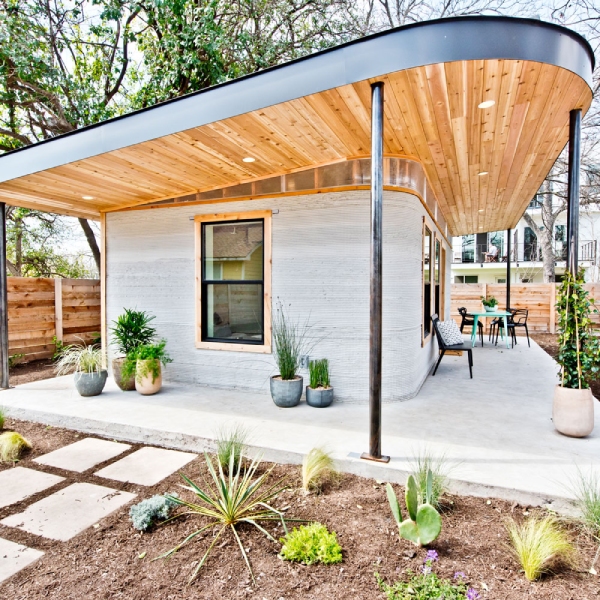
In the present times technology is advancing by leaps and bounds in every sector. Construction industry is no exception. Building of houses and structures should also see the same light.
After long years of study, research and development, large scale 3D printing technology is finally coming into existence and with the infant steps has started entering the construction industry. The ambition of seeing 3D printed houses in towns and cities all around the world is now looking bright.
3D printed concrete house is a revolution in the construction industry. It is welcome technology as it offers a sustainable alternative to traditional building processes that can make a significant contribution to reducing construction waste worldwide.
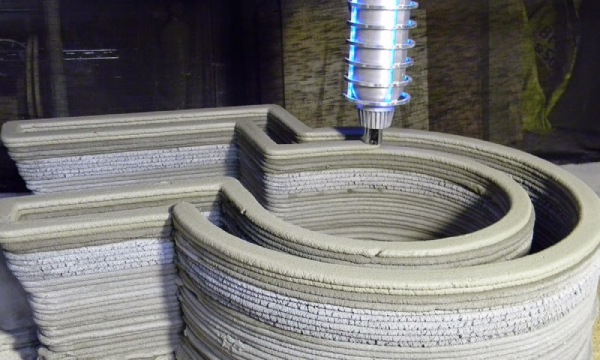
History
In the early times which marked the beginning of human settlement, the houses were built by using stones. Later, bricks and mortars were used. In 1853, Francois Kanye, a French industrialist for the first time, used a new type of material called reinforced concrete to build his house. Since then, most of the buildings and structures were constructed using the same method introduced by him which continued for more than 150 years or so.
In the recent years, with the introduction of 3D printing technology, the technology has become prevalent in many industries including construction. New 3D printers can print materials such as concrete that in turn can make 3D printed building and structures.
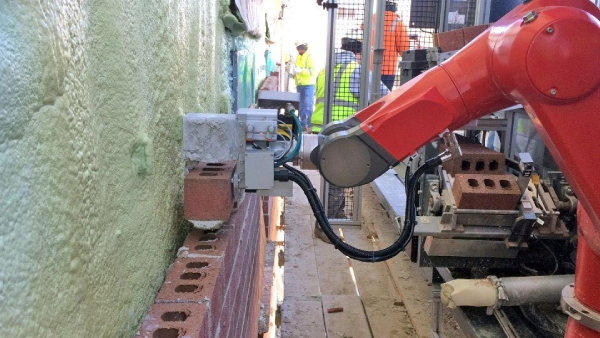
The invention of 3D printing in construction goes way back to the 50s when “robotic bricklaying” was first conceptualized. It has been developing then over the years, until the year 2008, when 3D concrete printing began at Loughborough University, UK, headed by Richard Buswell. The licensing to use this technology to build houses and structures was issued in 2014. Ever since then, various firms have been building houses and offices using concrete 3D printing technology.
Need of 3D Printed Concrete
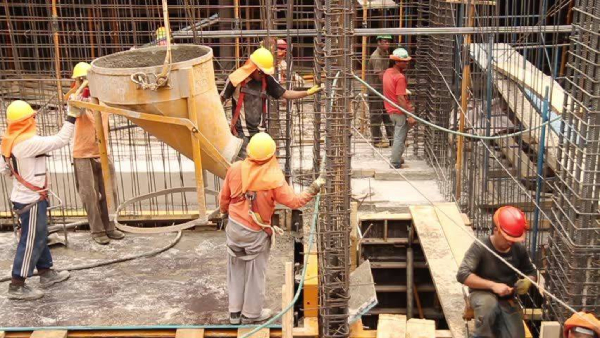
The dilemma of construction industry is that though it has a worth of 10 trillion dollars globally, and happens to be one of the largest industries in the world, it lacks productivity compared to the other industries. Just for the sake of comparison let us take an instance. Agriculture and manufacturing sectors have increased their productivity 10 to 15 times since 1950. In contrast to this, construction industry has not seen much of a change for almost 80 years and more particularly in developing and undeveloped countries. The reason behind this is that the manufacturing and other industries gradually introduced and mastered the use of automation and digital technologies in their respective sectors quite earlier, whereas construction industry remained significantly manual.
The conventional or the standard methods fundamentally need to be upgraded with the help of technology and made advanced to tackle housing problems all around the world. With this in mind, a revolution in the construction industry is essential and the 3D printing architecture could be the transformation needed to dramatically increase the quality of the modern building and construction.
Benefits of 3D Printed Concrete Technology
Less Cost of Overall Construction Project:
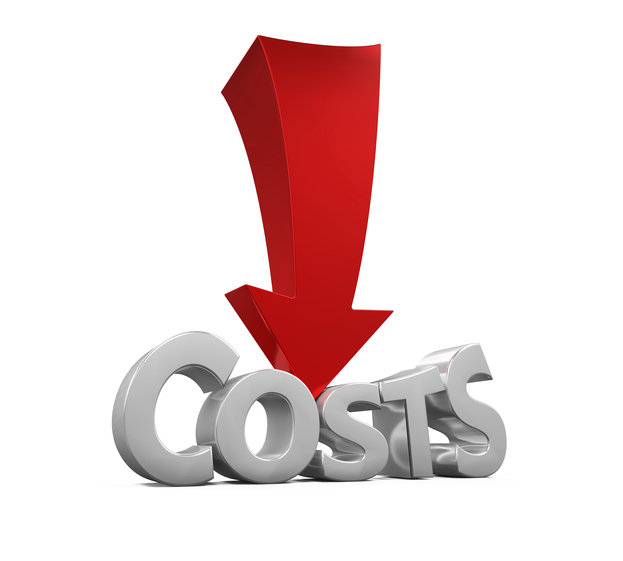
The cost of 3d printed concrete house is less than traditional construction techniques and processes. With the diminution of injuries, time, and material cost, the overall cost of project is reduced.
According to Le et al. (Published in: Hardened properties of high-performance printing concrete’, 2012), in the 3-D printing process, the integration of mechanical and electrical resources optimize the use of materials and site work, leading to a reduced possibility of expensive remedial work. The cost of 3-D printing, however, should include the cost of 3-D printers as well. Well, this makes us hopeful and probably 3-D printing will achieve a reasonable cost savings in the short term.
Less Labour Cost:
According to ‘Jenee A. Jagoda’ (Published in: An Analysis of the Viability of 3D-Printed Construction as an Alternative to Conventional Construction Methods in the Expeditionary Environment), the construction industry is one of the most risky with a higher injury, disease, and fatality rate than most other industries due to hazards such as irritation of the eye, skin, and respiratory tract; chemical burns; slips, trips, falls; and over-exertion. However, as the construction process progressively turns on toward automation, the number of employees required and the corresponding number of injuries will decrease. This will further help to minimise risk and reduce labour-related costs as well as accident or fatality costs. For example, WinSun, a Chinese company, reported that using 3D printing technology to construct the Dubai Future Foundation office building reduced labour cost by 50 % to 80%.
Quality and Sustainability:
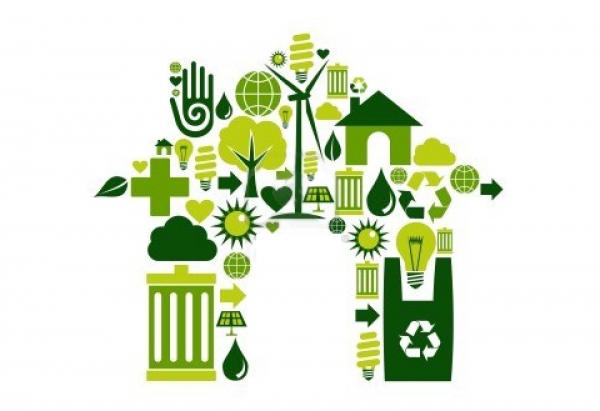
According to ‘build with rise‘, the elimination of wastage of materials is one of the most important contributions to the sustainable construction movement that 3-D printing can bring. A 3-D printer can help in estimating the exact amount of materials required for the construction of the home after modelling a home on a screen. 3-D printers have the potential to significantly decrease the carbon footprint associated with constructing homes by reducing construction waste and material transportation costs.
Using concrete 3D printing technology could be a new way to reduce the construction waste. Up to 50% of the raw materials used by the 3D printers are made from recycled materials. Moreover, because of the capability of 3D printers to create complex shapes such as overhangs and folds, it allows the contractors to use less material in the first place. This eventually results in production of less waste.
Gharpedia has written article on recycle construction waste as well. Click on the link below to know more.
Speed of Construction:
Construction speed is another substantial criterion when it comes to building houses. Typically to build a personalized house using the conventional method of construction, it would take anything between 6-10 months, depending upon the size and other factors associated with the construction.
However, it will take just 24 hours to build a small house by using concrete 3D printing method. This demonstrates how fast the concrete 3D printers are. For example, ICON a single storey 75 sq. meter house in Texas was built in less than 24 hours with the cost of less than $4000.
The construction speed in 3D printed houses can definitely vary with the size of the building but it does not change the fact that concrete 3D printers are extremely faster than conventional method of construction.
3D Printed Concrete Technology Creates Variety of Shapes:
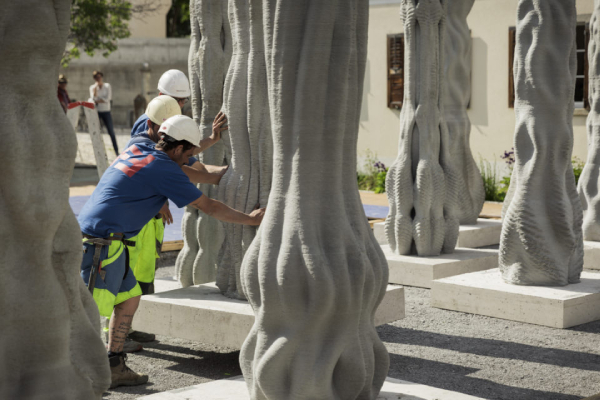
Construction industry has not seen much of progress in creating different forms and shapes. It is mainly due to the fact that the industry has yet not been fully automated. In conventional construction method, to create a form, concrete must be poured into a mould known as formwork. Here comes the limitation which restricts the creativity of architects to build various shapes.
But concrete 3D printing technology incorporates digital technology and application of material technology to create freeform construction without the use of formwork. With the help of 3D printing technology more shapes such as curves, spheres and numerous other forms can be created in less time, and lesser cost.
Limitations of 3D Printed Concrete House
- One of the main disadvantages is that you have a smaller margin of error. This is because 3D printed concrete hardens rapidly. And if you make even a slightest mistake in the print, you just have to discard the whole thing and start again.
- You are also limited by the size of the printer and the size of the object being printed.
- The cost of the machines and hardware used in concrete 3D printing are very high in today’s market.
- 3D printers are yet not proficient enough to build a completely functioning home.
- According to ‘Constrofacilitator‘, only the frame and walls of the house are constructed; other components such as windows, electricity, or plumbing need to be built separately. The roof of house also needs to be printed separately. The frame of the house including, conventional steel reinforcements and plumbing pipes are first erected. It is also possible to use concrete 3D printers to print bridges, tables, or just outdoor decorations.
Since this is fairly a new technology, we cannot expect it to be completely up to the mark. It does have some shortcomings which must be rectified with further development. But we do expect that the cost of the machines will just keep going down gradually with time. 3D printing has a huge potential as a sustainable tech solution but existing 3D processes are not sufficiently practical or efficient.
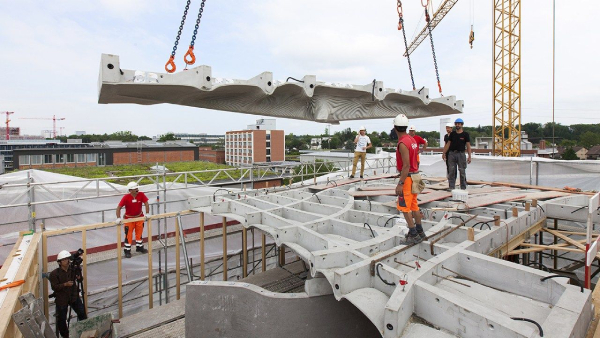
Hardware Used for Concrete 3D Printing
01. Industrial Robots:
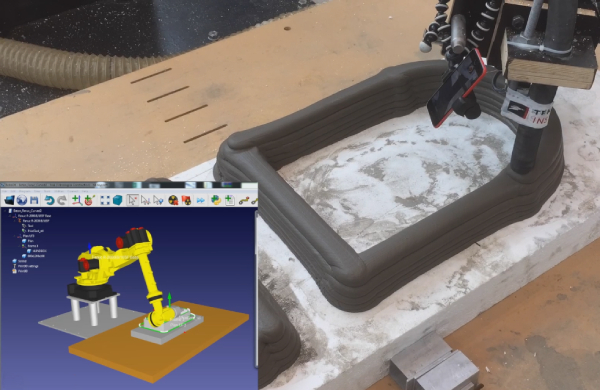
They have a very large mass and a small operating area. For example, a robot with a reach of only four meters weighs 5 tons. You cannot place it on a slab; it will simply break through the floor. The permitted standard load on a floor slab is 600 kg/m2 and due to lack of stabilization, at maximum arm extension the robot will simply topple over. In order to overcome this issue, it will be necessary to either modify the design or securely affix the robot in place or change the entire mechanism.
02. Portal 3D Printers:

Portal 3D printers are huge and gigantic. They have to be installed on a perfectly levelled surface so that the mechanism of the printer does not jam. Now, imagine how huge a printer would have to be to build a high rise building. And moreover, how much it would cost for the transportation of such a printer and later assemble it in place. A printer which is light in weight and can print a building with no limits in square size just by moving it around is the solution to this problem.
03. Stabilization System:
The printer will not topple over and its installation will take not more than an hour, so thanks to the stabilization system. And the small dimension makes the transportation of the printer quite easy. The automatic construction material and the supply system provide a stable flow of fibre concrete, handling all of the most complex and filthy work.
How does 3D Printing Work?
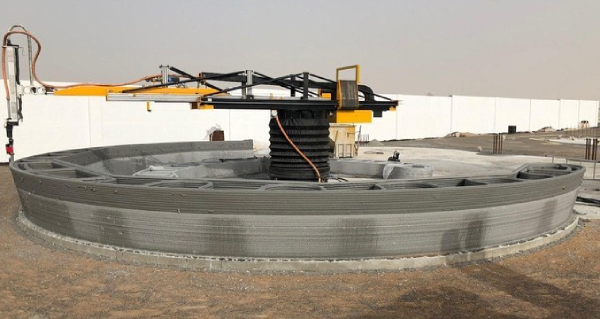
To understand the process of building a 3D printed house, a detailed yet simplified elucidation is required. Various types of materials can be printed by 3D printers such as filaments, metals, concrete and more.
Concrete 3D printer, like any other 3D printer consists of three axes: X, Y and Z. X and Y are opposite directions in which the rail runs, whereas Z axis represents the height of the wall. To operate the concrete 3D printer, experienced and professional constructors must be present to supervise the concrete 3D printer.
Before the arrival of the printer, construction site has to be prepared for it. The construction site has to be flattened for 3D printer so that the rails for the printer can be installed.
In addition to creating a flat surface, the concrete 3D printer foundations are needed before the process of printing concrete can begin. After all these preparations are wrapped up and finished, the next phase is to install the concrete printer on the rails. When a 3D design of a building is ready, designers or architects convert the blueprint into G-code and dispatch it to the concrete 3D printer.
Afterwards, the material for 3D printer is brought by a normal concrete truck to the construction field. During the 3D printing process of construction, the reinforcement and electrical installations of the walls are done. These operations can be done as a result of the recent developments from an expert in concrete 3D printing provided by the company.
These advancements in concrete 3D printing technology have helped to create a special method of wall reinforcements that make bare concrete walls even stronger than what they normally are.
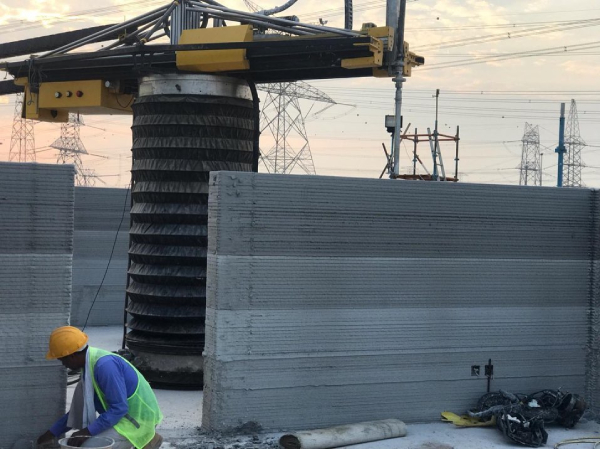
To be able to successfully print buildings, the concrete for the 3D printer has to be made in a precise and special manner, compared to conventional concrete. The concrete mix of 3D printer must contain two important traits –maximal build ability when concrete is poured and also the flow ability of concrete mix to make sure that the nozzle does not get clogged.
This high quality concrete mix can be attained by using accurate amount of chemicals such as superplasticizers. The main purpose of superplasticizer is to reduce water in a concrete mix. Moreover, there are various additives that are added into the concrete mix. For instance fibres are added to the mix to enhance the strength of concrete.
Well, the strength of concrete is an utmost important property of concrete. If you are interested in knowing how the strength of concrete is measured, refer the below mentioned article.
One of the most leading and prominent methods of concrete 3D printing is called “Contour craft”. The contour crafting is utilized in the construction of multi-storey buildings and also construction in space.
According to ‘Rawan Allouzi’ et. al (Published in: Conventional Construction and 3D Printing: A Comparison Study on Material Cost in Jordan), Automated tiling of floors and walls could be incorporated using contour crafting by robotically distributing and spreading the bonding material to floors or walls. The method of contour crafting is based on the building form of layering, and it is therefore possible to create utility conduits inside walls. This increases the ability for the building of plumbing and electrical networks to be automated. For plumbing, a pipe segment can be mounted and connected to the lower segment that is already installed via the built conduit (after adding several wall layers). The modules have conductive pieces for power and communication lines inserted into nonconductive materials for automating electrical and communication line wiring. These pieces can be grabbed by a simple robotic arm and attached to the component already mounted while the wall is being printed.
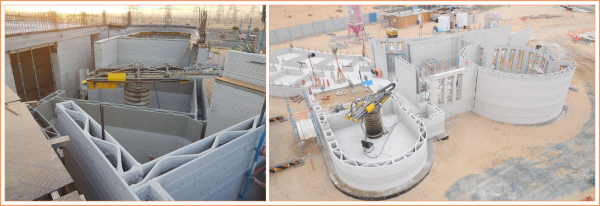
The printer can construct the foundations and the walls of a home or building layer by layer. Basically, the ground is the build plate of the printer. However, some concrete 3D printers are used to print 3D brick moulds. After being moulded, the bricks are then manually (or with a robotic arm) stacked atop each other.
Case Study:
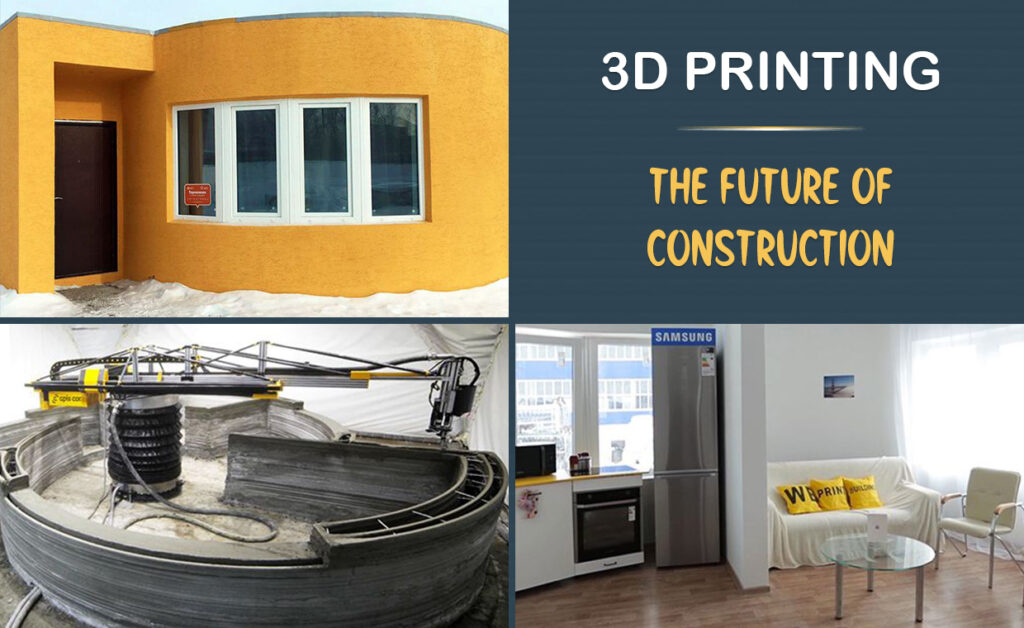
The first residential 3D printed house was printed in a day and it amounted just $10,134 in total. It is a potential breakthrough in the construction industry of affordable housing. 3D printing company Apis Cor built the house with a mobile printer. It is a pioneer in the world. The company says that the house can withstand tough weather conditions and lifespan of the structure can be 175 years or so. The structure was printed in concrete. Windows and interior design were added and later even a fresh coat of paint was added. Inside, there are four rooms with water and electrical supply. The model is the first step in building houses quickly and cheaply, potentially all around the world.
Cost of 3D Printed Concrete House
A house called Apis Cor was built in Russia by a Russian architecture company called Apiscor using their robotic 3D printers. The size of the house is 410 sq. feet and it cost approximately $10,150 for the entire construction, i.e. $24.75 per sq.ft.
According to the Russian firm – ‘Craftcloud’, the detailed costs of the house are:
- Foundation $277
- Walls $1624
- Floor and roof $234
- Interior and exterior finishing $2000
- Wiring $242
- Windows and doors $3548
However, it has to be understood that the cost of construction will vary based on the size and location of the building.
Could 3D Printing of the House be the “Future of Construction”?
Well, we can say that 3D printing technology is an upcoming technology for building a 3D printed concrete house. It is a new stage in the evolution of construction industry. The equipment is unique and has no analogues in the world. With this, now affordable houses around the world no longer seem to be merely a dream of human beings. It will become a reality for every living person on this globe.
The equipment currently used is best suited for low-rise construction and requires the constant control of a single operator. The second phase of this development is to create equipment for use in high-rise construction. If needed, it will also initiate development to enable the printing of foundations; floors and roofing which will allow entire homes to be printed in one go.
In the future, the equipment can also be made entirely self- reliant and autonomous, bringing us closer to constructing structures and buildings all around.
Image Courtesy: Image 2, Image 3, Image 4, Image 7, Image 8, Image 9, Image 10, Image 11, Image 12, Image 13(a), Image 13(b), Image 14
Author Bio
Arfa Falak – My name is Arfa Falak and I have my graduation in BE (civil). I live in Bangalore. I am an aspiring design Engineer.