Plumbing is a system which includes supply of potable water at desired locations in house or building. It carries away sewage or waste water hygienically. Plumbing system is further divided into the water supply system and sewerage system. Both systems include series of pipes that convey either the water or waste water.
Among the plumbing pipes, cast iron pipes(Ci Pipes) are very famous from 19th century. They have a good compressive strength so they can resist the earth pressure easily. They are highly corrosion resistant and hence, they are also used to transmit water. They are brittle and hence they are difficult to cut and fit.
Let’s understand the basic information of cast iron pipes.
Classification of Cast Iron Pipes Based on their Class
01) Class LA
02) Class A
03) Class B
04) Class C
05) Class D
06) Class E
Class LA cast Iron pipes have been taken as the basis for evolving the series of pipes. Class A cast iron pipes allow a 10 percent Increase in thickness over class LA cast iron pipes. Class B cast iron pipes allow a 20 percent Increase In thickness over class LA cast Iron pipes. For special uses, Classes C, D, or E may be derived by allowing corresponding increases of thickness of 30, 40, or 50 percent respectively.
Since long Cl pipes are being used as reliable material for sewerage ‘Force mains’, mainly due to its good compressive strength for resisting high earth load and good corrosion resistance. The suitability of CI Pipe for sewage application in light of various design requirements are discussed below:
Structural Stability of Cast Iron Pipes
Good compressive strength gives it good structural stability for resisting high earth load. However, Cl pipes being brittle in nature are sensitive to point loading, and impact loading. CI pipes are not recommended for use under dynamic loading component in their use, e.g. under major carriage ways, or where there is higher risk of ground movement or subsidence. Being a brittle material CI pipes need to be handled carefully during laying.
Hair line Crack in Cast Iron Pipe
During handling and installation Cl pipes, sometimes the pipes develop minute hair-cracks which are not clearly visible. The failure / bursting occurs when the pipeline is charged or pressure tested. It is advisable to check CI pipes for hair-crack before laying.
Cast iron Pipe for High Pressure Application
Due to low tensile strength, the pressure bearing capacity of Cl pipes are much lower compared to other metallic pipes like MS or DI. So, for high pressure applications or where there is high chance of sudden positive pressure build up due to surge, CI pipes should be avoided.
Internal Corrosion of Cast Iron Pipe
Cl pipes ore normally available with Internal Bitumen coating only. So Internal corrosion starts within few years of service, which leads to deposition or corrosion products (tuberculation) and pitting. As a result, the internal diameter reduces restricting the carrying capacity. This process of internal corrosion takes place faster while carrying sewage. This should be kept in mind while designing sewerage force mains. However, for sewage collection system, Cl pipes are normally not used as when partially filled, the septicity is more and the corrosion is faster. Cement mortar lining with high alumina or Sulphate resisting cement can only minimize corrosion problem.
Encrustation, Tree Root Penetration and Rodent Attack
Though it is a metallic pipe, it resists Incrustation and tree root penetration as also rodent attack.
Maintenance of Cast Iron Pipes
Gravity and Force Mains can be cleaned using rods, cutter heads and in some cases even pressure stream to remove solids and grease build-ups. Cl pipes do not get damaged due to such operations.
Recommended Use of Cast Iron Pipes
Cl pipes may be used for sewerage force mains but they are not recommended for collection systems without lining. The main reason is in partially filled pipe the septicity is more and the corrosion is faster which will reduce flow in long term.
Types of Joint and Inter Connection of Cast Iron Pipes
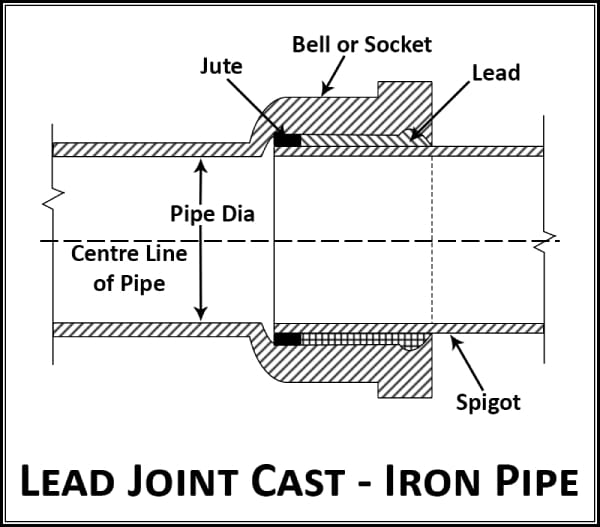
Generally, two types of joining arrangements are very famous for cast Iron pipes(Ci Pipes). One, in which one end of cast Iron pipe has socket and on the other end, there is the spigot. Second, in which flanges are provided at both ends of the cast Iron pipes.
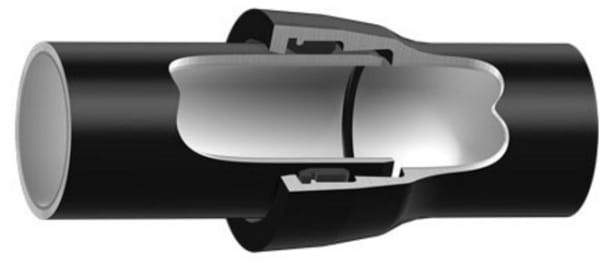
The socket and spigot pipes can be joined with lead joint or push on joint. Few years ago, lead joints were very famous In Asian countries but nowadays they are prohibited due to the ill effect of lead. Cast-Iron pipes can be joined together with cast Iron Joint sealant In place of lead. In case of push-on Joints, the spigot ends shall be suitably chamfered or rounded off for smooth entry of pipe in the socket and shall befitted with the rubber gasket.
In case of the cast iron pipes with flange, they can be joined with bolts.
Laying of Cast Iron Pipes
Cast iron pipes are laid in slope under the ground or hanged on the celling to convey the sewerage of house. In case of external sewerage system, they are laid underground on the side of the street with cover of 1 meter on the top of pipes. The laying of pipes is generally governed by the regulation of municipalities and corporations which ensures proper laying as well as safety of the laying workers.
Manufacturing of Cast Iron Pipes
According to IS – 1536 (Bureau of Indian Standard), cast iron pipes are manufactured from the iron (metallurgy materials). They are heat treated in order to achieve the necessary mechanical properties and to relive casting stresses. They are centrifugally casted in metal moulds or sand lined moulds. Generally metal moulds are used up to the diameter of 300 mm and sand lined moulds are used for over 300mm dia.
Cast iron pipes are available in 3 ft (91.44 cm), 6 ft (182.88 cm), 8 ft (243.84 cm), and 10 ft (304.8 cm) length and 3” (7.62 cm), 4” (10.16 cm), 5” (12.7 cm) and 6” (15.24 cm) in diameters. Length other than specified above may also supplied on mutual agreement between the manufacturer and the purchaser.
Mechanical Tests for Cast Iron Pipes
After manufacturing, cast iron pipes are tested by following test.
01. Ring Test and Tensile Test
The ring test is conducted for pipes for sizes up to 300mm diameter. For sizes greater then 300mm, tensile test is carried out.
Ring Test:
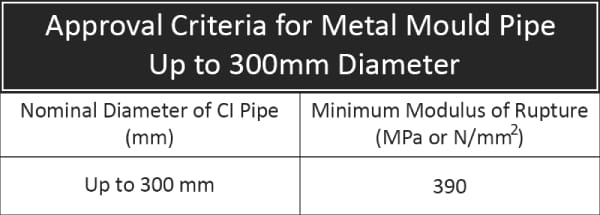
Tensile Test:
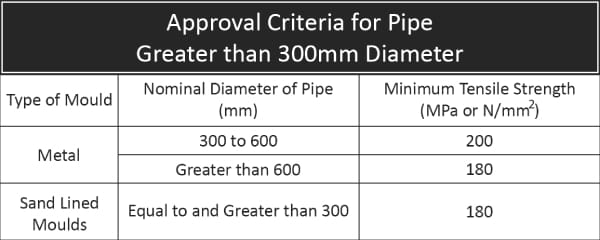
02. Brinell Hardness Test
According to IS 1500 (Bureau of Indian Standard), the name itself suggest that the Brinell hardness test is used to measure the hardness of the cast iron pipe. In this test a hard metal ball is forced into the surface of cast iron pipe and hardness is measured with help of brines hardness machine.
03. Hydrostatic Test
In hydrostatic test, steady pressure is applied internally in cast iron pipes.
The table below shows hydrostatic pressure for centrifugally cast pipes with sockets and spigots pipes.
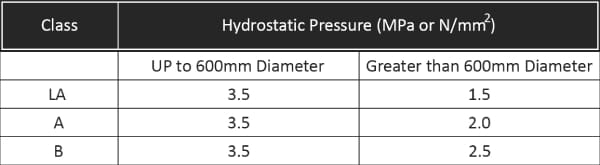
The following table shows hydrostatic pressure for centrifugally cast pipes with screwed on flanges socket and spigot pipes.

Finally, it is necessary to check the quality of cast iron pipe. The surface of cast iron pipe must be smooth and it should be stamped with the manufacturer’s name, initials, or identification mark. It is also stamped with the nominal diameter, class reference, mass of pipe and last two digits of the year of manufacture. By selecting a good quality cast iron pipe, you can make your plumbing drainage system more efficient and it will stay repair free for a long duration.
If you confused about how to choose Right Contractor, Must Read:
Also, Refer: Plumbing Safety Tips and Precautions-for safety Tips of Plumbing.