Concrete is highly heterogeneous. It is a material highly in demand for the construction industry all over the globe. Significant material involved in making concrete is cement but overuse of cement is a major environmental concern. Thus, to overcome this problem and precisely to keep intact the strength of concrete, it is essential to seek out new supplementary cementing materials. Therefore, in recent years, researchers are into finding better alternatives for concrete and have tried developing materials that consists properties acquired by concrete by adding alternative byproducts in construction.Some additives which can reduce Co2 emission with additional strength and durability are as follows:
- Silica Fume (Micro Silica, Condensed Silica Fume)
- Fly Ash
- Ground Granulated Blast Furnace Slag (GGBS)
- Rice Husk Ash
- Metakaolin
Mentioned above are all pozzolanic materials. Pozzolanic material consists of siliceous and aluminous mineral substance. Hence, they have some inbuilt cementitious properties and conjointly a byproduct. Here we are discussing about only one supplementary cementing material i.e. silica fume or micro silica.
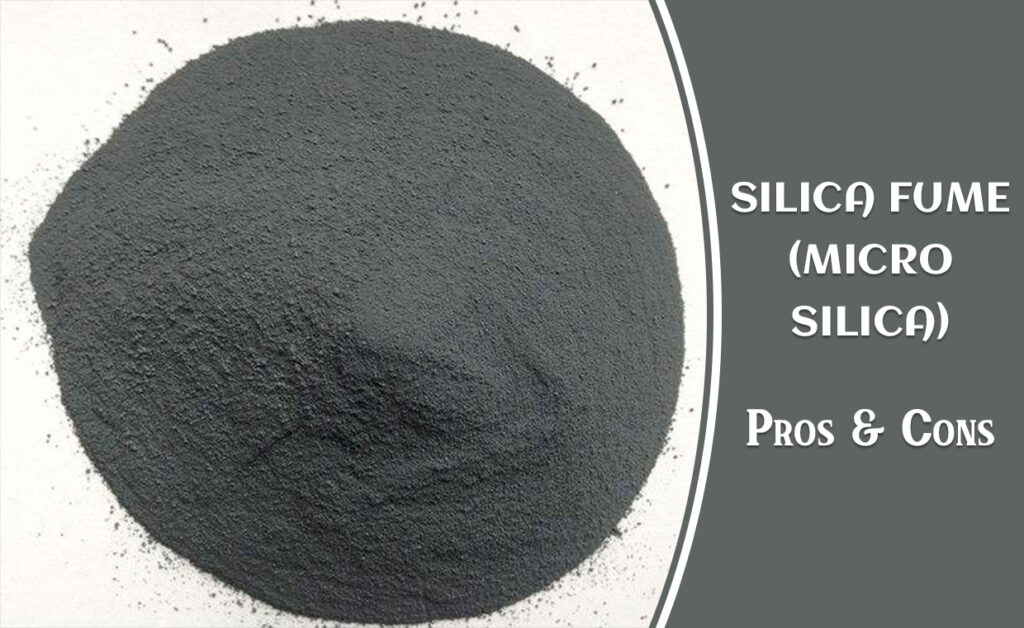
What is Silica Fume or Micro Silica?
Silica fume is a byproduct of ferrosilicon and silicon. According to ‘ACI Concrete Terminology- CT-13’ (An ACI Standard), silica fume is very fine non-crystalline silica produced in electric arc furnaces as a byproduct obtained while manufacturing elemental silicon or alloys containing silicon. It rises in the form of oxidized vapour. Later when it cools and condenses, it is collected in cloth bags.
A further process is conducted to remove impurities in it and to control the size of its particle. Silica fume has a spherical shape. It is an extremely fine particle with size less than 1 (micron) and an average diameter of around 0.1 (micron). It is about 100 times smaller than an average cement particle. Silica fume has a specific surface area of about 20000 m2/kg as that of 225 to 300 m2/kg of cement, which is responsible for the compressive strength and durability of concrete.Silica fume is also known as condensed silica fume, micro silica and volatized silica. It is basically silicon dioxide (more than 90%) in a non-crystalline form. Silica fume has both the pozzolanic as well as cementitious properties. It is also recognized as a pozzolanic admixture or supplementary cementing material. Silica fume effectively enhances the mechanical properties to a great extent. It is durable and offers a good resistance against corrosion of embedded steel.
How does Silica Fume/Micro Silica Work in the Concrete?
Silica fume when added to the concrete, initially it remains inert. Once cement and water in the mix start reacting with each other, primary chemical reactions produce two chemical compounds. In other words, once the hydration process starts between the cement and water, two chemical compounds are produced namely:
- Calcium Silicate Hydrate gel (CSH) which is responsible for the strength of the concrete.
- Calcium Hydroxide (CH) – free lime, which is a by-product and works as a filler in the available pores.
According to the ‘European Silica Fume Committee’, when silica fume is added to the concrete, it gives highly pozzolanic effect, due to its extreme fineness and very high amorphous silicon dioxide content. It reacts with the free lime (CH) and produces additional gel (CHS) in many of the voids around hydrated cement particles. This additional gel makes a dense matrix of the concrete. This improves compressive, flexural and bond- strength as well as reduce the permeability of the concrete.
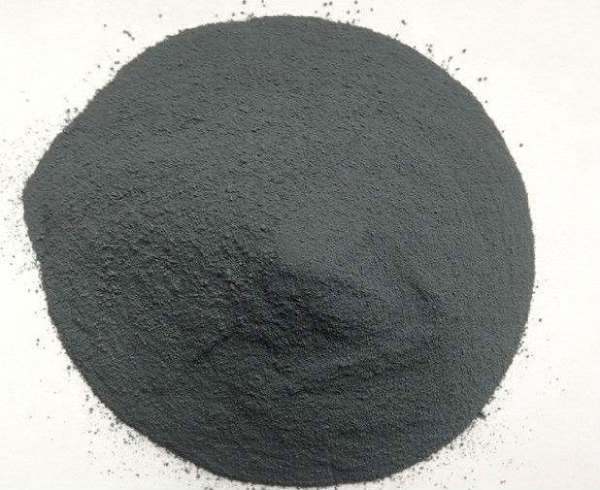
Silica Fume
Other Materials Similar to Silica Fume
According to ‘Silica Fume Association- U.S.’ (Published in Technical Report), there are various other materials which holds physical and chemical properties very similar to silica fume. These materials may or may not be a byproduct. Some of these materials may perform well in concrete but considering their cost factor i.e. they are quite costly, their use is restricted. This is because; cost factor is amongst one of the major aspects taken into consideration while raising a structure. Mentioned below are such kind of materials:
- Precipitated Silica
- Fumed Silica
- Gel Silica
- Colloidal Silica
Use of Silica Fume/Micro Silica
- Silica Fume is largely used for producing high strength and high-performance concrete.
- Silica Fume is broadly used for high strength structures.
- It is also used for high rise structures.
- Condensed silica fume is mainly used to produce concrete with higher resistance to chloride penetration for applications such as parking structures, bridges, and bridge decks.
- It also used for building decks, floors, overlays and marine structures etc.
- Micro silica is also used for shotcrete in rock stabilization; mine tunnel linings; and rehabilitation of deteriorating bridge and marine columns and piles.
Advantages of Silica Fume/Micro Silica
- Use of micro silica improves the mechanical properties of the concrete such as,
(a) It gives a high early compressive strength of concrete.
(b) It gives high tensile strength and flexural strength and modulus of elasticity.
(c) It provides higher bond strength to concrete.
- Condensed silica fume has a very low permeability to chloride and water intrusion.
- Silica fume increases the durability of concrete.
- It also improves abrasion resistance.
- Silica fume decreases the bleeding and segregation thereby allowing a better efficient finishing process to the concrete.
- Condensed silica fume has superior resistance capacity against chemical attack from chlorides, acids, nitrates and sulphates.
- It provides high electrical resistivity and low permeability.
- Silica fume produces superior shotcrete. It gives greater bonding strength and assures outstanding performance of both wet and dry process of shotcreting.
Disadvantages of Silica Fume/Micro Silica
- Silica fume concrete has a large shrinkage rate. In case the external temperature is high, it will lead to early dry shrinkage. Hence, it is more prone to cracks which may ultimately affect the overall strength.
- The construction with the silica fume concrete is difficult; as workability of silica fume concrete is poor. Therefore, it is difficult to place and compact. Moreover, it influences the smoothness of concrete and surface uniformity.
- Condensed silica fume has a large surface area. Hence the amount of water required in the concrete mix increases which makes it necessary to use a plasticizer or super-plasticizer along with it.
- Cost factor is also one of the disadvantages while using silica fume in cement.
Chemical and Physical Properties of Silica Fume
01. Chemical Properties
- Silica (SiO2): 85 -97%
- CaO: < 1%
02. Physical Properties
- Colour: Light to dark grey
- Specific Surface Area: 20000 m2/kg
- Specific Gravity: 2.20
- Bulk Density: 200 to 300 kg/m3
- Physical Form of Silica Fume
‘A.M. Neville’ (Author of Properties of Concrete) specifies that,
- Basically, silica fume is available in a very light powder form, but it is quite difficult to handle it.
- Due to difficulty in handling of fine powder form, silica fume is available in the densified form in the market which has a bulk density of around 500 to 700 kg/m3.
- Another form of silica fume is It is formed using an equal part mass of water and silica fume. The density of slurry is around 1300 to 1400 kg/m3. Periodic agitation of the slurry is necessary to maintain a distribution of silica fume in the slurry. You can add admixtures like water reducer, concrete retarder, and super plasticizers in the slurry.
How Can Silica Fume be Added in the Concrete?
Condensed silica fume or micro silica can be added directly into the concrete as an admixture or blended as an individual ingredient with ordinary Portland cement. Silica fume can replace 9-15% by mass of Portland cement.
Followings are Different Manufacturers whose Products are Easily Available in the Market:
- Elkem – Micro Silica
- MLA Industries – Micro Silica
- CABOT – Cab-O-Sil
- Triveni Chemical – Silica Fumed
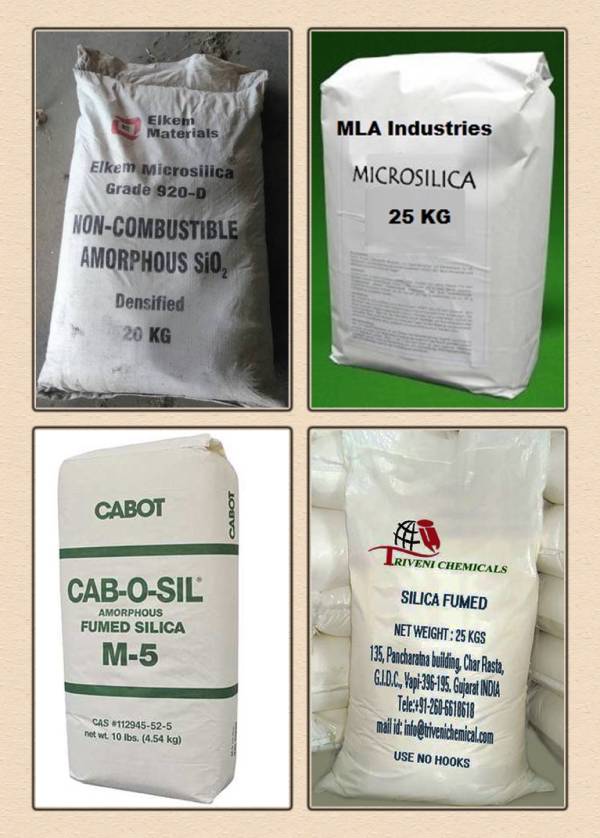
Micro Silica Products
Effect of Silica Fume on the Properties of Concrete
01. High Water Demand:
- due to high surface area.
02. Workability of Concrete:
- The silica fume concrete is more cohesive and less susceptible to segregation as compared to the ordinary concrete. As the amount of silica fume content increases, the concrete may seem to become sticky.
- In the silica fume concrete, the workability is lost with time and loss is directly proportional to the increase in the amount of condensed silica fume because of the large surface area of silica fume. Though the slump or workability decreases, the mix remains highly cohesive.
03. Bleeding and Segregation:
- Use of silica fume reduces bleeding significantly since the free water more than actual required for hydration is consumed in wetting of the large surface area of the micro silica and therefore, the excess water responsible for bleeding also decreases. Thus, concrete containing silica fume shows substantial reduced bleeding. Silica fume also fills the pores in the fresh concrete, so water within the concrete is not allowed to come to the surface. Silica fume also reduces the segregation of concrete due its high cohesiveness.
04. Permeability:
- Use of condensed silica fume makes concrete dense and also gives greater impermeability.
05. Strength:
- Silica fume concrete has good mechanical properties such as good compressive strength, bond strength, flexural strength etc.
06. Chemical Diffusion:
- Silica-fume concrete is highly resistant to penetration by chloride ions. It also gives better resistance against the attack of sulfates and other aggressive substances.
07. Unit Weight:
- Use of silica fume does not remarkably change the unit weight of concrete.
Summing up, the use of silica fume gives rise to a variety of concretes with different properties which can be used in fresh as well as in the hardened state with less cement. Silica fume provides high durability to the concrete. Where at one end there are advantages associated with it, there are few difficulties in the form of disadvantages too associated to work with silica fume. Therefore, usage of water-reducing admixtures or high range water reducing admixtures or both is recommended to maintain the desired w/c ratio as well as workability as the addition of silica fume increases water demand.If this is handled properly, it is certainly a new-age material that can achieve high strength concrete above M40 grade and simultaneously give impermeable, dense and durable concrete, thereby extending the basic life of the structure and lessening the pollution.
Also Read:
Fly Ash for Concrete: Properties, Uses, Advantages & Disadvantages
Polymer Concrete: Its Pros-Cons, Uses & Properties
Bioconcrete: New Perspective of Self-Healing Concrete
Image Courtesy: Image 2, Image 3(a), Image 3(b), Image 3(c), Image 3(d)