General practice is to check when the beam and slab elements are ready for concreting i.e. reinforcement fully tied up but ideal practice would be to check it in two phase i.e.
01. First check formwork before you allow placing of reinforcement. This is necessary as certain formwork defects can’t be corrected or are difficult to correct after reinforcement is placed in position.
02. Checking reinforcement.
Things to Check Before Concreting Beams & Slabs
Hence as a standard engineering practice one should check first the formwork before reinforcement is placed or tied.
01. Centering and shuttering / Formwork
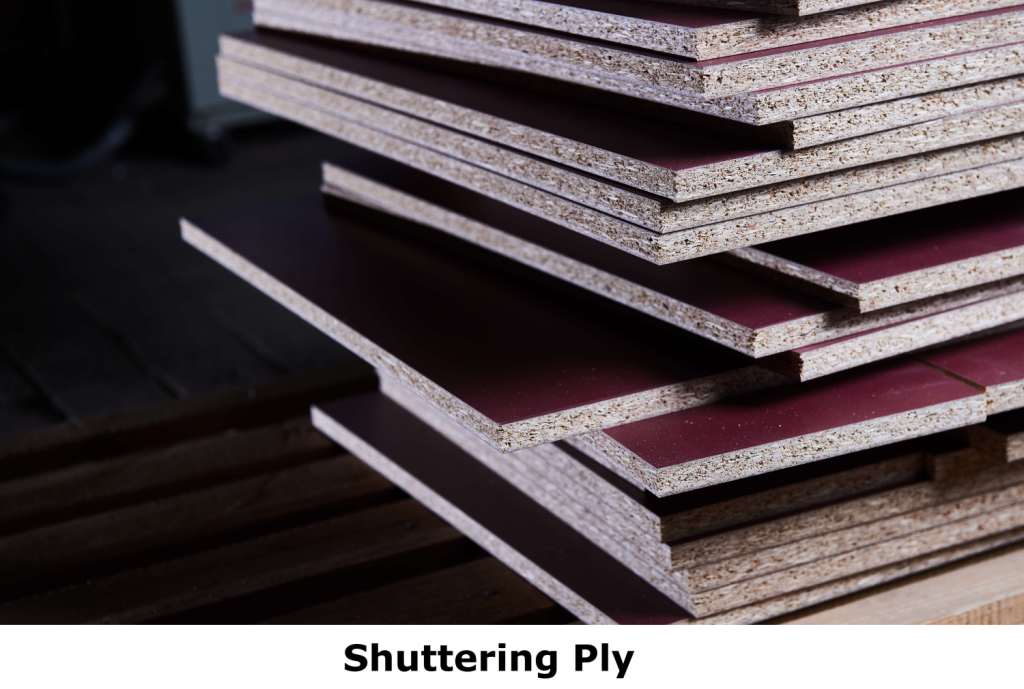
Image Courtesy- 123rf
- First check the quality of shuttering plates. Avoid using plates with uneven surface and damaged edges. They must be of regular size.
- If plywood is used, it should be of BWP grade and durable under alternate wetting and drying conditions.
- Take approval for shuttering from Engineer-in-charge or supervisor before tying reinforcement.
- Engineer-in-charge or supervisor must check the slope, level of slabs and beams before placing reinforcement in position. Preliminary inspection should be done even before commencing tying of reinforcement.
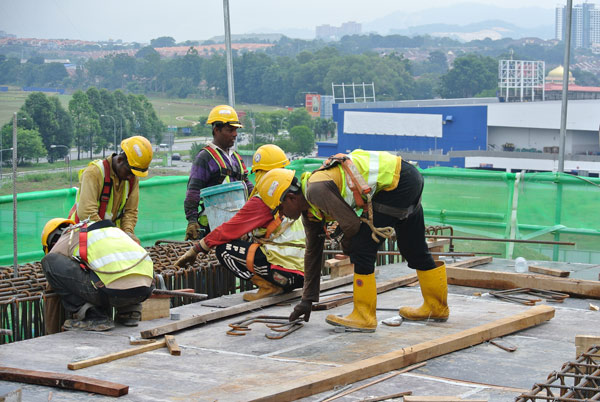
Image Courtesy 123rf
- Shuttering should be hard enough to withstand the load of concrete and impact of placing of concrete and vibrations.
- Oil or mould release agent should be applied on shuttering plates so that shuttering can be easily removed after concrete gets initial strength.
- 12 mm diameter PVC pipe nipples should be provided before casting of sloping roof. These nipples will be useful for cement grout after slab is concreted. The grouting is needed as however great precautions you may take while concreting sloping roof, the slab is liable to leakage. The grouting will reduce the leakage.
- Mark one level on every column as per beam depth.
- Position and level of beam bottom supports should be with respect to the depth of the beam.
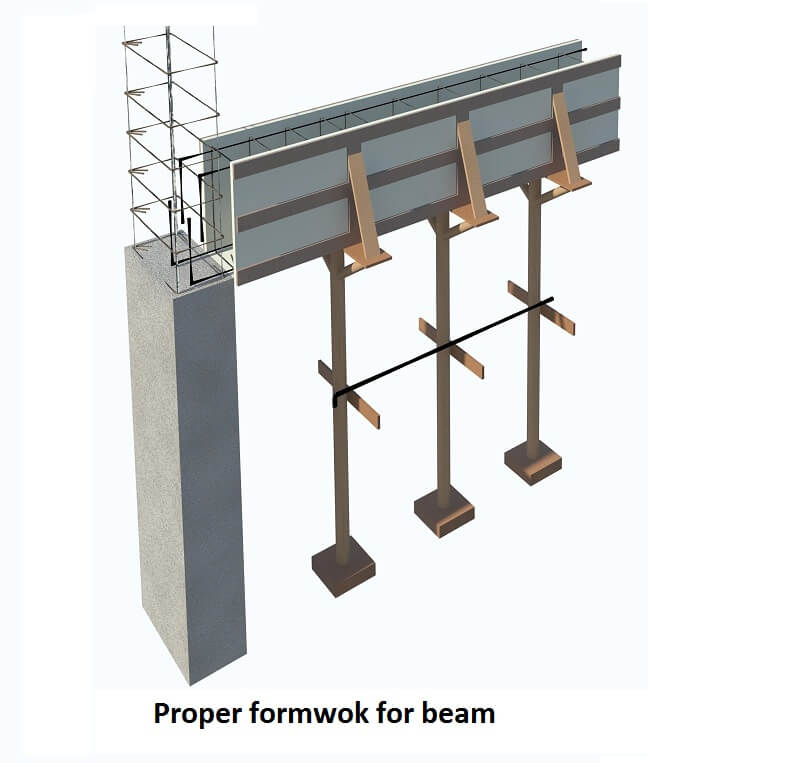
- Bottom plank of the beam should be straight. It should not be bent.
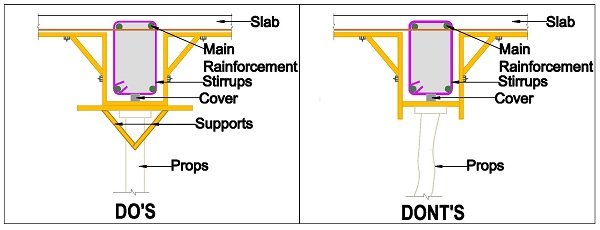
- Joints of beam bottom should be properly propped so that formwork doesn’t bulge during concreting.
- Before providing beam sides, level of the beam bottom should be checked.
- After levelling of beam bottom bracing should be provided.
- The plumb of beam sides at each end should be checked with the help of line dori. Shuttering of beam column junction should be in plumb and watertight.
- Formwork joints in beam sides should be taken at the end of beam.
- Before casting a slab, all shuttering gaps must be properly closed giving particular attention to column cap, beam junctions, beam side to slab bottom junction and beam side to beam bottom junction as well as jointing between two plates.
- Adjustable plates (gabadi plate or gap plate) should be used to avoid gabadi in particular bay. Contractors are ignorant about repairing the small This affects the strength of concrete.
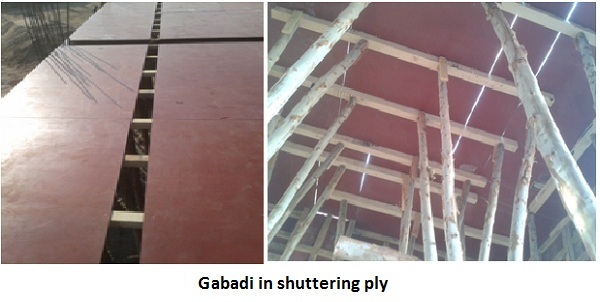
- In such cases, contractors use scrap material where it is not possible to place shuttering plates and bottom of slab is not in same level. It affects the thickness of plaster.
- The slab thickness should be marked on the side of slab as per the thickness of slab.
- Wooden props should be avoided as far as possible. Wooden props, if used, check for soundness, proper sizes, plumb and see that they are not butt spliced.
- Props must be braced in both directions by tubes and fixed couplers.
- Wooden plates are not recommended as due to surface deformations they give uneven surface resulting in increasing the thickness of ceiling plaster.
- All the props must be in proper alignment, plumb and not jointed more than 20%. Props must not get staggered.
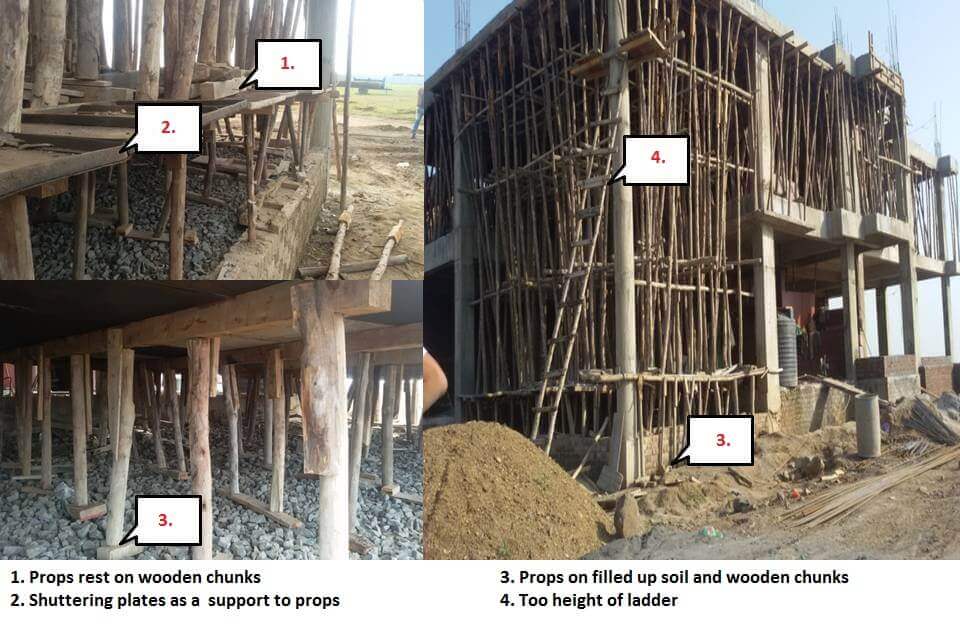
- All the props must be kept vertical by providing wedges and cross bracings. Do not use bricks or blocks below props to adjust height. Contractors fix the props in a slant position to avoid cutting of props or to utilize short prop they give more packing below the prop. They are dangerous and may slip while concreting and invite failure of cantilever formwork.
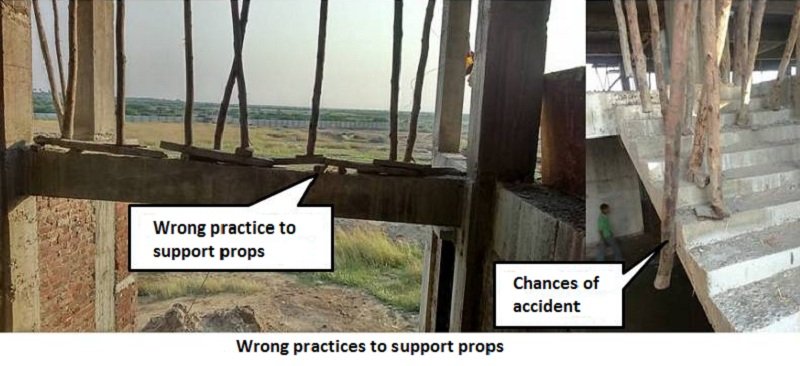
- Individual prop must be braced both ways with continuous runners and prop system braced laterally.
- Minimum spacing between props should be 0.60m (2.0′) center to center in case of wooden props and M.S. props.
- Extra care need to be taken when cantilever slab (for Balcony) has to cast at first floor. In this case let’s say plinth height is 0.9 meter & floor height is 3 meter then total height of the props would be 3.9 meter. In this case, sometimes it may happen that the props are placed on freshly filled up soil. At that moment temporary C.C. should be done before placing those props for cantilever slab on filled up soil. The filled up soil should also be properly compacted / watered.
- The reason for temporary PCC is that freshly filled up soil may settle and cantilever slab may sink.
- Proper camber should be provided as per drawing particularly in large span beam at the center and in case of cantilever beam at the end.
- When span of the beam is more than 6 to 9 meter then camber should be provided in centre of the beam. It is possible that when span to depth ratio is not maintained the chances of deflection at center may arise. To check the deflections of large beam follow this site experiment.
- To check whenever deflection is taking place during concreting or not (particularly in case of long span between) adopt the match box technique. Take a single prop and place it in the centre of the beam with empty matchbox placed on top of prop (leave a space between beam shuttering and prop). Once casting has been carried out, if the empty matchbox gets crushed it can be clearly said that the deflection has occurred.
- If it deflects and if deflection is more than permissible limits, it is serious and immediately consults your structural engineer to arrive at right engineering solutions.
- Providing camber can minimise the risk of deflection particularly in long span of beam. This also happens after hardening of concrete.
- M.S. props must used when height of the staging is more than 3.6m (12′).
- Remove all the debris e.g. dust, paper, leaves, chippings of woods, nails, reinforcement wastage, soil particles etc…
- Before placing the concrete, sprinkle some water over the shuttering of slab.
02. Reinforcement
- The reinforcement steel should be free of any loose scale, rust, mud, or oil.
- Cutting of reinforcement should be done beam wise and for the total number of the beams, required for slab. Extra length of cutting bars at the ends leads to improper end cover.
- Make sure that cover blocks used for casting of slab and beam have the same grade as of concrete. They are not broken and properly positioned and should not get disturbed during concreting operations.
- Proper cover to reinforcement should be provided to slab bottom, beam bottom and sidewalls.
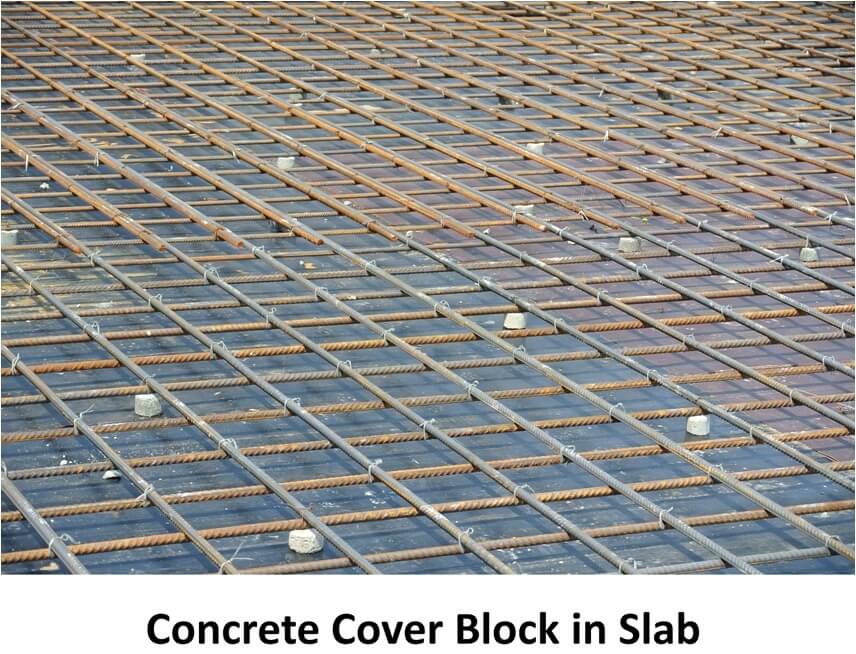
Image Courtesy – 123rf
- Before placing the concrete, Check the reinforcement details with bar bending schedule and get an approval from structural consultant.
- The reinforcement of slab must be in proper alignment and the slab bends must be lifted up to give a bend up of height 12.5 mm less than slab thickness without cover.
- Make sure that size and spacing of reinforcement are as per drawing, particularly for main reinforcement of slab or beam.
- Full bearing of beam bars should be given on column.
- Beam bars should be passing through column reinforcement fully.
- Provide M.S. chairs in cantilever slab reinforcement as well as for lifted bent up bars.
- Check the laps of beam or slab with detailed drawing. Never keeps lap in middle of beam or slab if they have long span. Keep the lap in alternate pattern and it should be in staggered manner.
- Check the joints beam-column joint details as per detailed drawing- flexible or rigid.
- Bent up bars must be as per detailed drawing. It should not be in middle height.
- See that whenever the reinforcement of cantilever beam are at top and also ensure that the counter balance in cantilever beam is adequately provided e. top bars are adequately taken into the main beams or slabs (Minimums double the cantilever length).
- Oil should not come in contact with surface of reinforcement. It will reduce the bond.
- Stirrups must be provided at junction of beams and columns which is generally avoided.
- Dowels (if any) Should be provided for elevational features / future extentions/ upper storey column.
- Parapet (Pardi) bars shall be left for balconies/staircase