Concrete sealer or coat is a thin or thick protective film which protects the surface of old or new concrete against damage, corrosion, staining, etc. by sealing the entry of water, harmful chemical, gases, etc.
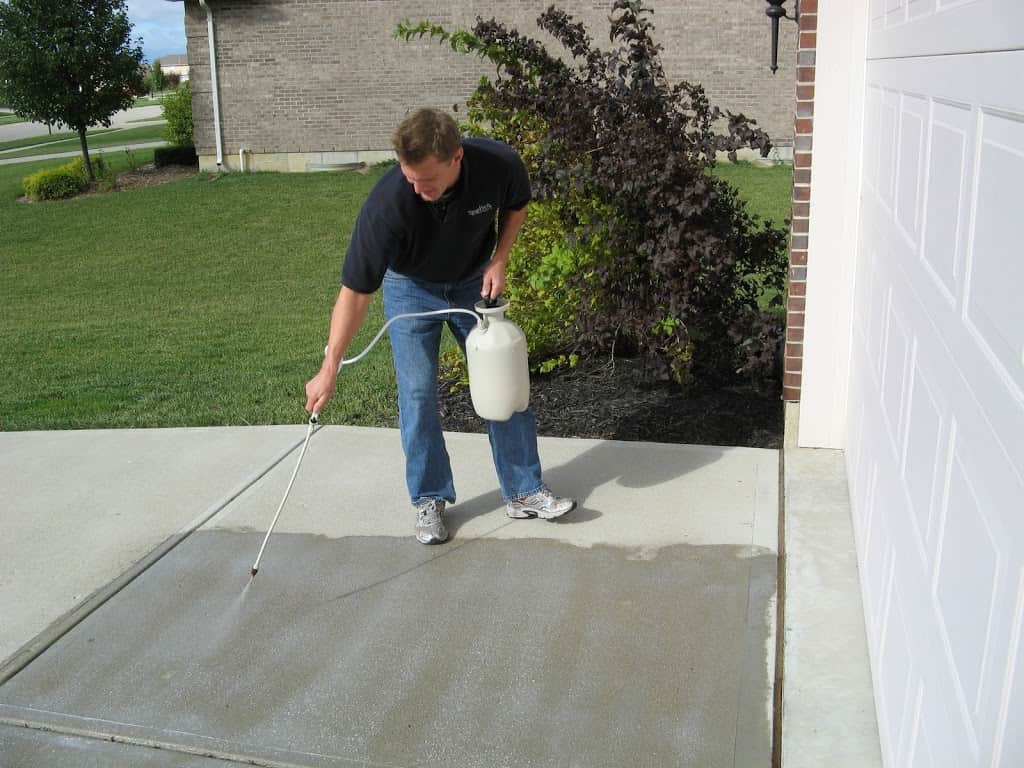
Nowadays, concrete sealing and coating compounds are applied to dry concrete as a maintenance and repair procedure to reduce or prevent the penetration of water, aggressive solutions, or gaseous media. They are used to prevent the deterioration due to corrosion of steel, freeze-thaw, carbonation, or chemicals damage. The sealing and coating materials are suitable to seal concrete surfaces and cracks in concrete that is in overall good condition.
Key Benefits of Sealing or Coating of Concrete
- It increases the service life of the concrete house
- It improves the appearance of the house
- It adds value to the home
- It reduces chances of occurrence of spalling, flaking, and cracking in concrete
- It protects from oil spills and various other stains.
- It resists the mildew
- It reduces the time of repair-maintenance during repairing as some of the sealers gets dried within 1 to 3 hours after the application
- It is effective and easy to use
- These compounds are easily available in the market as they are produced all over the world
- Epoxy concrete floor sealers are more suitable for the floor when it is applied in the thicker film
Nowadays, different types of paints, coating (which forms membrane) and surface penetrating chemicals are manufactured, and they are sold as sealing compounds for concrete surfaces.
There are mainly three basic types of protective surface treatment performed on concrete.
01. The concrete surface can be treated with a coating that just covers the surface. These treatments are typically polymeric materials such as epoxy, polyurethane or polyurea.
02. The concrete surface can also be protected with low viscosity cracks sealers which are used to fill the voids and cracks of surface. They can be applied by flooding the surface, spraying onto the surface, or placing into cracks up to the width of 0.002 inches to 0.5 inches (0.05 mm to 12 mm). These surface treatments are typically low viscosity epoxies, high molecular weight methacrylates (HMWM), and urethanes.
03. The concrete surface can be treated with the surface sealers. Surface sealers saturate the concrete surface with a penetrating water repellant compound. It leaves the pores and cracks open, but it stops the ingress of water from the treated concrete surface. These materials do not rebond cracks, but it seals the cracks up to the width of 0.002 inch (0.05 mm) or smaller. Silane or silixane based water repellent and sodium silicate solution are two types of surface sealing treatments which are widely used in the concrete industry nowadays. Both are based on silicon technology.
Depending on the condition of exposure and anticipated use, silanes, siloxanes, HMWM, and low viscosity epoxies can be used. Nowadays formulations of the newer gels and creamy chemicals seem to be the most effective in achieving deeper penetration
Sealing Compound for Concrete
There are several concrete sealing technologies which are effective for reducing water infiltration in the structure. Here are details of majorly used sealing compounds for the concrete.
01. High Molecular Weight Methacrylic Sealing Compound (HMWM)
This type of sealing compound is very effective and they are known as a high molecular weight methacrylic healer-sealer. This compound can penetrate into concrete surface up to a depth of about 1/16 inch (1.5 mm) or less, but it is most effective in sealing fine cracks in the concrete or mortar surface. A properly applied methacrylic sealing compound will stay up to 10 years.
It is used above or below the concrete or mortar surface and helps to protect the surface against the attack of water and other harmful chemicals. Generally, it is applied to the horizontal deck slabs, patio, driveway, parking garages, and other surface exposed to foot and pneumatic-tire traffic.
The chief manufacturers of high molecular weight methacrylic sealing compound are Sika, Fosroc, Chemmaster, Kwikbond, etc.
02. Low Viscosity Epoxy Sealing Compounds
Low viscosity epoxy sealing compounds are somewhat easier to use than high molecular weight methacrylic sealing compound (HMWM). They have more flexibility in cure times than the HMWM. However, they have a higher viscosity than HMWM, hence they cannot penetrate into fine cracks effectively.
This sealing compound is composed of an epoxy resin and the appropriate hardener. Sometimes, these types of epoxies are formulated to penetrate into fine cracks in concrete. They are easily sprayed over the horizontal concrete surfaces with the brooms or squeegees. The use and performance of theses sealer is very similar to an HMWM. If properly applied, these materials stay up to 7 to 10 years on the surface of the concrete.
The key manufacturers of low viscosity epoxy sealing compound are Sika, Fosroc, Chemmaster, Kwikbond, etc.
03. Silane and Siloxane Sealing Compound
Silane and siloxane sealing compounds are becoming popular due to their effective use to seal the concrete surfaces and to fill the cracks smaller than the width of 0.002 inch. They are used to reduce the penetration of water into the concrete and cracks. The silane and siloxane solids are mixed with water or alcohol or mineral spirits that evaporates from the concrete after the application. Solvent-based sealers work better than water-based sealers. It does not change the appearance of the treated concrete. Theses sealing compound does not protect the concrete which is in water, except for short periods. Silane and siloxane sealing compond will protect the concrete up to 5 to 7 years.
Coating Compounds for Concrete
The concrete coating can be classified into four categories.
01. Waterproofing Coating Compounds
Waterproofing is typically used to prevent the flow of water into or out of concrete. Waterproofing is generally done on surfaces that are exposed to water. The waterproof coating is generally thicker films of asphalts, urethanes, or epoxies. They can be spray applied or installed in layup sheets. We have already discussed the need of waterproofing for your house. It is a general guide of waterproofing and the brief introduction of different types of damages that may occur to the building if waterproofing is not done.
02. Damp-Proofing Coating Compound
Damp-proofing is used to seal the porosity of concrete and prevent absorption of water. It is generally a thin film asphaltic emulsion and is not usually effective against hydrostatic pressure. Damp-proofing is used to seal concrete and masonry structure to prevent the water absorption and to prevent the damage due to freeze-thaw action.
There is a minor difference between the damp proofing and waterproofing treatments. Know more about damp proofing vs waterproofing.
03. Decorative Coating Compound
Decorative coatings change the appearance of concrete and masonry to enhance aesthetics. Decorative coatings and sealers can be used to obtain a specific color or texture, to increase stain resistance, and to make it easier to clean and to maintain an acceptable appearance.
04. Barrier Coating Compound
Barrier coatings are installed over concrete and masonry to form an insulating and physical barrier to protect against their service environment i.e corrosive elements. Barrier coating protects the concrete and masonry from the exposure of chemicals/gases.
The success of coating largely depends upon the carefulness in the surface preparation, selection and application of coating material. Some of the examples of coating material are epoxies, acrylics, polyurethanes, polyureas, vinyl esters, chlorinated rubbers, and elastomeric coatings. Many concrete coatings are not able to seal the cracks in concrete, so be careful while selecting the surface coating
You can find the latest coating and sealing compounds on Gharpedia – Materials Exhibition.
Whether the concrete surface is new or old, it is necessary to understand the product before you carry out the coating or sealing of concrete. Hence know the packaging details, coverage, surface preparation guide, mixing tips, and application procedures of coating or sealing compound which are specified in the manufacturer’s catalogue sheet.
Read More:
5 Valuable steps of repairing of concrete!
How to Repair Concrete Cracks in RCC Structure or House?
How to repair damaged concrete which is under attack of corrosion!
Image Courtesy: Image 1