What is Curing and Why is it Necessary?
Hydration is a process through which concrete acquires its strength and durability. This process takes place between cement particles and water. This hydration process of cement is not a momentary action but a process going on for a long time. It is very essential to maintain appropriate temperature and moisture for the complete hydration. But practically speaking, concrete is open to the atmosphere at the working site. This leads to the evaporation of water; hence the water available in the concrete will not be adequate for sufficient hydration process. In that case, additional water must be added to replenish the loss of water on account of absorption and evaporation. This is called curing of concrete.
According to the ‘A.M. Neville’[01] (Honorary member of the American Concrete Institute and the author of Concrete Technology), “Curing is the name given to the procedures used for promoting the hydration of cement, and thus, the development of strength of concrete, the procedure to control the temperature and the movement of moisture from and into the concrete.” The curing can be considered as the creation of a favourable environment during the early period of concreting for uninterrupted hydration. Water curing generally requires abundant water and at times, it can be quite challenging to perform concrete works at the locations where there is scarcity of water or sufficient water cannot be made available at the site for various other reasons. Thus, it is necessary to find alternative measures for water curing such as the provision of impervious covering, i.e. plastic sheets or application of curing compounds.
We have elaborately discussed in the below mentioned articles
- Curing by Wet Covering Method
- Curing by Spraying & Fogging Method
- Curing by Ponding Method
- Non-Conventional Curing Methods
- Steam Curing at Atmospheric Pressure
- High Pressure Steam Curing, Etc.
Now here in this article Gharpedia is coming up with some alternatives to these traditional methods of curing.
What is a Curing Compound?
Curing compounds are used to retard or reduce the loss of water or moisture from the concrete caused due to evaporation during the early period of setting and hardening. These curing compounds form a thin liquid membrane on the concrete surfaces thereby preventing the process of evaporation to a certain extent and retaining moisture in the concrete. Therefore, they are also known as Liquid membrane-forming curing compounds.
Curing compounds consist of waxes, resins, chlorinated rubber and other materials. They are used as per the standard guidelines of ASTM C309-19 – “Standard Specification for Liquid Membrane-Forming Compounds for Curing Concrete” and AASHTO M 148 – “Standard Specification for Liquid Membrane-Forming Compounds for Curing Concrete”.
Use of Membrane-Forming Curing Compounds
Membrane-forming curing compounds are used not only for curing fresh concrete, but also for further curing of concrete after removal of formwork or after initial water curing for one or two days. Curing compounds have a broad range of usage. They can be used extensively from curing small concrete works to large work like canal lining, sloping roofs and textured surfaces of concrete pavements etc. They can also be advantageous in preventing the absorption of water from the concrete by the ground (soil/earth) if used at the interface of the ground level.
Right Curing Compound
According to the ‘Steven H. Kosmatka et al.’ (Author of Design and Control of Concrete Mixtures) “Curing compounds should be able to maintain the relative humidity of the concrete surface above 80% for seven days to sustain cement hydration.”
There are two types of membrane-forming curing compounds:
01. Clear or Translucent Curing Compounds
02. White Pigmented Curing Compounds
01. Clear or Translucent Curing Compounds
The clear or translucent concrete curing compounds contains a fugitive dye. Its complete application and coverage on the concrete surface can be confirmed even by visual inspection. After the application, this dye fades out within a couple of hours.
02. White Pigmented Curing Compounds

The white-pigmented compounds consist of finely divided white pigment. While using the pigmented compounds, the problem that arises is of the settlement of pigments. To overcome this problem, they should be kept agitated in the container. Such curing compounds are recommended in the hot, sunny days as they shun absorbing the solar heat thereby reducing the concrete temperature. As temperature is one the crucial factors affecting the concreting process; you must pay attention to its effect and take some necessary precautions during hot weather concreting as well as during cold weather concreting
Types of Curing Compounds
Mentioned below are four types of curing compounds which are popular and easily available in the market.
01. Synthetic Resin-Based Curing Compounds
02. Acrylic-Based Curing Compound
03. Wax-Based Curing Compound
04. Chlorinated Rubber Based Curing Compound
01. Synthetic Resin and Wax-Based Curing Compounds
Resin and wax-based curing compounds can effectively seal the concrete surface. But with passage of time, they lose their efficiency. Within 28 days after their application, they get disintegrated and start peeling off. So, if you want start your plasterwork, it can be done after 28 days or so.
According to the ‘M.S. Shetty’[02] (Author of Concrete Technology), the average efficiency of resin and wax-based membrane-forming curing compounds can be considered nearly 80%, although practically the typical curing efficiency has been found to be 96% for 24 hours, 84% for 72 hours, 74% for 7 days and 65% for 14 days.
02. Acrylic-Based Curing Compounds
Acrylic-based curing compounds allow better adhesion of subsequent plaster, and this is the additional advantage. This membrane does not disintegrate or collapse, and due to inherent characteristics of acrylic emulsion, the bonding of the plaster is better.
03. Chlorinated Rubber Based Curing Compounds
Chlorinated rubber based curing compounds forms a thin film and fills the minute pores in the surface of the concrete that protects the concrete from drying out. Eventually, the surface film wears out.
Points to Be Remembered While Using Membrane-Forming Curing Compounds
The following precautions are necessary while using membrane-forming curing compounds:
- Before using them, the Membrane-forming curing compounds must be stirred in a container to make them. It is easy to maintain a thoroughly mixed solution. They should not sag, runoff peaks, or collect in grooves. The film formed by curing compounds should be tough to withstand immediate construction traffic without wear or tear.
- The curing compounds film must be non-yellowing. It should not discolour the concrete surface, and must have good moisture-retention properties.
- It should be applied soon after the formwork of vertical surfaces is removed or soon after the final finishing of the horizontal surface is completed.
- Curing compounds should be sprayed uniformly on the concrete surface. If the coating is sprayed evenly, the curing compounds will usually cover anything between 3.5 and 5.0 sq.m.per litre. But this may again vary from manufacturers to manufacturers and the type of curing compounds.
- Membrane-forming curing compounds are preferably sprayed in two layers. The second layer must be sprayed at a right angle to the first layer. The application can be done by hand or by a power sprayer generally at 0.5 to 0.7 MPa (0.055 to 0.077 Kg/mm2) pressure.
- The spray nozzle must be held 300 to 500 mm away from the surface, especially during windy conditions.
- It is very important that curing compounds accomplish complete coverage of the concrete surface because even small pinholes in the membrane will enhance the evaporation of moisture from the concrete.
- Whenever the spraying equipment, nozzle or hose remains out of use for more than half an hour, apply cleaning solvent on them before use. Thus, make sure that cleaning solvent is available for cleaning these tools.
- Do not use concrete curing compounds on the surface between hardened concrete and a freshly placed concrete overlay, renderings, flooring, paints etc. This is because it prevents bonding of any surface application which may come on the concrete surface subsequently. For example, some curing compounds may affect the adhesion of paint to concrete.
- Monitor two things continuously that are mentioned below:
01. Test the surface with NDT test to verify the strength of hardened concrete. To know more in detail, visit our blogs on various tests for hardened concrete like cube test and flexural strength test.
02. Always buy a product of a standard company. Compromising on the quality of curing compounds will make it impossible to repair or strengthen uncured concrete.
Conclusion
On the concluding note, the concrete curing compounds are suitable for application on concrete surfaces to reduce the loss of water during the early hardening period. They are very useful when concrete is placed in some inaccessible, difficult or far off places where wet curing is not possible. Curing compounds are also very suitable for large areas of concrete that are in direct contact with sunlight, heavy winds and such other environmental influences. The membrane-forming curing compounds are used when original water/cement ratio of concrete is more than 0.50. It gives the best results if you apply the membrane a day or two after actual wet curing if possible.
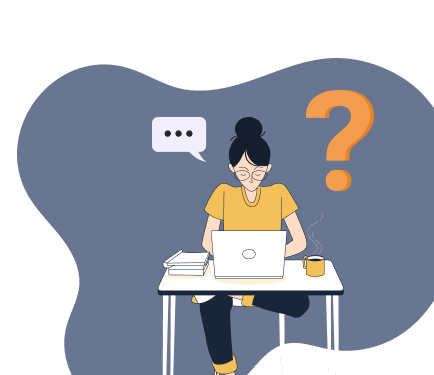
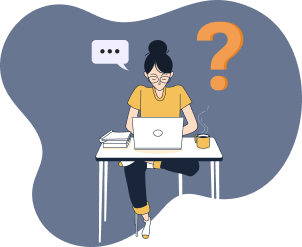