Concrete is a widely used construction material due to its accessibility and durability. Nowadays, concrete technology increases its span in research and improves performance by modifying its traditional component. In this blog, Gharpedia brings all the details of the same. Here, we discuss Reactive Powder Concrete. This blog contains all the following details:
- What is Reactive Powder Concrete?
- Who Invented Reactive Powder Concrete?
- Advantages of Reactive Powder Concrete
- Applications of Reactive Powder Concrete
- Limitations of Reactive Powder Concrete
- Properties of Reactive Powder Concrete
- Components of RPC
- Reactive Powder Concrete Mix Design
- Mixing of RPC
- Curing of Reactive Powder Concrete
- Case Study on Reactive Powder Concrete
Let’s have a detailed look-
What is Reactive Powder Concrete?
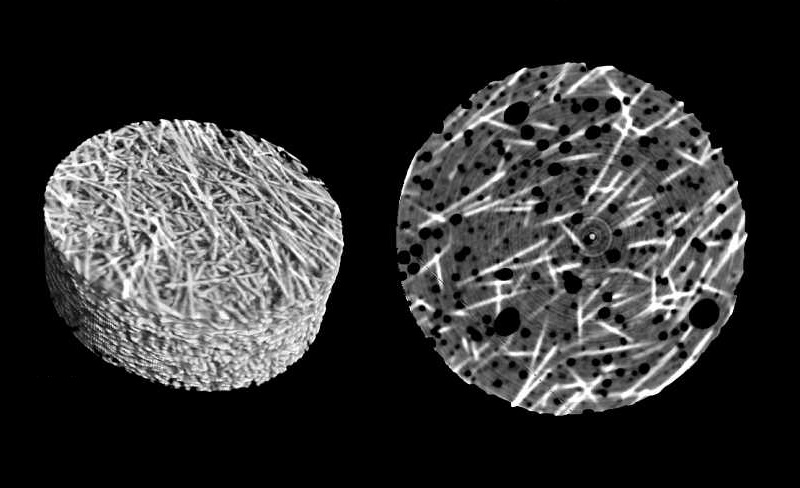
Reactive Powder Concrete, or RPC, is made with quartz sand as its major aggregate, along with silica fumes as one of the vital ingredients. Pierre Richard had experimented with reactive powdered concrete and found its compressive strength between 200 MPa to 800 MPa.
RPC is an ultra-high strength, high ductility Portland cement-based material, and it’s an emerging technology that lends a new dimension to “High-performance concrete”. It has immense potential in construction due to its superior mechanical and durability properties compared to conventional high-performance concrete.
Reactive powder concrete could even replace steel in some applications because of its strength. Various scientists have conducted multiple studies, and they found that reactive powder concrete displays excellent compressive and flexural strength. Therefore, it is generally divided into two grades, which are RPC200 and RPC800.
Who Invented Reactive Powder Concrete?
As per the ‘R. Selvaraj and R. Priyanka’ (published in International Journal of Engineering Research & Technology (IJERT)), M. Cheyrezy and P. Richard first developed reactive powder concrete. It was first produced in the early 1900s by the technical division of Bouygues, S. A. France.
Advantages of Reactive Powder Concrete
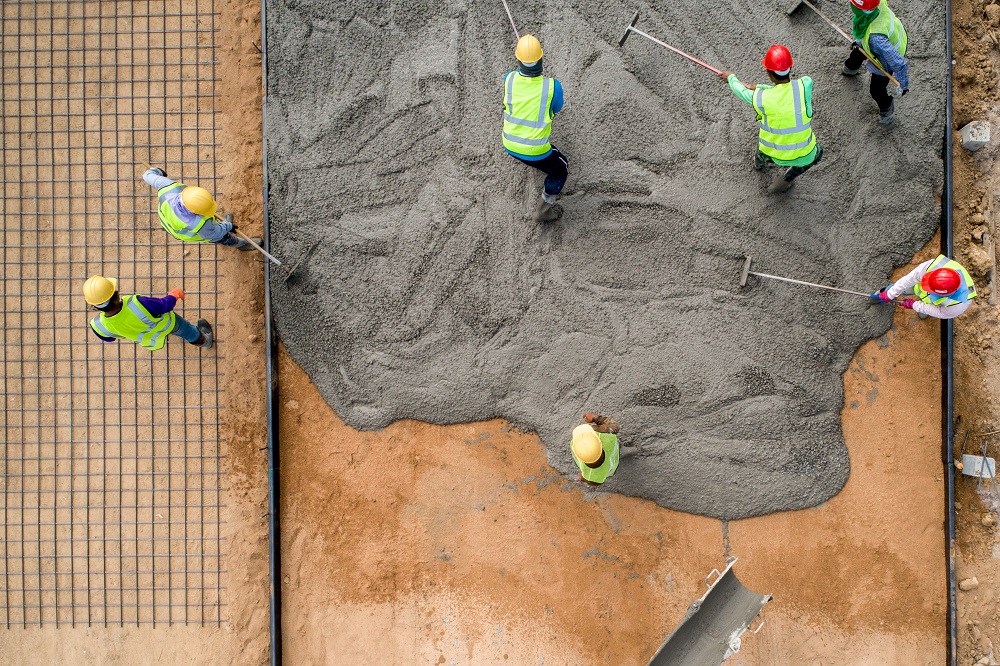
The followings are the advantages of RPC –
- Elimination of coarse aggregate for enhancement of homogeneity. It results in a more consistent final product because rubble and gravel are put together in their fine form.
- Utilization of Silica fume with fly ash to increase comprehensive strength because their pozzolanic properties enhance the mix’s mechanical properties.
- Optimum usage of superplasticizer to minimize the water-cement ratio and in turn, increase the workability of concrete.
- Post-set heat treatment of the mixture helps in the optimization of the microstructure.
- The addition of steel fibres improves the ductility of RPC.
- The structural stability of reactive powder concrete is so good that it has the potential to compete with steel.
- It has almost no shrinkage or creep.
- The combination of high strength and high shear capacity can result in significant dead load reduction.
- Optimization of the granular mixture in order to enhance the compacted density of RPC.
Applications of Reactive Powder Concrete
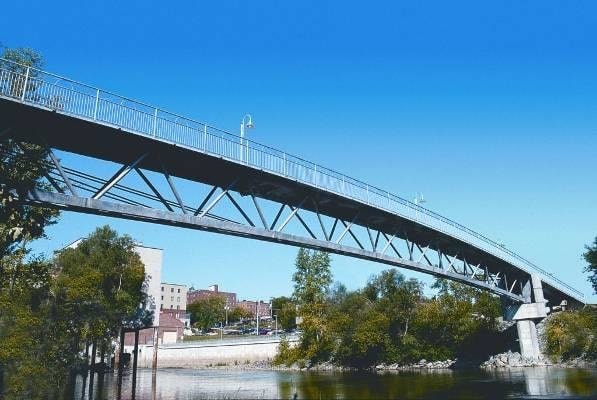
Due to the high properties of reactive powder concrete, it is a great choice for things that need lower structural weight and great structural span. The numerous reactive powder concrete applications are there, such as:
- Light-weight and high-span bridges
- Multi-storey buildings
- Inside water structures
- In seismic region
- Seawall anchors
- Vehicular bridges
- In building power plants
- Railway bridge and light rail transit station
- Blast resistant structures
- Mass concreting
So, the wide range of reactive powder concrete applications is there, and it shows the expansion of the reactive powder concrete market.
Limitations of Reactive Powder Concrete
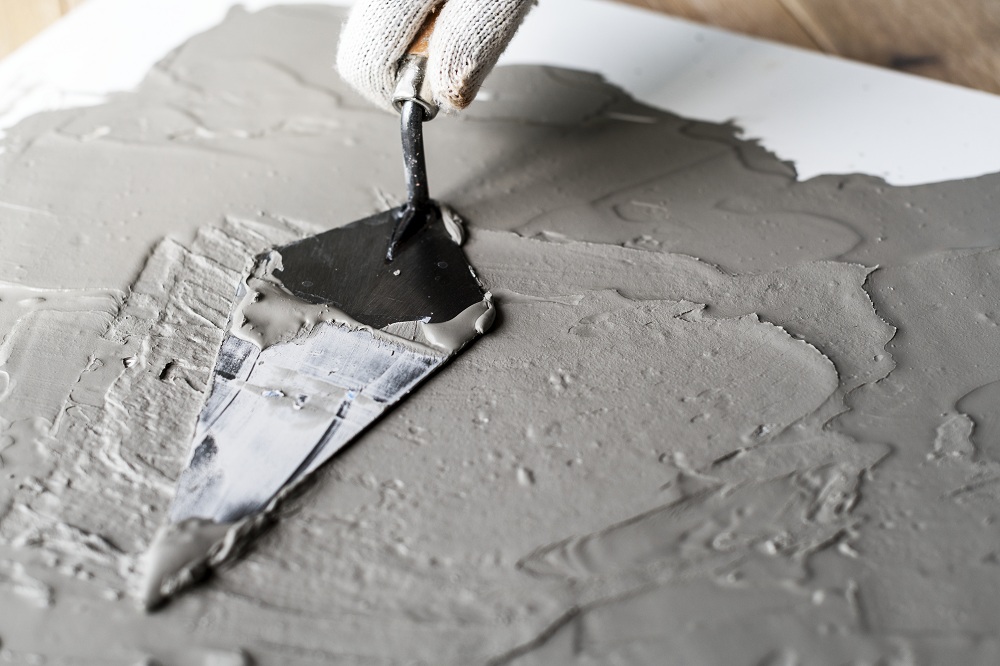
As every coin has two sides, reactive powder concrete applications are wide; but its limitations are also there. The followings are the limitations of reactive powder concrete-
- The materials/components used in the mixed design of RPC are expensive.
- There is no official code for use under any formal worldwide documents, although it is under research.
- The mineral component increases its cost by approximately 5 to 10 times more than high-performance concrete.
- Since RPC is still in its developing stage, its long-term properties with respect to its performance are still not known.
Properties of Reactive Powder Concrete
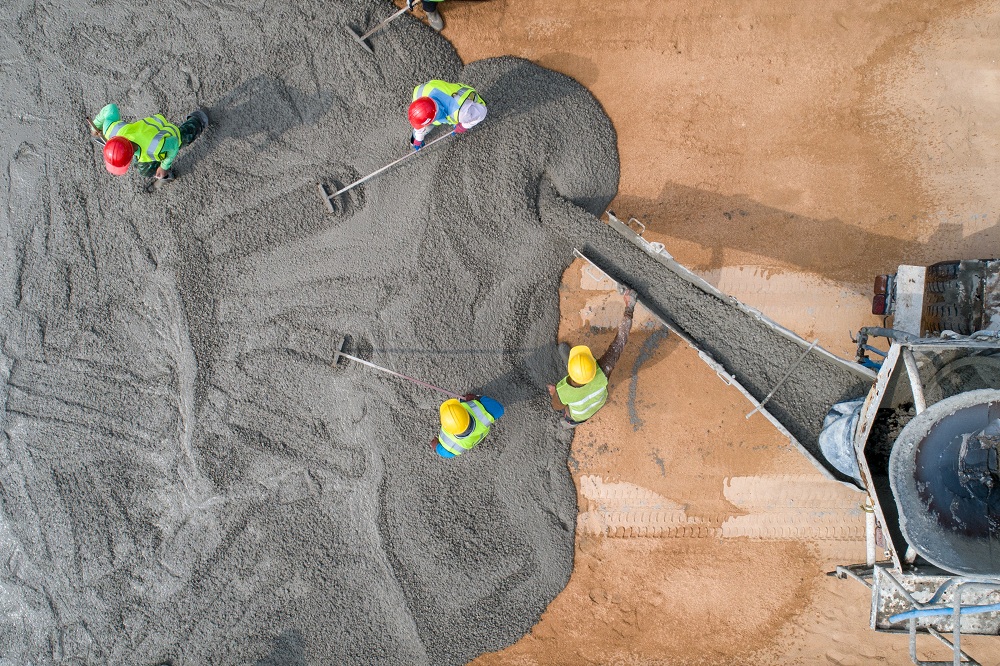
01. High Compressive Strength
RPC has a more compressive strength in comparison to high-performance concrete, its maximum compressive strength is approximately 200 MPa. Compressive strength is one of the major factors that affect the strength of concrete
You can check the compressive strength of concrete by conducting a cube test on concrete.
02. High Workability
In order to measure the workability of RPC, a slump test is conducted. This test is conducted by filling the mould with reactive powder concrete and measuring the spread diameter of RPC in two directions, orthogonally. It is done after lifting the mould upwards, vertically. Finally, the average value of the workability of concrete is expressed as the spread of concrete. Whereas the bleeding and segregation can be visually examined.
The workability of the RPC measured was found to be in the range of 120mm to 140mm; it means that it has high workability, which results in self-compaction.
Gharpedia has also written a detailed article on self-compaction concrete, you might know more about it then click on the below link-
03. High Flexural Strength
Plain reactive powder concrete has relatively high flexural strength in comparison to regular concrete. The addition of steel fibres increases the strength of reactive powder concrete. However, the diameter and length of the steel fibres have a considerable impact on the flexural strength of the mix.
You can check the flexural strength of the concrete by conducting a flexural strength test.
04. Low Water Absorption and Permeability
Water absorption of RPC decreases with age. Although, its water absorption percentage is less compared to that of high-performance concrete. This particular property is one of the most desired properties of the material used for nuclear waste containment. Similarly, the water permeability of the reactive powder concrete decreases with age.
05. Great Frost Resistance
The level of frost resisting of RPC is high with a low mass-loss rate below 1%. Henceforth, it has great resistance to high frost conditions.
Components of RPC
Ordinary portland cement, quartz sand and silica fume are the major components to produce reactive powder concrete. The other components include steel fibres, aggregates, river sand, and plasticizers. Use of plasticizers can reduce the water-cement ratio by approximately 0.23, which eventually gives more workable concrete, and also improve its strength.
The followings are the specifications of components of RPC:
01. Cement
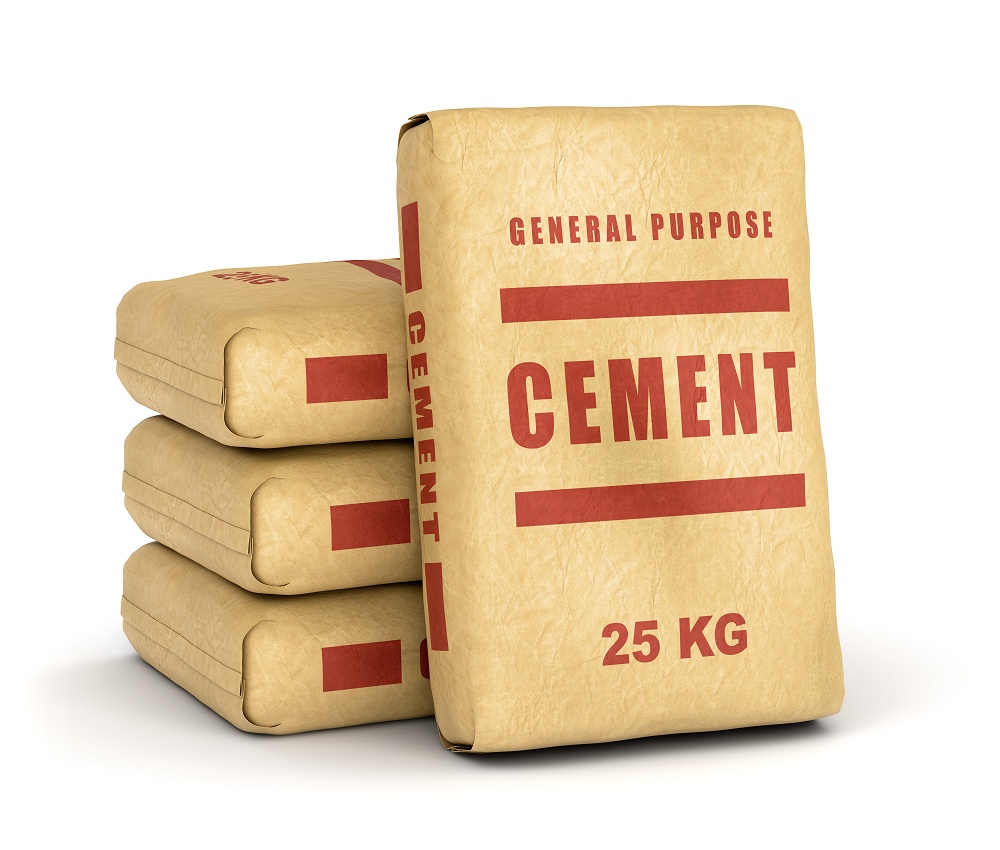
The cement used must be ordinary Portland cement (OPC) of 53 grade with particle sizes ranging from 1 µm to 100 µm. Ordinary Portland cement acts as a binding material.
02. Sand
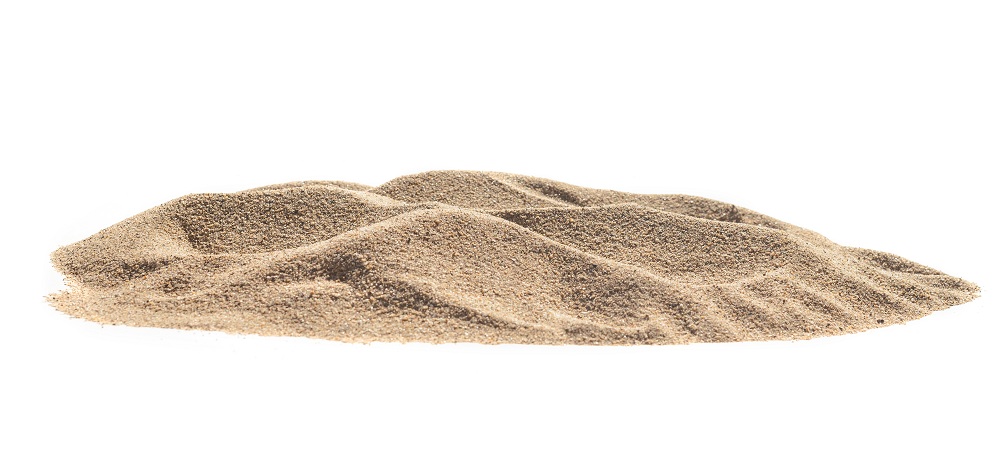
The particle size must be between 150 µm to 600 µm. Sand adds strength to the mix.
03. Silica Fume
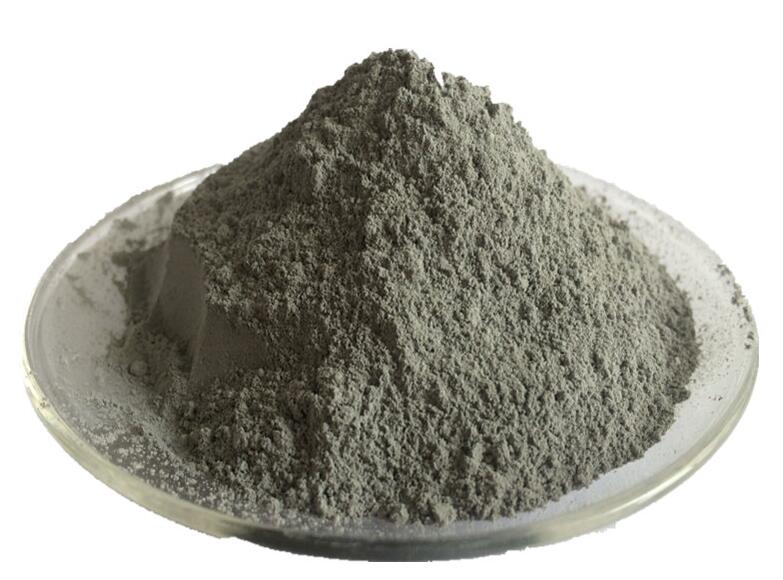
The size of the silica fume must be of 22 m2/g (fineness). The diameter of silica fume must be less than 1 µm, with average size being about 1.5 µm. The basic function of silica fume is to fill the voids. They also enhance the rheology as well as in the production of secondary hydrates.
04. Quartz Powder
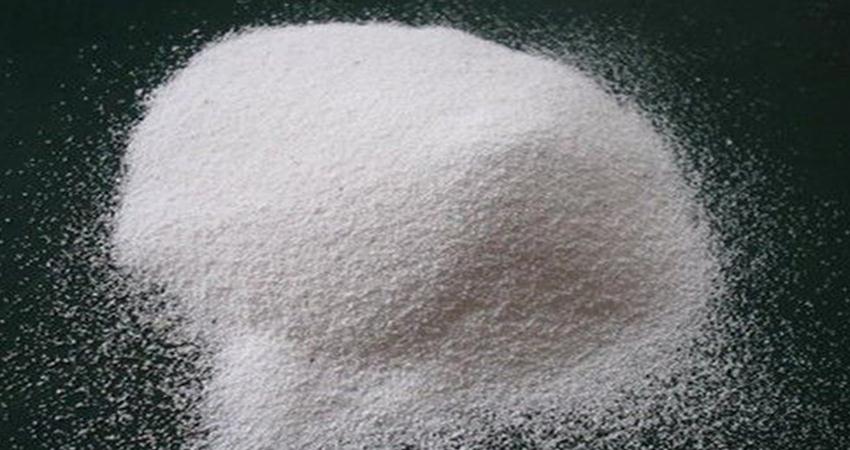
The particle size of quartz powder must range from 5 µm to 25 µm. Quartz powder imparts maximum reactivity during the heat treatment of the mix. It is pH neutral and consists of 99.9% SiO2. It has a specific gravity of 2.6 to 2.7.
05. Steel Fibres
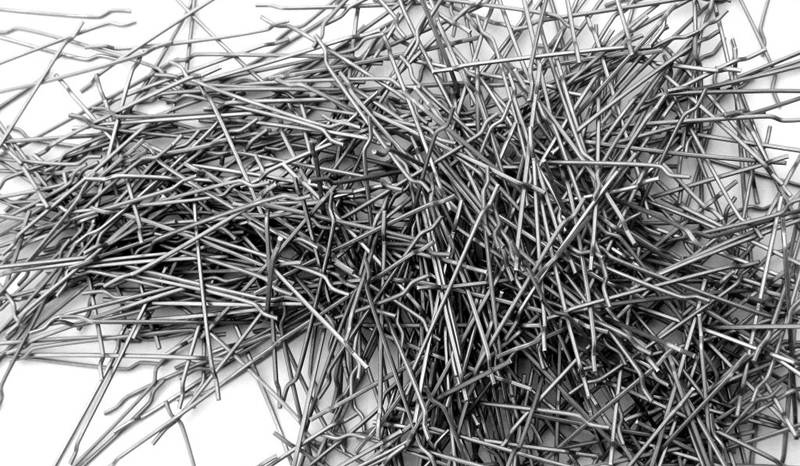
The typical dimensions of steel fibres recommended are as follows: Length – 13 to 25mm and Diameter – 0.15 to 0.5 mm. It improves the ductility of reactive powder concrete.
06. Super Plasticizer
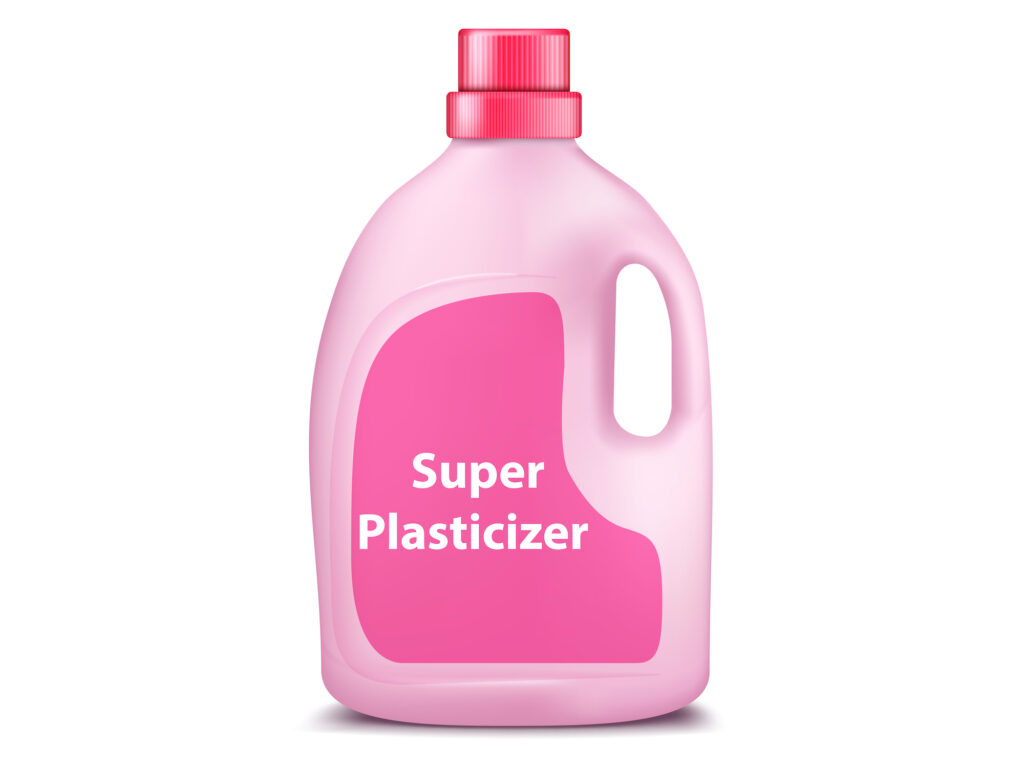
The superplasticizer used is polycarboxylate, having a pH of at least 6.0 and volumetric mass up to 1.09 kg/litre at 20 degree Celsius. The main of a superplasticizer in reactive powder concrete is to reduce the water-cement ratio. Additionally, it also reduces the water binding of the concrete mix.
Reactive Powder Concrete Mix Design
According to the research of ‘Sarika S & Dr Elson John’ (Published in the International Journal of Engineering Research & Technology (IJERT)), the followings are the mix proportion for reactive powder concrete mix design. With this mix, they got 130 MPa strength after 28 days of standard water curing. Image shows the mix proportion for reactive powder concrete mix design.
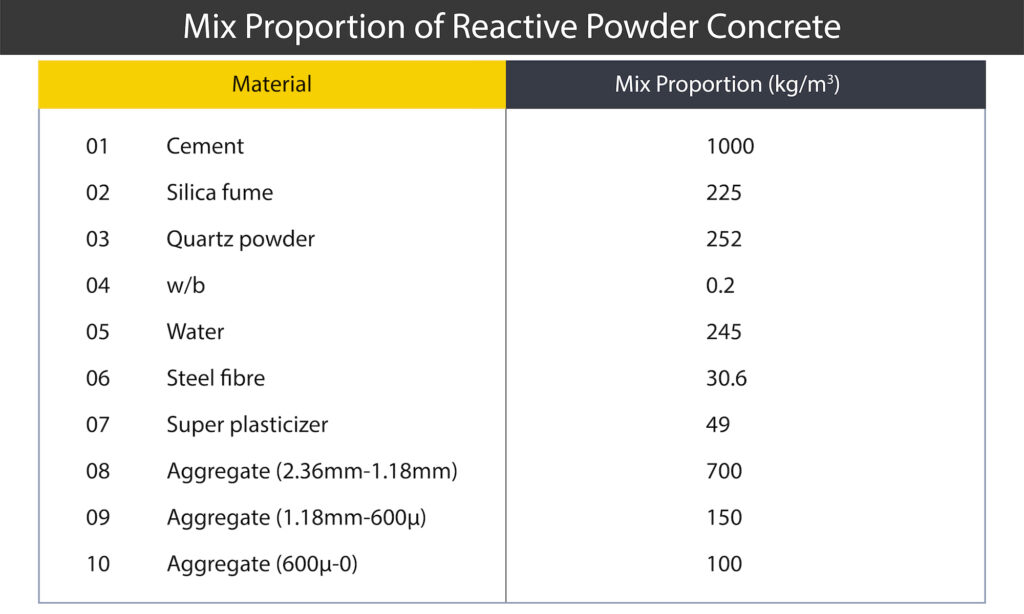
Mixing of RPC
Concrete mixing is the first process. The first step of the procedure is to mix all the dry materials for about 2 minutes. Once dry materials are properly mixed, 80% of the mixing water is added and mixed for about 3 minutes. After that, 70% superplasticizers and the remaining 15% of the water are added and mixed with the help of a mixing machine. Then, the remaining 30% of the superplasticizer and 5% water are added to the mix and are mixed meticulously for approximately 4 minutes.
Finally, steel fibres are added to the mix and mixed for about 1 minute to achieve uniform distribution. The concrete cubes of size 100mm x 100mm are cast and left for curing for about 28 days.
Curing of Reactive Powder Concrete
Concrete curing is most important for its strength. The curing of reactive powder concrete is done using three different curing methods, indoor natural curing, standard curing, and compound curing. Each of the processes is mentioned in brief below:
Indoor natural curing (NC): One-day de-moulding in addition to maintenance for 7 and 28 days under indoor natural curing conditions.
Standard curing (SC): One-day de-moulding and maintenance for 7 and 28 days under standard curing conditions.
Compound curing (CC): One-day de-moulding by using hot water for 36 hours, and maintained for 7 and 28 days under indoor natural curing conditions.
Various curing conditions significantly influence RPC’s mechanical properties for 7 to 28 days. At the time of combined hot water curing, the strength of reactive powder concrete suddenly increased in 7 days. This particular outcome remained pretty much the same as that of 28 days and higher than that of 7 days/28 days under the standard and natural curing conditions.
Additionally, the result also verified that an appropriate amount of steel fibres in the mix could effectively enhance the internal structure of the matrix and stabilize the performance of RPC. Choosing the appropriate temperature for heat curing and time is crucial for improving the strength of reactive powder concrete. This particular approach can decrease the cost of a prefabricated structure and accelerate the process of construction.
Case Study on Reactive Powder Concrete
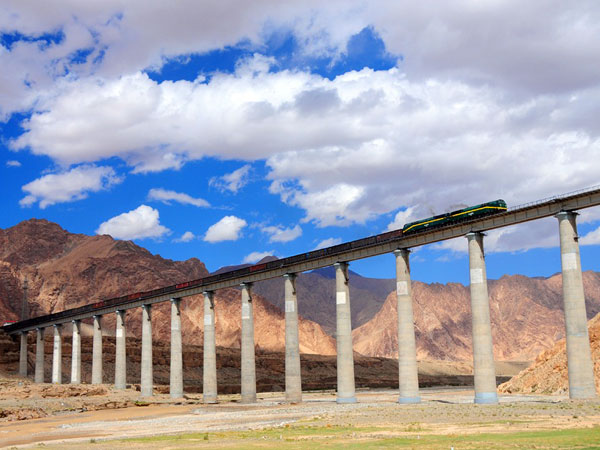
The Qinghai-Tibet railway is located in the west area of China at an altitude that is more than approximately 4,000 meters. A railway of length 576 km is built on the frozen earth. The bad climate along with the sandstorms of the tundra region require the concrete that is used to construct the bridge to have superior mechanical properties and high durability.
Reactive powder concrete consisting of Portland cement, silica fume, superfine fly ash, and superplasticizers is preferred in the sidewalk systems of the bridge with a compressive strength of approximately 160 MPa.
There are numerous difficulties and problems when working with conventional concrete such as rusting of reinforcing steel bars, corrosion, and the rupture of the concrete slab. This results in the yearly maintenance of the conventional concrete sidewalk system. Also, note that the dead weight of the traditional sidewalk system is way more than that of the RPC sidewalk system.
Additionally, the sidewalk system made of reactive powder concrete has various advantages such as lesser deadweight, high durability, minimal cost and low maintenance. Henceforth, RPC was the suitable choice to build the sidewalk system of the Qinghai-Tibet railway in comparison to conventional concrete.
Conclusion
RPC has high strength and durability, and better temperature curing can improve its mechanical properties. The use of RPC in the bridges could replace the use of steel bars for reinforcement. Henceforth, it simplifies the entire procedure of construction. The excellent properties of RPC, such as its strength and durability, could prolong the life of service of the bridge.
Reactive powder concrete is an emerging technology which imparts a new vision to the term “high-performance concrete”. It has immense potential in the construction field due to its durability and other mechanical properties compared to conventional high-performance concrete. It could, therefore, be the optimum choice for industrial and nuclear waste storage facilities.
Gharpedia has also written amazing blogs on special concrete you would like to know,
Polymer Concrete: Its Pros-Cons, Uses & Properties
Bioconcrete: New Perspective of Self-Healing Concrete
Image Courtesy: Image 2, Image 4, Image 9, Image 10, Image 11, Image 14
Author Bio
Arfa Falak – My name is Arfa Falak and I have my graduation in BE (civil). I live in Bangalore. I am an aspiring design Engineer.