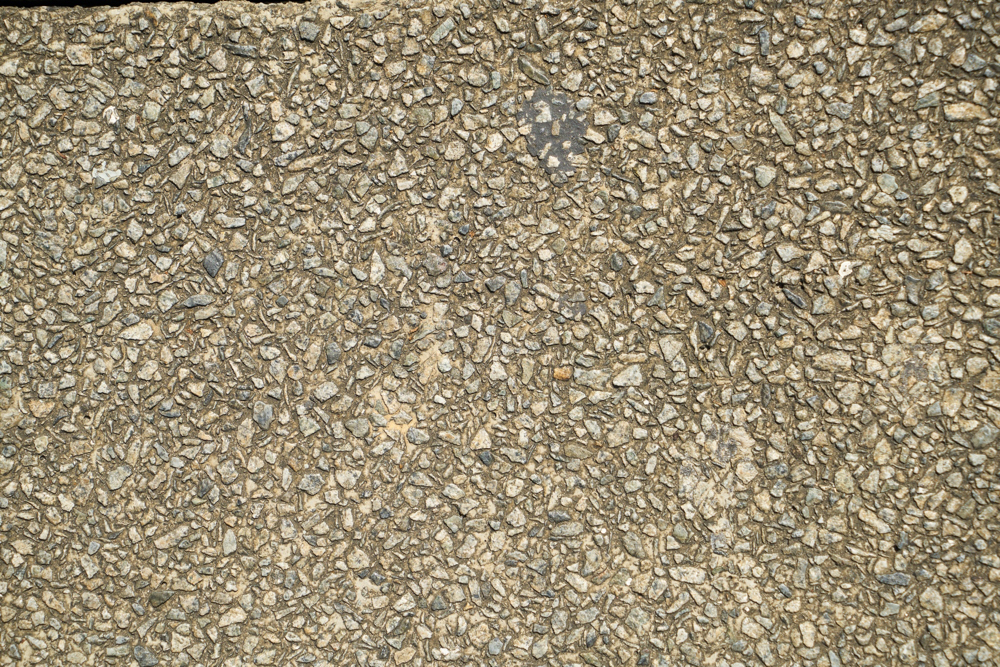
The subgrade is the foundation of your garage slab and must be stable and compacted. Begin by removing any vegetation, debris, or organic material. This ensures a clean base.
Gravel is often used as a base layer, providing drainage and stability. Spread and compact it to prevent settling. The thickness of the gravel layer typically ranges from 4 to 6 inches.
Moisture control is essential. A vapor barrier, usually made of plastic sheeting, should be placed between the gravel and the concrete. It prevents ground moisture from seeping into the concrete, which could compromise its strength and longevity.
02. Best Practices for Concrete Pouring and Curing
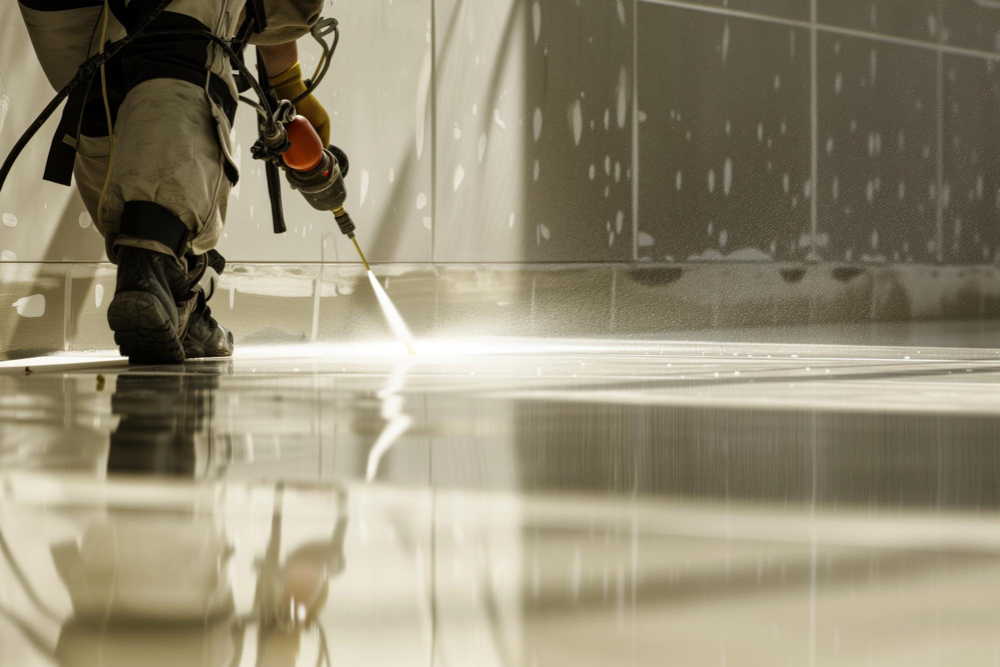
When pouring concrete, timing and consistency are vital. The concrete mix should have the right proportions of cement, sand, gravel, and water. Too much water weakens the concrete.
Pour the concrete continuously to avoid cold joints. Use a screed to level the surface, and then a float to smooth it.
Proper curing is essential. After finishing the surface, cover the slab with a curing compound or wet burlap sacks. Keep it moist for at least 7 days. This process prevents cracking and enhances strength.
03. Reinforcements: The Role of Rebar and Wire Mesh in Garage Floor Slab
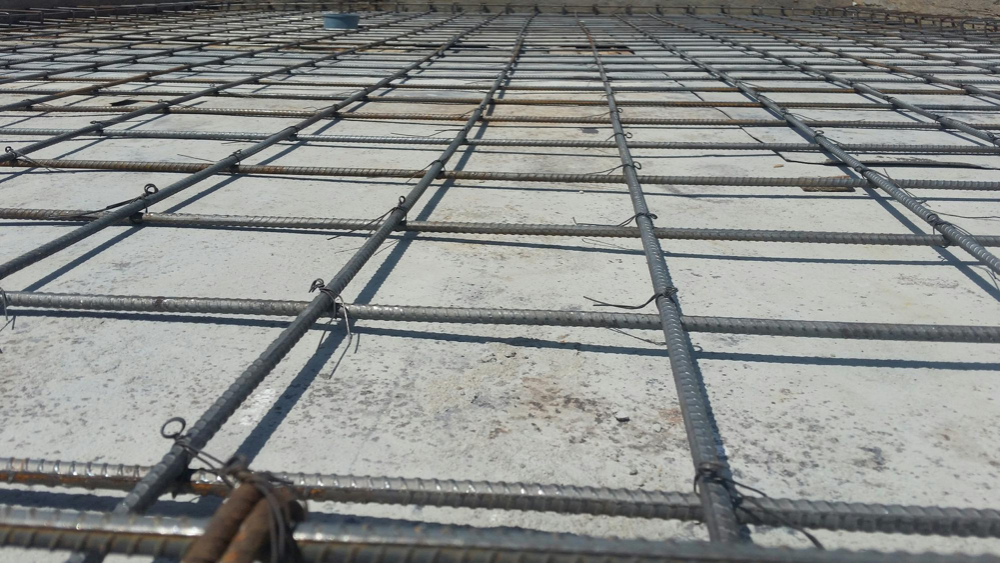
Reinforcements like rebar and wire mesh add tensile strength to the concrete. Rebar is typically used in a grid pattern, placed at approximately 12 inches apart. Use rebar chairs to keep it positioned correctly within the slab.
Wire mesh, often made of steel, provides additional support. Lay it on top of the rebar before pouring concrete. This combination enhances the slab’s ability to bear loads, making it suitable for heavy vehicles and metal building structures.
Effective reinforcement ensures the slab can resist cracking and shifting, contributing to its longevity and durability.
Hope this blog will helpful for your next garage floor construction. If you want to read more such similar articles, then please refer the following blogs:
7 Steps for Building a Beautiful GarageSetting up the Perfect Home Garage for Working on Your Car!