Table of Contents
The quality of concrete significantly depends upon design mix proportions and mixing of the constituents of concrete. Concrete mixers help mix concrete ingredients and produce a workable concrete paste. Gharpedia, through this blog, brings you a guide on different types of concrete mixer.
What is Concrete Mixer?
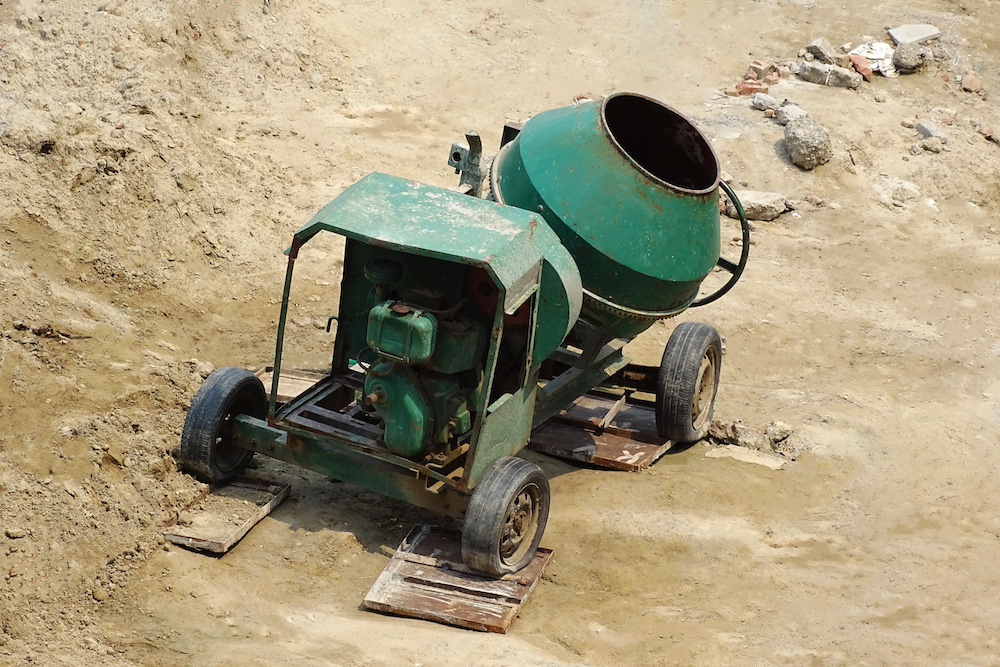
Concrete mixers are machines used in construction to mix cement, water, and other materials (sand, gravel, and occasionally additives) to prepare concrete. They can be large industrial-sized mixers used on construction sites, or they can be small portable mixers. A variety of industries use concrete mixer machines to prepare concrete on-site, giving workers enough time to use the mixture before it sets. These machines save a lot of time and labour, make the process more efficient and economical, and increase labourers’ productivity. The concrete mixers should not only achieve the uniformity of the mixture, but they should also discharge the mixture without disturbing its uniformity.
In the absence of concrete mixers or while working on small jobs, concrete is sometimes mixed manually. But, due to the carelessness of the labourers, the concrete is either mixed poorly or is frequently over-mixed. Hence, it is advisable to use concrete mixers for proper mixing of the concrete. Remember, mixing is the heart of concrete and poor mixing means poor quality of concrete.
Types of Concrete Mixer
Concrete mixers are of two types: Batch mixers and Continuous mixers:
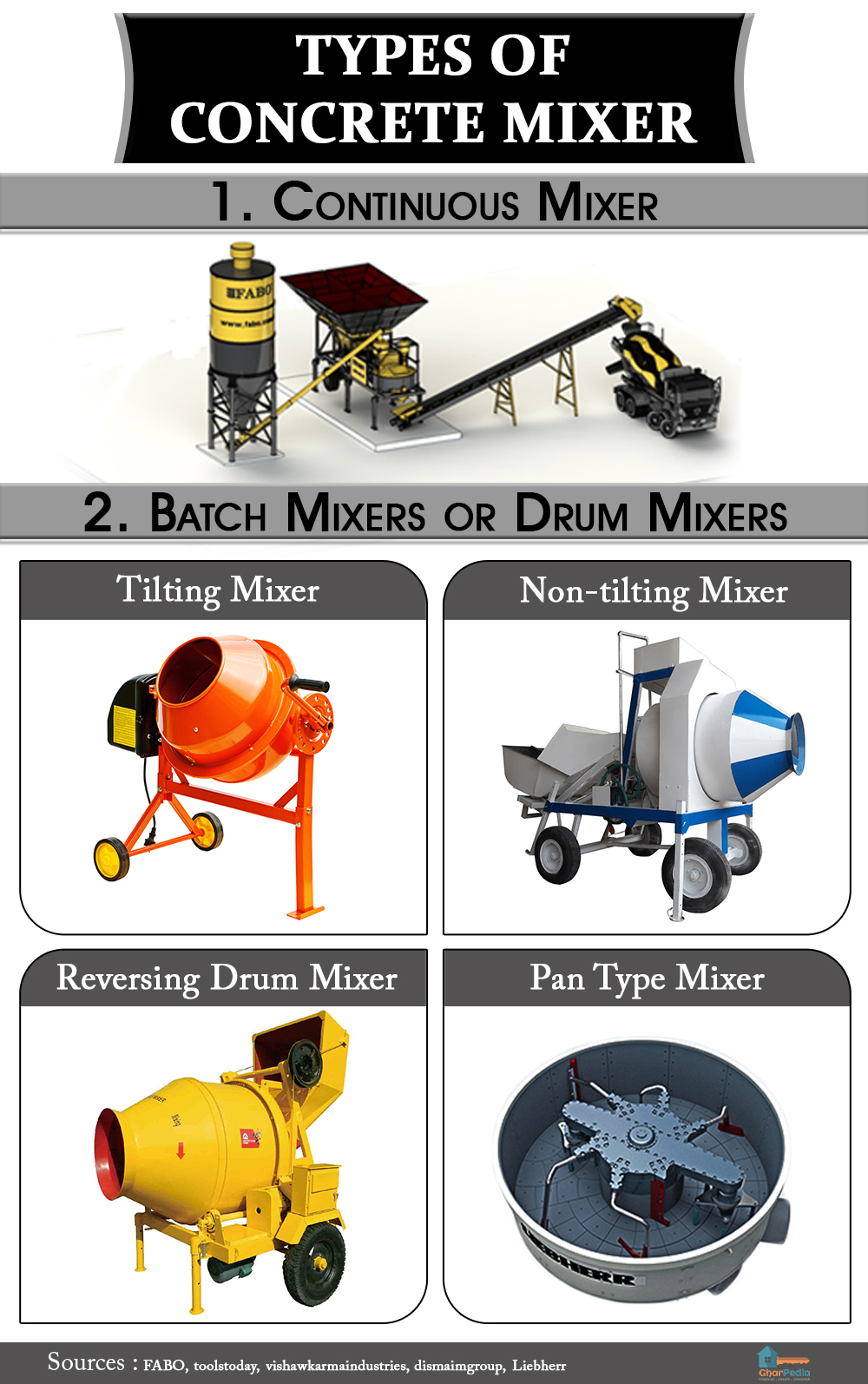
01. Concrete Batch Mixers
Batch mixer is one of the most common types of concrete mixer. As the name suggests, it produces one batch of concrete mix at a time. In batch mixers, the concrete mix is prepared by rotating a pan or a drum with blades. It is possible to regulate the drum’s rotational speed, blade angle, and, in certain situations, inclination angle. Batch mixing is a superior option for products that must pass strict quality checks since it allows for precise alteration of each batch. Using batch mixers, you can load additional components after blending a portion of the ingredients. Batch mixers can carry out several mixing procedures in this manner.
It consists of a revolving drum with blades or baffles fitted within it. In this type of concrete mixer, all the materials in the desired proportion are mixed and fed into the hopper of the revolving drum. Then the drum, when rotated at a certain speed, mixes the materials with the help of a series of blades fitted inside. The resultant mixture is finally discharged from the drum and is ready for use. Batch mixers work well for small to medium-sized construction projects where there isn’t a huge need for concrete.
There are two types of batch mixers: drum mixers and pan mixers.
A. Concrete Drum Mixers
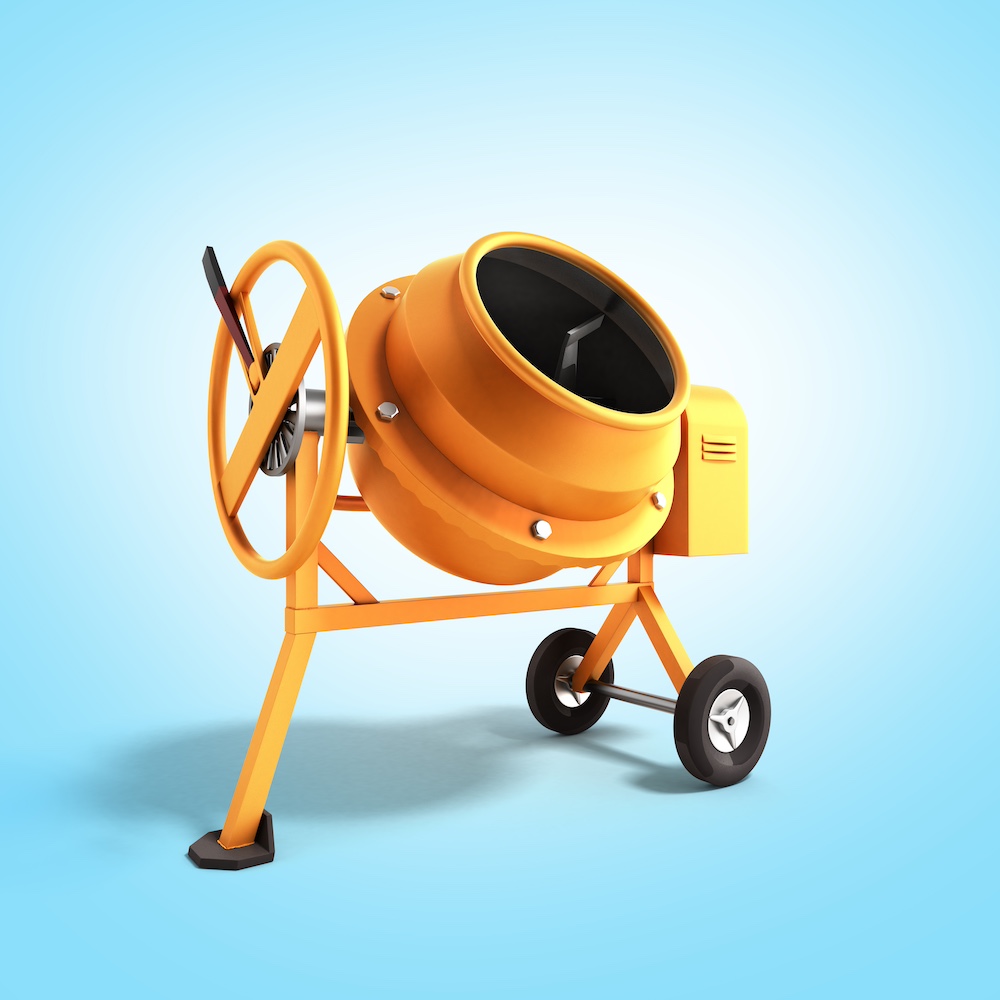
This type of mixer consists of a double conical frustum shaped drum. Depending on its type, the drum either has a single set of blades or multiple sets of blades, which mix, prepare, and discharge the concrete mixture. The drum revolves on its axis, and the blades inside the drum aid in mixing the concrete while the drum spins. Drum mixers are available in a variety of configurations to suit different needs and applications. In comparison to other kinds of mixers, they also require less labour and are simple to run. There are three types of drum mixers. They are:
- Titling mixers
- Non-tilting mixers
- Reverse drum mixers
Tilting Type Concrete Mixers :
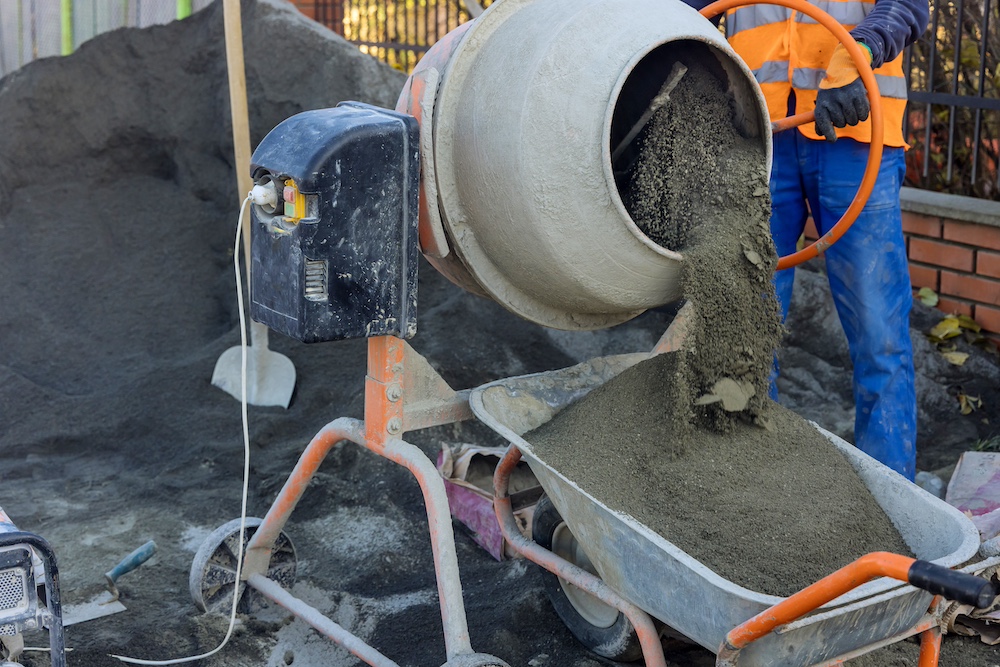
Tilting type mixers have a conical or bowl-shaped drum with vanes inside. When the drum is in a horizontal position, more energy is given to the material inside the drum, allowing the material to be raised to its maximum height before falling. About 90% of the mixing happens during this drop step. According to the author Chiara F. Ferraris (Author of a research paper titled “Concrete Mixing Methods and Concrete Mixers: State of the Art”), for optimum mixing, the drum axis usually stays at an angle of about 15° from horizontal during mixing.
Tilting type drum mixers are a popular option, because of their ability to quickly unload concrete. One can pour the concrete mix into a predetermined location by tilting the drum downward. Therefore, they have an advantage over non-tilting drum mixers. Because of this, they are a popular option for modest to medium-sized construction projects. These types of mixers are preferable for mixes of low workability and for those containing large aggregates.
Know in detail about the workability of concrete:
What is the Workability of Fresh Concrete?
Non-Tilting Concrete Mixers :
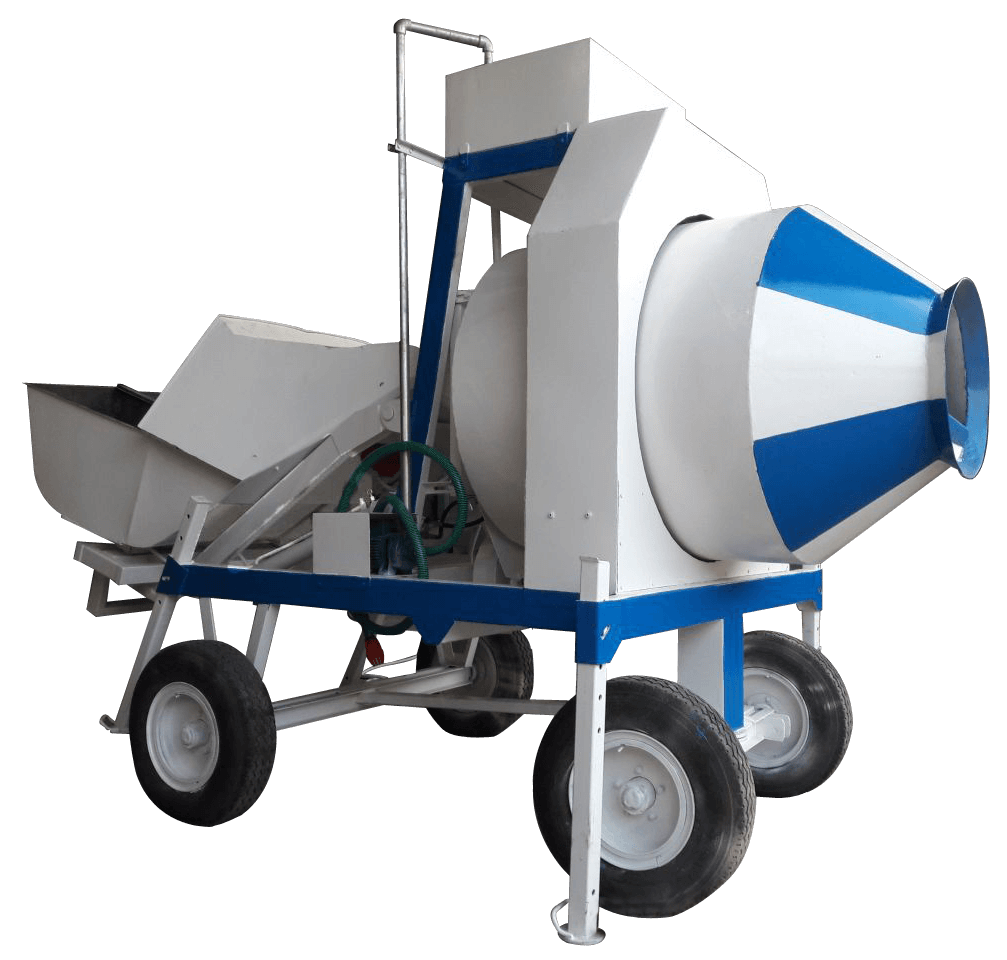
The concrete mixture in non-tilting mixer does not tilt, and the mixer’s drum revolves around its horizontal axis to mix the concrete. To finally discharge the concrete mix, a chute is positioned at an angle such that it empties the drum. The drum has openings on both sides. One end is fed with the ingredients needed to make the mix, while the other is used to collect the finished product. Simple design and effortless operation are two benefits of this concrete mixer. Mixing wet and dry mixes is possible with them, making them appropriate for small to medium-sized construction projects. Additionally, they require less upkeep than other models. The major disadvantage of non-tilting mixers is that they cannot automatically unload the mixed material. This may not be cost-effective for large-scale construction projects because it takes physical labour to discharge the concrete mix.
Reversing Drum Concrete Mixers :
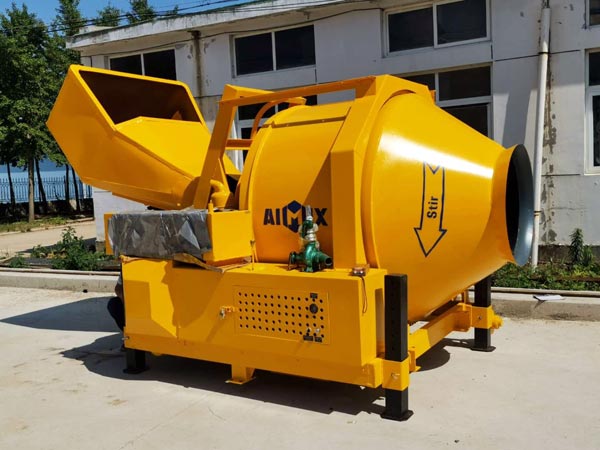
Reversing drum mixers function similarly to non-tilting type mixers, however the reverse rotation is for a different purpose. The drum features two openings: one for inlet of material and the other for mix discharge. The horizontal axis of the drum rotates. When discharging, the drum rotates in the opposite direction from when it is mixing. There are two distinct sets of blades organized for discharging and mixing. Reverse drum mixers work well with dry concrete mixtures. One of the advantages of reverse drum mixers is that they can create extremely uniform concrete mixtures, whether wet or dry form. They are easy to clean and maintain, making them appropriate for modest to medium-sized construction projects. Nonetheless, they could be less appealing for some building projects because of their comparatively high cost.
B. Pan Type Concrete Mixers:
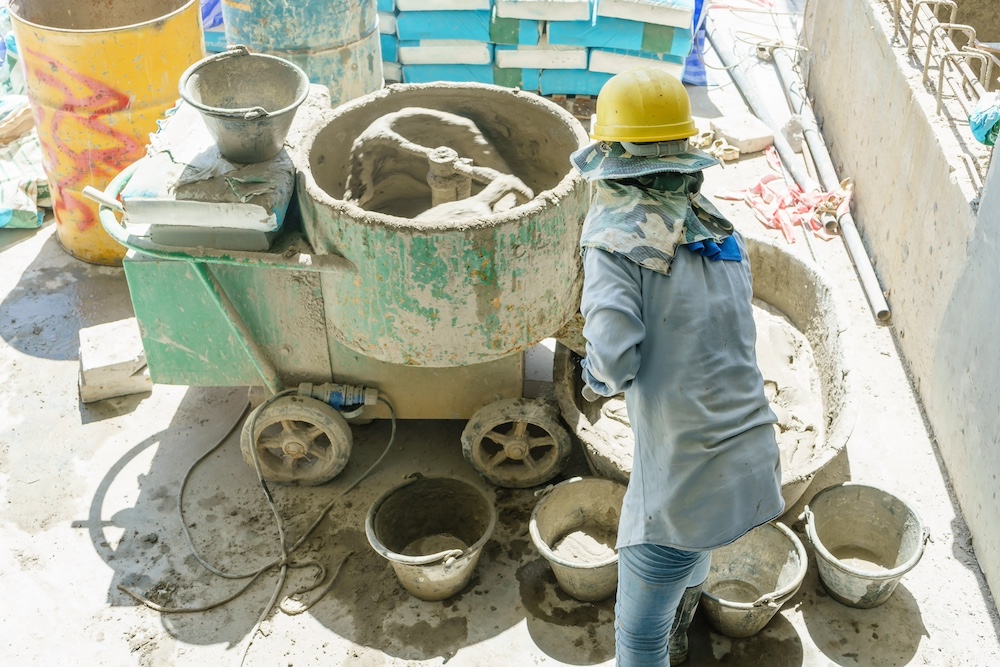
As the name suggests, instead of a drum, this type of concrete mixer prepares concrete in a cylindrical pan that has blades. Typically, these blades have a star-like form for maximum effectiveness. The pan-type mixer comprises a horizontally positioned circular mixing pan fixed on a caster frame. Generally, pan-type mixers are of two types, based on the mechanism of mixing:
- In the first type, the pan is fixed, and the blades rotate about the vertical axis of the mixer.
- In the second type, the cylindrical pan rotates and the blades are static.
Both the aforementioned types work efficiently and produce the concrete mix with the same consistency. Generally, the mixture of concrete is discharged from the bottom of the pan. When construction requires a bit of stiff mixture, these types of concrete mixers are used. One of the major benefits of pan mixers is they create very homogeneous concrete mixes. They have lesser mixing capability in comparison to other types of concrete mixers, which is one of their primary disadvantages. Hence, larger building projects requiring high-capacity mixing equipment might not be a good fit for them.
02. Continuous Concrete Mixer
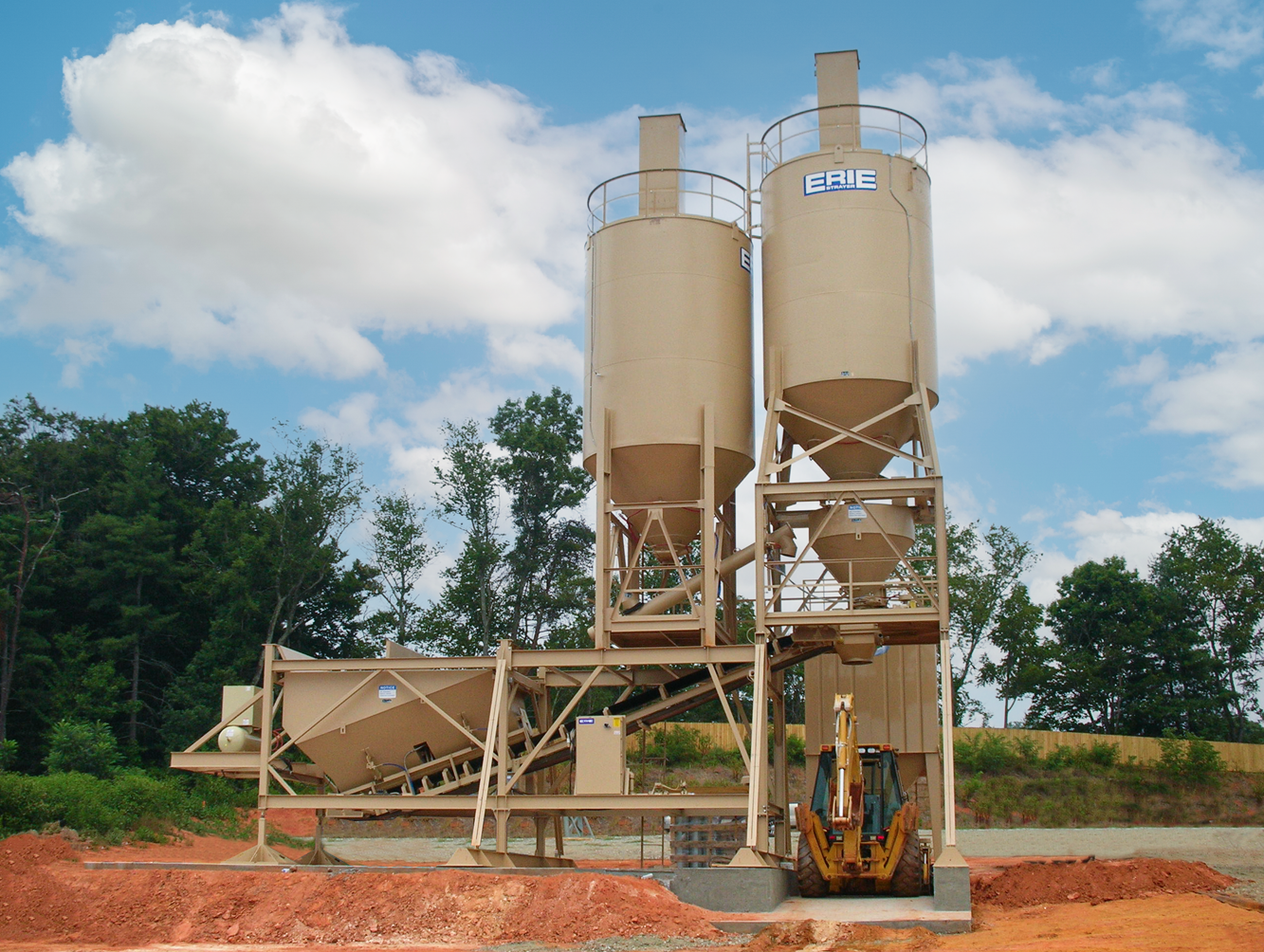
As the name suggests, the main function of a continuous concrete mixer is to load, mix, and discharge the mix constantly, until the task is finished, or a break is taken. The screw feeders of this machine continuously load materials. Continuous mixers are best suited for large construction sites such as the construction of high-rise buildings, dams, bridges, etc., which involve the use of large masses of concrete and also require a continuous flow of concrete. They have relatively high costs and require more space for operation. This makes them unsuitable for small construction projects.
Conclusion
For mixing the ingredients of concrete, the contractors use different types of concrete mixers depending upon the quantity of concrete and the cost of the work/project. The type of concrete mixer, the duration of the mixing cycle, the loading technique, and the energy of mixing, all have an impact on the complex process of mixing of concrete. When speed and efficiency are of the essence in large-scale operations, a continuous mixer is frequently the best option. Batch mixing is usually a preferred choice when the project requires more precise ratios. Only in cases where mix ratios can vary between batches should it be employed. Hence, it is very important to select the proper mixing procedure and concrete mixer type to mix the concrete.
Want to know more about the batching of concrete? Check out our detailed article: