Cost control is very important to managing un expected costs in construction projects successfully. Without a clear plan for handling expenses, even well-planned projects can lose money, cause delays, cut profits, and hurt relationships with clients.
Unexpected costs in construction can occur for several reasons, such as changing material prices, not having enough workers, changes in design, or surprise problems at the work site. If not dealt with quickly, these issues can delay projects and might affect quality and safety.
In this article, we’ll look at how to manage unexpected costs in construction including their causes, how they affect construction projects, and effective ways to manage and prevent them. We’ll discuss things like planning for emergencies, leveraging construction management solutions, and adopting new technologies to help you stay on budget and ensure your projects run efficiently.
Understanding Unexpected Costs in Construction Projects
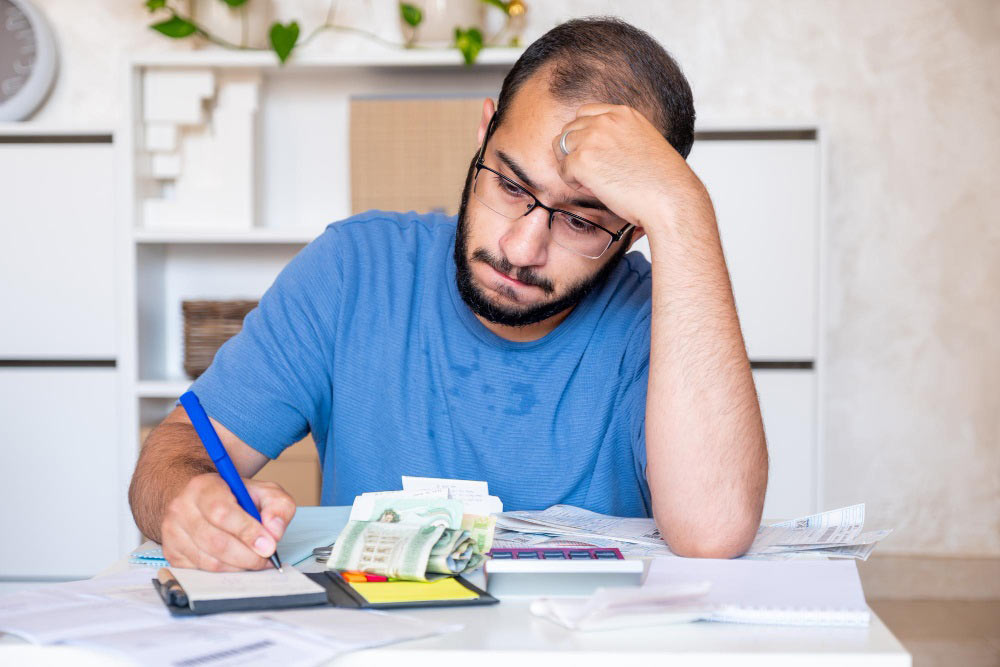
Unexpected costs in construction projects are a common challenge that can significantly impact budgets and timelines. These unforeseen expenses can arise from various sources, making it essential for construction professionals to understand their nature and implications.
01. What are Unexpected Costs?
Unexpected costs are expenses exceeding the initial budget estimates, often arising from unforeseen circumstances during construction. Examples of such costs include:
- Labor Costs: Unanticipated increases in labour rates or the need for additional manpower due to project delays.
- Material Costs: Fluctuations in the prices of materials are often influenced by market conditions or supply chain disruptions.
- Equipment Costs: Additional rental fees for machinery or tools should have been accounted for in the original budget.
- Legal Costs: Fines, regulatory compliance costs, or mid-project legal disputes.
These costs can be categorized into several common areas, including labour, materials, equipment, and legal fees, each contributing to the overall financial strain of a project.
A comprehensive solution like the Anterra CPM Platform can help manage these costs efficiently, providing better visibility and control throughout the project lifecycle.
02. Why do They Happen?
The complexity of construction projects creates a fertile ground for unexpected costs. Projects involve many variables, and internal and external factors can lead to cost overruns.
Factors influencing these overruns can be both external and internal:
- External Factors: These include economic fluctuations, changes in regulatory requirements, and unforeseen environmental conditions that necessitate adjustments in project plans.
- Internal Factors: Internal challenges such as poor project management, inadequate planning, and communication breakdowns can lead to misestimations and scope changes, further complicating budget adherence.
Understanding these factors is crucial for identifying potential risks and implementing effective strategies to mitigate their impact.
03. The True Impact of Cost Overruns
Cost overruns don’t just affect finances; they can disrupt timelines, strain relationships, and damage reputations. Here are the key areas where their impact is felt:
- Delayed Project Timelines: Unexpected costs often lead to delays as teams scramble to secure additional funding or adjust project scopes. ERP construction software helps prevent these delays by making it easier to adjust budgets and project plans.
- Budget Strain and Reduced Profit Margins: Exceeding the budget not only diminishes profit margins but also places financial stress on the entire project. As costs escalate, contingency funds may be depleted, leaving little room for further unexpected expenses.
- Damaged Client Relationships and Reputation Risks: Frequent cost overruns can damage a construction company’s reputation, losing client trust and future business opportunities. Clients expect transparency and adherence to budgets; failing to meet these expectations can result in long-term repercussions for the contractor’s credibility in the industry.
Top Causes of Unexpected Costs in Construction Projects
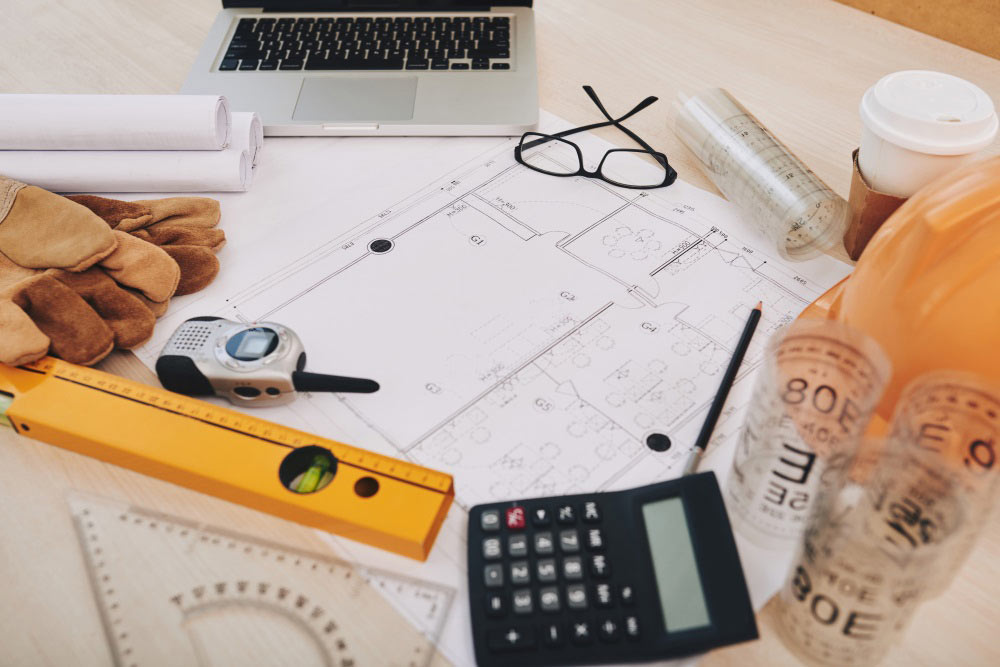
Unexpected construction costs often arise from various predictable yet overlooked sources. Identifying these areas helps teams anticipate and mitigate financial surprises effectively.
01. The Role of Inaccurate Initial Estimates
Inaccurate cost estimates are a leading cause of unexpected expenses in construction projects. These errors often arise from insufficient data, outdated pricing, or unrealistic assumptions during the planning phase.
When critical factors like labour, materials, and logistics are underestimated, the project budget can quickly spiral out of control. Failing to include contingency funds for unforeseen circumstances can also exacerbate financial strain.
To reduce this, teams must use modern estimating software, like Acumatica or Viewpoint Vista, and conduct thorough reviews to ensure accurate and comprehensive projections.
02. Hidden Challenges in Site Conditions
Unexpected site conditions can present costly obstacles during construction. Issues such as unstable soil, buried utilities, or contaminated land often remain undetected until work begins. These hidden challenges require additional time, specialized equipment, or remediation efforts, leading to budget overruns.
Poor initial site assessments can worsen these problems, causing delays and resource reallocations. Investing in comprehensive site surveys and geotechnical evaluations upfront can help identify and address potential risks early on.
03. Design Changes and Scope Creep
Design changes and scope creep are significant contributors to unforeseen construction costs. When project specifications are altered or expanded after work has begun, additional materials, labour, and time are required, inflating the budget.
Poorly defined project goals or inadequate stakeholder communication often lead to these issues. Unchecked, scope creep can disrupt schedules and strain resources, negatively impacting project outcomes.
Implementing strict change management protocols and maintaining clear project documentation can help minimize these challenges.
04. Market Volatility and Inflation
Market volatility and inflation can dramatically impact construction costs, particularly for materials and labour. Sudden price increases for essential items like steel or concrete can strain project budgets, especially for long-duration projects.
Labor shortages or fluctuating demand further complicate cost predictability. Currency exchange rates and global market trends also play a role in driving costs higher than anticipated.
To manage these risks, project teams should include contract escalation clauses and foster strong relationships with reliable suppliers.
05. Unforeseen Regulatory and Legal Requirements
Changes in regulations or legal requirements during a project can lead to unplanned expenses. Obtaining additional permits, complying with updated safety standards, or addressing zoning issues often involves time-consuming and costly adjustments.
Legal disputes, such as contractor disagreements or compliance failures, can also disrupt budgets and timelines.
Without proactive monitoring of regulatory changes, projects may face penalties or delays. Regular consultations with legal experts and adherence to compliance protocols can reduce these risks.
06. Major Disruptions (Weather, Natural Disasters)
Major events, including severe weather and natural disasters, can cause significant disruptions and unexpected costs. Heavy rains, storms, or floods can halt construction, damage materials, or require costly repairs.
These events not only delay timelines but also demand additional labour and equipment to resume progress. Seasonal weather variations may also necessitate schedule adjustments, further increasing expenses.
Comprehensive insurance coverage and robust contingency planning can help protect projects from the financial impact of these unpredictable events.
07. Human Factors: Errors, Miscommunication, and Conflicts
Human factors, such as errors, miscommunication, and conflicts, are common sources of unexpected costs in construction. Mistakes during execution often lead to rework, wasting time and resources.
Miscommunication between stakeholders can cause delays, misunderstandings, and budget overruns. Internal conflicts or disputes among contractors disrupt workflows and negatively impact efficiency. Lack of proper training or experience further compounds these issues.
Clear communication protocols, regular team meetings, and proper training programs are essential to minimizing human-related risks.
Strategies to Prevent and Manage Unexpected Costs
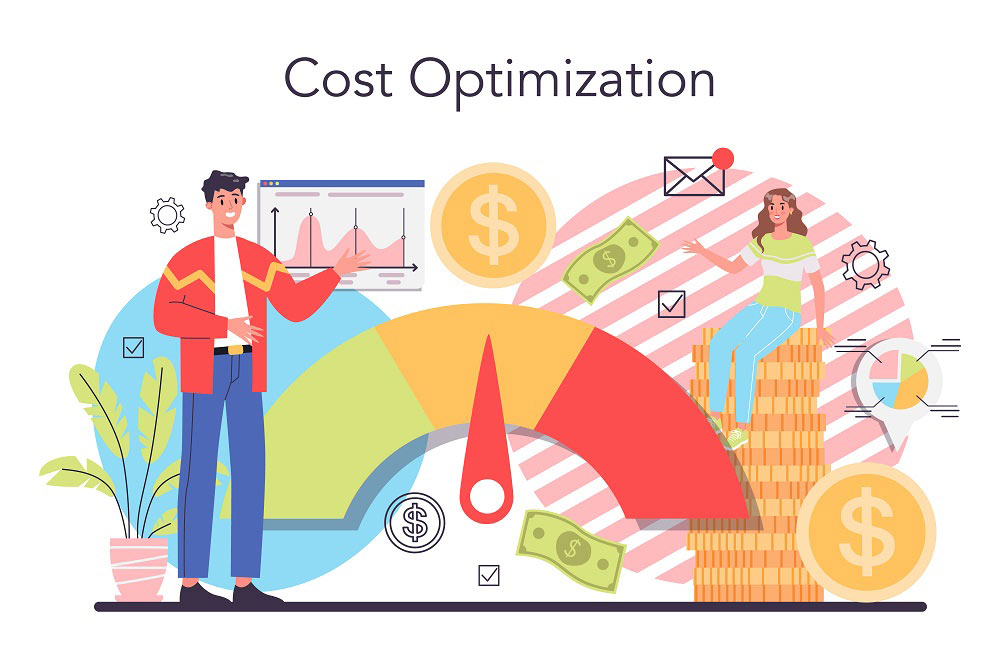
Managing unexpected costs in construction projects requires proactive strategies and effective planning. Tools like Anterra construction management dashboards can provide real-time insights, helping teams minimize financial risks and ensure smoother project execution.
01. Conducting Comprehensive Risk Assessments
Conducting a thorough risk assessment at the outset of a project helps identify potential problem areas that could lead to cost overruns. These assessments involve evaluating factors like site conditions, labour availability, and supply chain vulnerabilities.
Once high-risk areas are pinpointed, project teams can create detailed plans to reduce these risks before they escalate.
Regular risk reviews throughout the project further ensure preparedness for unforeseen challenges. Taking a proactive approach reduces uncertainty and builds a stronger foundation for success.
02. Building a Robust Budget Contingency Plan
A robust contingency plan is essential to manage unexpected expenses effectively. Setting aside realistic reserves, typically 5–15% of the project budget, ensures funds are available for unforeseen issues. This approach provides financial flexibility to handle emergencies without derailing the entire project.
To optimize the plan, regularly update contingency reserves based on ongoing project assessments and market conditions. A well-thought-out contingency strategy acts as a safety net, ensuring smooth project progression despite challenges.
03. Improving Initial Project Estimates
Accurate project estimates are key to avoiding budget surprises. Using advanced tools and software for cost estimation allows for more precise forecasting of materials, labour, and equipment costs. These tools factor in real-time market data and project-specific details, reducing the likelihood of errors.
Involving experienced professionals during the estimation phase adds another layer of reliability. Accurate estimates not only set realistic expectations but also minimize the chances of significant budget deviations.
04. Enhancing Communication and Collaboration
Strong communication and collaboration between field teams and office management are critical for preventing cost overruns. Miscommunication often leads to delays, errors, and resource mismanagement, all of which inflate project expenses.
Establishing clear channels for regular updates and fostering teamwork helps bridge gaps between stakeholders. Collaborative project management tools and regular meetings ensure everyone stays aligned, reducing the likelihood of costly mistakes or misunderstandings.
05. Using Advanced Technology for Real-Time Monitoring
Technology plays a vital role in tracking project progress and expenses in real-time. Tools like Building Information Modeling (BIM), project management platforms, and data analytics provide instant insights into budget performance and potential risks.
Among these, real-time dashboards for project insights stand out as an essential tool, helping project teams identify and address cost discrepancies early to prevent minor issues from escalating. These dashboards enable real-time monitoring, enhancing decision-making and allowing teams to make quick adjustments to stay within budget and on schedule.
06. Establishing a Clear Change Management Process
A well-defined change management process minimizes the impact of scope changes on the project budget. This involves creating protocols for evaluating, approving, and implementing changes efficiently.
Clear documentation of all change requests and their financial implications ensures transparency and reduces conflicts. By managing changes proactively, teams can avoid unnecessary delays and expenses, maintaining better control over the project’s financial health.
07. Negotiating Supplier and Subcontractor Agreements
Flexible and well-negotiated contracts with suppliers and subcontractors are essential to managing unexpected costs. Securing terms that account for price fluctuations or delivery delays helps cushion the financial impact of market changes.
Long-term partnerships with reliable vendors also improve cost stability and resource availability. Open communication during negotiations ensures both parties understand and agree to terms that accommodate potential uncertainties.
08. Investing in Staff Training and Development
Well-trained staff are better equipped to handle unforeseen challenges effectively. Investing in training programs improves team members’ problem-solving skills, ensuring quicker responses to unexpected issues.
Comprehensive development initiatives, such as workshops and certifications, also enhance their ability to work efficiently with advanced tools and technologies.
A skilled workforce reduces errors, improves resource management, and contributes to smoother project execution, ultimately minimizing additional costs.
Advanced Cost Management Techniques
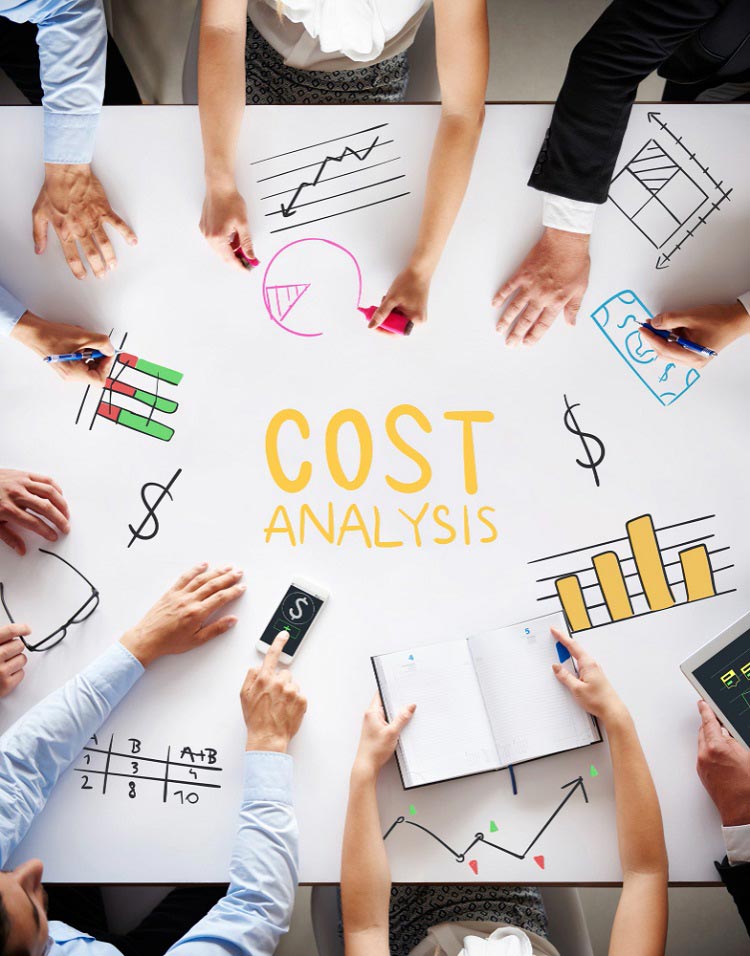
Advanced cost management techniques can help construction projects stay on track financially while maintaining quality and efficiency. By adopting innovative methods, project teams can better anticipate and manage potential cost challenges.
01. Data-Driven Decision Making
Data-driven decision-making uses predictive analytics to identify potential cost overruns before they happen. By analysing historical data and current trends, teams can forecast issues like material price spikes or labour shortages.
This approach helps in setting realistic budgets and planning mitigation strategies. Tools like data visualization and reporting software provide clear insights, enabling more informed and proactive decisions.
Harnessing the power of data ensures better control over project costs and minimizes unexpected financial surprises.
02. Implementing Escalation Clauses in Contracts
Escalation clauses in contracts protect against sudden price increases for materials or labour. These clauses allow for adjustments in payment terms when market conditions change, ensuring fairness for all parties involved.
By incorporating such clauses, contractors can reduce financial risk while maintaining relationships with suppliers and subcontractors.
Clear terms and transparent communication during contract negotiation ensure that escalation clauses are effective. This proactive measure safeguards the budget without compromising project progress.
03. Adopting Modular and Prefabricated Construction
Modular and prefabricated construction offers significant cost-saving benefits by moving parts of the building process off-site. These methods reduce labour expenses, material waste, and construction time.
By manufacturing components in controlled environments, teams can ensure higher quality and efficiency. Additionally, fewer on-site disruptions mean lower indirect costs, such as equipment rentals or extended project timelines.
Prefabrication is an innovative approach that delivers both financial and operational advantages for construction projects.
04. Exploring Value Engineering Options
Value engineering involves finding ways to reduce costs without compromising quality or functionality. This process identifies alternative materials, designs, or construction methods that achieve the same goals at a lower expense.
By collaborating with architects, engineers, and contractors, teams can explore creative solutions that balance budget and performance.
Value engineering also ensures compliance with project specifications while optimizing resource allocation. It’s a thoughtful approach to managing costs while delivering high-quality outcomes.
Real-World Examples: How Companies Managed Unexpected Costs
Real-world examples offer valuable insights into how construction companies can effectively manage unexpected costs. By learning from successful strategies, teams can be better equipped to handle financial challenges in future projects.
Case Study 1: Managing Scope Creep on a Large-Scale Project
A construction company managing a large office building project faced significant scope creep when the client requested several design changes midway through the project.
To tackle this, the project manager implemented a formal change request process, ensuring all alterations were documented and evaluated for their impact on costs and timelines.
By setting clear boundaries on what could be altered and integrating these changes into a revised budget, the team was able to manage the additional costs without disrupting the overall project schedule. This proactive approach minimized unexpected costs and ensured that client expectations were met.
Case Study 2: Overcoming Supply Chain Challenges Amid a Pandemic
During the COVID-19 pandemic, a construction company struggled with supply chain disruptions that caused delays in the delivery of critical materials. To address this, the company diversified its suppliers and negotiated flexible delivery schedules to account for potential delays.
They also maintained a close relationship with their suppliers, allowing them to anticipate shortages and secure materials in advance.
Through strategic planning and flexibility, the project stayed on track despite the unpredictable circumstances, demonstrating the importance of adapting quickly to unforeseen challenges in the supply chain.
Case Study 3: Leveraging Technology to Stay on Budget
A construction firm working on a residential development project leveraged advanced project management software and building information modeling (BIM) to stay within budget. The technology allowed for real-time tracking of costs and material usage, identifying discrepancies early on.
Using BIM, the team could visualize the project in 3D, which helped in detecting potential design issues that could lead to extra costs.
This proactive use of technology allowed the firm to quickly address issues, streamline resource allocation, and make informed decisions, ultimately ensuring that the project was completed within the planned budget.
FAQs
01. What are the most common causes of unexpected costs in construction?
Unexpected costs in construction often arise from scope changes, inaccurate initial estimates, unforeseen site conditions, and material price fluctuations. Delays due to weather, regulatory changes, or supply chain disruptions can also contribute. Proper planning and risk assessment can help mitigate these risks.
02. How can technology help in managing construction costs?
Technology, like project management software and BIM, helps track costs in real time, improving budgeting accuracy. Predictive analytics and automated tools can identify potential overruns before they occur. These tools enhance collaboration, streamline workflows, and reduce human error.
03. What is the role of risk management in construction budgeting?
Risk management helps identify potential issues early and allows for the creation of contingency plans. It ensures that all possible cost risks, such as labour shortages or site delays, are accounted for in the budget. A solid risk management strategy reduces the chance of budget overruns.
04. How much should be allocated for contingency in a construction project?
Typically, 5-10% of the total project budget is set aside for contingency, depending on project complexity and risk. High-risk projects may require a higher allocation to cover unforeseen challenges. Adjusting the contingency amount throughout the project ensures flexibility in managing unexpected costs.
05. What strategies can minimize cost overruns?
To minimize cost overruns, focus on accurate initial estimates, strong project planning, and regular monitoring. Clear communication with stakeholders and well-defined contracts also helps. Implementing a contingency plan and utilizing technology to track costs can further reduce financial risks.
Also Read: Effective Strategies for Managing a Construction Project from Beginning to End