The manufacturing process of the decorative laminates involves many steps starting from impregnating the paper to thermosetting to finishing.
The manufacturing process of decorative laminates involves the following steps:
Manufacturing Process of Decorative Laminates
Step 1 – Impregnating the Paper:
01. The back of a laminate sheet is made of a type of Kraft paper that can be saturated soggy and tearing
- A theatre drenches it with resin containing phenol (compound derived from benzene)
- The resin does not merely coat the paper it is absorbed right through
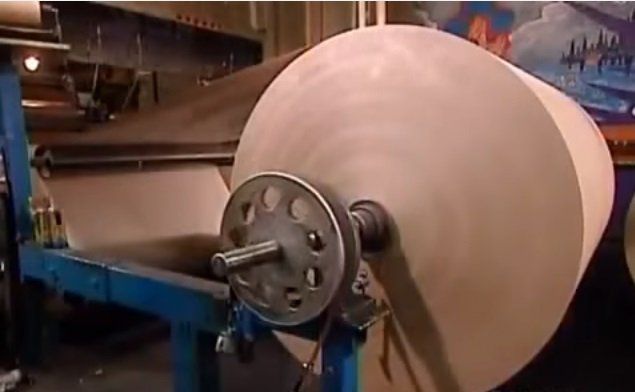
Courtesy – Ian Collier

Courtesy – Ian Collier
02. The top of the laminate is called the decorative layer. It’s a sheet of paper in either a printed design or solid color.
The manufacturing process is different for both solid color paper and Printed design layer as follows:
a) Solid Colour Paper:
- They go through a process that impregnates them with more durable melamine resin.
- The durability is essential because the decorative layer must withstand wear and tear.
- Two big rollers ring out the excess resin. The resin treatment makes the paper stiff and brittle
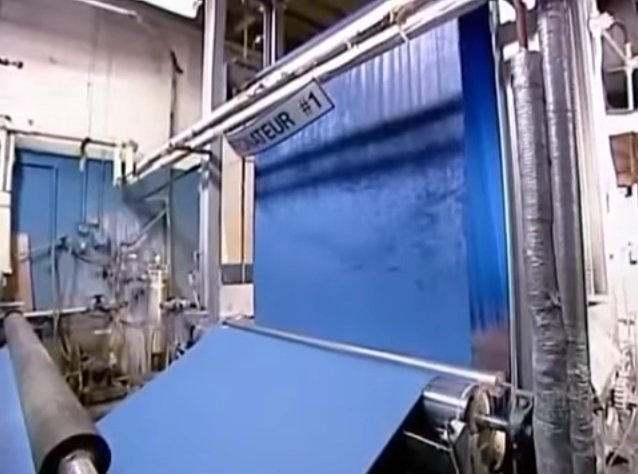
Courtesy – Ian Collier
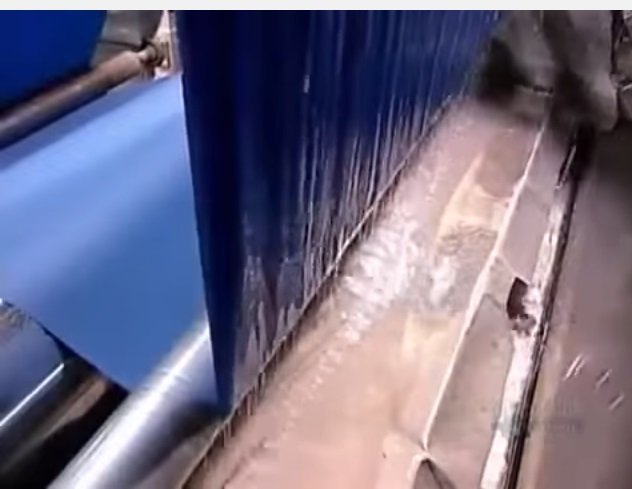
Courtesy – Ian Collier
b) Printed Design Decorative Layer:
- Workers start by cutting them into sheets, the same length as the craft paper.
- These papers don’t go in to theatre to be saturated with resins instead they are stacked by placing an overlay on each one
- Overlay is a transparent sheet of paper that is saturated with melamine resin.

Courtesy – Ian Collier
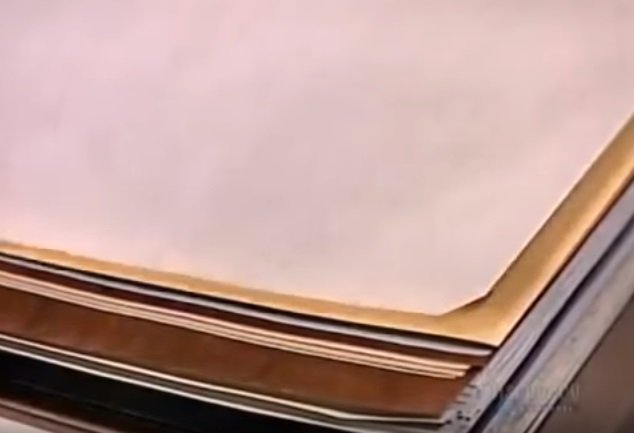
Courtesy – Ian Collier
Step 2 – Drying:
The saturated paper now goes through a drying oven, where hot air dry’s the resin in matter of seconds. With the resin now cured a cutter slices the paper into sheets.
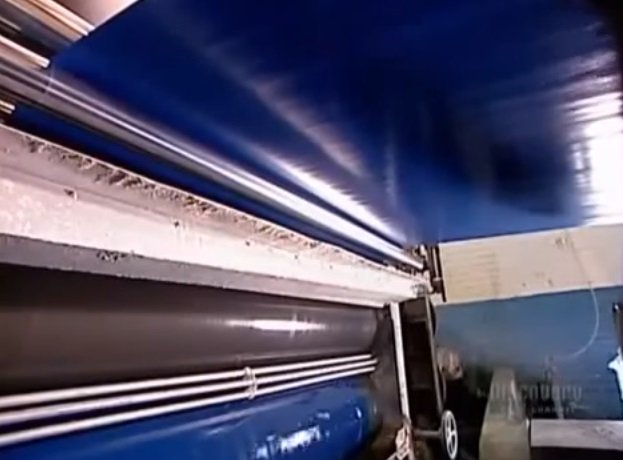
Courtesy – Ian Collier
Step 3 – Stacking:
Now a saturated Kraft paper is placed under each decorative layer. On top of each decorative layer a textured plate is laid, this will prevent the finished laminates from sticking together. The solid color paper is also stacked with these sheet, they don’t need an overlay.
Step 4 – Thermosetting:
Everything now comes into a press.
The intense heat and pressure compress the layers.
Overlays bond to the printed papers and the saturated craft paper bonds to each decorative layer creating laminate sheets. The textured plates between each set meanwhile imprints their print on to the heat softened resin, texturing the laminate surface.
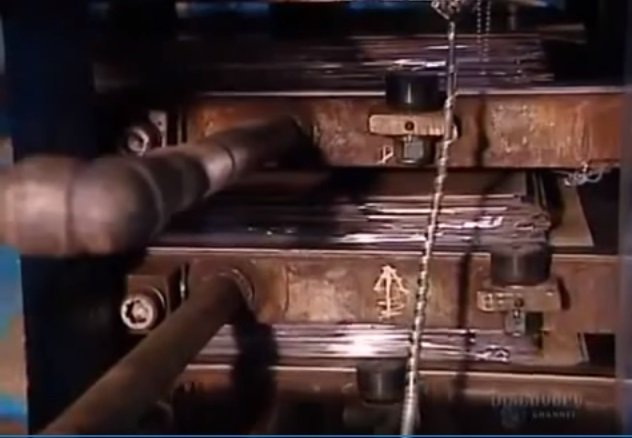
Courtesy – Ian Collier
Step 5 – Finishing:
On finishing line machines trim of any excess paper on the edges and sand the back of the sheets. This helps the laminate to adhere better to particle board or other substance.
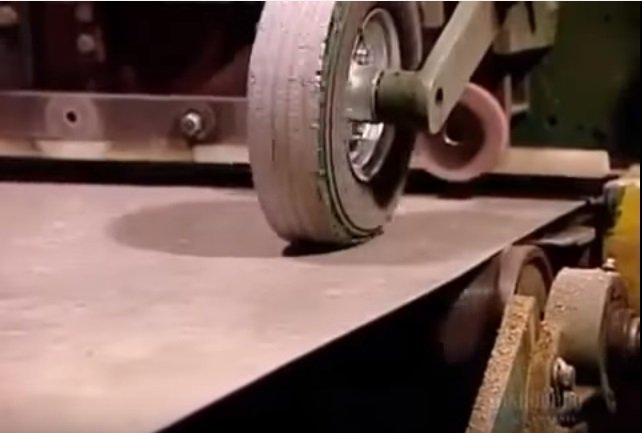
Courtesy – Ian Collier
