Metals are used for various engineering purposes such as structural members, roofing materials, damp proof courses, pipes, tanks, doors, window etc. Out of all the metals, iron is the most prevalent metal and used in construction activity since pre-historic times.
Metals are classified into two basic categories,
- Ferrous Metals: Ferrous metals are the type of metals which contains iron as their main constituent.
- Non – Ferrous Metals: Non – ferrous metals are the type of metals which does not contain iron as their main constituent. The earth’s crust contains about 5% iron. However, it is present as iron oxide. Iron is obtained from iron oxide by reduction with a reducing agent. The principal reducing agent that is used naturally occurring carbon in the form of coke, coal or charcoal.
According to ‘Ahindra Ghosh and Amit Chatterjee’ (Author of Ironmaking and Steelmaking Theory and Practice), For economic extraction of iron, relatively well deposited iron ore, with iron contents above 55 – 60% are generally used. Iron can form alloys with many elements. Iron is most commonly used metal in construction industry since pre-historic times. Nowadays, it is used in makingstructural members, roofing materials, damp proof courses, pipes, tanks, doors, windows etc. Any construction is incomplete without iron. To suit various needs, alloying of Iron is done to produce various grades of Iron having multiple properties. Iron can form alloys with many elements.
Broadly speaking, the iron products can be classified into three categories,
- Steel
- Cast-iron
- Wrought iron
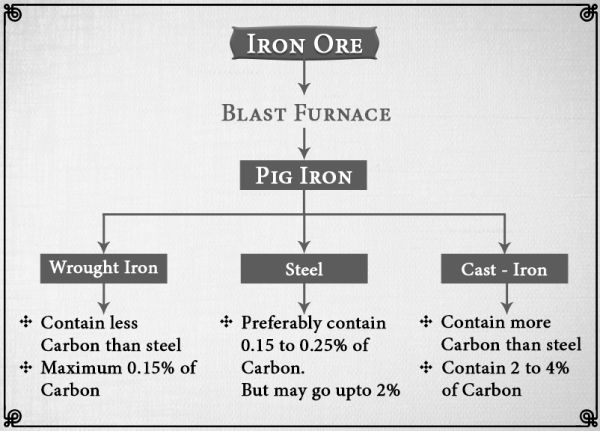
Products of Iron
All three products are modified form of iron, artificially produced and having qualities of hardness, elasticity and strength varying according to composition. Today steel is an essential product of iron used for construction, while wrought iron is used in very small quantities for ornamental purposes.
Here, we are discussing the difference between Mild steel, Cast-iron and Wrought iron.
Comparison of Mild Steel Vs Cast-Iron Vs Wrought Iron
01. Definition
Mild Steel
- According to ‘Christopher Gorse’, ‘David Johnston’ and ‘Martin Pritchard’ (Author of Oxford Dictionary of Construction, Surveying & Civil Engineering), Mild steel is a type of steel containing not more than 2 % carbon content and very few additional alloying elements. It is also called Low Carbon Steel or soft steel.
Cast-Iron
- According to ‘David Blockley’ (Author of New Dictionary of Civil Engineering), Cast-iron is a brittle alloy of iron and carbon that can be readily cast in a mould.
Wrought Iron
- According to ‘David Blockley’ (Author of New Dictionary of Civil Engineering), Wrought iron is very malleable form of iron with low carbon content suitable for forging or rolling rather than casting.
02. Composition
Mild Steel
- Carbon Steel is unalloyed steel, which contains elements such as carbon, manganese, phosphorus, Sulphur and silicon. Mild steel is a type of carbon steel which contains 0.15 to 0.25 % carbon.
Cast-IronCast iron contains about 2 to 4 % of carbon. Also, it contains various impurities such as manganese, phosphorus, silicon and Sulphur.
- The manganese makes cast-iron brittle and hard. Therefore, its proportion should be kept below 0.75 %.
- The phosphorus increases the fluidity of cast-iron. It also makes cast-iron brittle and when its proportion is more than 0.30 %, the resulting cast-iron lacks toughness and workability. Sometimes, its percentage is kept at about 1 to 1.5 to get very thin castings.
- The silicon combined with part of iron makes a reliable solution. It also removes combined carbon from graphite form. If its amount is less than 2.5%, it decreases shrinkage and ensures softer and better castings.
- The Sulphur makes cast-iron brittle and hard. Also, it does not allow smooth cooling in sand mould. Its presence causes rapid solidification of cast – iron, resulting in blowholes and sand – holes. The Sulphur content should be kept below 0.10%.
Wrought Iron
- Wrought iron is almost pure iron, produced by removing the impurities of cast-iron. The total impurities are limited to 0.5 % with a maximum percentage of carbon 0.15%, silicon 0.15 – 0.20%, phosphorus 0.12 – 0.16%, Sulphur 0.02 – 0.03% and manganese 0.03 – 0.10%.
03. Structure
Mild Steel
- Mild steel has a fibrous structure.
Cast-Iron
- The structure of cast-iron is granular and crystalline with a whitish or greyish tinge.
Wrought Iron
- The fresh fracture of wrought iron shows clear bluish colour with silky, lustrous and fibrous appearance.
04. Strength
Strength of material is its capacity to resist a force, pressure or stress. The Strength increases with increase in carbon content.
Mild Steel
- The Strength of mild steel is less than Cast-iron and more than wrought iron.
Cast-Iron
- The Strength of Cast-iron is more than mild steel and wrought iron.
Wrought Iron
- The Strength of wrought iron is least among the three.
05. Ultimate Compressive Strength
Ultimate Compressive Strength is the maximum stress that a material can withstand before getting crushed.
Mild Steel
- The ultimate compressive strength of mild steel varies from 800 to 1200 N/mm2.
Cast-Iron
- The ultimate compressive strength of cast-iron is 600 N/mm2.
Wrought Iron
- The ultimate compressive strength of wrought iron is 200 N/mm2.
06. Ultimate Tensile Strength
Ultimate tensile strength is the maximum stress that a material can endure under a resultant tensile force or stress.
Mild Steel
- The ultimate tensile strength of mild steel varies from 600 to 800 N/mm2.
Cast-Iron
- The ultimate tensile strength of Cast-Iron is 150 N/mm2.
Wrought Iron
- The ultimate tensile strength of Wrought Iron is 400 N/mm2.
07. Hardness
The ability of a material to resist penetration by a harder body is known as its Hardness. According to ‘Francis D. K. Ching’ (Author of Building Construction Illustrated), with the increase in carbon content, hardness increases.
Mild Steel
- The Hardness of mild steel is less than Cast-iron but more than wrought iron.
Cast-Iron
- The Hardness of Cast-iron is more than mild steel and wrought iron.
Wrought Iron
- The Hardness of wrought iron is less than mild steel and cast iron.
08. Brittleness
Brittleness is a measure of how brittle material is, which is characterized by little or no plastic deformation. A material which breaks into pieces or which can be easily reduced to powder form is known as a brittle material. E.g. Glass. A deformation is said to be plastic when the solid deforms when it is loaded, and change in shape takes place after the load is removed. The increase in carbon content increase the brittleness.
Mild Steel
- Mild steel is not brittle.
Cast-Iron
- Cast-iron is brittle.
Wrought Iron
- Wrought iron is not brittle.
09. Toughness
Toughness is a material property indicating the energy required to break a material. A material which does not easily break under a hammer is called tough material. According to ‘P. N. Khanna’ (Author of Indian Practical Civil Engineers’ Handbook), toughness decreases with the increase in carbon content
Mild Steel
- The toughness of mild steel is more than Cast-iron and less than wrought iron.
Cast-Iron
- The toughness of Cast-iron is less than mild steel and wrought iron.
Wrought Iron
- The toughness of wrought iron is more than mild steel and cast iron.
10. Tempering
Tempering is a process in whichthe brittleness of material is reduced by heating.
Mild Steel
- Mild steel cannot be easily tempered.
Cast- Iron
- Cast-iron can be hardened by heating and sudden cooling, but it cannot be tempered.
Wrought Iron
- Wrought iron cannot be easily tempered.
11. Malleability
Malleability of material is defined as its ability that material can be hammered or pressed into shape without breaking or cracking. According to ‘M M Goyal’ (Author of Construction Handbook for civil engineers and Architects), as the carbon content increases, the malleability decreases.
Mild Steel
- The malleability of mild steel is more than cast iron and less than wrought iron.
Cast-Iron
- The malleability of cast-iron is least among the three.
Wrought Iron
- The malleability of wrought iron is more than the other two.
12. Melting Point
Melting point is defined as the temperature at which the solid changes into liquid.
Mild Steel
- The melting point of mild steel is 1400 0C.
Cast-Iron
- The melting point of cast-iron is 1200 0C.
Wrought Iron
- The melting point of wrought iron is 1500 0C.
13. Ductility
Ductility is the ability of a material to undergo plastic deformation. According to ‘M M Goyal’ (Author of Construction Handbook for civil engineers and Architects), with the increase in carbon contentthe ductilitydecrease.
Mild Steel
- Mild steel is ductile. Ductility of mild steel is more than that of cast iron and less than that of wrought iron.
Cast-Iron
- Cast-iron is not ductile.
Wrought Iron
- Wrought iron is ductile. Ductility of wrought iron is more than mild steel and cast-iron.
14. Elasticity
Elasticity is the ability of a material to restore its initial form and dimensions after the load is removed.
Mild Steel
- Mild steel is more elastic than wrought iron.
Cast – Iron
- Cast-iron is not an elastic material.
Wrought Iron
- Wrought iron is moderately elastic.
15. Plasticity
Plasticity of a material is defined as its ability to change its shape under load without cracking and to retain its shape after the removal of load.
Mild Steel
- Mild steel is not a plastic material.
Cast – Iron
- Cast-iron is a plastic material.
Wrought Iron
- Wrought iron is not a plastic material.
16. Weldability
Weldability is the ability of the material to get welded under specific conditions. According to ‘M M Goyal’ (Author of Construction Handbook for civil engineers and Architects),with the increase in carbon contentthe weldability decreases.
Mild Steel
- The weldability of mild steel is more than cast-iron and less than wrought iron.
Cast-Iron
- The weldability of the cast-iron is less than mild steel and wrought iron.
Wrought Iron
- The weldability of wrought iron is more than mild steel and cast-iron.
17. Magnetization
Magnetization is a measure of how easily a material can exhibit magnetic properties when subjected to a magnetic field.
Mild Steel
- Mild steel can be permanently magnetized.
Cast-Iron
- Cast-iron cannot be magnetized.
Wrought Iron
- Wrought iron can be temporarily magnetized.
18. Forging
Forging is a process used to shape metal by heating and hammering.
Mild Steel
- Mild steel can be immediately forged
Cast-Iron
- Cast-iron is unsuitable for forging.
Wrought Iron
- Wrought iron can be easily forged.
19. Rusting
Rusting is a form of material degradation highly prevalent in metals, especially ferrous metals and usually initiated by the presence of oxygen and water.
Mild Steel
- Mild steel rusts easily and rapidly than cast-iron. But do not rust easily than wrought iron.
Cast-Iron
- Cast-iron does not rust easily than Mild Steel and Wrought iron.
Wrought Iron
- Wrought iron rusts easily and rapidly than Mild steel and cast-iron.
20. Corrosion Resistance
Corrosion Resistance of material is defined as its ability to withstand contact with ambient natural factors without degradation or change in properties. Any increase in carbon content will increase the rate of corrosion.
Mild Steel
- The corrosion resistance of mild steel is less than wrought iron. But corrosion resistance of mild steel is more than cast – iron.
Cast-Iron
- The corrosion resistance of cast-iron is less than mild steel and wrought iron.
Wrought Iron
- The corrosion resistance of wrought iron ismore than mild steel and cast-iron.
21. Specific Gravity
The ratio of the density of the given material to the density of the reference material is called as Specific gravity. It is also called as relative density.
Mild Steel
- The specific gravity of mild steel is 7.80
Cast-Iron
- The specific gravity of cast-iron is 7.50
Wrought Iron
- The specific gravity of wrought iron is 7.25
22. Uses
Mild Steel
- Mild steel is used in the form of rolled sections, reinforcing bars, roof coverings and sheet piles and railway tracks.
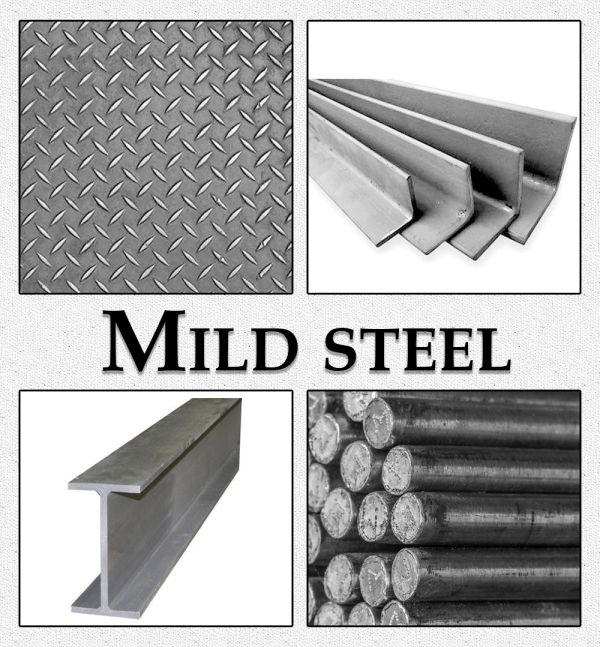
Cast IronThe important uses of cast-iron are:
- For making cisterns, water pipes, gas pipes and sewers, manhole covers and sanitary fittings.
- For making ornamental castings such as brackets, gates, lamp posts, spiral staircase etc.
- For making machinery parts which are not subject to heavy shocks.
- For manufacturing compression members like columns in building, bases of columns etc.
- For preparing agricultural implements.
- For preparing rail chairs, carriage wheels etc.
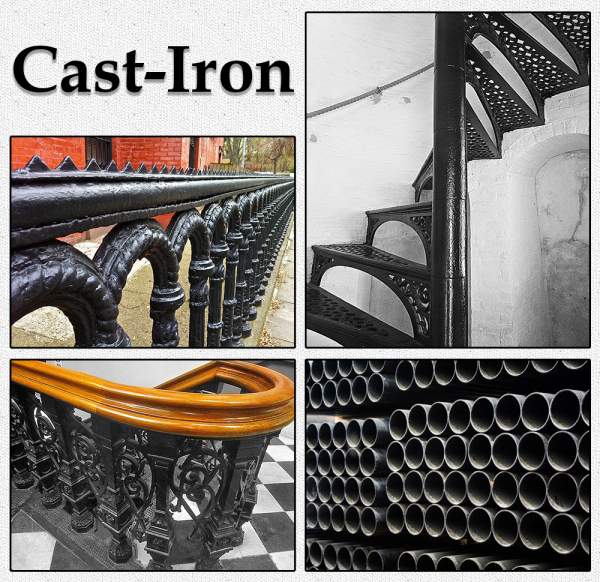
Wrought IronNowadays, wrought iron is widely used in place of mild steel. Generally, it is used where tough material is required.
The wrought iron is used for making
- Rivets
- Chains
- Ornamental ironwork
- Railway couplings
- Water and steam pipes
- Raw materials for manufacturing steel
- Bolts and nuts
- Horseshoe
- Handrails
- Straps for timber roof trusses
- Boiler tubes
- Roofing sheets
- Armatures
- Electromagnets etc.
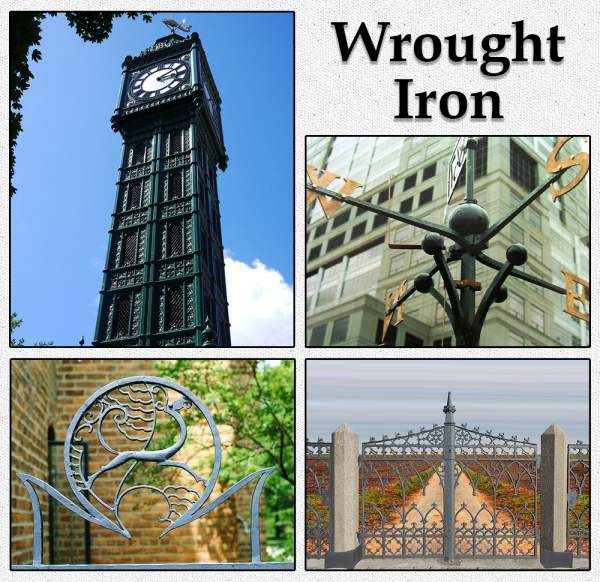
Conclusion:
Iron products are mainly classified as Steel, Cast-iron and Wrought iron. The differences in their properties are due to the different amounts of carbon they contain.
Smaller the amount of carbon in steel, nearer will its properties be to those of wrought iron and greater the quantity of carbon, Steel would resemble the cast-iron.
Here, we have discussed the difference between Mild Steel Vs Cast-iron Vs Wrought Iron with respect to constituents, properties and uses. We hope this article would enable to you to choose the perfect iron product for your various needs. If you have any queries, feel free to leave a comment.
Also Read: