Ready-mix concrete offers significant advantages in construction projects where on-site concrete preparation is impractical or uneconomical. It provides versatility in strength and workability, delivered in precise quantities with tailored mixes. Outsourcing production to specialist’s streamlines logistics and ensures quality assurance.
Batching and mixing of the ready-mix concrete take place in controlled environments, allowing for precise customisation and rigorous testing. Admixtures further enhance properties and application versatility. Its time-sensitive nature requires prompt placement after batching. Various methods, including transit mixers and pumps, facilitate on-site delivery. Notably, its durability and lifespan outperform alternative materials, making it a preferred choice for long-term infrastructure projects.
How is Ready-Mix Concrete Made?
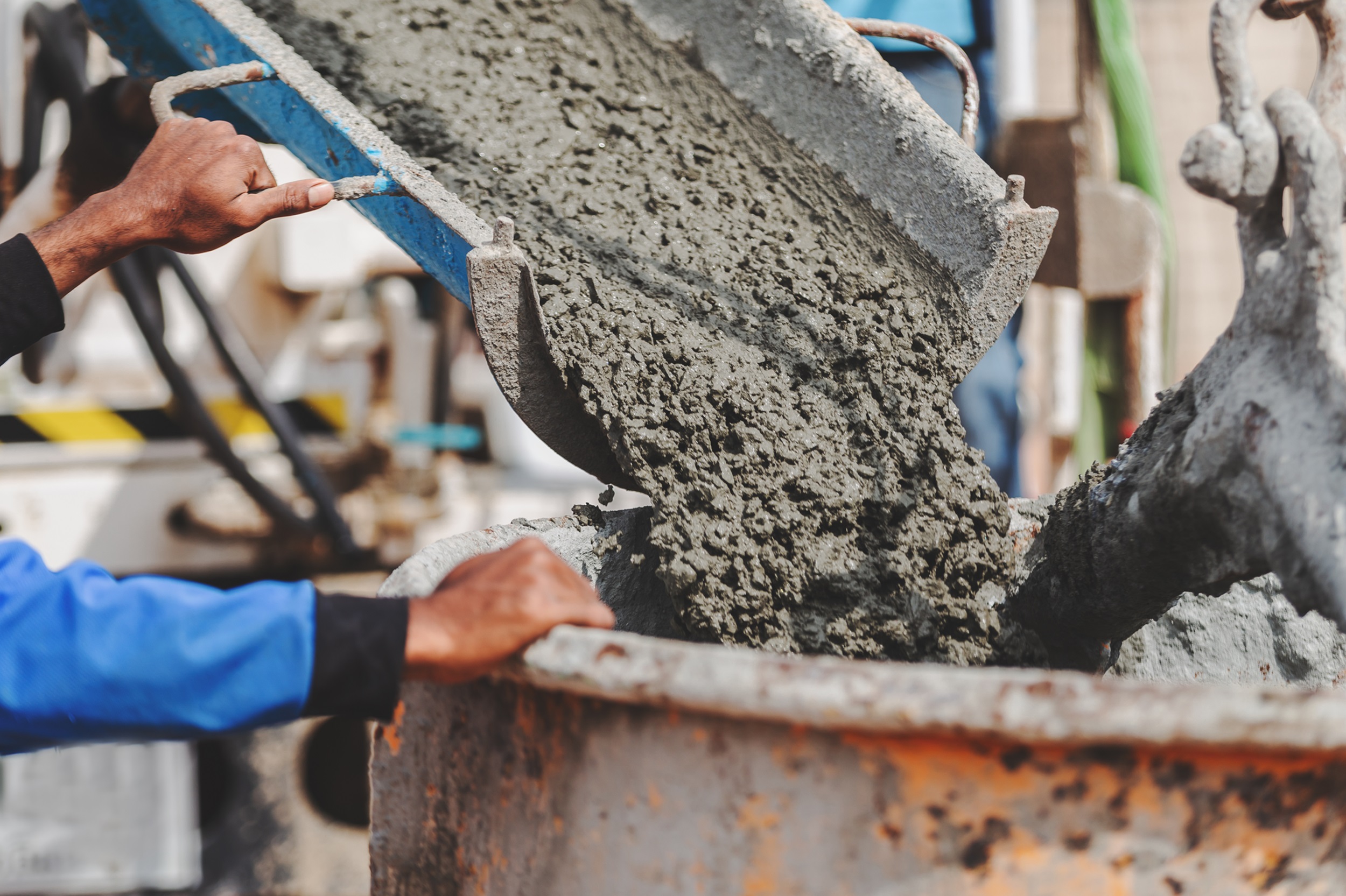
Firstly, a paste is prepared by combining water and cement, which covers and binds together aggregates (which include rocks and sand) to produce the mass known as concrete. These proportions must be carefully harmonised to generate a durable product with the appropriate amount of workability. In most cases, the concrete is produced in batches in the plant before it is mixed on the construction site.
Types of Ready Mixed Concrete
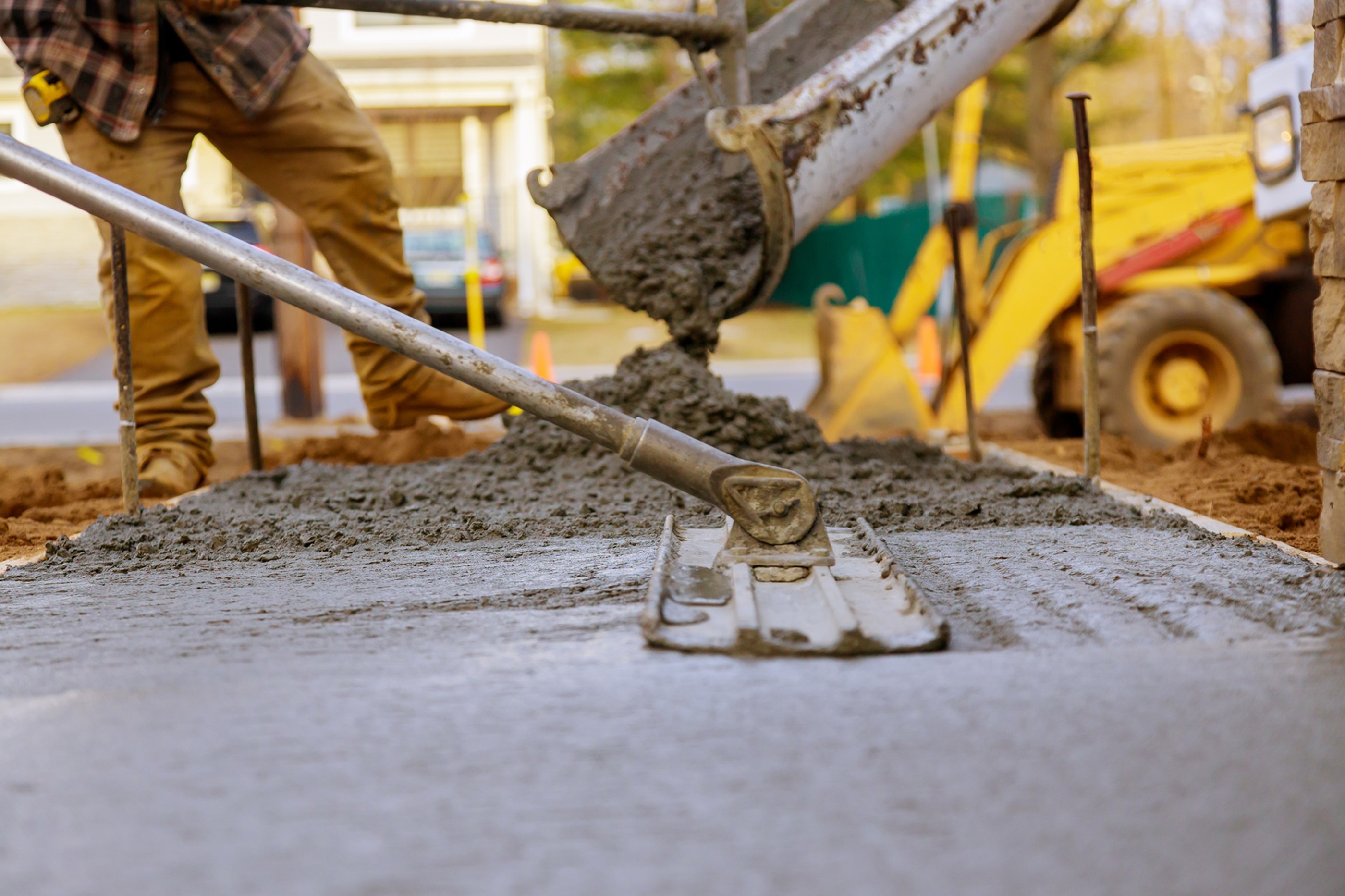
There are three varieties of ready-mixed concrete (RMC) based on various materials.
Transit Mixed Concrete
Ready-mix concrete, known as dry-batched concrete, involves charging all materials directly into the truck mixer. The mixer drum moves swiftly during loading and then slowly for agitation. Three methods include on-site mixing with varying drum speeds, mixing during transit with medium speed, and yard mixing with fast drum speed.
Shrink Mixed Concrete
The concrete is half-blended in the plant mixer before levelling in the truck drum mixer throughout transportation. The blending done in the central mixing plant determines the amount of blending inside the transport mixer. Tests are conducted to estimate the mixing demands of the drum mixer.
Central-Mixed Concrete
Because the concrete is mixed before being delivered into a truck mixer, it is also called a central batching plant. A wet-batch or pre-mix factory is another name for this facility. While moving the concrete, the truck mixer acts as an agitator. Non-agitating machinery or dump trucks are used when the workability requirements are low or the lead time is short.
Fundamental Characteristics of Ready-Mix Concrete
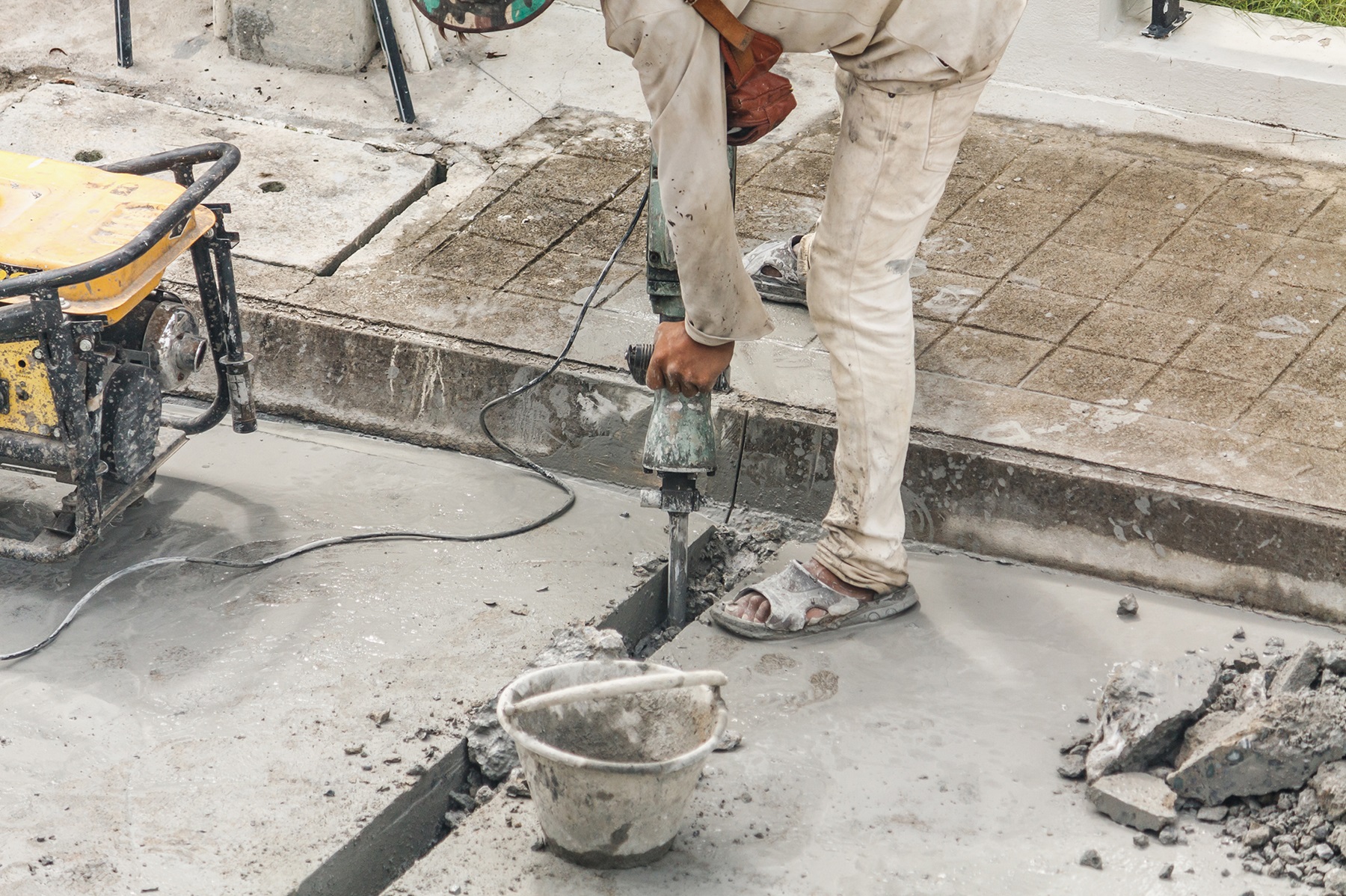
Mix Design
- Most ready-mix concrete is weighed, and all material proportions are placed in the mixing bin based on weight.
Setting Time
- The setting time for typical concrete is around one hour.
- However, in usual operations, placing the concrete further into slabs, walls, columns, mat foundations, and other structures will take more than an hour.
Admixtures
- At the batching plant, various admixtures are added to ready-mix concrete.
- The specifications of the suppliers determine the technique of adding admixtures.
Slump at Batching Plant and Site
- After mixing, the concrete is placed into the truck, and a sample is obtained to assess the slump. The plant’s collapse is noted in the delivery note that the engineer on site must produce.
- A slump test ensures the slump is correct when ready-mix concrete is transported to the job site. The design slump stated in the mix design is the slump at the location. If other conditions are met, concrete might be used if it’s within the guidelines.
Concrete Temperature
- To achieve a low level of hydration, it is necessary to manage the temperature of the ready-mixed concrete. Lowering the temperature of the ready-mix concrete involves several steps. Here are a few examples:
- Concrete mixing is done with cold water.
Aggregate
- No changes to the aggregate shall be made after a mix design has been completed, and trial mixtures have been completed (tested cubes for 7 days and 28 days).
- As we all know, if we modify the material sources (not just the aggregate but also additional additives), the mix design will change, and the trial mix findings will no longer be relevant.
Quality of Ready-mixed Concrete
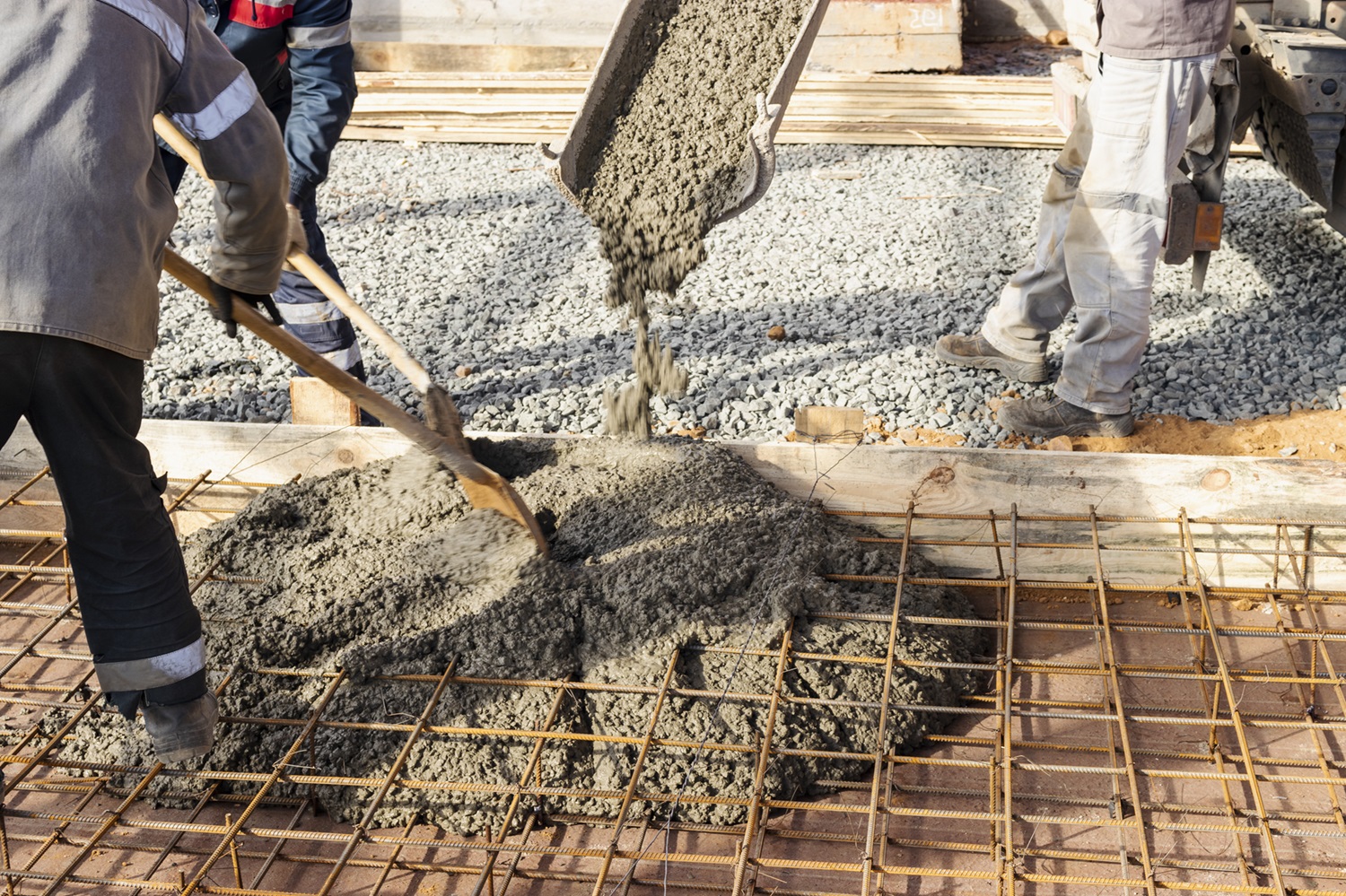
Ready-mix concrete operations require regular truck cleaning and inspection of compression machines. Precautions like enclosing water storage ponds ensure safety. Quality assurance involves analysing materials and performing sieve analysis. Continuous agitation during transport prevents concrete settling. Consider lead distance while adding admixtures. Skilled labour and continuous concrete availability are essential for efficient concreting operations.
What Is Ready-Mix Concrete Used for?
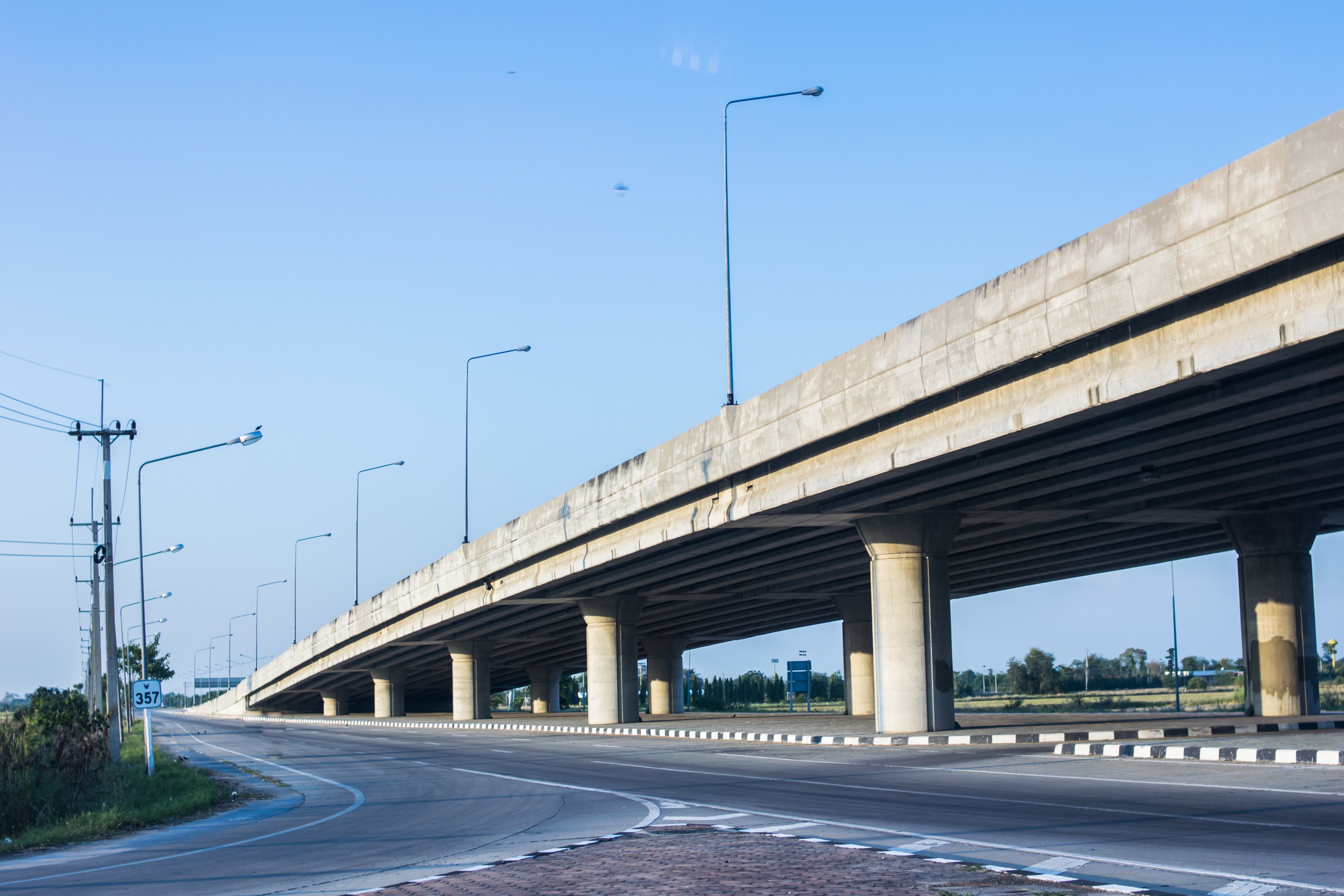
Construction projects, roadway development, foundations, bridges, walls, floors, foundations, driveways, and footpaths are just a few of the many construction applications for ready-mix concrete. The strength and ease of ready-mixed concrete can assist in any construction that demands a lasting material and versatility in properties.
Conclusion
Ready-mix concrete (RMC) is increasingly favoured in construction for its environmental friendliness, superior quality, and low maintenance requirements. Its enhanced durability makes it ideal for industrial use. However, proper site preparation and equipment readiness are crucial when working with ready-mix concrete to ensure efficient and safe operations.
Author Bio
Mira Zala – Mira Zala is a civil engineer by profession and an avid content writer. She graduated from S.S. Gandhi Degree Engineering College, Gujarat. She loves to write blogs on building materials, gardening and technology. Apart from writing, she loves singing and painting.