The batching of concrete ingredients is an essential task for every concrete work. Batching is the process, in which the quantity or proportion of materials like cement, aggregates, water, etc. are measured on the basis of weight or volume to prepare the concrete mix. Before making the concrete mix, concrete ingredients should be batched or proportioned properly and accurately to achieve the excellent quality of the concrete. The batching helps to improve the workability of the concrete, to achieve a smooth surface of the concrete, and increase the speed of the construction and reduce the wastage of the concrete ingredients. Thus, batching of concrete ingredients is an essential process while making concrete. Know more about the importance of batching of concrete.
Water and admixture can be measured by volume in a calibrated tank or container. However, it is not practically possible to measure sand and aggregates by volume. Because, a mix, which is formed by volumetric weigh batching does not meet specifications. I.e. during the rainy season, the sand and aggregates have the maximum moisture content. Hence, it is necessary to weigh the sand and aggregates instead of measuring their volume. Weigh batching of concrete is the correct and preferred method of measuring concrete ingredients which leads to more uniform proportioning. Weigh batching is done in a very modern batching plants or mixing plants.
Weigh batching system facilitates simplicity, flexibility and accuracy for batching of concrete ingredients. Different types of weigh batchers available in the market and it depend upon the nature of the job.
Choice of the Batching System
There are different factors those affect the choice of the batching system are:
- Size of job
- The production rate of concrete
- Based on the accuracy of weight measurement and standard batching performance
Weigh batchers function in either electronically or mechanically. Nowadays electronic weigh batchers are more trending than the mechanical weigh batchers, but still some plants use mechanical weigh batchers to serve as a backup for an electronic weigh batcher. Mechanical weigh batchers have dial type scales which use spring to measure the weight of concrete ingredients. Electronic weigh batchers have electronic scales which are suspended by load cells which convert force into a measurable electric quantity. Load cell is supported by the hoppers, tanks or other vessels that convert strain into an electrical signal. Electronic scales measures accurately and it does not need to repair frequently.
Electronic weigh batchers are available in a variety of forms. Depending upon the type of batch plant, the weigh batcher should be used i.e. high-silo, low-profile, or underground batching plant. Batchers can be stationary ones that are not moving while they are weighing, or they can be non-stationary batchers that weigh as they transport materials.
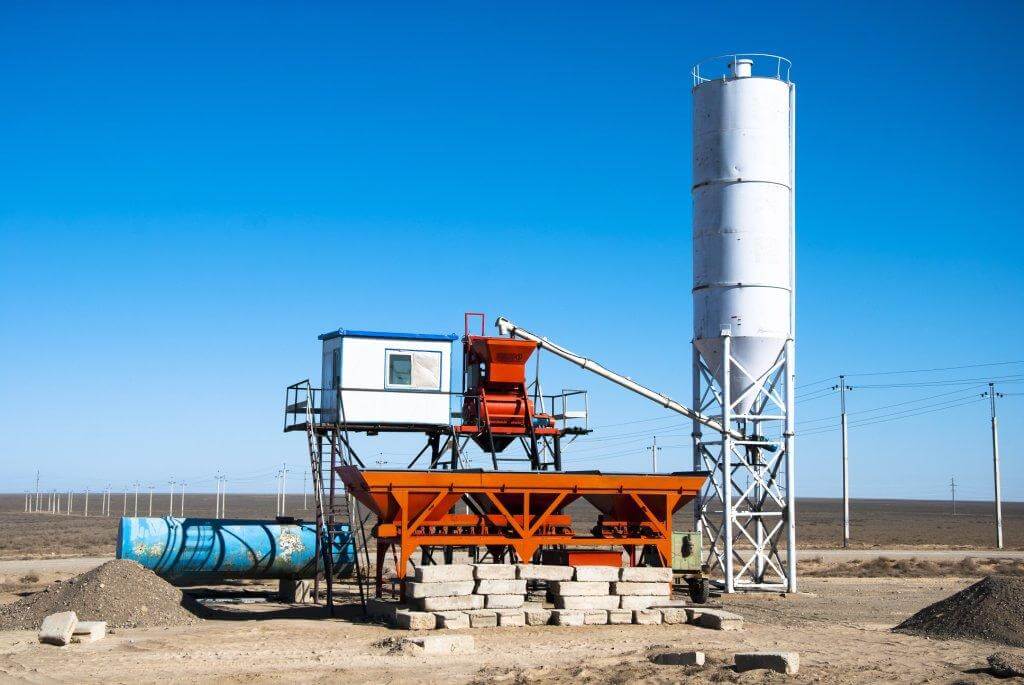
Weigh Batchers Equipment
These type of equipments fall into three categories:
01. Manual Weigh Batching:
In manual batching, weighing of all concrete ingredients is done manually. Manual weigh batching system may be used for small jobs.
02. Semi-automatic Weigh Batching:
In semi-automatic weigh batching, the aggregate bin gates are opened by manually operated switches and gates are closed automatically when the material has been delivered.
03. Fully Automatic Weigh Batching:
It is automatic equipment for batching of concrete ingredients requires qualified and experienced engineers. These systems have automatic microprocessor controlled batching arrangements. Not only the aggregates are batched in correct proportion but also their moisture content is automatically measured and necessary corrective action should be taken so that mix has desired consistency. For example, if wet sand is batched instead of dry sand, then batching plant auto corrects the quantity of water so that it reduces the quantity of water during the batching and maintain the w/c ratio.
These types of batching plant are mostly suitable for large and very important jobs like mass concreting. In weigh batching the mix proportions are usually based on the 50-Kg bag of cement and specified as 50 Kg of cement to so many Kg of sand to so many Kg of aggregates.
For example, M25 grade of concrete:
Mix proportion of M25 grade concrete is 1: 1: 2. So take one 50 Kg bag of cement, 50 Kg of sand and two times 50 Kg of aggregates.
Weigh batching has a great advantage as it gives good quality of concrete and providing more accurate and consistent mixture. Sometimes errors occurred due to imperfect calibration of weigh batcher which leads to inconsistencies in quality so calibration of the plant is always required.
The strength and durability of concrete largely depends on the proportion of concrete ingredients and water-cement ratio. Hence weigh batching of concrete ingredients is must and recommended. There are various ready-mix concrete companies and ready-mix concrete suppliers who supplied weigh batched concrete. They have concrete plant having different capacity. They help us to deliver right quality and quantity of concrete as per required mix design within stipulated time. Thus, it is advisable to use ready mix concrete rather than make it on site without weigh batch.