Concrete is a composite material made up of cement, sand, coarse aggregates, water and chemical admixtures (if required). It is the primary construction material. It plays a significant role in the structure’s serviceability and durability. Not only the concrete but the process of concreting such as batching, mixing, transporting, compacting and finishing etc. also plays a significant role. Though making concrete is very easy, the proper concreting process is quite difficult and requires extra care specially the process of mixing of concrete ingredients.
Importance of Mixing of Concrete
Proper mixing of concrete ingredients is of utmost importance in order to produce good quality of fresh concrete. During the process of mixing the surface of all the aggregate particles is coated with cement paste. Well mixed concrete is required for the desired workability and performance of concrete in both the fresh as well as the hardened state. If the concrete is not well mixed, then it tends to segregation and bleeding.
Characteristics of Well Mixed Concrete
- Concrete should be of uniform colour.
- All concrete materials like cement, fine aggregates, coarse aggregates and water should be homogeneously mixed.
- Cement paste should cover all the surface of the aggregate.
- Segregation or bleeding of concrete should not occur after the concrete mixing.
Methods for Mixing Concrete
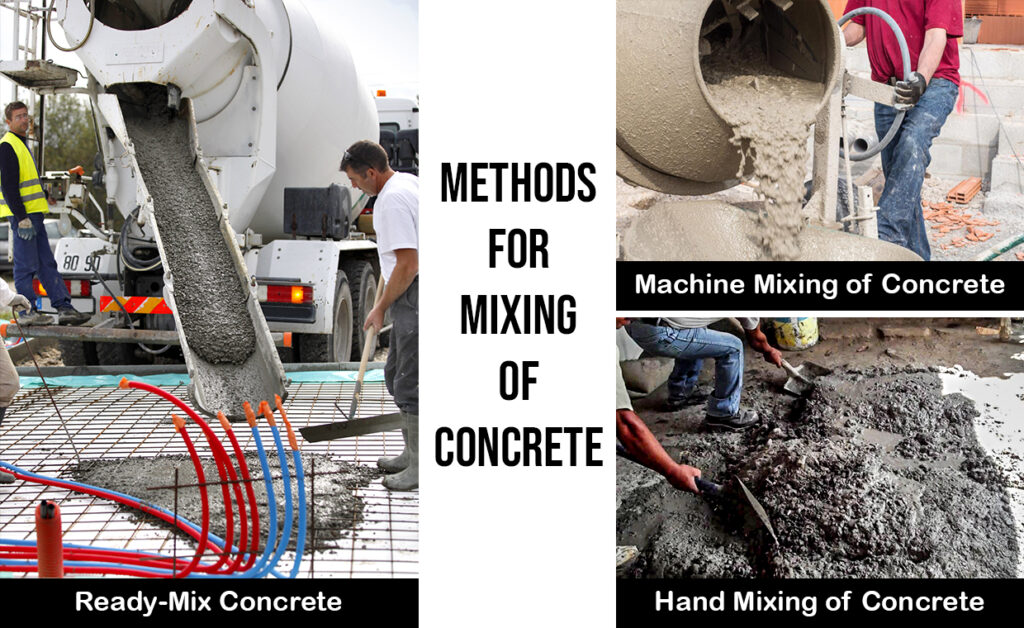
When it comes to mixing concrete, following three mixing methods are used for the production of effective and good quality concrete.
01. Hand Mixing of Concrete (Mixing concrete manually without a mixer machine)
02. Machine Mixing of Concrete (Mixing concrete with a mixer machine)
03. Ready Mix Concrete (Mixing in automatic or semi-automatic batching plant)
Different constructions require different type of concrete mixing. For the efficient result, using appropriate method of mixing of concrete for the specific use and application is essential. Several factors affect the method of concrete mixing such as,
- Location of the construction site with sufficient land for construction activities e.g. highly congested urban areas
- Available space for concrete batching and mixing and storage of aggregates
- Volume of concrete needed
- The construction schedule like the volume of concrete required per hour or per day
- Height at which concrete is to be placed
- Cost
Let’s take a detailed look into each of the above mentioned three methods of concrete mixing.
01. Hand Mixing of Concrete (Mixing of Concrete Without a Mixer Machine)
Hand mixing is the process of mixing the ingredients of the concrete manually without a mixer machine. Mixing concrete without a mixer is used only for small works where the concrete requirement is less and quality control is less important. In the hand mixing of concrete, uniformity of mixing is difficult to achieve and requires special care and efforts.
According to ‘M. M. Goyal’ (Author of Construction Handbook for Civil Engineers and architects), concrete may be mixed by hand only as an exception when the volume to be used does not warrant the use of a mechanical mixer. 10% extra cement shall be added to the nominal mix concrete proportion in case of hand mixing.
Our mentor, ‘Shri Mahadev Desai’ (CMD of Sthapati Designers & Consultant PVT LTD, the leading multidisciplinary consultancy organization of India since 40 Year) cautions never to use hand mixed concrete for important structural elements like columns, shear walls etc.
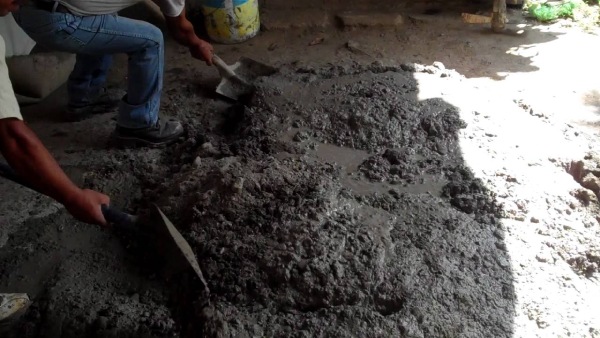
Process of Hand Mixing of Concrete:
- Hand mixing of concrete is done on a hard, clean and non-porous base made of masonry or flat iron sheet plates.
- The measured quantity of sand is spread on the platform and then the cement is dropped over the sand.
- The sand and cement are mixed thoroughly for several times with the help of shovels in the dry state until the mixture attains an even colour throughout and is free from streaks.
- Next, the measured amount of coarse aggregates is spread out in uniform layer on the above mixture and mixed properly. Remember to use measurement boxes for batching of aggregates, i.e. to determine how much aggregates are to be used. Never use or allow the use of ‘Ghamelas’ for batching, i.e. measuring quality of aggregates.
- Later, the whole mixture is blended properly like turning over by twist from the center to the side, then back to the center and again to the sides several times.
- After that, depression is made at the center of the mixed materials.
- And, 75% of the required quantity of water is added in the depression and mixed with the help of shovels.
- Lastly, the remaining amount of water is added and the mixing process is continued till a uniform colour and consistency of concrete is obtained. The total time taken for mixing of concrete should not exceed 3 minutes.
Precaution to be Taken Care While Hand Mixing of Concrete:
- Base platform must be clean, dirt free and watertight.
- Use a good and clean shovel for the mixing procedure.
- If there are any dirt or debris in the aggregates, wash them before use.
- The personal protective equipment like hand gloves, mask etc. are must to be worn by the labours and masons while mixing and handling the concrete.
- The mixing platform should be cleaned at the end of the day’s work.
02. Machine Mixing of Concrete (Mixing Concrete with a Mixer Machine)
Machine mixing is the process of mixing the ingredients of the concrete with a concrete mixer machine. It is highly effective for fulfilling the demands of short mixing time, optimum consistency and homogeneous quality of concrete.
According to ‘A. M. Neville’ (Author of Properties of Concrete), machine mixing of concrete not only imparts the uniformity of the mix but also discharges the mix without disturbing that uniformity. Machine mixing of concrete is most suitable in the large projects where large masses of concrete are needed because it ensures the consistent homogeneity of the concrete.
Nowadays various types of concrete mixers powered by petrol, diesel or electricity are available. Even there are various company provides concrete mixing services such as Baton Rouge Concrete Experts which provides the best results for concrete practices. To know more about the types of concrete mixers in detail, please read Different Types of Concrete Mixers/Machines.
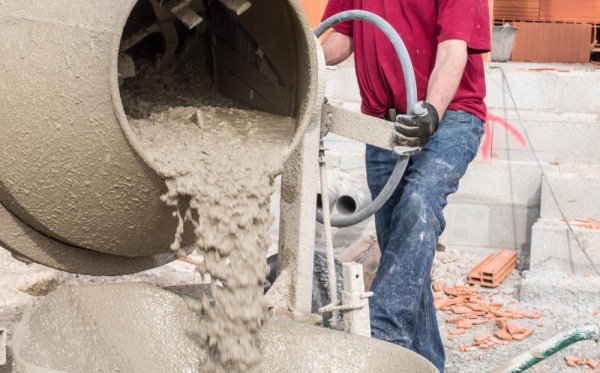
The Process of Machine Mixing of Concrete:
- First of all, wet the inner surfaces of the drum of concrete mixer.
- Coarse aggregates are placed in the mixer first followed by sand and then cement.
- Mix the materials in the dry state in the mixing machine. Normally it should be 1.5 to 3 minutes.
- After proper mixing of dry materials, gradually add the correct quantity of water while the machine is in motion. Do not add more water than required. It is not advisable as it reduces strength.
- After adding the water, you must mix concrete for a minimum of two minutes in the drum.
- If there is any segregation of concrete after unloading from the mixer, then remix the concrete.
Precautions to be Taken While Machine Mixing of Concrete:
- Concrete mixer machine must be wet before use.
- Take care of mixing time, speed and numbers of revolution of mixer drum as per the recommendation of the manufacturers of the mixer machine.
- Concrete should be used within 30 minutes after mixing and discharged by the concrete mixer.
- If your mixing is batch type then, after discharging one batch of concrete, the interior surface of the mixer drum should be cleaned thoroughly. If not, lumps of hardened concrete from the mix of previous batch may form a part of the subsequent batch and deteriorate the quality of concrete.
- If your mixing is of a continuous type, it is necessary to clean the concrete mixer after fixed intervals.
- The inner portion of the concrete mixer should be carefully inspected at regular intervals to check for damages, shatter or corrosion.
03. Ready Mix Concrete
In India, on-site production of the conventional concrete with the use of labour force and with the primitive mixer machine equipment is very commonly used. However, the ready mix concrete is also becoming popular nowadays.
According to ‘K. Newman’ (Lecture notes on Ready mix concrete published by Indian Concrete Institute), Ready Mix Concrete (RMC) is a specialized material in which the cement, aggregates and other ingredients are weighed and batched at a plant at a central location, then mixed either in a central mixer or in truck mixers, before being delivered to the construction site in condition ready for placing by the customer.
The quality of resulting concrete is much better than the site-mixed concrete i.e. both the hand mixed and machine mixed concrete.Ready mix concrete is particularly useful on congested sites or in road construction where there is little space or no space available for a mixing plant or for storage of aggregates.
In this method, quality control of concrete is easy as the batching and mixing of concrete is done at the mechanized central batching plant. This method of mixing is very useful for several places i.e. in congested area, at night concreting work, at large construction site etc.
In the ready mix concrete, water/cement ratio can be controlled easily as compare to the other mixing methods. It is possible to mix the admixtures i.e. fly ash and cement in exact quantities or proportioned or otherwise overuse of construction chemicals may happen. These difficulties can also be avoided with the use of ready mix concrete.
To know more about ready mix concrete, please read our articles ‘Ready Mix Concrete (RMC): High Speed Concrete Construction without Sacrificing Quality’ and ‘Material Buying Guide for Ready Mix Concrete’. It will definitely help you in ordering the ready mix concrete.
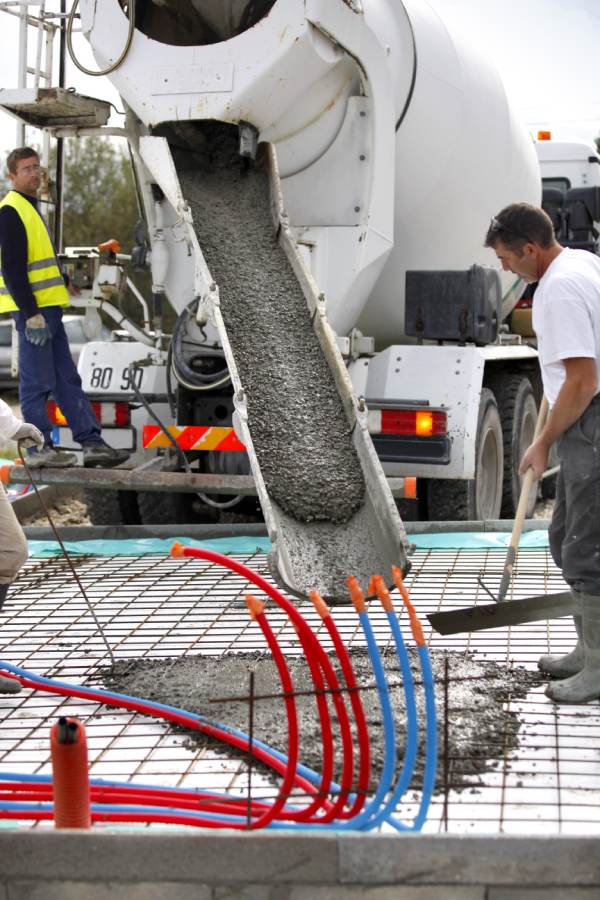
Summing up, hand mixing of concrete is the cheapest method of concrete mixing but recommended only for very small works where only small amount of concrete is required, because, uniform quality of concrete is difficult to achieve in this method. On the other side, the machine mixing of concrete gives proper mixing of materials and hence used for medium sized projects.
Ready mix concrete requires less time as compared to site mixing (hand and machine mixing) and quality of concrete is also better than the site mixing. Further, it is very useful when you need huge volume of concrete per day, which otherwise is not possible to achieve with even more than one machines on site. It of course has solved many problems on highly congested urban sites full of traffic.