Table of Contents
Formwork in construction refers to temporary moulds or frameworks that support wet concrete while it sets and hardens. It gives the concrete its shape and holds it in place until it is strong enough to support its weight. In short, concrete formwork (shuttering) serves as a mould into which fresh concrete is poured and left to harden.
The choice of formwork for a particular building will depend on various factors, including the size and type of the structure, its intended use, local climate and weather conditions, and the availability and cost of materials.
According to the International Research Journal of Engineering and Technology (IRJET), constructing a formwork is time-consuming and can account for 20% to 25% of the total building cost or even more. The formwork must meet certain standards to ensure safety and efficiency because any failure in its structure can jeopardise workers’ safety. Stripping, which is the careful removal of the formwork, must be done sequentially to prevent structural failures.
Importance of Formwork in Building Construction
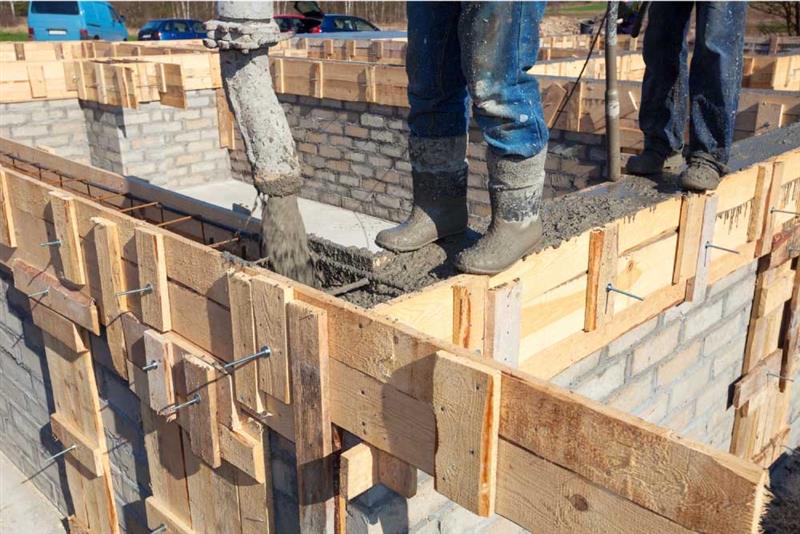
There are several reasons why formwork is essential in building construction:
- Accuracy and Consistency: Formwork ensures that concrete is poured and shaped to precise dimensions, angles, and finishes. This is especially important for structures with complex shapes or tight tolerances.
- Quality and Durability: Proper formwork creates a smooth and even surface on the finished concrete, enhancing the overall quality and durability of the structure. It also helps prevent defects such as honeycombing, which can weaken the structure and shorten its lifespan.
- Safety: Formwork provides a stable and secure working environment for construction workers, preventing wet concrete from collapsing or shifting while it sits.
- Accessibility: Throughout all phases of construction, formwork provides workers with the necessary access and working platforms, significantly improving scaffold safety. It allows access to difficult areas where cracks or other construction issues may arise, places that machinery alone cannot reach.
- Economy: Fixing bad concrete finishes is costly. The quality of the formwork directly impacts the surface finish of a concrete structure. There is no need for plastering if the formwork system used is perfect, thus reducing additional costs.
- Flexibility: Formwork can be designed and customised to meet the specific needs of a particular project, allowing for a wide range of shapes and sizes. It can also be easily modified or removed as required during construction.
Disadvantages of Formwork Systems
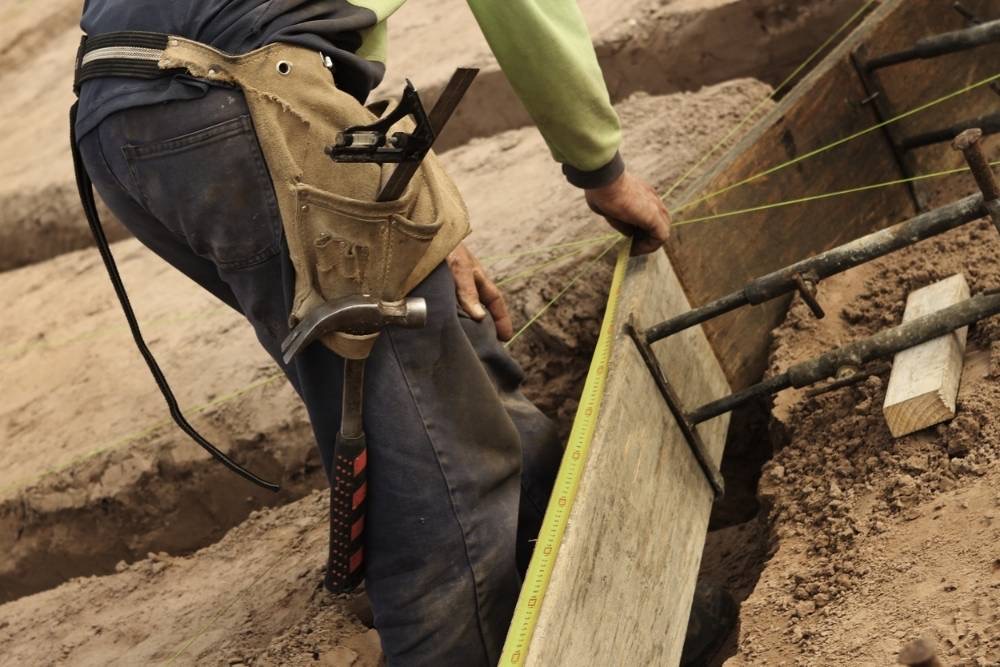
Formwork has several disadvantages that require special attention:
- Cost: Formwork can be expensive, especially if it is custom-made for a specific project. Additionally, designing and building formwork can be time-consuming, increasing the project’s overall cost.
- Weight: Formwork can be heavy, posing challenges when working on upper floors or transporting it to another site.
- Limited Reuse: Formwork can only be used a limited number of times before it needs replacement. This can be a disadvantage if the formwork is expensive or if the project requires a large quantity of it.
- Safety: Working with formwork can be hazardous, as it involves working at heights and handling heavy materials. Thus, it requires proper safety procedures to prevent accidents.
- Time-Consuming: Setting up and dismantling formwork can take significant time, potentially delaying construction progress.
- Weather: Adverse weather conditions, such as strong winds or heavy rain, can affect formwork construction, making it difficult to work with formwork in certain conditions.
All these disadvantages should be taken seriously, and appropriate measures must be implemented to mitigate their impact.
Types of Formworks in Construction
Several types of formworks are used in building construction. Here is a complete breakdown of the same:
01. Based on Material used for Construction
1. Timber Formwork
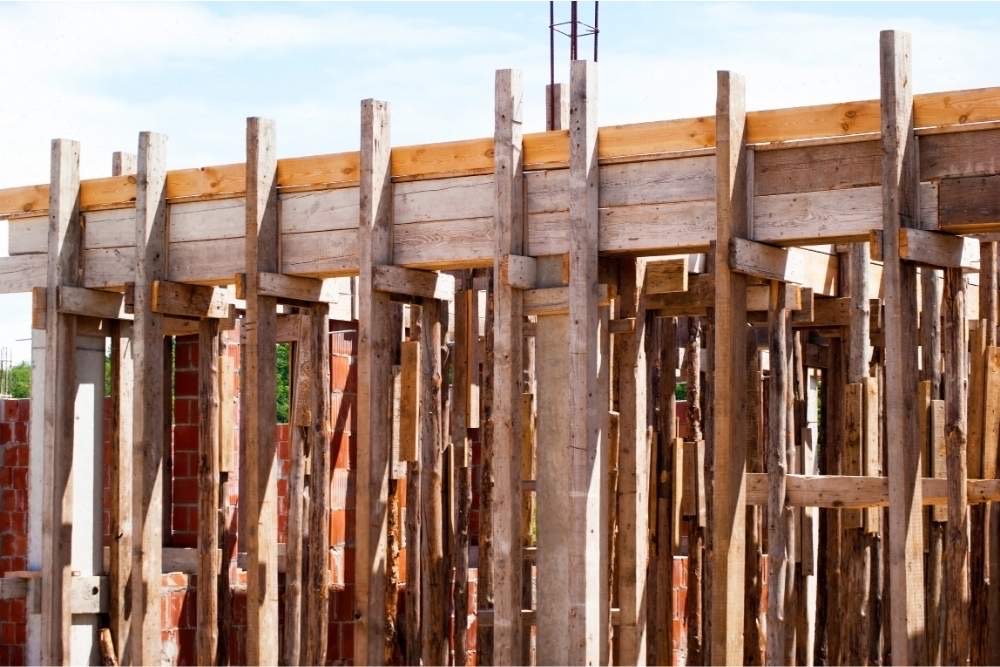
Timber formwork is made of wooden boards and is commonly used for smaller projects. It is relatively inexpensive and easy to modify to suit the structure’s shape. However, it is not as durable as other types of formworks and may not be suitable for larger or more complex projects.
2. Steel Formwork
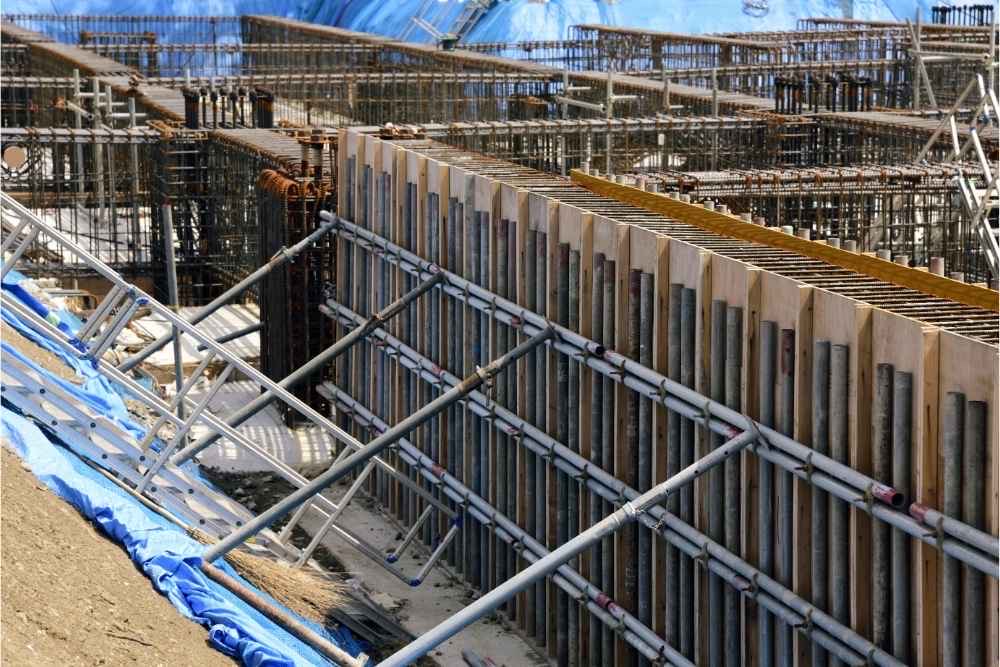
Steel formwork is commonly used for large, complex projects. It is more durable than timber formwork and can be reused multiple times. However, it is pricier and requires specialised equipment for handling and installation. Compared to timber formwork, steel shuttering gives concrete a smoother finish. It can be used to build tanks, columns, chimneys, sewers, tunnels, and curved or round retaining walls.
3. Aluminium Formwork
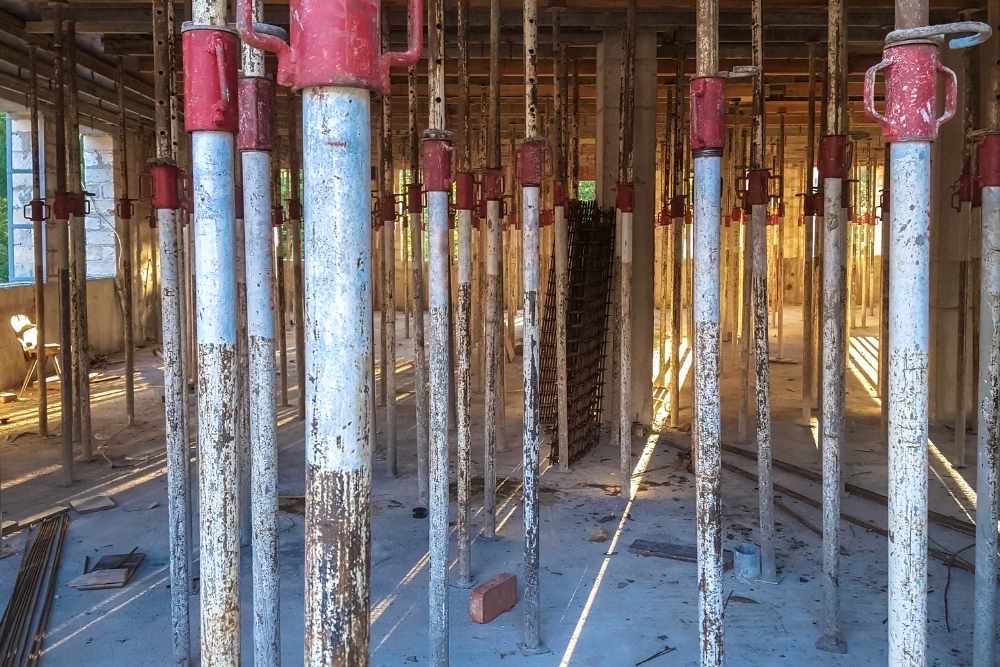
This lightweight formwork material best suits projects that require frequent relocation or where weight is a concern. Although it is costlier than timber formwork, it is more durable and can be reused multiple times.
Also Read: Mivan Formwork in Building: All You Need to Know
4. Plastic Formwork
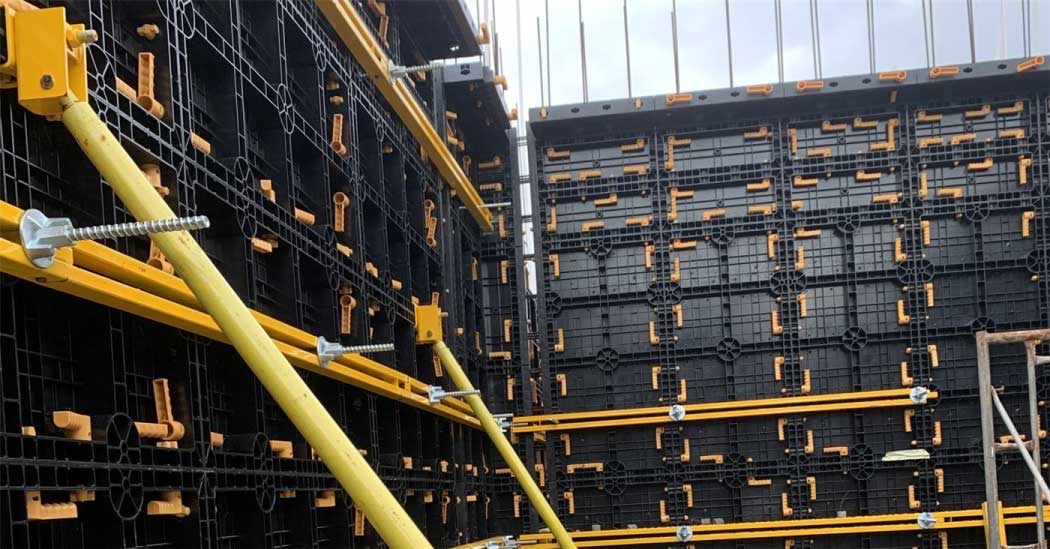
Courtesy - zoloformwork
This formwork is made of plastic and is often used for small projects or those requiring lightweight, easy-to-handle materials. It is inexpensive but not as durable as other types of formworks and may not be suitable for larger or more complex projects. According to the International Journal of Scientific Engineering and Research (IJSER), plastic formwork can be reused 80 to 100 times.
5. Insulating Formwork
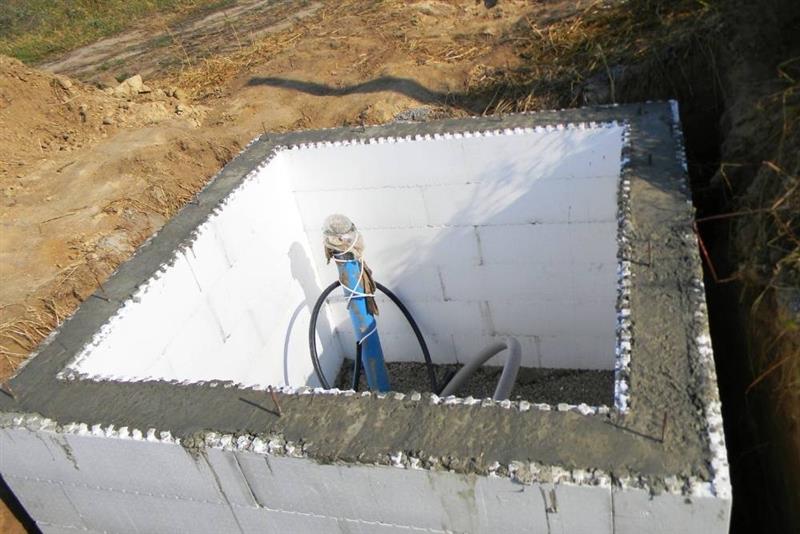
Insulating formwork is made of insulating materials and is used to pour concrete walls that also serve as insulation. This type of formwork is more expensive than others and is often used in energy-efficient construction projects.
6. Plywood Formwork
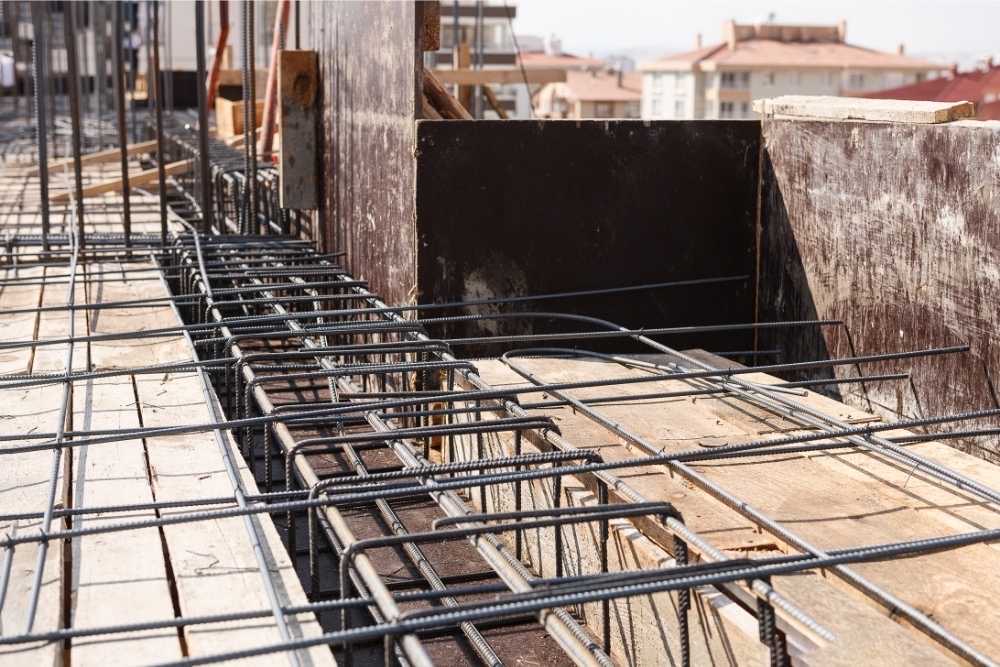
Plywood formwork is one type of engineered timber. In this method, resin-bonded plywood sheets are attached to wooden frames to create right-sized panels. It is strong, flexible, and easy to work with. Plywood is becoming more popular for formwork because of its smooth surface, which requires no additional finishing and can typically be reused 20 to 25 times. Plywood can cover large areas, making formwork assembly and removal more efficient and cost-effective.
02. Based on Function
1. Vertical Formwork
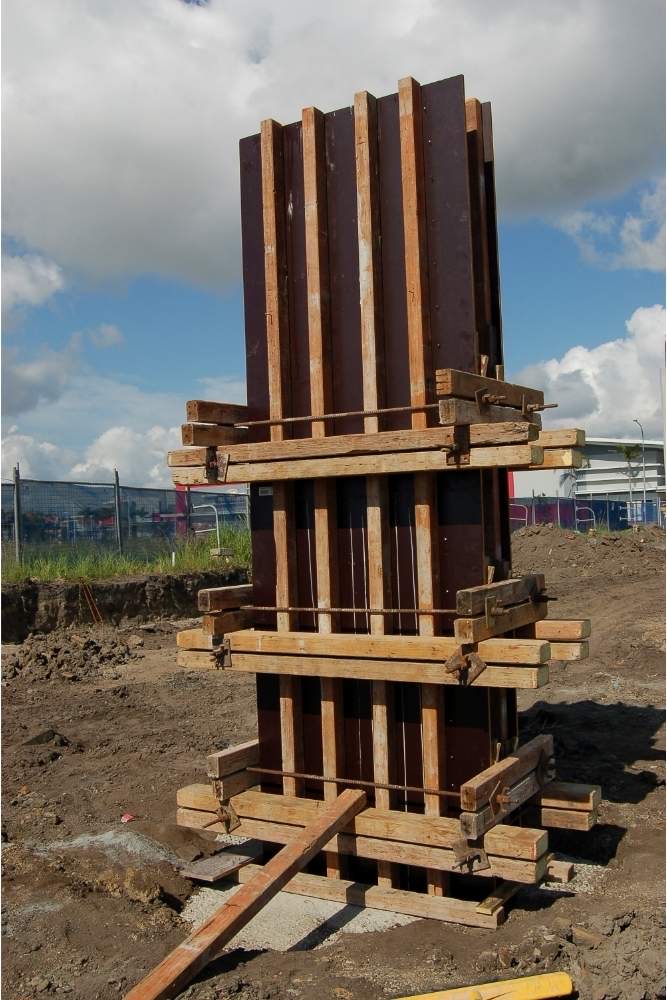
Vertical formwork creates vertical concrete surfaces, such as walls, columns, and sides of beams. It is typically made of timber, steel, or aluminium and can be either custom-made or prefabricated.
2. Horizontal Formwork
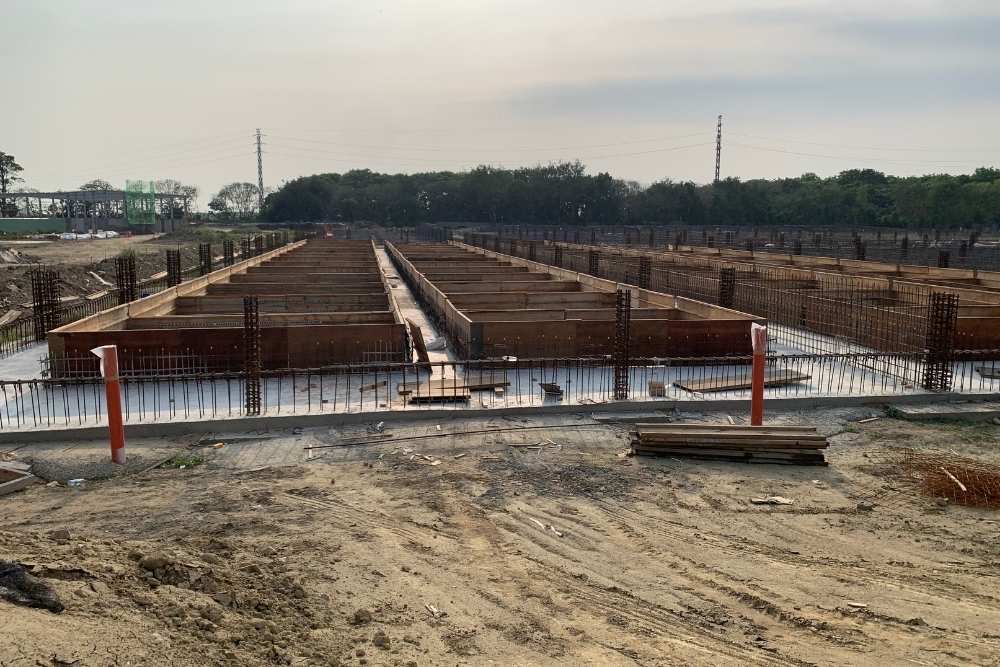
This type of formwork makes horizontal concrete surfaces, such as floors and slabs. It is typically made of timber or steel and can be either custom-made or prefabricated.
3. Circular Formwork
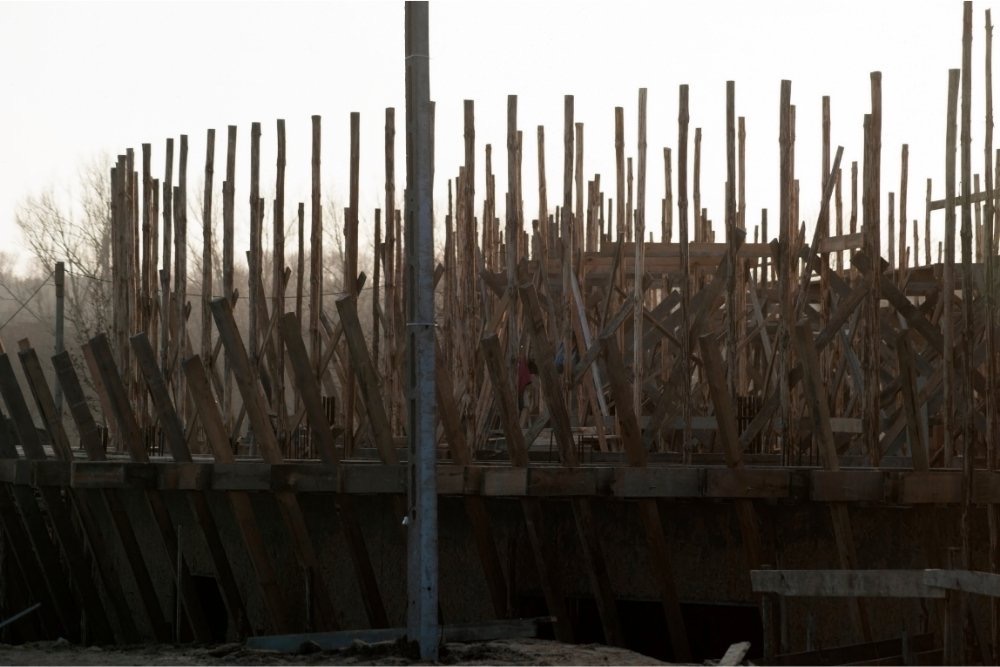
Circular formwork is designed for constructing circular or curved concrete surfaces, such as cylindrical columns or arches. Made of steel or aluminium, it may be custom-made or prefabricated.
4. Suspended Formwork
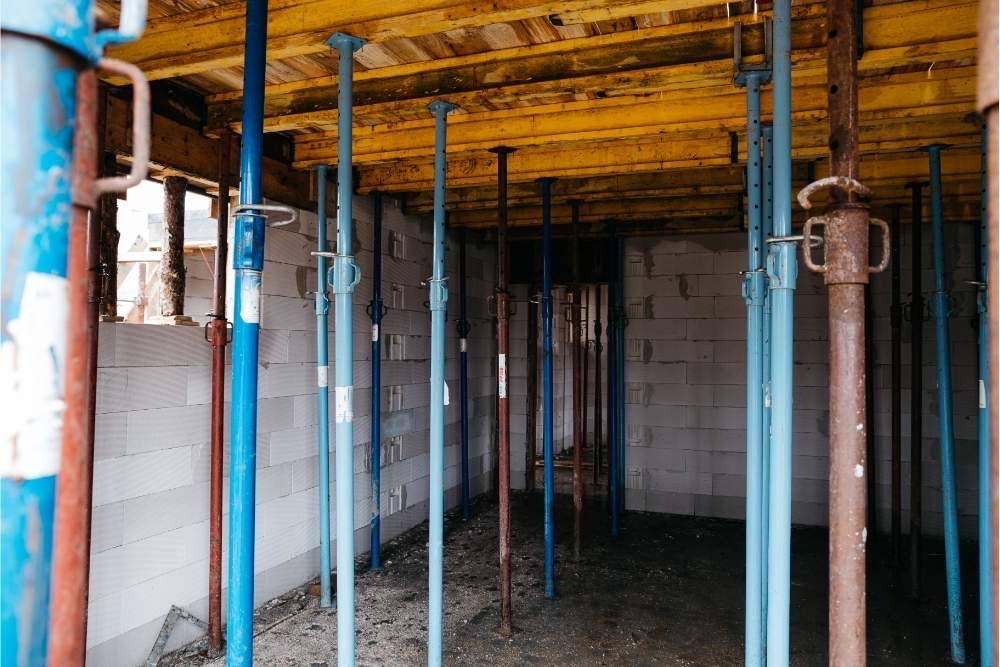
This type of formwork is used to create suspended concrete surfaces, such as bridges or overpasses. It is typically made of steel or aluminium.
5. Specialty Formwork
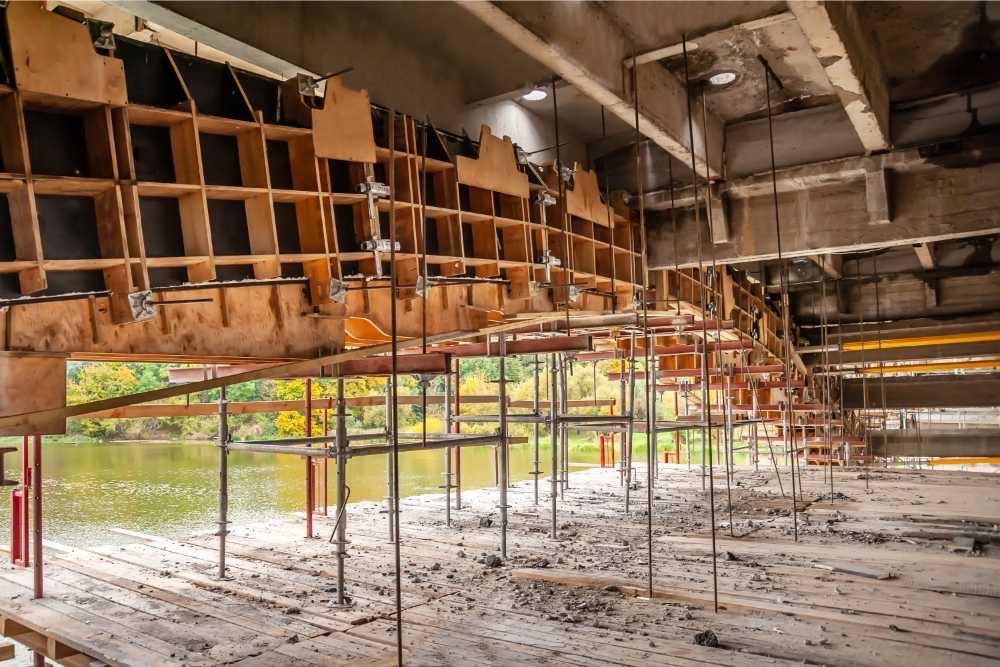
Specialty formwork is designed for specific projects or applications, such as tunnel formwork for creating tunnels or in situ formwork for creating complex or irregular shapes.
03. Based on the Purpose of Construction
1. Wall Formwork
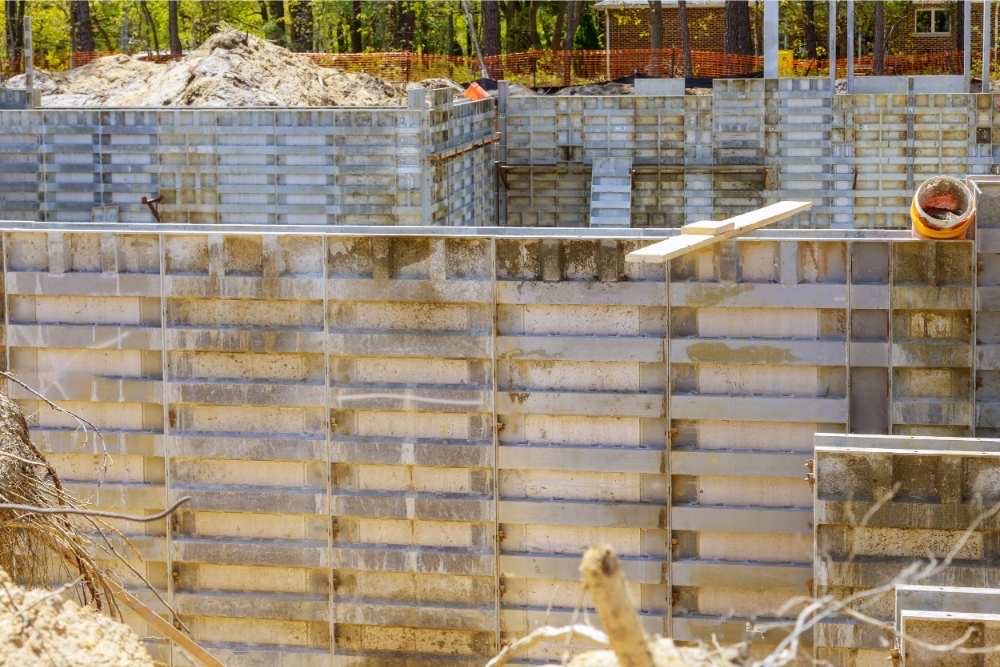
Wall formwork is a type of formwork used to create vertical concrete surfaces, such as walls and columns. It consists of several key components:
- Panels: They form the main structure of the wall formwork, shaping the size and dimensions of the wall. They can be made of timber, steel, aluminium, or other materials and are typically held in place by braces or other supporting elements.
- Braces: They support the panels and keep them in place. They can be made of timber, steel, or other materials and are typically attached to the panels at intervals along the length of the wall.
- Wales: These are horizontal members that distribute the load of the concrete evenly across the wall’s width. They are made of timber, steel, or other materials and are typically attached to both the panels and braces.
- Ties: Ties secure the formwork, preventing movement during the pouring and curing of concrete. They can be made of steel, plastic, or other materials and are inserted at regular intervals along the length of the wall.
- Spacing: It is the distance between ties and panels. Maintaining consistent spacing ensures quality, strength and structural integrity of the finished wall.
2. Climbing Formwork
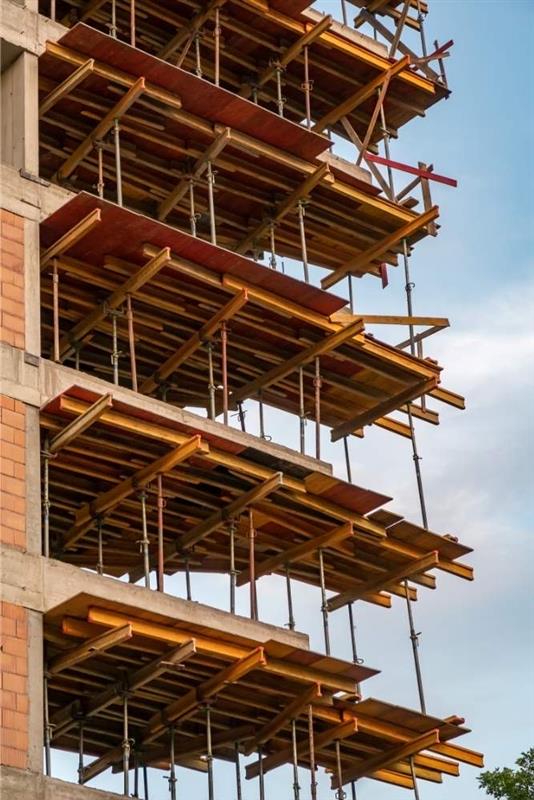
Climbing formwork is a specialized type of formwork used for constructing tall or large structures, such as skyscrapers, bridges, and dams. It consists of an adjustable scaffold-like structure that can be moved upward while pouring the concrete and curing, enabling the structure to be built from the bottom up without requiring external support or scaffolding.
The climbing mechanism is the component that allows the formwork to be adjusted and moved upward as the structure progresses. It can be hydraulic, mechanical, or a combination of both and is typically controlled by a central control system. In addition to wales, spacing, ties, braces and panels, climbing formwork includes support towers or vertical supports holding the climbing formwork in place and providing stability as it is adjusted and moved upward. These support towers can be made of timber, steel, or other materials and are typically placed at intervals along the length of the structure.
3. Table Formwork
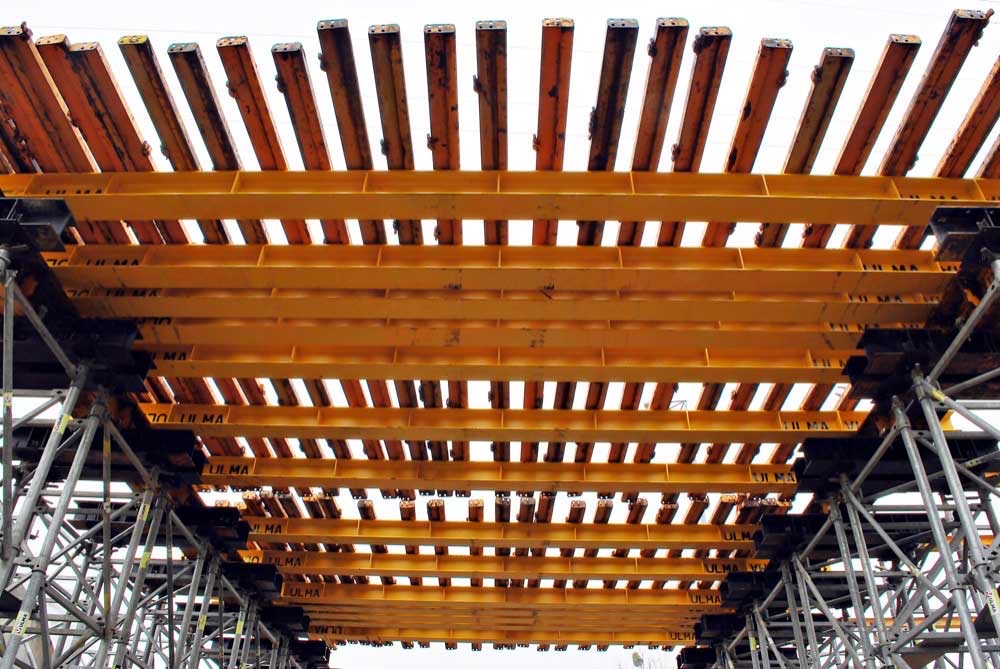
Table formwork creates horizontal concrete surfaces, such as floors, slabs, and roofs. It consists of a framework of beams and panels supported by a series of legs or supports. The beams help hold the panels in place, ensuring stability. Table formwork can be made of timber, steel, or other materials and is attached to the panels at regular intervals along its length and width.
4. Tunnel Formwork
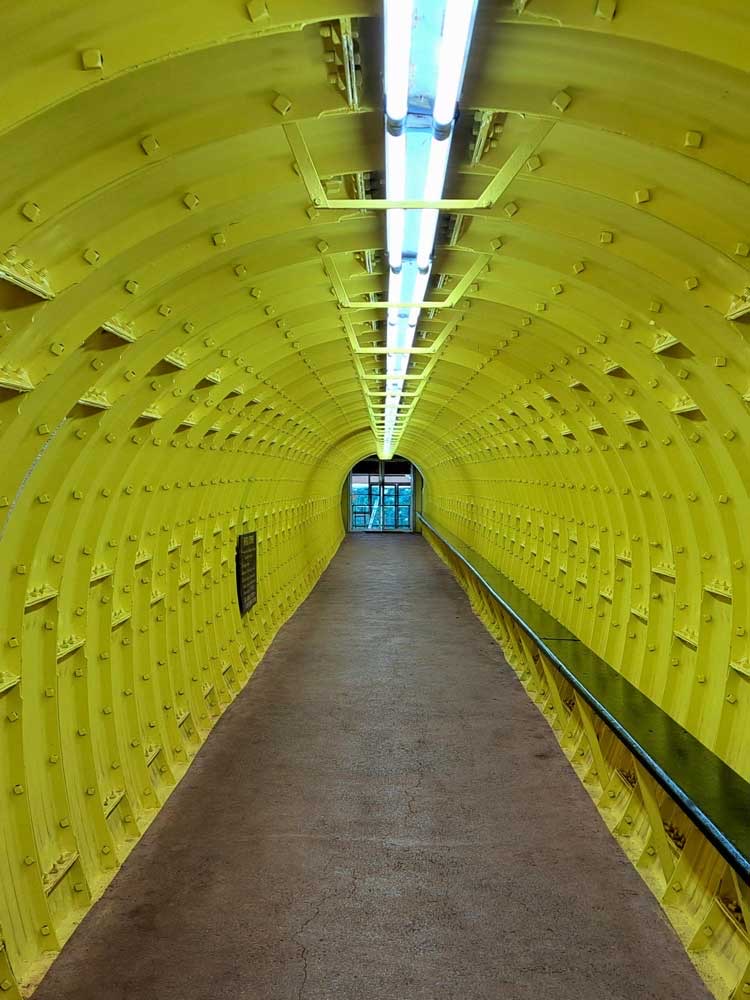
Tunnel formwork consists of a shell and a chariot. The shell, typically 1.5 meters wide, lets the chariot move on the rails, facilitating the sequential pouring of concrete. Tunnel forms come in different shapes, such as horseshoes or ovals, depending on their intended use, including underground buildings, tunnels, and defence facilities. The tunnel formwork design varies based on the type of structure being built. While this type of formwork is fast and easy to use, it requires approximately 30% less reinforcement than concrete structures, resulting in significant cost savings.
Formwork Design Considerations
While designing formwork, consider the following criteria:
- Loads: The formwork should be such that it withstands all applied loads, including the weight of the concrete, live loads, and any wind or seismic forces.
- Shape and Size: The formwork should match the shape and dimensions of the structure. It must support the concrete in the desired form and be able to withstand any movement or shrinkage during the curing process.
- Material: The material used for the formwork should be strong, durable, and capable of withstanding the loads and conditions of the construction site. It should also provide a smooth and accurate concrete finish.
- Reuse: If the formwork is intended for multiple uses, it must be durable enough to withstand repeated assembly, disassembly and reassembly.
- Ease of Use: The formwork should be easy to install and remove, requiring minimal specialised equipment or labour.
- Safety: The formwork should be designed with worker safety in mind, minimising the risk of accidents or injuries.
- Cost: The formwork should be cost-effective, balancing initial investment with durability and reusability.
- Time Efficiency: The formwork should be designed to streamline the construction process and minimise delays.
- Weather Resistance: The formwork must withstand site-specific weather conditions, including wind, rain, and extreme temperatures.
Some important points to note while implementing formworks include:
- Pre-Pouring Preparation: Before pouring concrete, remove all debris from inside the formwork. Clean the surface touching the concrete or thoroughly wet or treat it with an approved composition. It is crucial to ensure that the composition does not come in contact with the reinforcement.
- Formwork Removal: It is important to remove the formwork once the concrete is strong enough, at least twice the force that could be exerted on it at the time of removal. Additionally, the formwork should remain in contact with the concrete for as long as possible to support proper curing. Avoid shocks or vibrations while removing formwork, as they disturb the reinforced concrete. Inspect the concrete surface before dismantling the soffit and struts to ensure it has sufficiently hardened and is strong enough to bear the required load. Take proper care, as the hardening rate slows down when all the cement is added at once. Use cold water only if it was accounted for during the beam design process.
Conclusion
Overall, formwork is a crucial component of any concrete construction project, ensuring the quality, accuracy, and safety of the finished structure. It is available in various materials, shapes, and sizes, and one can customise it to suit the needs of each project. A well-designed and properly constructed formwork system is essential for maintaining the quality, strength and integrity of the final structure. It should withstand the loads and environmental conditions of the construction site. When selecting and designing formwork, key factors to consider include design, material, reusability, ease of use, safety, cost, time efficiency, and weather conditions.
Must Read: Big Mistakes that must be Avoided in Formwork while Concreting
FAQs on Formwork Construction
1. What is the Purpose of Formwork in Construction?
The main purpose of formwork is to safely support reinforced concrete until it has gained adequate strength.
2. What is the Difference between Formwork and Shuttering?
The terms formwork and shuttering are often used interchangeably. However, formwork is a broader term that refers to the entire system used to mould and support concrete, while shuttering specifically refers to the vertical temporary moulds, like those used for walls and columns.
3. How Many Times can Formwork be Reused?
The reusability of formwork depends on the material used. Formwork can typically be reused multiple times, ranging from approximately 7 to 50 times, depending on the type and quality of the material.
4. After How Much Time Can Formwork Be Removed?
Formwork is typically removed 24 to 48 hours after constructing walls, columns, and the vertical faces of all structural elements.
Reference
Jyoti Deupa. (2022) Selection of Formworks for Building Construction. International Research Journal of Engineering and Technology (IRJET). [Online] 09 (09), 175-179. Available From: https://www.irjet.net/archives/V9/i9/IRJET-V9I931.pdf
Imtiyaz Mohi U Din, Chitranjan Kumar. (2015) Impact of Plastic Formwork over Conventional Formwork, International Journal of Scientific Engineering and Research (IJSER). [Online] 5 (7), 478-483. Available From: https://www.ijser.in/archives/v5i7/IJSER171763.pdf
Author Bio
Nafisa Nazneen Choudhury – Nafisa Nazneen Choudhury is a Civil Engineer (completed B.E. from Assam Engineering College) and is currently pursuing M.Tech in Structural Engineering at National Institute of Technology, Silchar. She is a Technical Content Writer, having over 3 years of experience and has wrote many articles related to Civil Engineering. She is also a Book Author (Authored – “Dream Tales of NNC: Revenge By Murder”) and her book can be found on Amazon. She is also a Guest Author at Gharpedia. Moreover, she is a certified member at Institution of Civil Engineers (ICE) and National Society of Professional Engineers (NSPE). She writes her blogs at her website – nnc2017.wordpress.com. She can be reached on LinkedIn.