In this ever-growing world, the waste generation is multiplying with every passing minute. The quantum of waste generation is scary as it leads to ecological imbalance. Though commendable work is done regarding creating awareness about plastic wastes, the education regarding glass recycling is low among the masses. Recycling of waste materials is green way of living since it reduces the depletion of resources and avoid dumping of waste in seabeds and landfills.
Glass is recycled by engaging with different communities to collect glasses in the form of bottles and others from landfills, dumpsites, households and institutions. Thereafter, the glass is processed through an efficient system to produce glass pieces of desired shape and size. Here, we have discussed recycled glass as an interior designing material.
How is Glass Recycled?
According to ‘Glass Packaging Institute’, “Glass can be recycled completely and endlessly without loss in quality or purity”. The entire recycling process starts from collecting the glass containers, either from kerbside boxes, bags, and bins or from recycling banks. After The sorting and separating of the materials kerbside, the glass is taken to a nearby recycling company. Glasses are delivered to a reprocessing company. Glass is initially screened to remove the contaminants like corks and metal lids. The glass is then crushed and sent to the glass manufacturing company to produce desirable products. The crushed glass is known as “cullet”.
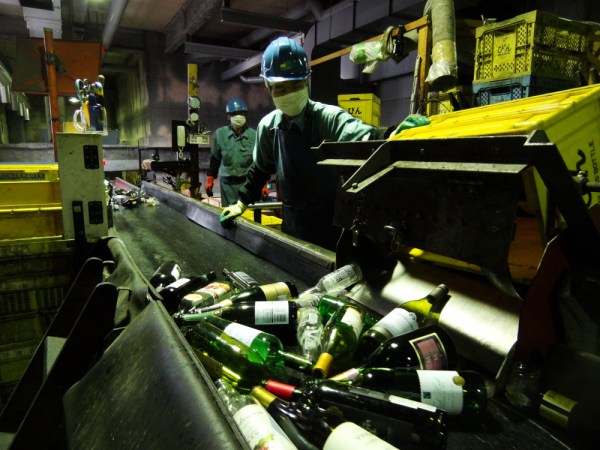
Recycling of Glass
Contrary to the general misconception of going green is an expensive endeavor, recycling the glass or repurposing it in some way is a very cost-effective solution. Additionally, you are also salvaging and reducing the consumption of glass. Recycled glass is an extraordinary green product, which can be used in many ways to furnish your house. Hence, we discuss some of the ways recycled glass can be used,
01. Recycled Glass Countertops
02. Bio Glass
03. Foam Glass
01. Recycled Glass Countertops
Countertops made from recycled glass are more affordable, durable and greener alternative to marble or granite-based countertops. The main aim behind the manufacturing of the recycled glass countertops is to take the waste glass product and transform it into an artistic interior material. It is done by processing recycled glass into stunning countertops that are strong and durable as granite.
Glasses that are used to manufacture recycled glass countertops can be anything like,
- Wine Bottles
- Beer Bottles
- Water Bottles
- Building Demolition Glass
- Tinted Window Glass
- Shower Door Glass
- Storefront safety glass and many others
Why Choose Recycled Glass Countertops for Your Interiors?
The first and foremost reason is that they are made from recycled glass, a locally available material. All the materials used in this product are post-consumer materials and help in reducing the ecological footprint.
This product consists of 80% crushed glass and 20% binder that holds the glass together. The binder used in the manufacturing process is resin free cement binder making the product completely green and environment friendly.
They are very affordable. The cost of recycled glass countertops is actually less compared to marble or granite countertops. Moreover, they are available in a wide range of colour and texture ranging from different coloured glass to different binder colours.
Apart from countertops, they can also be used for various other interiors such as tables, fireplaces or literally any surface where you want to replace stone.
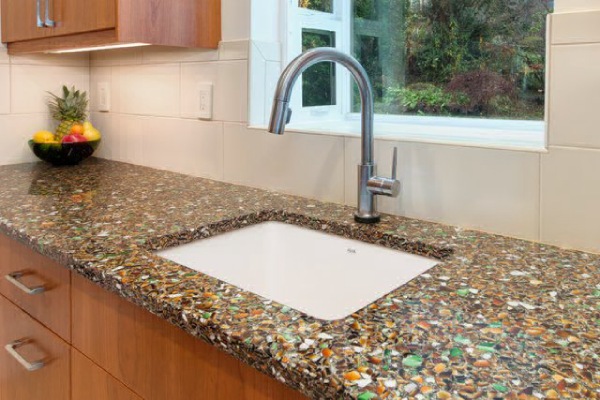
Recycled Glass Countertops
Manufacturing Process of Recycled Glass Countertops
(a) Mixing of Raw Materials
The glass collected is separated by its colour. The designer of the countertops puts the specific colours into the specified mixer based on the design of the finished product. The glass is then blended with cement and other binding agents. The recycled glass is 85% of the material, but a number of other materials are also added which gets recycled in the process like fly ash.
Fly ash helps to bind the materials and essentially turn them into a hard and durable countertop that is almost concrete like. Fly ash is a waste product removed from the smoke stacks at coal burning power plants which were dumped at the landfills until its utility was researched. Fly ash has properties that are similar to cement which makes it an alternative material to be used in concrete. It is very popular in green building products, nowadays.
(b) Pouring & Compacting
After the glass mixture is ready, it is poured into a mould to settle. The mould is then transferred over to the vibration table to consolidate the material. The table shakes heavily and allow the glass to flatten at the bottom of the mould, which is nothing but the top of the counter.
(c) Curing & Polishing
Once the glass is settled, the entire mixture is put into a curing oven to harden overnight. Thereafter, when it comes out of the curing oven, it looks like a raw slab of concrete. Later, it is transferred on to the polishing bed, where diamond abrasive bed is used to expose the glass and polish it up, to look like a countertop material. These diamond abrasive machines come from the granite industry where they’ve been used for polishing granite stones. This technology has been used for centuries, and the same technology is adopted for polishing the glass countertop slabs.
The last step of the process is to apply a chemical freeze sealer to the countertop. The slab is given is a final check and is shipped out. However, that is not the end. This recycled glass countertop can be recycled again.
02. Bio-Glass
Bio-Glass is an environment and future friendly material, which is made up of 100% recycled and recyclable glass without the use of any colorants or additives. Additionally, it has a Silver Cradle to Cradle Certification.
During the manufacturing of bio glass colorants, epoxies or resins are not added and it is made of a 100% post-consumer recycled glass obtained from,
- Beer bottles
- Wine bottles
- Other bottles or jars that are diverted from the landfill
Bio-Glass serves as a solid surfacing for countertops, walls, floors, and other applications. It is manufactured by heating and agglomerating the materials under pressure. Bio-Glass is available in many sizes and colours. It can be used for counter or worktops, interior flooring, walls as well as other decorative purposes.
Bio-Glass received the “Interior Innovation Award – Winner” in the “Wall, Floor, Ceiling” products category in the year 2014.
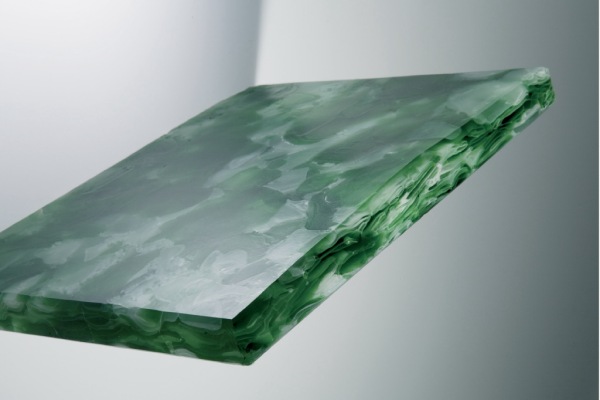
Bio-Glass
Material Properties of Bio-glass
- The texture is smooth and has a satin type glossiness.
- The translucence property of the product ranges from 0-50%.
- The fire resistance and UV resistance of the product is very high, whereas the weather resistance is moderate.
- The product is heavy weight and odourless.
- It has good scratch resistance as well as chemical resistance.
- It is available in sheet sizes measuring 110” x 50” x ¾” or 280 cm x 127 cm x 2 cm thick.
- Bio-glass does not contain any hazardous ingredients. Bio-Glass materials are non-reactive. When burnt, no known hazardous by-products are emitted.
- Bio-glass has a closed surface and all panels are supplied with facetted edges. Hence cleaning with all the traditional cleaning agents and solvents is possible.
Why Choose Bio-Glass for Your Interiors?
Bio-glass is an ecologically intelligent material that offers a low environmental impact solution without compromising on the aesthetics. Also, it is made from a 100% recycled glass taken from different waste streams like bottles, old plates, etc. and are pressed together into slabs.
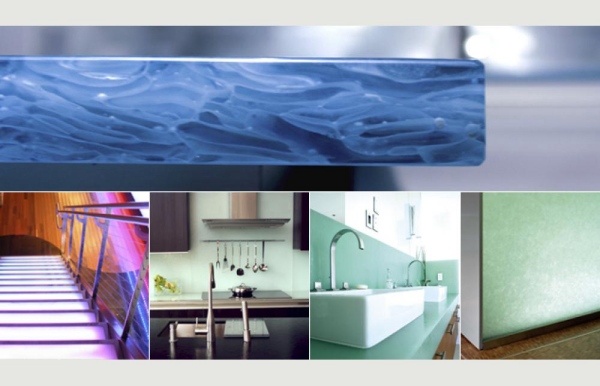
Interior Design using Bio-Glass
Bio-glass is most suitable material for partitions, facades, and other decorative surfaces. It is as durable as granite and, being a closed surface, it can be easily maintained.
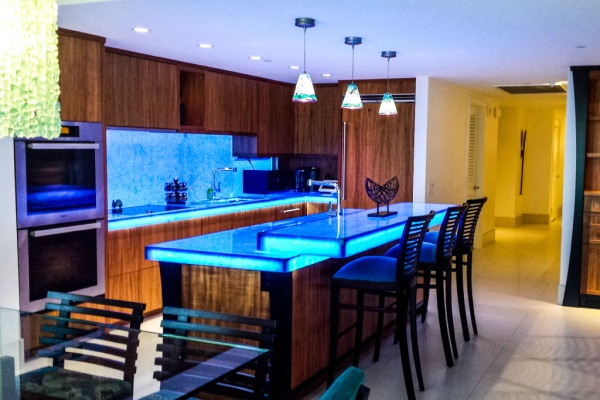
Bio – Glass Countertops
03. Foam Glass
The key to both ease of construction and reducing environmental impact are these recycled foam glass blocks. Foam glass provides a sponge like insulation made by melting powdered glass. Foam glass is made by melting glass and adding small bits of coal to it. The thin glass cell structure present in foam glass makes it easy to cut and shape desirably. Additionally, it prevents the glass from shrinking and swelling over time. They are fireproof and the closed cell structure of foaming glass provides insulating power to reduce energy use.
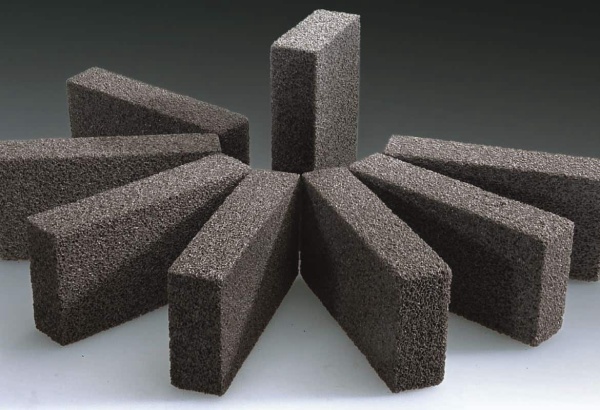
Foam Glass
Material Properties of Foam Glass
- It is over 10 times lighter than concrete, and can be easily assembled in a metal or wooden frame.
- The foam glass also gives the communities DIY construction a speed boost.
- To install a wall using these energy saving bricks require only two people, one for fetching the blocks and the other for placing them. Construction using foam glass is extremely simple and fast.
- Made from closed pores of pure glass, it is entirely waterproof.
- Consisting of glass and coal, it will not deteriorate with age and lasts long.
- Being entirely inorganic, it neither rots not gets damaged by insects and rodents, but create a healthier living environment.
- Made up of pure glass, it is non-combustible and does not distribute fire or produce poisonous gases.
It has good sound proofing and heat proofing properties.
Why Choose Foam Glass?
Apart from the benefits of using recycled material and their ease of assembly, these foam glass blocks have a few more tricks up their sleeve as mentioned above. Hence this product is the kind of product that should be used in the future. The technology used in the manufacturing process of foam glass is very energy efficient. By using this foam glass technology, around 65- 80% energy can be saved. Altogether, foam glass is a combination of security, energy efficiency, soundproofing and greener planet.
Manufacturing Process of Foam Glass Countertops
The raw materials used for this new building material are piling up at the most recycling facilities, i.e. The post-consumer recycled glass. Specifically, LCD glass is used in the manufacturing process of this product. The mineral additives make the screen glass conductive and also extremely hard to melt.
The LCD panel glass is broken up and crushed into powder. Then, silo is filled with the powdered screen glass. The recipe also includes a foaming agent and mineral additives. After the ingredients are mixed together, heat approaching 10000 Celsius is applied to the glass cake batter. This results in melting of the material and triggering a reaction that produces gas bubbles. The slabs of foam glass continue to rise as they are set to cool like giant brownies.
The reaction slows as the material solidifies, trapping the bubbles inside and creating the closed cell structure that is the key to its insulating ability. The slabs are removed from their moulds and cut into uniform size. If the entire process has been followed precisely, the material composition bubble size and the density will give the foam glass its desired properties.
In the final note, we have a lot of waste glass in our society and it is possible to use these waste glasses to make an interior material for beautiful dream homes. Reuse of those glasses can help in waste management as well as sort out the problem of disposal of waste glasses. Recycled glass is the best option for interior design. It’s an eco-friendly material without compromising on the aesthetic appearance of a home. With these significant benefits, it’s also an affordable and locally available green building material.
Also Read
Concrete Countertops: All You Like to Know!
Corian Countertops: Know Pros & Cons before you Spend!
Image Courtesy: Image 2, Image 3, Image 4, Image 5, Image 6, Image 7
Author Bio
Arfa Falak – My name is Arfa Falak and I have my graduation in BE (civil). I live in Bangalore. I am an aspiring design Engineer.