Table of Contents
Prestressed concrete is a type of concrete designed to be stronger and more durable than conventional concrete. It is made by applying compressive stress using high-strength steel cables or tendons. This process pre-stresses the concrete, allowing it to withstand larger loads and stresses without cracking or failing. It is used in construction to increase the strength and durability of concrete structures, especially when they are expected to bear heavy loads or stresses, such as in the construction of bridges, long-span floors, and other similar structures.
Prestressing can be applied after the concrete member has gained sufficient strength by tensioning cables inserted into cast-in ducts, a method known as post-tensioning. In contrast, pre-tensioning is accomplished by stretching wires or strands, called tendons, between two anchorages to a predetermined tension before placing the concrete.
Advantages of Prestressed Concrete
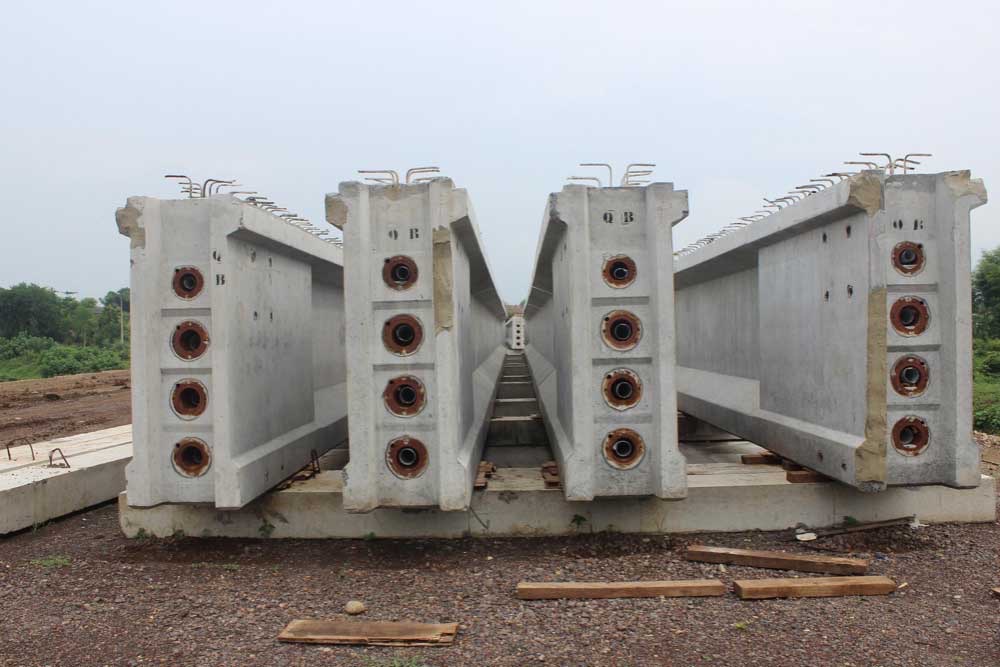
There are several benefits to using prestressed concrete in construction:
- Increased Strength: Prestressed concrete has higher tensile strength and load-carrying capacity than conventional concrete, making it suitable for structures subjected to heavy loads or stresses.
- Durability: It is less likely to crack or deform under load compared to conventional concrete.
- Reduced Maintenance: Prestressed concrete requires less maintenance over its lifetime, as it is less prone to cracking or other forms of deterioration.
- Longer Span Length: It can span longer distances than conventional concrete, making it suitable for constructing bridges, long-span floors, and other structures.
- Protection Against Cracks: Both concentrically and eccentrically applied compressive prestressing forces along the member’s longitudinal axis help to prevent cracks, especially at mid-span, and enable the structure to sustain its weight under normal use.
- Better Performance: Prestressed concrete allows the full compressive strength of the concrete to be utilised throughout its depth under full loading.
- Improved Construction Efficiency: Post-tensioned slabs, which are capable of supporting their own weight while being stressed, can significantly boost construction efficiency. Contributing factors include:
- Less impact on other industries and less material handling
- Reduced soffit complexity with drop caps and panels
- Better access to lower slabs is achieved by faster shoring removal
Disadvantages of Prestressed Concrete
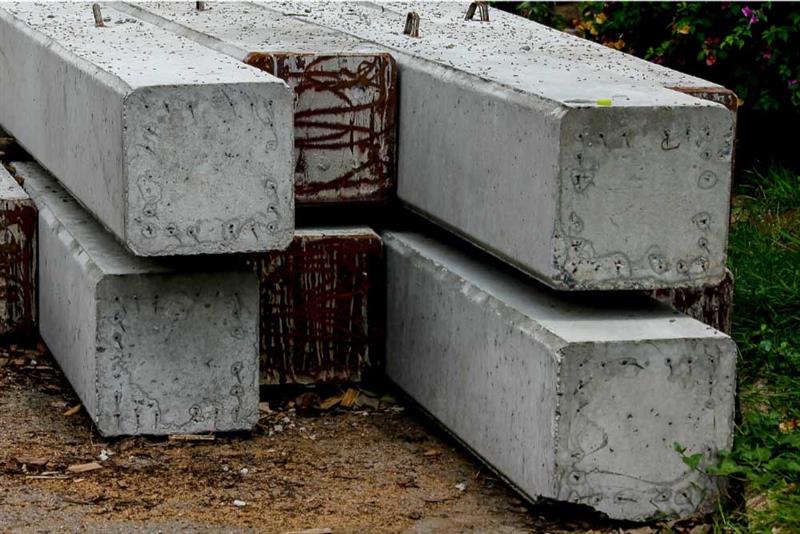
The following are the prestressed concrete disadvantages:
- High Initial Cost: Due to the specialised equipment and techniques required, the initial cost of constructing a prestressed concrete structure is often higher than that of a comparable reinforced concrete structure.
- Limited Shape Options: Prestressed concrete elements are typically made using moulds, which can limit the range of shapes and sizes that can be achieved.
- Complex Construction Process: The construction of prestressed concrete is more complex than that of reinforced concrete. It requires specialised equipment and trained personnel, which can increase the overall cost of the project and may lead to delays.
- Loss of Prestress: Over time, prestressed concrete can lose some of its prestress due to creep, shrinkage, and tendon relaxation. This can reduce the load-carrying capacity of the structure and may require additional maintenance or repairs.
- Sensitivity to Temperature Changes: Prestressed concrete is more sensitive to temperature changes than reinforced concrete and can experience more significant contraction and expansion. If the structure is not designed and constructed properly, this can lead to cracks and other forms of damage.
Despite these drawbacks, prestressed concrete remains a versatile and durable construction material, widely used in various applications.
Types of Prestressed Concrete
There are several types of prestressed concrete, including:
1. Pre-Tensioned Concrete:
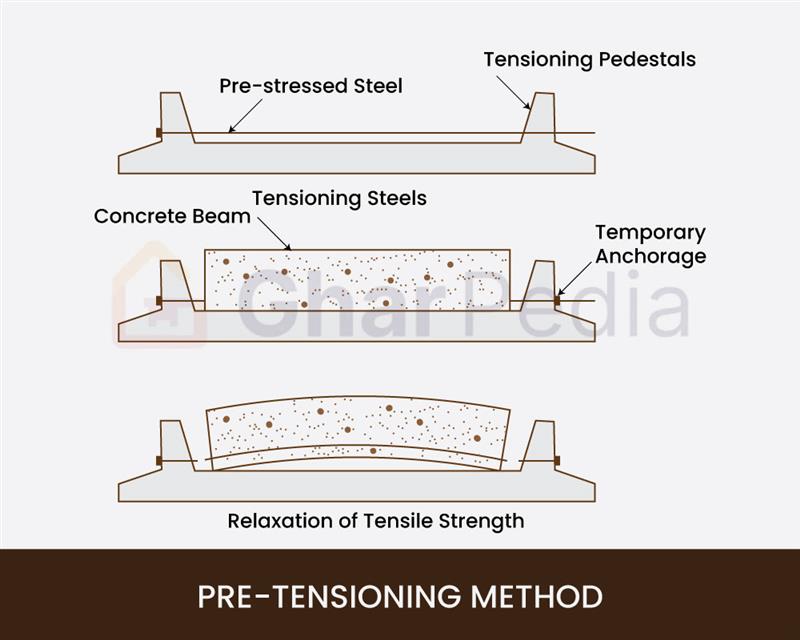
In pre-tensioned concrete, the prestressing tendons are tensioned before the concrete is cast. Once the concrete has hardened, the tendons are anchored to the structure, and the tension is transferred to the concrete. Wires or cables are stressed before being anchored at the end of a metal form, which is used to create prestressed concrete.
The wire is stressed using hydraulic jacks, typically with an extra 10% tension to account for creep and other prestress losses. After the wires are tensioned, the side moulds are secured, and the concrete is poured. As the concrete hardens and shrinks, it applies a compressive force along the length of the steel, effectively transferring the tension from the jacks to the concrete. The wires are unhooked from the jacks once the concrete has attained the required strength. The minimum strength of pre-tensioned concrete should be 40 N/mm2.
Regarding the mechanism, the tendon in pre-tensioned concrete is protected from corrosion and direct tension transfer is possible. Static friction causes the tension to be transferred from the bars to the concrete as compression when the concrete has hardened and adhered to the bars. However, it calls for strong anchoring sites between which the tendon is to be stretched, and tendons are often aligned straight.
As a result, the size of pre-tensioned concrete elements is limited by the fact that they must be manufactured at a factory and then transported to the construction site. Despite this limitation, pre-tensioning is beneficial for various structural components such as balcony posts, lintels, floor slabs, beams, and even foundation piles.
2. Post-Tensioned Concrete:
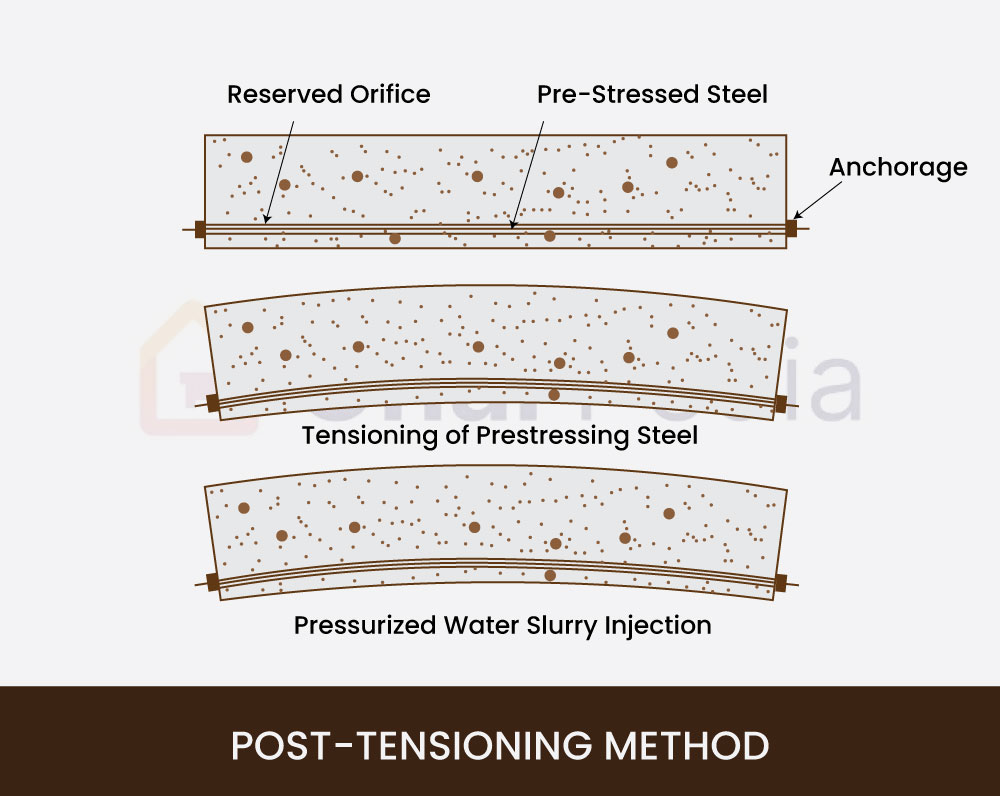
In post-tensioned concrete, the tendons are left unbonded and are tensioned after the concrete has hardened, typically using hydraulic jacks. Here, the unstretched steel is enclosed by the concrete, but does not bond with it. Ducts, often created using thin-walled steel tubes, are placed within the concrete unit to house the tendons. Once the concrete has achieved the desired strength, the steel tendons are inserted into the ducts and then tensioned against the concrete structure. This is the method of choice for large-scale construction projects such as bridges and floor slabs, which require cast-in-place installation. For post-tensioning, minimum grade of concrete used is M30.
Post-tensioned concrete can be further classified into two types: bonded and unbonded.
Bonded Post-Tensioned Concrete:
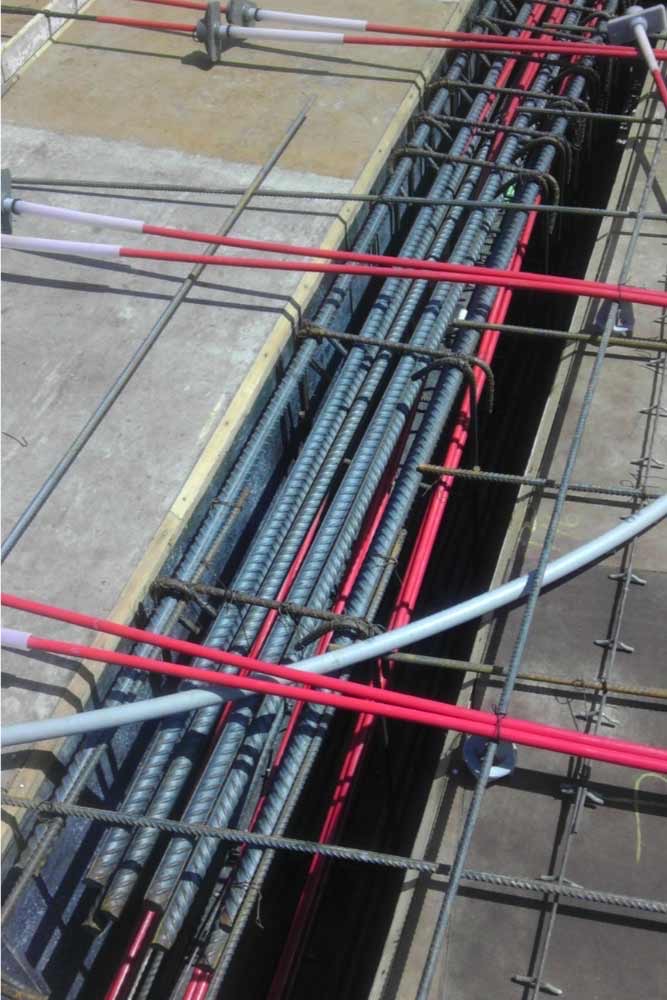
In bonded post-tensioned concrete, the tendons are coated with a sheathing material, which bonds to the concrete as it cures. This helps transfer the tension from the tendons to the concrete more effectively. Cement grout is used to fill the void between the duct and the tendon. The grouting technique significantly improves the steel’s resistance to corrosion. This strategy improves ultimate strength by enhancing resistance to live loads. The grout mixture is cement and water blended with or without additives, and does not contain sand.
Unbonded Post-Tensioned Concrete:
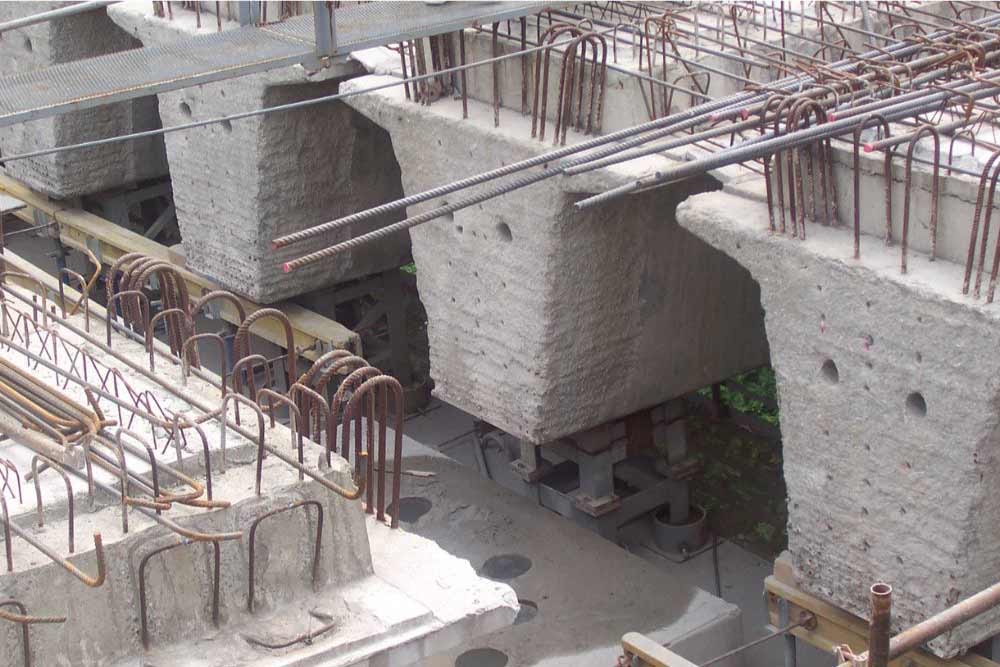
In unbonded post-tensioned concrete, the tendons are not coated with a sheathing material and are not bonded to the surrounding concrete. This allows the tendons to move independently within the concrete, which can be advantageous in certain applications. For a building to be unbonded, the gap between the duct and tendon must not be filled with grout. For this purpose, the steel has been galvanised to prevent corrosion. A waterproofing substance is utilised for galvanising. The biggest drawback of unbonded post-tensioning compared to a bonded system is safety: if a tendon breaks, such as during repair, it may lose tension suddenly and potentially burst out of ye slab.
Process of Implementation of Prestressed Concrete
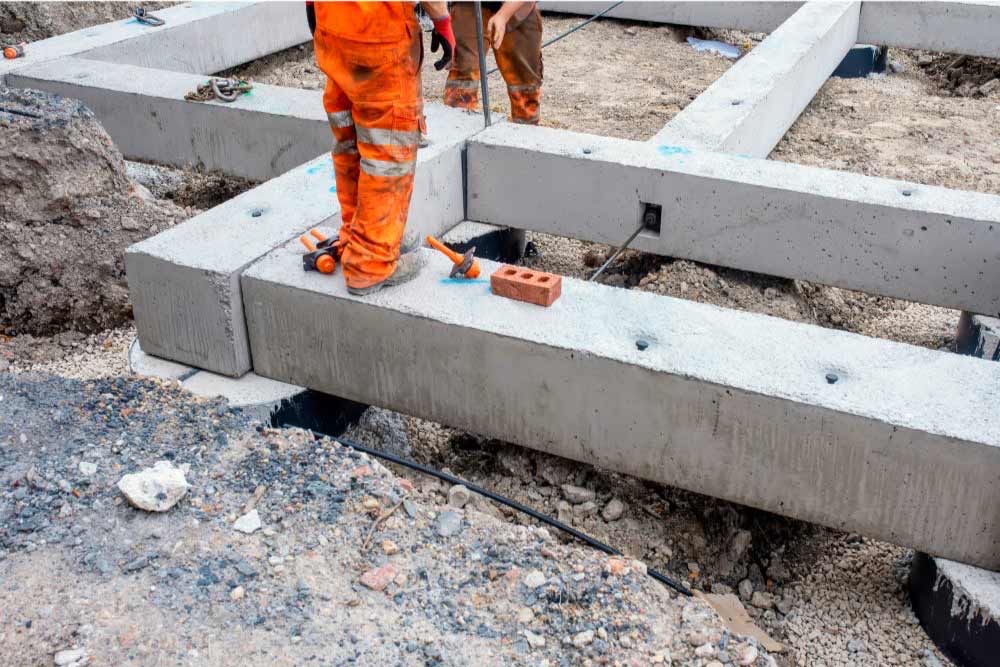
The process of implementing prestressed concrete in a construction project typically involves the following steps:
- Design: The step involves determining the size, shape, and configuration of the various structural elements, as well as selecting the type and arrangement of the prestressing tendons.
- Fabrication: Prestressing tendons are typically fabricated off-site using high-strength steel wire or strands. These may be pre-tensioned or left unbonded for post-tensioning.
- Casting: The concrete elements of the structure are cast using forms and mould, with careful attention given to positioning the prestressing tendons correctly.
- Curing: Depending on the size and complexity of the element, the concrete is allowed to cure for a specific period to achieve the required strength.
- Tensioning: In post-tensioned concrete, tendons are tensioned using hydraulic jacks after the concrete has cured.
- Anchoring: The prestressing tendons are anchored to the structure using mechanical or grouted anchors to maintain the applied tension.
- Finishing: The surface of the prestressed concrete elements may be finished with various materials, such as stucco, plaster, or tiles, to achieve the desired appearance.
Design Considerations of Prestressed Concrete
Several design considerations must be taken into account when designing a prestressed concrete structure, including the following:
- Loads: The design must account for all types of loads that the structure will be subjected to, including dead loads, live loads, wind loads, and seismic loads.
- Material Properties: The design must consider the properties of the materials used, including the strength and stiffness of the concrete, the strength and elongation of the prestressing tendons, and the strength and stiffness of any other materials used in the structure.
- Prestressing Force: The design must determine the appropriate level of prestressing force required to counteract the various loads on the structure and ensure its stability and durability.
- Shape and Size: The design must determine the optimal shape and size of the various elements of the structure, taking into account the loads, material properties, and prestressing force.
- Detailing: The design must include detailed drawings and specifications for the construction of the structure, including the placement of the prestressing tendons and the dimensions and properties of the various elements.
- Construction Method: The design must consider the construction method used, including the type of prestressing (pre-tensioned or post-tensioned) and the means of tensioning the tendons (hydraulic jacks or other mechanical devices).
Prestressed Concrete Applications
Prestressed concrete has several important applications in the construction industry, including the following:
- Buildings: Prestressed concrete is used in the construction of tall buildings with long spans, where it provides the necessary stiffness and stability to withstand various loads and forces acting on the structure.
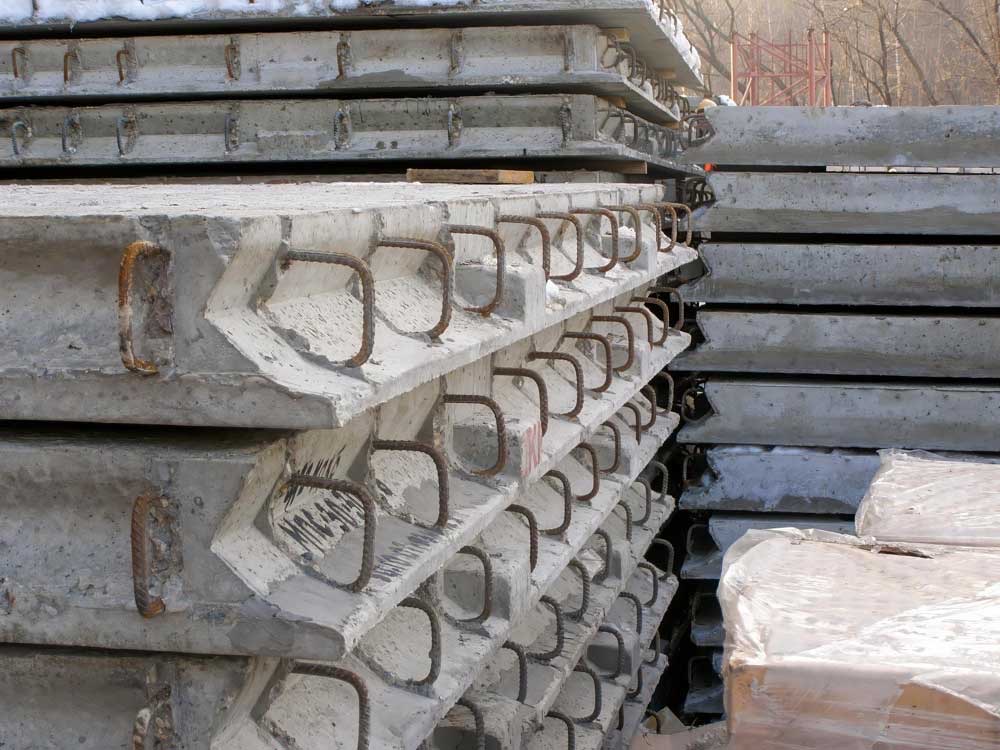
- Slabs: Prestressed concrete slabs are widely used in constructing floors, roofs, and other horizontal elements in buildings and other structures.
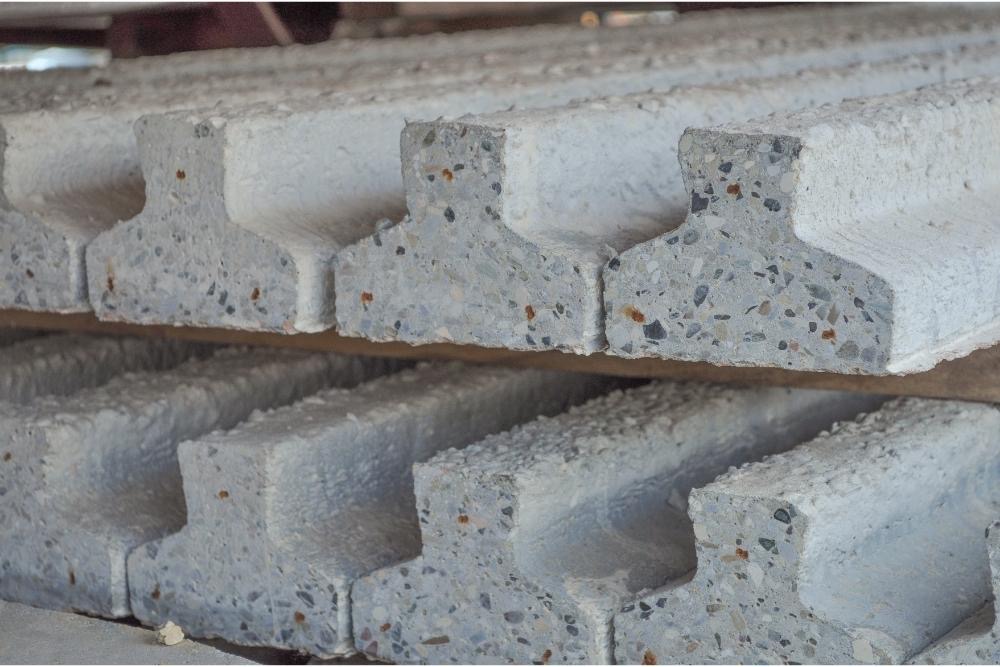
- Beams: Prestressed concrete beams are used in the construction of buildings, and other structures to support vertical loads.
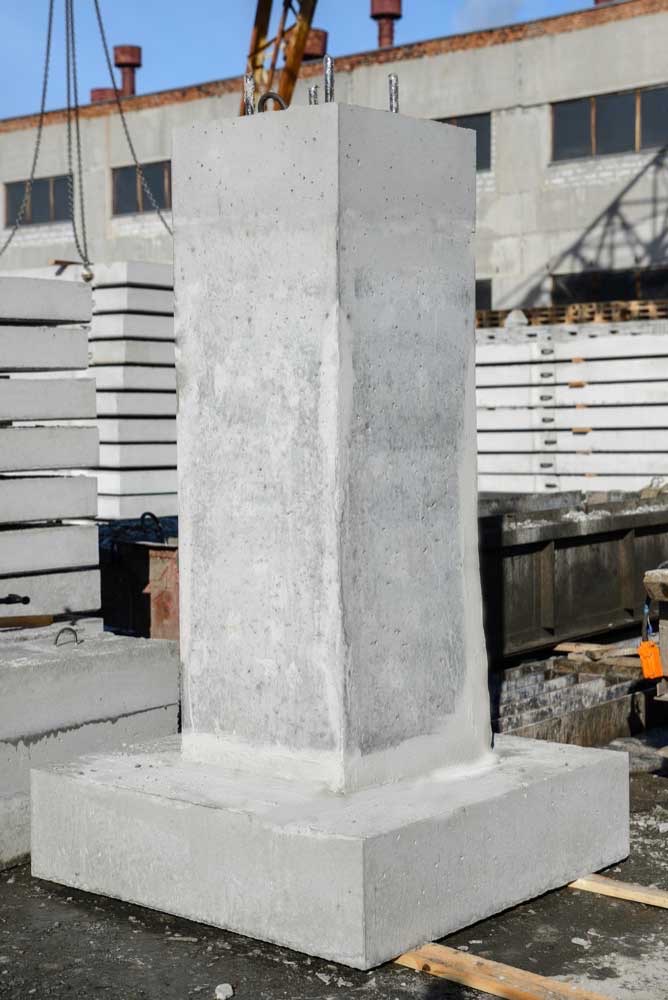
- Columns: Prestressed concrete columns support the loads from the beams and slabs in a structure and are commonly used in tall buildings and other load bearing structures.
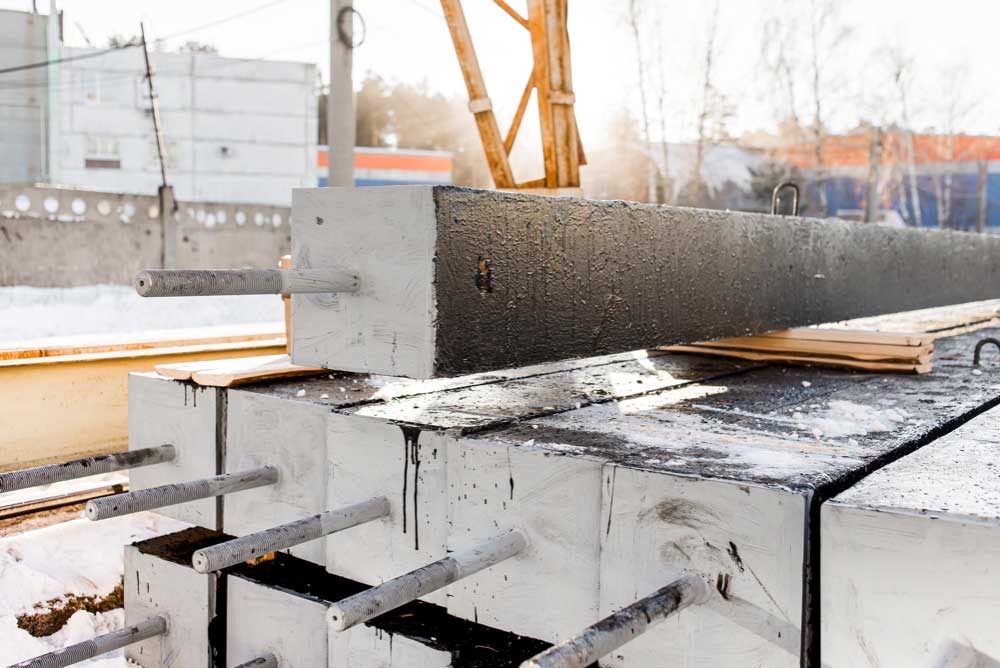
- Piles: Prestressed concrete piles are foundation elements used to transfer structural loads to the underlying soil or rock in the construction of buildings and other structures.
Read More: Types of Pile Foundation
Here are a few real-life examples of buildings that use prestressed concrete:
1. Sydney Opera House:
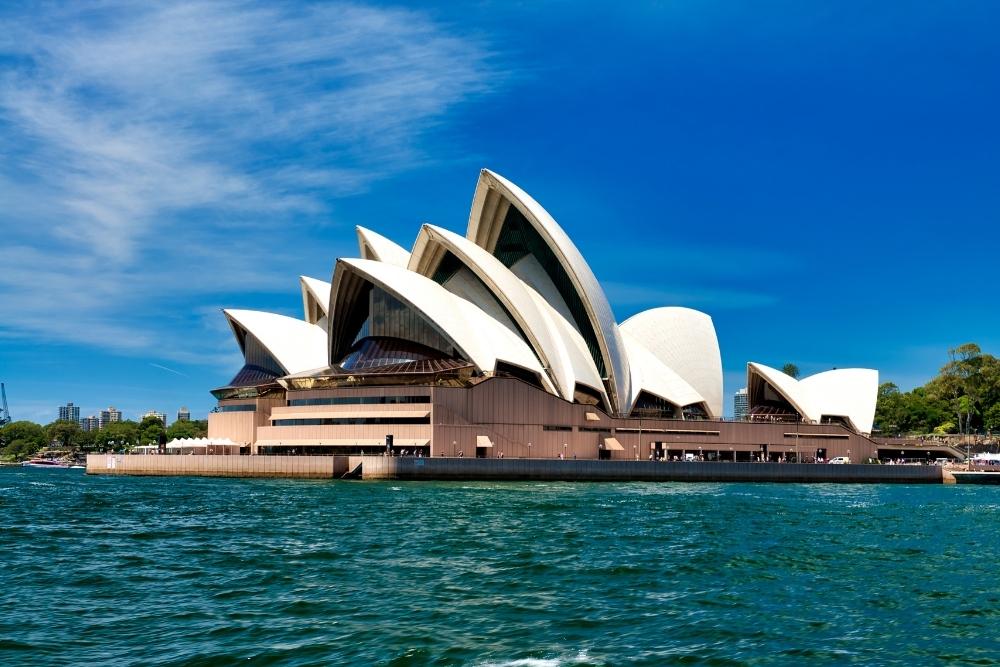
The Sydney Opera House in Australia is a world-famous performing arts centre that features a series of prestressed concrete shells as its roof structure. The shells, composed of prestressed concrete ribs and panels, are supported by a series of prestressed concrete beams and columns.
2. Kuala Lumpur Tower:
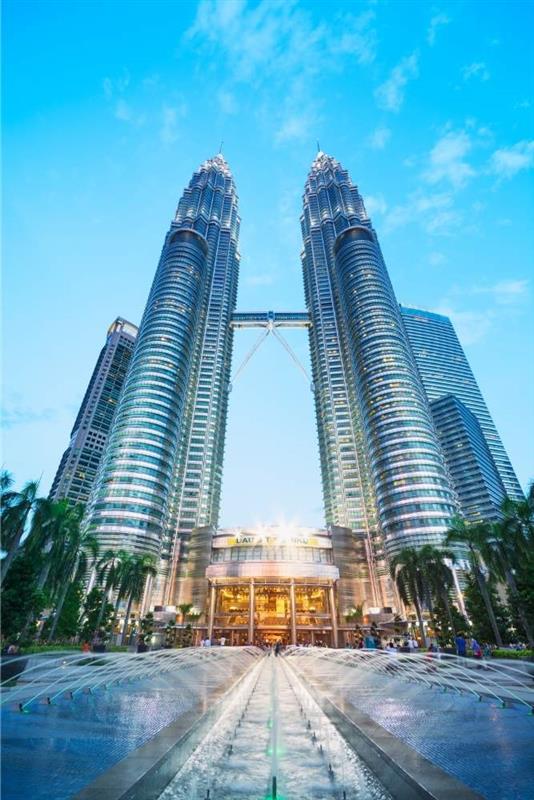
The Kuala Lumpur Tower in Malaysia is a tall telecommunications tower supported by a central prestressed concrete column. This column is anchored to the ground by a series of prestressed concrete piles, which transfer the tower’s loads to the underlying soil.
Conclusion
Prestressed concrete is a construction process widely used in the construction industry due to its high strength and ability to span long distances with minimal deflection. It is commonly used in the construction of buildings, and other structures and has a several important advantages, including reduced cracking, improved fatigue resistance, and increased stiffness and stability. However, prestressed concrete also has some potential disadvantages, including a higher initial cost and a more complex construction process, and requires careful design and construction to ensure its optimal performance.
Also Read: Precast Concrete Piles: Basic Info | Types | Advantages & Disadvantages
References
Tahmasebinia, F.; Fogerty, D.; Wu, L.O.; Li, Z.; Sepasgozar, S.M.E.; Zhang, K.; Sepasgozar, S.; Marroquin, F.A. Numerical Analysis of the Creep and Shrinkage Experienced in the Sydney Opera House and the Rise of Digital Twin as Future Monitoring Technology. Buildings 2019, 9, 137. https://doi.org/10.3390/buildings9060137
T. Y. Lin. (1999) The Father of Prestressed Concrete”: Teaching Engineers, Bridging Rivers and Borders, 1931 to 1999. University of California. Available from: https://oac.cdlib.org/view?docId=kt4w1003s9&query=&brand=calisphere
Author Bio
Nafisa Nazneen Choudhury – Nafisa Nazneen Choudhury is a Civil Engineer (completed B.E. from Assam Engineering College) and is currently pursuing M.Tech in Structural Engineering at National Institute of Technology, Silchar. She is a Technical Content Writer, having over 3 years of experience and has wrote many articles related to Civil Engineering. She is also a Book Author (Authored – “Dream Tales of NNC: Revenge By Murder”) and her book can be found on Amazon. She is also a Guest Author at Gharpedia. Moreover, she is a certified member at Institution of Civil Engineers (ICE) and National Society of Professional Engineers (NSPE). She writes her blogs at her website – nnc2017.wordpress.com. She can be reached on LinkedIn.