Concrete is one of the most widely used and versatile building materials known to man. Concrete is also amongst the most common artificial material on the planet. Humans use billions of tons of concrete every year for raising various structures. The history of concrete goes long back. It is evident that it has been in use since ancient Rome. A lot of modifications were made since then. Well, with the development of science and technology, civil engineering made a parallel progress. And, today with immense efforts and researches, concrete has made its way to being an integral part in construction.
So as to put it in simple words – Concrete is a building material made from cement, aggregates (rock and sand), water, and admixtures (chemicals that enhance or modify the properties of concrete). Now, there is lot of construction chemicals used in construction. The construction chemicals industry has a variety of products, ranging from concrete admixtures to sealants, grouts, bonding agents and waterproofing chemicals. These chemicals have an extensive usage in the construction industry. Such construction chemicals can increase the strength of concrete or when used with different permutations and combinations and, in different quantities, many other limitations can be overcome due to them. Bonding agent is one such chemical used in concrete and hence, this article we are going to discuss bonding agents for concrete.
What is a Concrete Bonding Agent?

The very first question that strikes our mind is – what is a bonding agent? Well, in simple words we can define them as – “Natural, compounded or synthetic materials used to join individual members of a structure without mechanical fasteners.” These Bonding agents are often used in different repair applications, such as bonding of new concrete to old concrete, sprayed concrete at construction joint or sand cement repair mortar to assist in achieving a reliable bond.
There are factors affecting the bonding between the old and new concrete. So, let us see what they are.
Primarily two factors affect the bonding between the old and new concrete:
- Strength and integrity of the old surface
- Cleanliness of the old surface
Why Bonding Agent is Necessary?
Generally, Bonding Agents are used in concrete where there is a requirement to join the old and the new concrete surfaces. It is also used to join the surfaces between the successive concrete layers.
The basic function of bonding agent is to increase the bond strength or let us say to strengthen the bond between the old and new concrete surface. The cement within a concrete mix does not have any natural bonding agent. Hence, when fresh concrete is poured on top of an existing layer of concrete, the existing and new poured concrete layer do not tend to join together. Once poured concrete layer is cured, the new concrete will simply settle on top as a separate layer. This will not create a strong bond between the two successive layers. Thus, when the two layers fail to behave like one unit, it will ultimately affect the performance and strength of the structure. A bonding agent (bonding adhesive) therefore needs to be applied onto the existing concrete surface so as to ensure that the fresh concrete successfully adheres.
The same is also true for floor repairs. The new concrete will not adhere to the old concrete without the help of a bonding adhesive if concrete without any bonding agent is used to fill gaps caused by damage.
While we discuss about bonding agents for concrete, we ought to know their characteristics. So, let us see one by one.
Characteristics of Bonding agents
01. It provides excellent adhesion and workability.
02. It enhances the tensile, flexural and bond strength of the concrete as well as mortar.
03. It also reduces the permeability of the concrete.
04. It reduces the risk of cracking.
05. It increases the resistance against frost and various other chemical.
06. It enables easy use and application.
Bonding Agents for Concrete
Let us now understand the various bonding agents that can be used in concrete. The preliminary Bonding agents are water emulsions of several organic materials which are mixed with cement or mortar grout. It is applied all over the old surface prior to patching with mortar or concrete. Bonding agents usually cause entrainment of air and have a sticky consistency in a mixture. They are effective only on dry, clean and sound surfaces.
The most commonly used types of bonding agents are generally made from natural rubber, synthetic rubber or from any other organic polymers. The polymers include polyvinyl chloride, polyvinyl acetate etc. In the olden days in absence of bonding agent cement slurry was used instead.
However, according to ‘M. M. Goyal’ (Author of Construction Handbook for Civil Engineers and Architects), cement slurry alone is not adequate for the proper bond between the old and fresh concrete. Latex or epoxy bonding agents distinctly improve the adhesion of the new concrete or mortar to the old concrete surface. The bonding agents can be used for cold joints. They can also improve water impermeability of concrete. They also serve for polymer modification of cement mortar and concrete. With the addition of bonding agent in repair mortar or concrete, the reduced water-cement ratio can be adopted for the same workability, thereby reducing drying shrinkage.

Bonding agents can be further categorized into two categories, namely, Re-emulsifiable type and Non-Re-emulsifiable type. Non-Re-emulsifiable type is better suited for external applications since they are resistant to water.
Now, there are several steps we need to follow systemically while applying bonding agent to the concrete.
Steps to Apply Concrete Bonding Agent
Step 1: Clean the Surface

It is very essential to have a clean surface. If the existing concrete surface consists of any dust, oil or grease, efflorescence the bonding agent will not work properly. Hence this step is very important in order to make sure that the bonding agent works well on the concrete surface. Intensive cleaning can be achieved by pressure washing or vacuum shot blasting.
Step 2: Prepare the Admixture
The container of concrete bonding agent must be shaken well before use. The chemical must be then poured in appropriate amount into a separate bowl and diluted with water as per required consistency. The whole mixture must be mixed properly. This mixture can be used as a primer. However, it is advised to follow the manufacturer’s instruction to decide proportions.
Step 3: Mixing
The next step is mixing. The concrete bonding agent must be mixed properly and thoroughly. Reading the instructions mentioned on the container is must. The amount and time for application (after the container is opened) mentioned on the container must be followed. It must be noted that the amount and time differs for different types of bonding agents. Inappropriate mixing can cause damage to the concrete surface, or the concrete chemical might not work properly. Hence it is very important to follow the instructions as specified.
Step 4: Placing or Applying the Concrete Bonding Agent
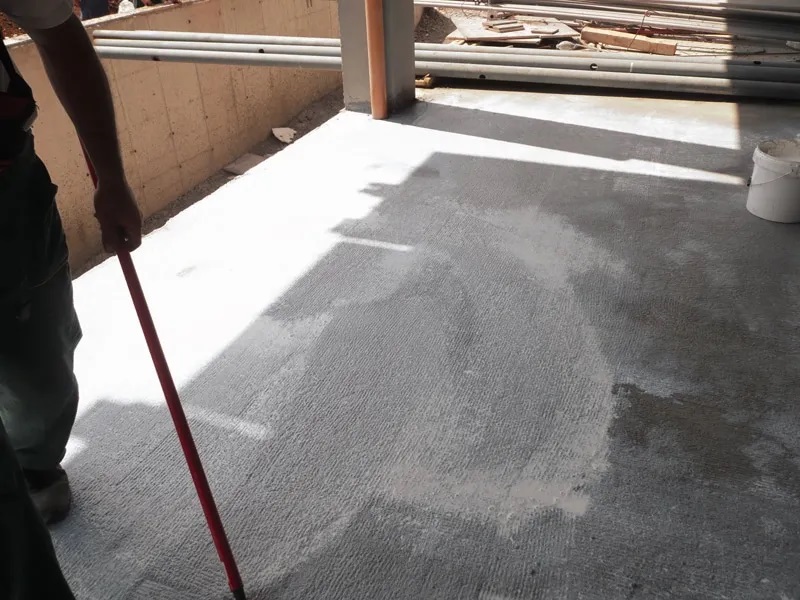
Once the concrete mix is prepared by incorporating the bonding agent, it must be applied on the surface immediately. If too much time has passed, the primary coating may dry off losing its adhesion. Hence, the mix has to be applied when the chemical is still tacky and not completely dry. For production and placing of the concrete, standard rules must be followed. Once the application is completed, smoothen the surface with the help of a trowel and allow it to cure.
Now that we know the steps of applying concrete bonding agent, let us further understand the types of bonding agents.
Types of bonding agents
Latex emulsions

Latex emulsions are most commonly used as the oil-in-water type emulsions in cementitious compositions. These emulsions contain more than 50% water in some compositions. Some have a greater degree of water resistance in comparison with the others. The composition of latex emulsions is generally stable in the cement/water system. However, all emulsions are not compatible with the cement. Selection of an appropriate Latex emulsion for a given application requires an understanding of its chemistry or, alternatively, consult the manufacturer. However, the use of the latex without cement content in the mix produces a failure plane due to the lack of film formation at the bond interface. There are a number of ways these emulsions can be used as bonding agents.
According to ‘Euclid Chemical’, (world-leading manufacturer of specialty chemical products for the concrete and masonry construction industry), three following methods can be used to modify latex into a useful bonding agent:
01. Preparing neat cement slurry, consisting of latex as part of the mixing water.
02. Using 1:1 water-latex diluted material.
03. By using re-emulsifiable latex, it can be softened and rewetted upon contact with water.
These latex emulsions which are commonly used in construction industry are classified into three categories. They are as follows:
01. Acrylic Latex
Acrylic esters are the polymers and co-polymers of methacrylic acid and esters of acrylic. The physical properties of acrylic latex ranges from soft elastomers to hard plastics depending upon the polymers used. Acrylic latex is milky white in colour and consists of 45% solid content in it. The primary use of this type of latex is bonding fresh concrete to the old concrete. It can be applied by a brush, broom, spray, roller as adhesive or trowel as a topping. This type of emulsion is used in the cementitious compounds in manner similar to SBR Latex.
02. Styrene Butadiene (SBR)
Styrene butadiene (SBR) latex is a co-polymer which is compatible with the cementitious compounds. However, if SBR latex is subjected to high temperatures for a long period of time, it may coagulate. Like Acrylic latex, SBR latex is also milky white in appearance, consisting of solid content up to 55%. They are primarily used for bonding fresh concrete to the old concrete and thin layer toppings. Additionally, they can be used as a plaster bond within 45-60 minutes.
According to ‘Sika AG’ (Sika AG- a Swiss specialty chemical company), the following are the uses of SBR,
01. It can be used for waterproofing of roof slabs, sunken slabs, basements, water tanks, sunshades etc. in combination with cement
02. It is used as a bonding agent for uses in repair and plastering.
03. For making polymer mortar for repairs, etc.
04. For treatment for leaching and saltpeter action
05. In addition, multipurpose mortar admixture can be utilized for injection grouts.
03. Polyvinyl Acetate (PVA)
There are generally two types of Polyvinyl Acetate latex (PVA) that are used for the repair applications in the construction industry. They are non-re-emulsifiable and emulsifiable. The non-re-emulsifiable forms a thin film that offers great water resistance, aging characteristics and ultraviolet stability. This type of latex is widely used as a bonding agent, mostly due to its compatibility with the cement. Additionally, they are also used as a binder for cementitious water-based paints and waterproofing coatings. Whereas, emulsifiable polyvinyl acetate latex (PVA) produce a film which can be softened and rewetted with water, if required. This type of latex permits application of the film way before the application of a water-based overlay. The applications of PVA latex are limited to use where the possible infiltration of the moisture to the bond line is precluded. They are also used for the interior surfaces of the cast-in-place concrete.
Epoxy Resin
Epoxy resin is the most ideal resin for high performance and lightweight parts. It has a great bonding capability and wets out fast. Epoxy resins are widely used in the construction field because of their high compressive strength, strong adhesion, chemical resistance and other unique properties. They are available for the bonding of fresh concrete to the old concrete. Additionally, they are also used for the bonding of concrete to steel. Epoxy resins may or may not contain fillers. The products are mostly available in various consistencies that range from highly filled paste to liquids similar to that of water.
Epoxies are perhaps the most versatile of the structural adhesives. Although generally characterized as being strong but brittle, they can be formulated to be more flexible without loss of tensile strength. They have an ability of bonding to a variety of substances efficiently and can be formulated to cure either at room temperature or elevated temperatures, under dry or wet conditions.
Epoxies bond well to almost every material provided the surface is properly prepared. The unique properties which give epoxies their unusual adhesion characteristics are:
01. Cured epoxies offer tensile and compressive strengths as high as, or even higher than concrete.
02. Compounds can be in liquid form and contain no volatile solvent, e.g. after polymerization (curing), the liquid resin turns into 100% solids.
03. They adhere to most construction materials.
04. There are no by-products during the curing period.
05. There is limited shrinkage during and after cure.
06. Cured epoxies have dimensional stability.
Primary Uses

The primary applications of epoxy resins for bonding concrete are as under:
01. It is used for bonding plastic mortar or concrete to hardened concrete or metal.
02. For bonding hardened concrete or other material to hardened concrete, e.g. setting dowels in preformed or drilled holes. Application of epoxy adhesives for jointing pre-cast concrete structural elements during erection. In this method, precast box sections are lowered successively into place as cantilevers from the bridge piers or building column. High strength epoxy being used as the jointing (structural gluing) material. The whole string of segments is made continuous by post-tensioning them.
03. Applying skid-resistant or protective coatings to hardened concrete, bituminous concrete or metals.
04. Preparing epoxy resins mortar or concrete for repairing spalls and other defects like cracks in concrete or defects in metals.
Application Procedure
The following procedure is recommended for its application:
01. Prepare only that amount which can be used within the pot life (the time taken from initial mixing of the resin and the curing agent to the point when the viscosity of the mixture becomes so high as to render the mix unsuitable for application is called pot life) of the product at the existing temperature.
02. The components should be thoroughly mixed by hand stirring or with a mechanical mixer.
03. Bonding agent should be applied by brush or roller to at least 0.25 mm film thickness.
04. Plastic concrete or mortar should be applied to the epoxy film while it is still tacky. Once the film has cured, plastic concrete will not adhere.
Depending on the temperature conditions, it is generally recommended that the epoxy resin bonding agent be applied just well enough in advance of placing the concrete so as to remain tacky.
Classification of Epoxy Resins
According to ‘ASTM’ (American Society for Testing and Materials), the epoxy-resin bonding systems are classified based on specific aspects i.e. type, grade, class, and color.
- The bonding systems can be classified as Type I, Type II, Type III, Type IV, Type V, Type VI, and Type VII as per their physical requirements.
- According to their flow viscosity and characteristics, the bonding systems can be classified as Grade 1, Grade 2, and Grade 3.
- Also, in accordance with the range of temperatures for which they are suitable, epoxy resin can be designated as Class A, Class B, Class C, Class D, Class E, and Class F.
- Classes A, B, and C are defined for Types I through V, and Classes D, E, and F are defined for Types VI and VII.
According to ‘Raymond J. Schutz’ (Published in: Protex Technical Bulletin), classification of epoxy resin as a bonding agent is as follows:
Based on Type
Type I: This type of epoxy resin is mostly used for bonding fresh concrete and other materials to the old hardened concrete.
We have written the article on how to check the compressive strength of hardened concrete. Have a look at that. Hardened Concrete Core Test for Compressive Strength
Type II: This type is commonly used for bonding of freshly mixed concrete to the cured concrete.
Type III: This type of epoxy resin is commonly used for the bonding of skid-resistant materials to the cured concrete. They can also be used as a binder in epoxy mortars and concrete.
Type IV: These types of epoxy resins are used in load bearing applications for bonding hardened concrete to hardened concrete and other materials and additionally as a binder for epoxy mortars and concrete.
Type V: They are used in load bearing applications for bonding freshly mixed concrete to hardened concrete.
Type VI: These types of epoxy resins are used for bonding and sealing segmental precast elements with internal tendons and for span-by-span erection when temporary post tensioning is applied.
Type VII: These are used as a non-stress carrying sealer for segmental precast elements when temporary post tensioning is not applied as in span-by-span erection.
Based on Grade
Classification of epoxy resins based on grade is generally defined by its flow characteristics, that is its viscosity. The classification is as follows:
Grade I: This type mostly consists of materials having low viscosity that is suitable for injection into the cracks as well as where the flow is required.
Grade II: This type consists of materials having medium viscosity that can be used for general purposes.
Grade III: This type of epoxy resin comprises materials that are of a non-sagging consistency.
Based on Class
Classification of epoxy resins based on class is generally achieved based on the test temperatures at which the gel times are determined. Gel time is nothing but the time interval between the beginning of mixing an epoxy system and the first formation of a gelatinous mass within that epoxy system. The classification is as follows:
Class A: Under this type, the epoxy systems for use should be below the temperature range of 5°Celsius.
Class B: Under this type, the epoxy systems for use should be in the range of 5°Celsius to 15°Celsius temperature.
Class C: Under this type, the epoxy systems for use should be above the temperature range of 15°Celsius.
It is very essential to play safe while working with concrete bonding agents. Following are tips you need to follow:
Safety Tips while Working with Concrete Bonding Agent
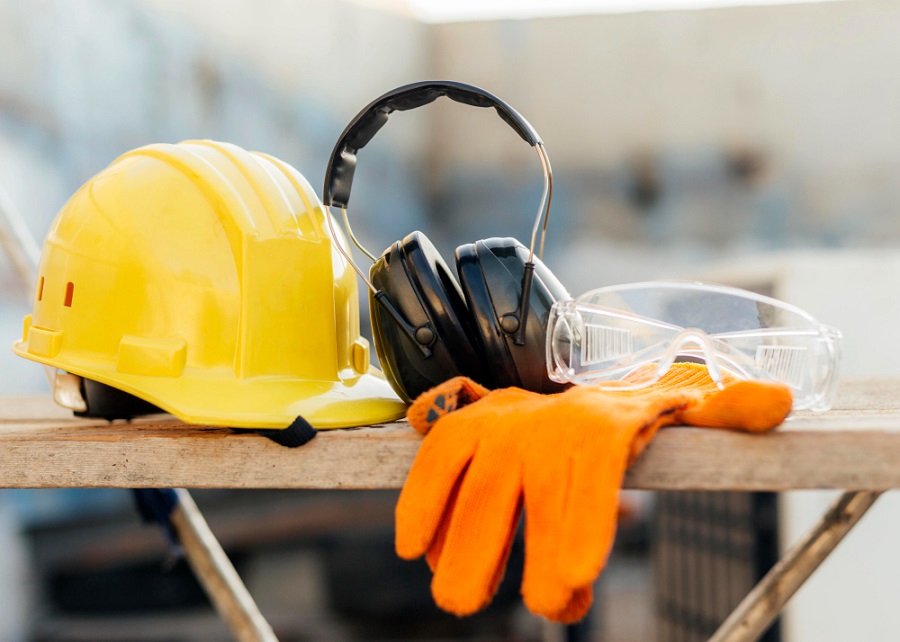
01. Wear safety shoes, hand gloves and safety goggles while using and handling the product.
02. In case the area near mouth or eyes is affected, wash with plenty of clean water and take medical treatment immediately.
Conclusion
“How to bond a new concrete to an earlier one?” The question is easily asked than done!! It is very well known that since the cement within the concrete does not contain any natural bonding agents, the fresh layer of concrete does not stick to the existing concrete surface. In such case, the new concrete surface will settle on it as a separate layer resulting in a weaker concrete surface or section. Here’s where the bonding agent has a role to play. The bonding agent needs to be applied on the existing concrete surface to ensure appropriate adhesion between the successive layers of concrete for its defect-free, uniform behavior under the loads.
This article deals with every aspect pertaining to bonding agents for concrete including its type, grade, class, colors, various processes, precautions, safety tips etc. Yet, while it comprehends a lot, it must be understood that there exists a lot many possible ways to bond concrete layers and a host of potential variables certainly needs to be taken into consideration while making of the soundest technical decision.
Image Courtesy: Image 4, Image 5, Image 6
Author Bio
Arfa Falak – My name is Arfa Falak and I have my graduation in BE (civil). I live in Bangalore. I am an aspiring design Engineer.