Concrete is a versatile, durable, sustainable, and economical material and it is the world’s most widely used construction material. To make the excellent quality of concrete, the proportion of concrete ingredients should be measured properly and accurately. One can accurately measure the concrete ingredients by carry out the batching process. Batching is the process in which the quantity or proportion of materials like cement, aggregates, water, etc. are measured on the basis of either weigh or volume to prepare the concrete mix.

Proper Batching improves the workability of concrete by reducing the segregation or bleeding in concrete. It helps to get a smooth surface of the concrete. It also increases the speed of construction and minimizes the wastage of concrete ingredients. Hence, batching of concrete is an essential process while making concrete. Know more about the importance of batching of concrete.
To form the durable, sustainable and economical concrete, one should have to carried out the concrete mix design (CMD). The scientific and systematic process of choosing economical relative proportion of various ingredients from the available material which gives cohesive concrete of the desired workability at the fresh stage and desired strength and durability in the hardened stage is known as Concrete mix design (CMD). Know more about concrete mix design (CMD).
Once concrete mix design is carried out, the first task is batching of concrete materials like cement, aggregates, admixture, etc. The batching of concrete is done by measuring and combining required concrete ingredients either by weight or by volume as per the mix design.
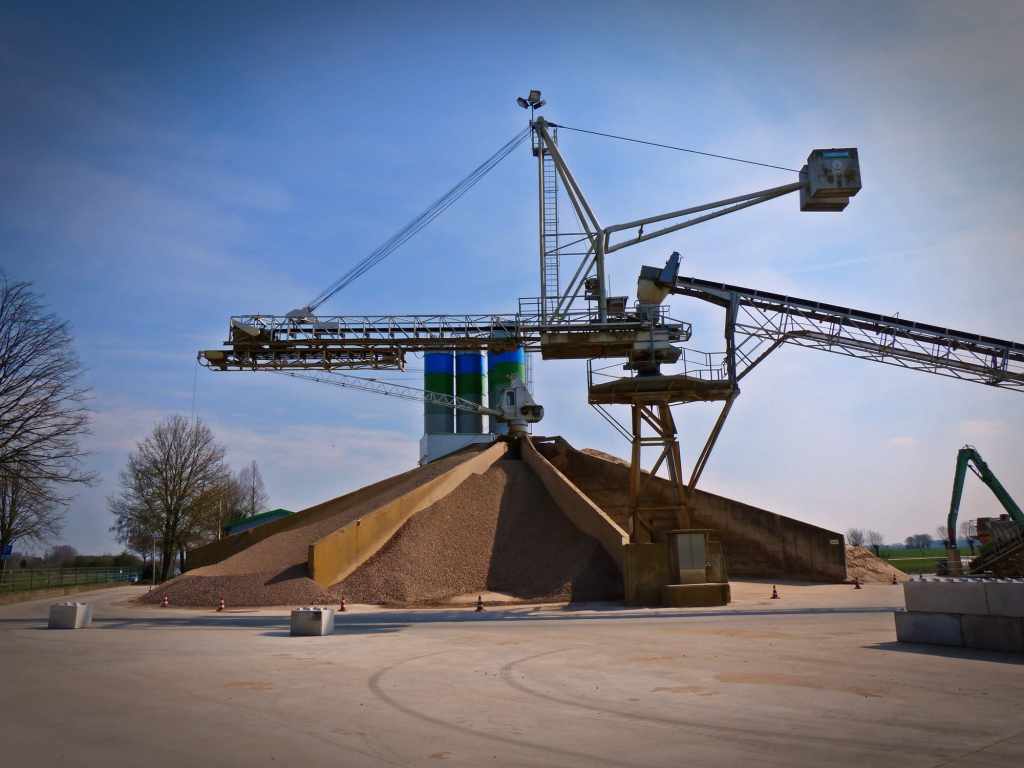
Once materials are batched, they are introduced into a concrete mixture to produce a uniform and homogeneous concrete mix. The concrete mixer machine combines cement, aggregates (sand or gravel), and water to form the concrete. The mixer machine not only achieves the uniformity of the concrete mix, but also discharges it without disturbing that uniformity. The mechanism which mixes concrete is known as the “mechanical concrete mixer”, or simply “concrete mixer”. Know more about different types of concrete mixture machine.
Methods of Concrete Batching
There are three modes of batching of concrete ingredients which are generally adopted before carry out concrete mixing. They are as follows:
01. Random Volumetric Batching of Concrete Ingredients
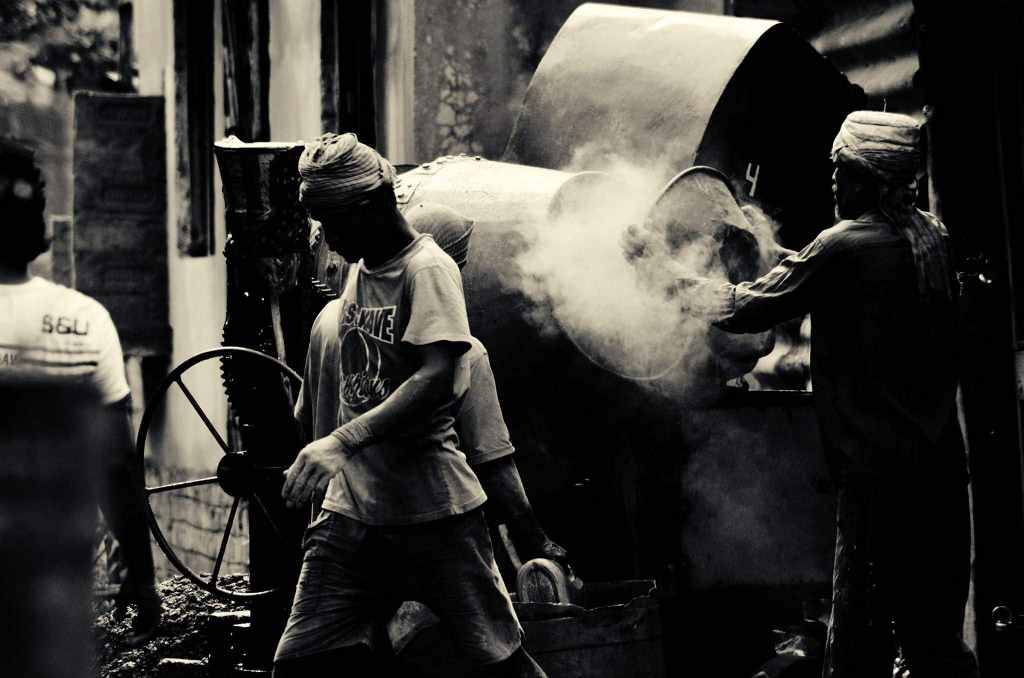
Random volumetric batching is a batching process in which, one cannot control the proportion of concrete ingredients like cement, aggregates, water, etc. It results in the errors, and ultimately, the concrete may not achieves its designed strength. In random volumetric batching, the proportion of concrete ingredients cannot be controlled due to the size and shapes of containers i.e. the workers counting the numbers of ghamelas (tagari) for proportioning the concrete ingredients. This practice is absolutely unscientific, crude and should never be allowed even for a small job.
Know more about the disadvantages of using ghamelas while batching of concrete.
02. Volume Batching of Concrete Ingredients
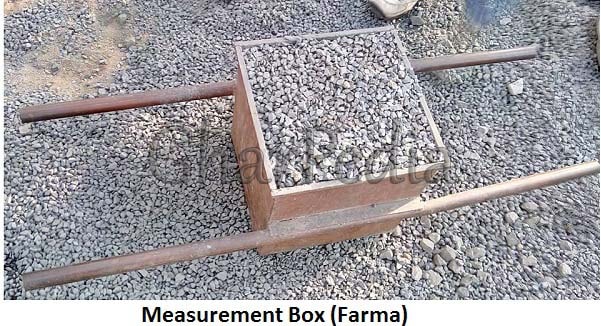
Volumetric batching of concrete is done by using measurement boxes, locally known as “farmas” or “gauge boxes”. In an ideal case, the volume of the farma is made equal to the volume of one bag of cement i.e., 35 litres or multiple thereof. Concrete ingredients like fine aggregates (sand), 10 mm Coarse aggregates or 40mm Coarse aggregates (Kapachi) are measured by farmas or gauge boxes. Care must be taken to see that the farmas or gauge boxes are not overfilled. In volumetric batching, water is measured either in Kg or litres. To measure the quantity of water, the water meter is used while batching or use cans of water having the fixed volume.
Know more about volumetric batching of concrete.
03. Weigh Batching of Concrete Ingredients
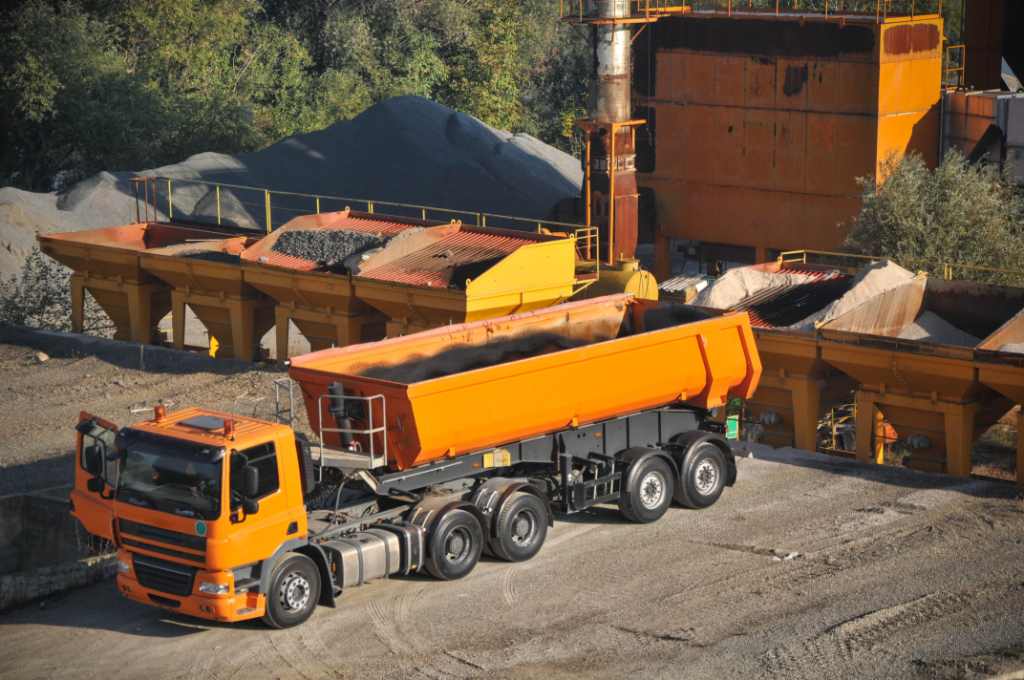
In weigh batching of the concrete, the proportion of concrete ingredients is decided by the weighing (batching plant). It is done either by using “weigh batchers” or by other equivalent weighing systems.
Weigh batching system facilitates simplicity, flexibility and accuracy. On large projects, automatic batching plants are usually installed, which helps in achieving ultimate quality and consistent. Depending upon the type of job, different types of weigh batchers are available in the market. I.e. manual weigh batching, semi-automatic weigh batching, and fully automatic weigh batching (batching plant).
Water is an essential constituent and hence using optimum water is must. Less water would make concrete unworkable while excess water will reduce the strength of concrete. Water must be measured accurately in litres.
Know more about weigh batching of concrete.
The choice of batching method depends on the size of the job, production rate and standards of batching performance.
Disadvantages of Poor Batching of Concrete Ingredients:
- Poor batching of concrete ingredients directly impacts the strength of concrete. Because of poorly batching, concrete ingredients never mix homogeneously and therefore workability will suffer.
- Poorly batched concrete ingredients may result in the formation of voids in the concrete which leads to honeycombing.
- Poor batching also results into porous concrete which becomes the reason of leakages in the house.
- The porous concrete may be the reason of corrosion and will ultimately reduce the life of the structure and increase the cost of repairs.
Traditionally batching of concrete is done by volume. Batching accuracy is important. It is however preferred to do weigh batching rather than volume batching. Volume batching may be allowed only where weigh batching is not practical. It is always advisable to spend little bit extra on the concrete mix design and follow all the batching process recommended by the designer, as in the long term, it will saves you a fortune.
Note: The quantity of cement should also be measured with an accuracy of ± 2 percent and the quantity of aggregates, admixtures and water should be measured with the accuracy of ± 3 percent.