Table of Contents
Value engineering is applied in construction projects to feed a clear and elaborated analysis of how best to meet the goals of the project.
Value engineering, coupled with cost estimation, allows for an independent evaluation of the entire construction project.
What is Value Engineering in Construction?
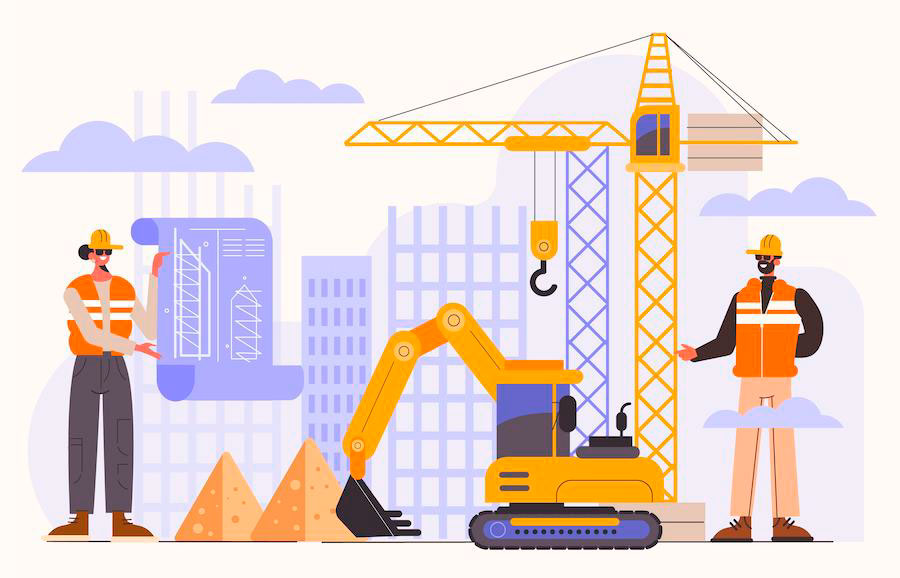
Value engineering is a systematic process aimed at enhancing the value of a product or service at every stage of the product life cycle. This means value engineering is a function-oriented, systematic team approach and study to allow value in a product, structure, or service. Often, the focus is on cost deduction; however, other crucial areas such as customer-perceived quality and performance are also of great importance in the value equation.
Value engineering motivates using alternative techniques and materials that are less costly and do not lower the functionality of the system, service, or product.
Most often, value engineering takes place after the completion of the design process, but it is advisable to conduct it before the design process so that specialists can understand the options for using alternative materials and methods.
In a house construction project, value engineering enhances the process of house construction, ensures quality, and checks construction costs simultaneously.
How Value Engineering is Used in the Construction of Houses?
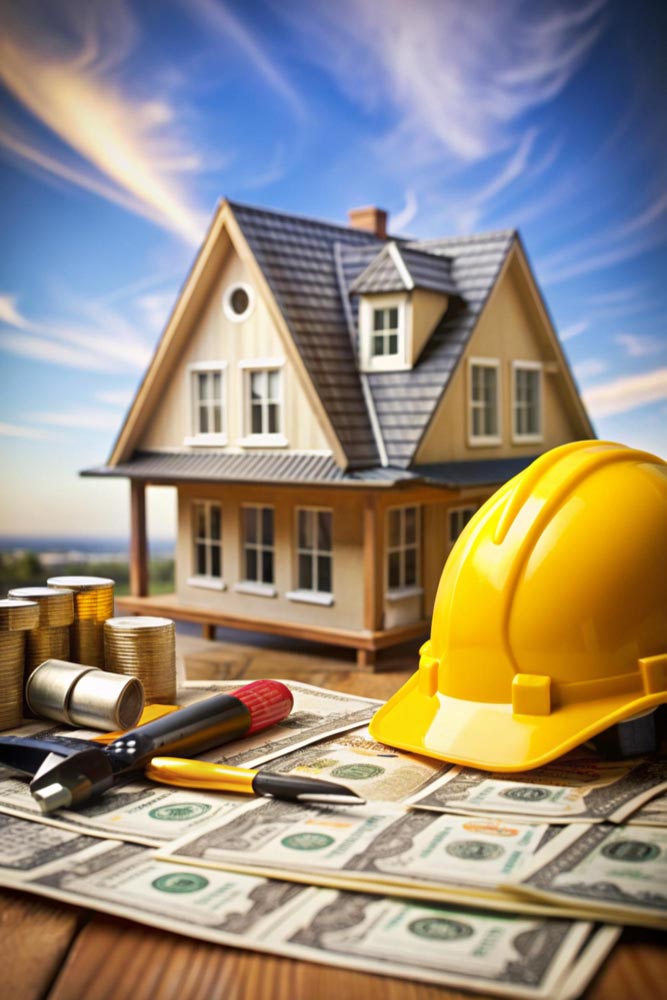
One can use value engineering at any phase of a construction project, but it’s most effective to use it at the very beginning.
Regardless, many companies only start utilising this method when they acknowledge they are running low on money. This usually happens during a project when it becomes clear that the initial plans and fund allotment will not work.
The absolute goal of every construction project is to remain within scope, within budget, and on time. This imposes a concerted, professional, independent review of every aspect of the construction project. Thus, they must try looking at alternative ways of completing the job to make sure it is still a success. The best way to prevent this situation is to use value engineering before red signals show up or before starting the project.
The materials used, budget, environmental factors, architectural design, community, and government standards and regulations, planning, and contingency plans.
This helps in avoiding possible problems that can arise, including:
- Last-minute design changes cost both time and money, as they need to alter the actual plan.
- Architectural redesign during a project results in delays, last-minute overruns, and a change in focus.
- Pressure and tension on contractors to construct within the specified time and budget.
- Every person working on-site gets pushed to their limits in terms of time and capabilities.
It’s important to underline that Value Engineering is not about:
• Cost cutting.
• Scope reduction.
• Loss of quality.
• Forced redesign.
Whether they’re accountable for materials purchase, architectural design, project management, or environmental assessment, value engineering can get a better job done.
Benefits of Value Engineering in House Construction Projects are:
– Lower operating and maintenance costs
– Improved quality management
– Enhanced resource efficiency
– Reduced waste
– Streamlined processes
– Reduced paperwork
– Lower staff costs
– Optimised construction expenditures
– Increased competitiveness in the marketplace
Value Engineering Techniques used in a House Construction Project:
01. Set up the Value Engineering Job Plan (Phases)
A job plan consists of five phases, ensuring a systematic evaluation.
- Information Phase – Collect all the information about the project, including goals, plans, materials, design, and resources.
- Ideation Phase – Get all creative here and brainstorm ideas and alternatives to improve the project.
- Analysis – Evaluate the alternative in the context of cost, quality, and feasibility.
- Development – Develop feasible solutions with details in them.
- Decision and Action – Count on the recommendations and then make the necessary decision.
02. Get Information From the Best Sources
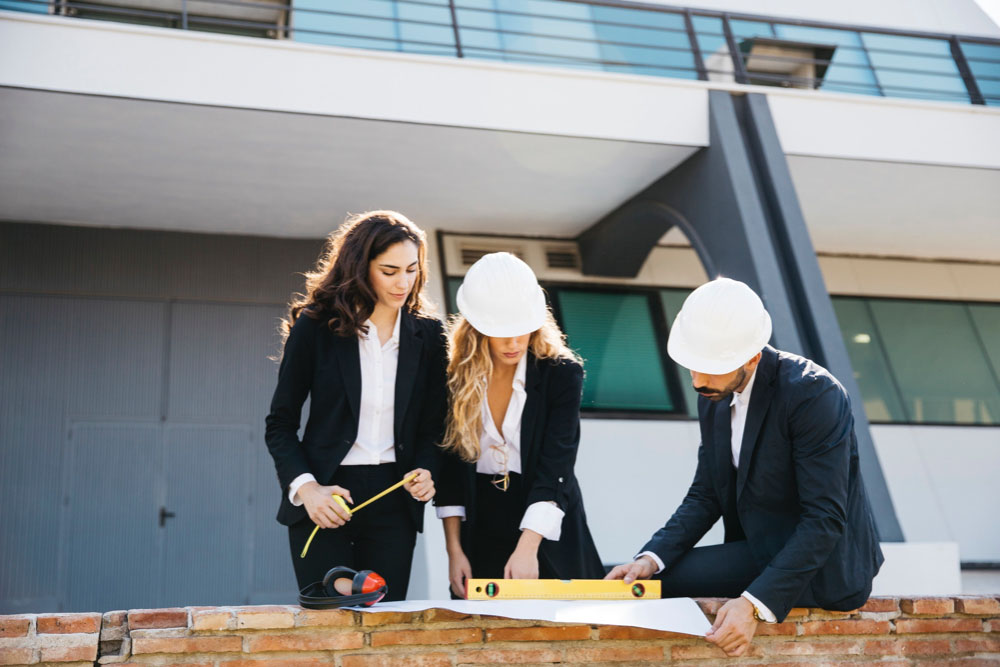
Contacting people who can provide the required information accurately and promptly. For instance, contact an architect for detailed plans and designs, an engineer for construction schedules and methods, and a material specialist for innovative materials.
03. Know Costs
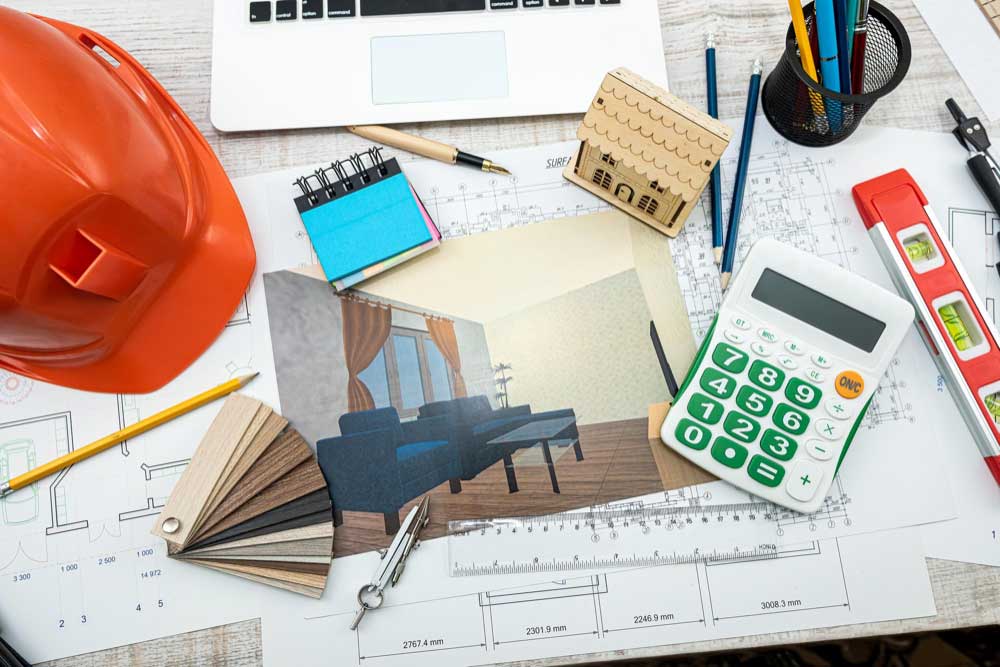
To make a detailed analysis of any element, it is essential to know not only the total cost of the element but also the breakdown of the total cost. This breakdown will include materials, labour, and overhead. Each operation eliminated will bring down that portion of the cost.
04. Define Each Function
This technique describes the function of each component of the house. A verb and a noun, such as “support roof” or “insulate walls,” define each function. You can then determine more cost-effective ways to achieve the same function without reducing quality.
05. Think Creatively
Using as many creative techniques as possible is mandatory to get a fresh point of view. Brainstorm alternative methods, materials, or designs for constructing the house. Evaluate every idea you get from all possible perspectives, and then move on to the next idea. Do not limit yourself to the conventional approach. The main purpose is to explore as many approaches to the problem as possible before examining any of them.
06. Alternative Materials
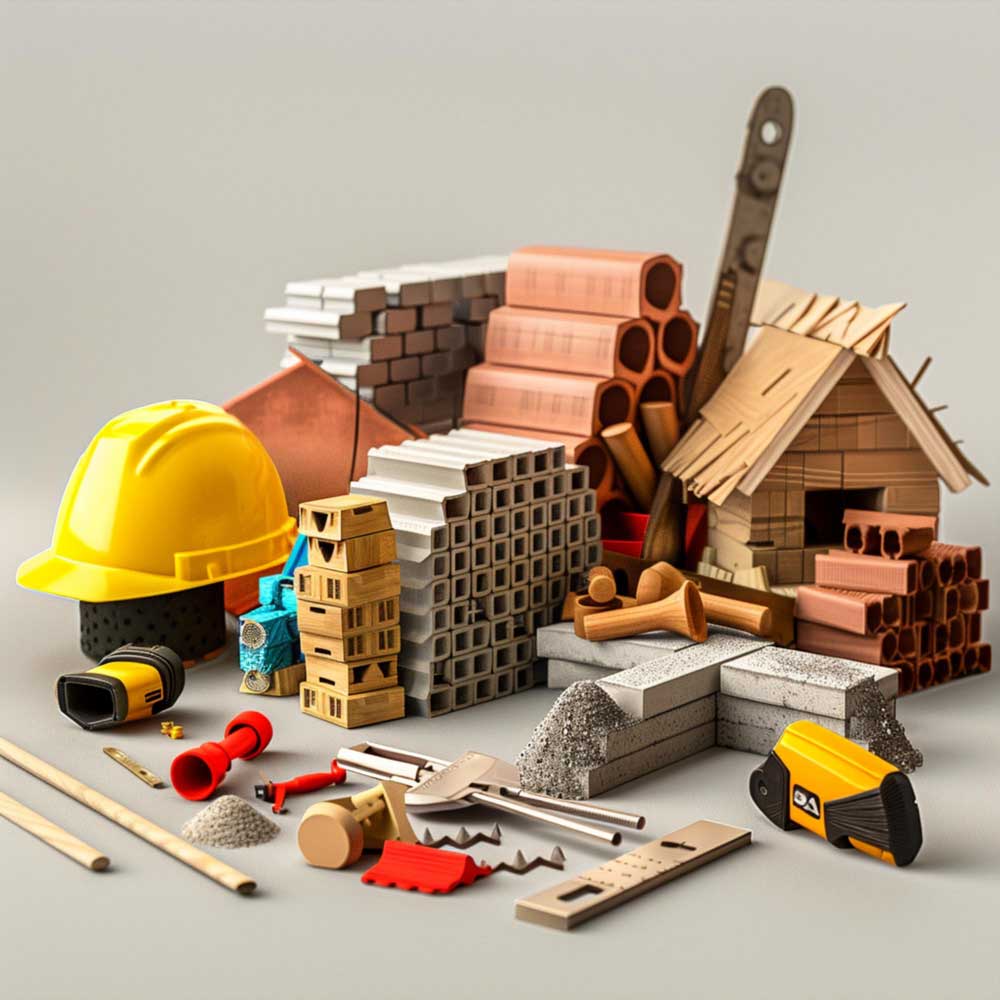
Research alternative materials that are cheap but meet the required standards. For example, the alternative for insulation with solid wood is engineered wood or recycled wood.
07. Life Cycle Costing
In this technique, the entire life cycle cost of the building is considered over the initial cost. This includes maintenance costs, energy use, and repairs over the life of the house. For example, the initial cost of energy-efficient windows is higher; however, in the long run, they will reduce your energy bills.
08. Standardisation and Simplification
This technique focuses on standardising and simplifying the design to reduce both material and labour costs. For example, the use of standard-sized windows and doors rather than custom ones reduces the cost, complexity, and time of construction.
09. Elimination of Non-Essential Features
Identify and eliminate unnecessary features that do not add value to the house, like elaborate decorative elements. These elements serve only an aesthetic purpose and have no functional use; hence, you can omit them.
10. Modular Construction
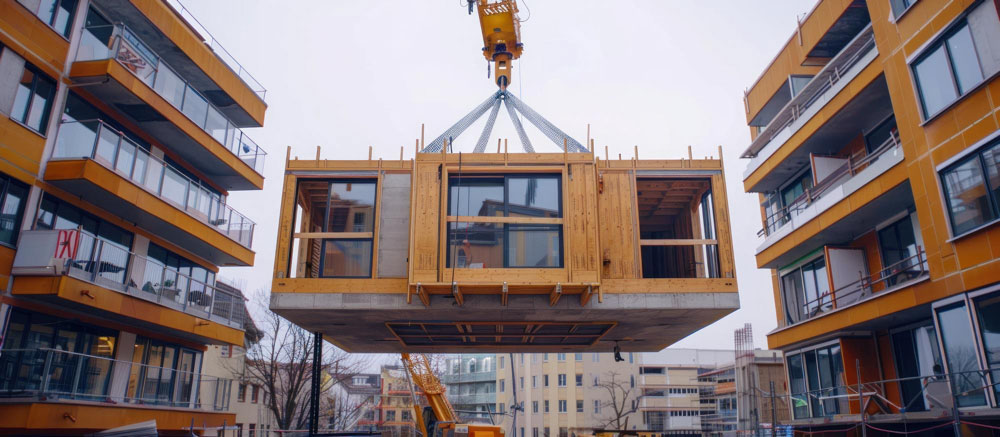
Modular construction practices use prefabricated components that are assembled on-site. Since on-site assembling is faster, you can save on construction time, labour costs, and material waste while maintaining quality.
We also have an interesting blog on modular construction given below:
11. Mindful Space Planning
With mindful space planning, you will save on the cost of materials as well as get more space. For example, creating open-plan spaces can reduce the number of walls and partitions needed.
12. Sustainable Practices
Practicing sustainable construction is part of value engineering. The use of eco-friendly materials, reducing energy consumption, and minimising waste reduces operational costs in the long term and can even qualify for tax incentives or rebates.
Conclusion
Value engineering analyses a service, system, or product to determine the best way to govern the important functions while decreasing the cost. Value engineering facilitates using alternative methods and materials that are less expensive and do not lower the functionality of the system, service, or product.
In the final estimation, value engineering is not only beneficial but essential because:
- It enhances the functionality of the project while generating tremendous savings on both the initial and life-cycle costs.
- A “second look” at the designs made by the architect and engineers assures that all reasonable alternatives have been scrutinised.
- Cost estimates and scope statements are scanned thoroughly, ensuring that nothing has been omitted or underestimated.
- It ensures that the building, over its life, will provide the best price.
Value Engineering Benefits FAQs
01. What is the difference between value engineering and cost reduction?
Cost deduction is concerned with cost, which is only one of the many objectives of value engineering. The value of a commodity/product, or service is the ratio of function to cost. Value can be expanded by expanding functionality while keeping the cost the same, deducting the cost, or letting the cost increase at a lower rate than the increase in functionality. Thus, value engineering does not necessarily result in a cost deduction, if the ratio of functionality to cost goes up.
02. Where should one draw the line on Value Engineering?
It has been established that value engineering undertakings are most beneficial when they are considered at an early stage of a project. With the passage of time, greater detailing of designs, awarding of contracts, and starting construction, the cost of value engineering keeps going up and the benefits keep going down. At some point, the cost of value engineering outstrips its benefit. While it is not easy to pinpoint this tipping point, it sometimes arises during the comprehensive design stage (before the start of construction). It is advisable to put a stop to value engineering at this stage and examine only those ideas as value engineering that have massive benefits.
03. What is the best time to do Value Engineering in a project?
The sooner, the better. However, value engineering can’t be done without the baseline being ready. In rare cases, value engineering can also be done at the construction stage, provided it has considerable benefits, is low-risk, and will not disrupt any action on a crucial path.
Do check out these interesting blogs here:
How to Estimate the Construction Time for Your House?
Innovations in Sustainable House Construction
Author Bio
Harsh Ved – I am a civil engineer, working as a site engineer and a freelance content writer. I hold a Master’s degree in Construction Engineering and Management. My keen interest lies in writing and research work. I have also written a research paper on “Building Integrated Photovoltaics” that is published in IRJET Journal.