The construction industry comprising a wide range of high-risk activities involving construction, alteration, remodeling, repair, etc. is highly hazardous. Construction workers are routinely engaged in several activities that expose them to severe hazards, such as falling from heights, electrocutions, unguarded machinery, inhaling harmful silica dust and asbestos particles, and getting struck by heavy construction equipment. Thus, practising a safe work culture is extremely important to ensure a safe work environment.
Construction Safety
Construction safety principle adhered to and enforced by safety managers. It results from safe equipment usage, regular site inspections, worker protection from hazards, and risk assessments. The main aspect of construction safety is compliance with the safety and health regulations of the area.
Why Construction Safety Matters the Most?
Besides compliance with site safety and health regulations, the other benefits of construction safety include reducing the number of safety hazards and incidents.This is crucial since safety hazards and accidents not only lead to a loss in the company’s reputation among industry professionals and regulatory agencies but can also incur huge financial costs for the company in terms of loss of productivity, liabilities, and compensations. Apart from penalties for nearly all types of OSHA violations, other direct costs of incidents resulting in injuries are medical expenses and costs for legal services. Indirect costs include loss in productivity, repairs of damaged equipment or property, and training the replacement or substitute workers.
The main advantage of construction safety is that it helps to strengthen the trust between workers, construction safety managers, and company executives, leading to better communication across the company, resulting in fewer misunderstandings and conflicts. Construction safety initiatives not only increase worker productivity and efficiency but also make them more equipped to do their work effectively and safely.
Construction Safety Risks to Lookout for
In a dangerous industry fraught with high-risk activities, construction safety managers must know what to look out for and pay extra attention to ensure that workers remain safe and protected from harm.
01. Working at Heights
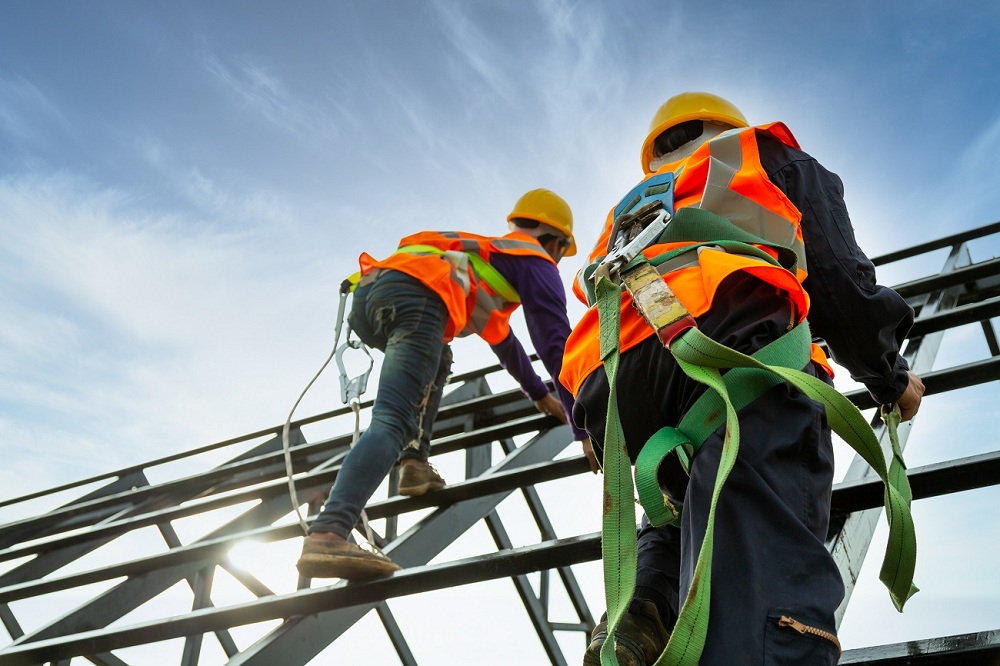
Carrying out construction work at an elevated height of 2 meters or more is one of the biggest causes of preventable work injuries and fatalities worldwide. Working at heights should be avoided as much as possible, but this may not always be possible for most types of construction work. To ensure the safety of workers performing construction work at elevated heights, construction safety managers must follow these steps:
- Inspect the nature of work and the team working onsite.
- Find the activities associated with working at heights.
- Identify possible risks like falling, slipping, or tripping.
- Assess controls such as planning, training, proper use of fall protection systems, and construction safety equipment.
- Workers must inspect safety harnesses before using them.
- Ensure that the equipment is in good condition for working at heights by checking the components such as lanyards, Tie-off adaptors/anchorages, and Horizontal lifelines.
- Scaffold inspections must be carried out accurately every seven days after installation by a scaffold-competent person.
- Create a ladder profile composed of the construction, type, class, length, weight supported, photos of the ladder, and its tag or label.
- Identify defects in ladder components such as the side rails, feet of the ladder, bolts and rivets, ropes, rung locks and spreader braces, steps, and rungs.
02. Falls, Slips, and Trips
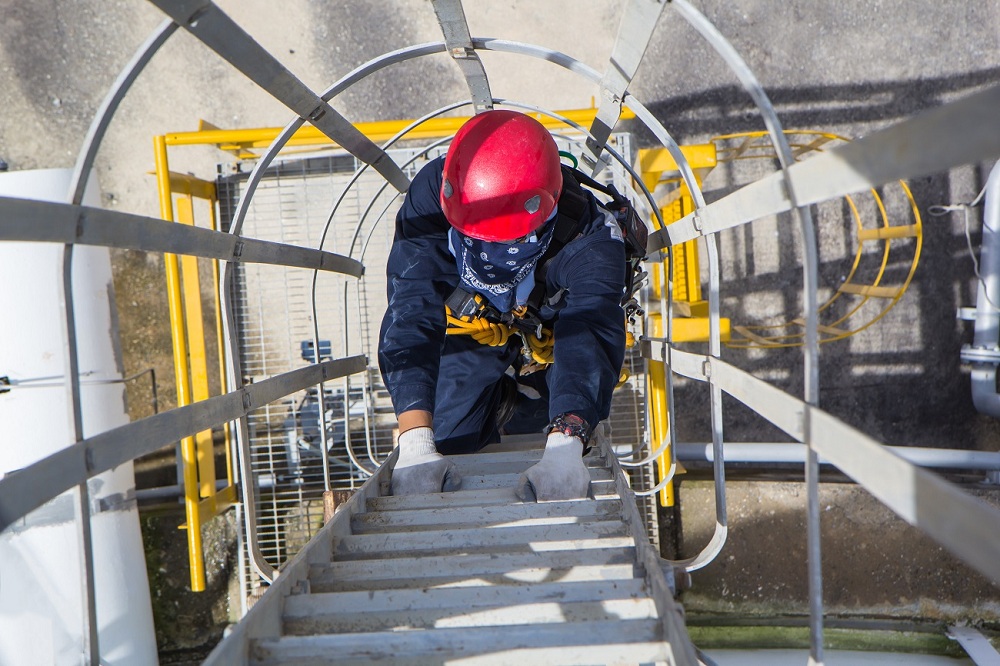
Falls, slips, and trips due to working at heights are often associated with ladders. Hence, ladder safety is vital in preventing such incidents, a reason why OSHA requires ladder inspections before initial use in each shift. Construction safety managers can meet this OSHA requirement by proactively catching issues that could lead to work-related injuries such as falls, slips, and trips.
03. Moving Equipment
Construction machinery or equipment used for lifting or lowering loads are greater threats to public safety than stationary scaffoldings and ladders. Hence, ensure that workers observe the proper safety procedures when operating, moving, or lifting equipment besides meeting regional requirements. Some standards like Occupational Safety and Health Administration (OSHA) require frequent, initial, and periodic crane inspections which must be conducted efficiently and regularly.
Construction safety managers must perform checks on connected electrical and hoisting equipment besides inspection, testing, and maintenance of overhead and gantry cranes. Daily Crane Inspection for tower cranes should be done before, during, and after operational shifts by recording work permits, evaluating operator competency, checking emergency controls, observing safety measures applied, and assessing post-job operation.
HSE requires LOLER inspections, to assess compliance with the Lifting Operations and Lifting Equipment Regulations 1998. Cranes, industrial lift trucks, hoists, and accessories for attaching loads are subject to these regulations, based on which the strength and stability of lifting equipment can be verified and their proper positioning and installation confirmed.
04. Noise
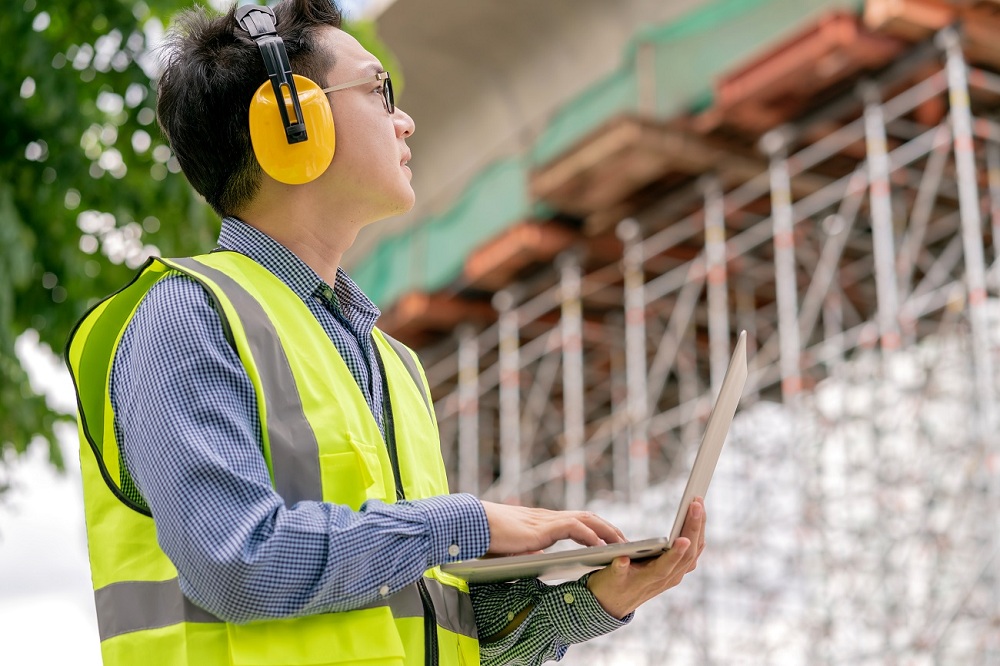
Excessive noise at work can result in people suffering from hearing conditions. Noise risk assessments in the construction industry can help identify the sources of these risks and their effects on the health and safety of workers.
05. Hand-arm Vibration Syndrome
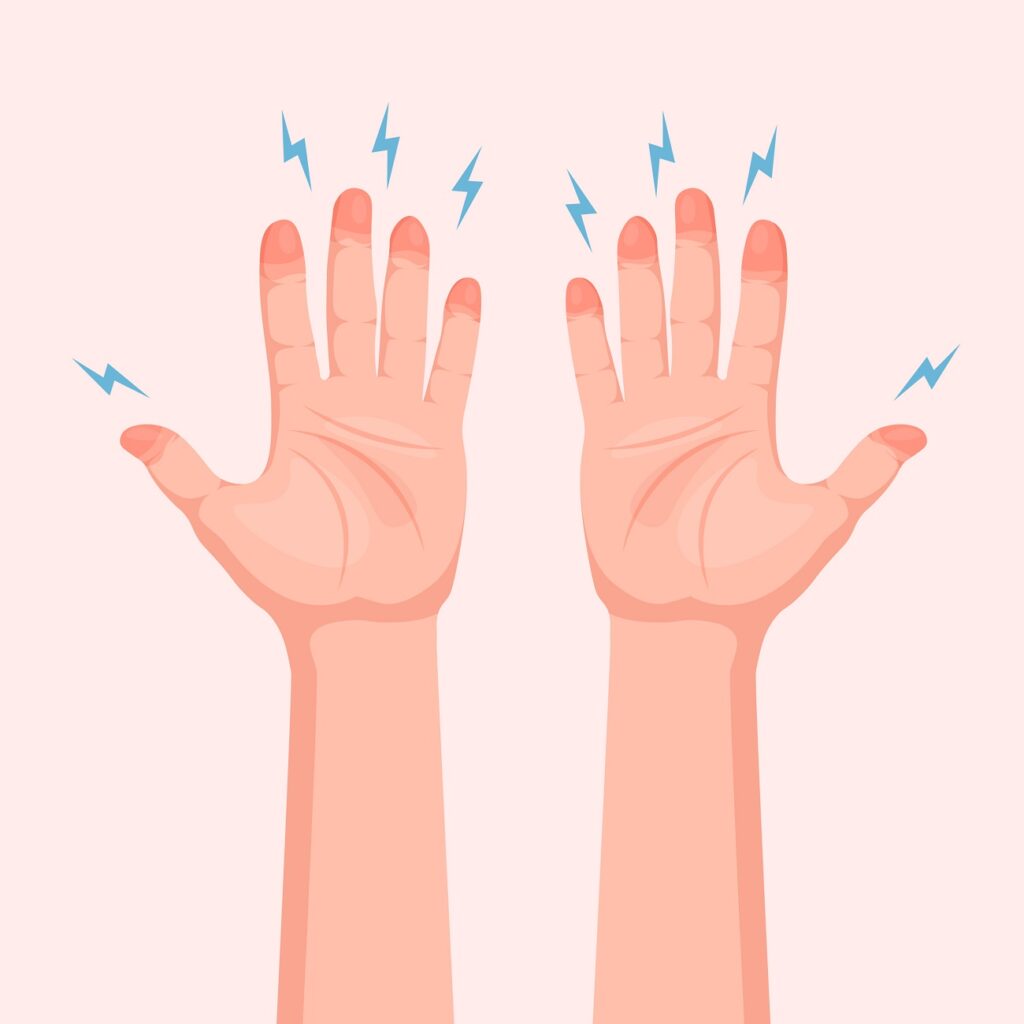
Hand-arm vibration syndrome (HAVS) affects the nerves and blood vessels of the hand. Due to the prolonged use of vibrating tools such as hammer drills, concrete breakers, and grinders, workers are at a greater risk of developing HAVS. Therefore, it is required to conduct regular HAVS assessments. Poor compliance with the regulations can result in huge penalties.
06. Manual Handling
Lifting, carrying, lowering, and moving objects during work operations fall under manual handling. Besides hand-arm vibration, high-risk manual handling involves sustained, repetitive, high, or sudden force, sustained or awkward posture, repetitive movement, and whole-body vibration. To protect workers from musculoskeletal disorders such as HAVS, rotator cuff injuries affecting the shoulder, and epicondylitis affecting the elbow, an assessment of the risks of manual handling is necessary.
07. Collapsing Trenches
According to OSHA, trenching work poses a serious risk to all workers involved. Collapsing trenches or cave-ins are more likely to result in worker fatalities than other excavation-related incidents. Construction safety managers should perform daily excavation risk assessments to mitigate this risk. They must ensure that workers enter trenches only after adequate protection measures such as benching, sloping, shoring, and shielding. They should evaluate the safety of an excavation site by checking access areas, spoil placements, protection systems, surface crossing, and water management.
08. Electricity
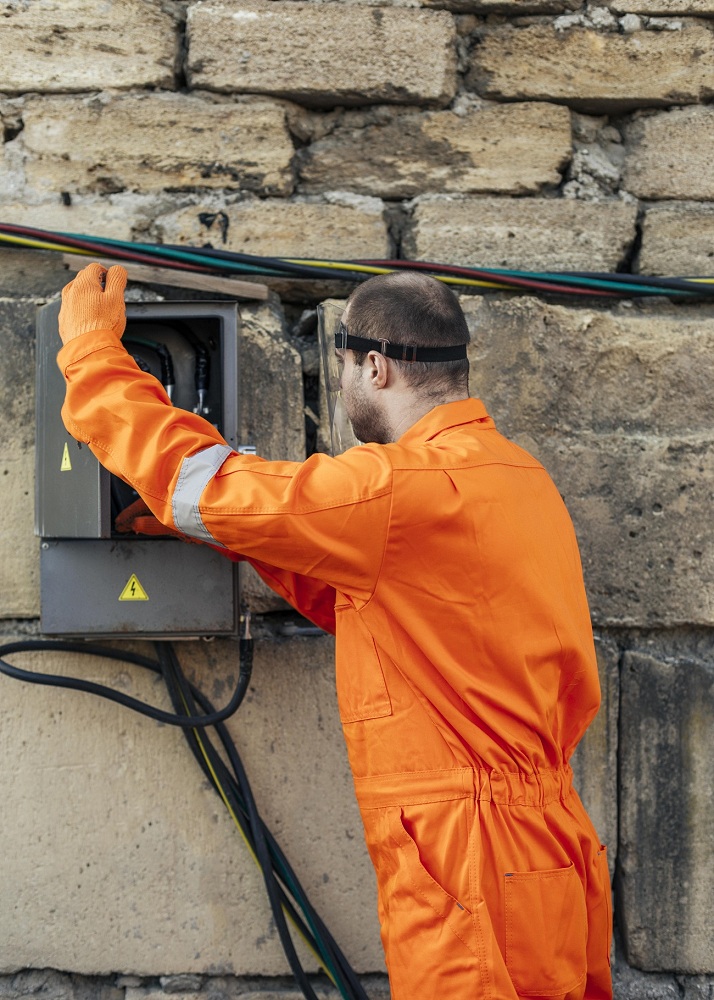
Exposure to electricity resulting in electrocutions is a deadly construction safety risk. One of the major causes of electrocutions among construction workers is the lack of basic electrical safety knowledge while handling electrical equipment. Construction safety managers should conduct frequent electrical inspections and maintenance checks as a preventative measure against electrocutions and other dangerous exposures to electricity, thus helping their company comply with OSHA standards on electricity.
09. Asbestos
According to the HSE, the risk assessment must be performed before any work involving asbestos begins, due to the high fatality of diseases caused by asbestos. Construction safety managers should remember that failure to implement the appropriate controls and failure to conduct asbestos inspections may lead to the company being reported to HSE or the enforcing authority in their region or may result in costly penalties for non-compliance with regulation. Construction safety managers should track their progress in asbestos management, ensuring that the presence of asbestos is properly identified and planned for.
10. Dust
Blasting, drilling, cutting, grinding, and polishing of common construction materials such as tiles, bricks, mortar, and concrete generate hazardous dust on construction sites. Prolonged and heavy exposure to silica dust can cause silicosis, lung cancer, and chronic obstructive pulmonary disease (COPD). Construction safety managers should perform dust risk assessments to regulate the emission of silica dust from construction tasks as construction workers are a high-risk group, thus complying with the Control of Substances Hazardous to Health (COSHH) Regulations of 2002.
Hence, adopting the above-mentioned protocols and safety measures will not only ensure a safe work environment on your construction site but also preserve your reputation, help you meet safety standards, and prevent loss of production and financial losses in terms of compensations and liabilities. Because construction safety matters!
Before you leave, don’t miss to read the following article: