Ever since my school days, the conservation of environment has been my concern. But as a young school girl witnessing, mountains of fly ash near power stations left me in worry as it would spread due to wind and pollute the farms and fruit yards in the vicinity. Now as a professional civil engineer, when I see fly ash being used for making of concrete and bricks, I feel happy and relieved.
Let’s take a look, what is fly ash, how can fly ash affects the environment as well as the technology. In this article, we have discussed, history of fly ash, its uses, pros-cons, properties, classification etc. for the concrete.
Fly Ash/ Pulverized Fuel Ash
Fly ash is one of the best pozzolanic admixtures. Pozzolanic admixtures or mineral admixtures are those materials which in itself do not possess any cementitious qualities but show cementitious properties in their finely divided form when combined with lime, i.e. Calcium Hydroxide (Ca (OH)2) in the presence of moisture. They chemically react with Calcium Hydroxide at room temperature to form cementitious compounds.
Fly ash, also known as pulverized fuel ash, is one such artificial pozzolanic material. Fly ash is finely divided amorphous alumino-silicate powder, which is produced in powdered coal burning power plants. It possesses almost little or no cementitious properties but becomes reactive in presence of lime. Fly ash produces gel (calcium-silicate hydrates (C-S-H)), which makes fly ash concrete dense, provides strength and reduces the permeability. Thus, it enhances the durability properties of concrete.
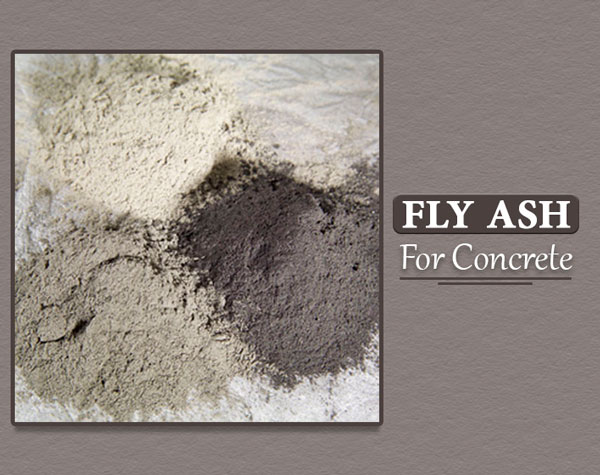
Fly Ash
According to ‘Malhotra V.M. and Ramezanianpour’ (Fly Aash in Concrete, Second Edition), fly ash is one of the residues generated during combustion of pulverized coal in thermal power plant and comprises of the fine particles that rise with the gases. Fly ash mainly contains silica (SiO2), calcium oxide (CaO), alumina oxide (Al2O3) and ferric oxide (Fe2O3). Its components vary depending upon the type of coal burnt. Fly ash is produced by rapid cooling and solidification of molten ash; hence a large portion of fly ash particles are in the amorphous state. Fly ash particles are generally spherical with diameter ranging from less than 1 µm to 150 µm while the particles of cement are smaller than 45 µm. The spherical form and size of the particle increases the flowability and reduces the water demand in concrete mix.
How can Fly Ash Affect Environment as Well as Technology?
According to ‘Raj Premani’ (2017) (Published in: Fly Ash-A Boon for Concrete), India alone produces more than 100 million tons of fly ash every year. Fly ash creates a bad impact on the environment and human health. Its disposal is a big concern. Few Years ago, fly ash was normally released into the atmosphere causing air pollution. Nowadays the fly ash is collected in pollution control equipment like electrostatic precipitator before the gases are released into the air, thereby reducing air pollution.
On the other side, fly ash is more effective in making concrete. Hence, the use of Pulverized fuel ash in concrete is attracting serious considerations of concrete technologists and government departments all over the world.
History of Fly Ash
Since many years, fly ash is being used in the concrete. According to ‘M.S. Shetty’ (Author of Concrete Technology Theory and Practice), that the first large scale use of fly ash was in the construction of Hungry Horse dam and later, Canyon Ferry dam in United States of America. The amount of fly ash used was about 30% by weight of cement. In India, earliest use of fly ash was in the construction of Rihand dam and its quantity was 15% by weight of the cement used.
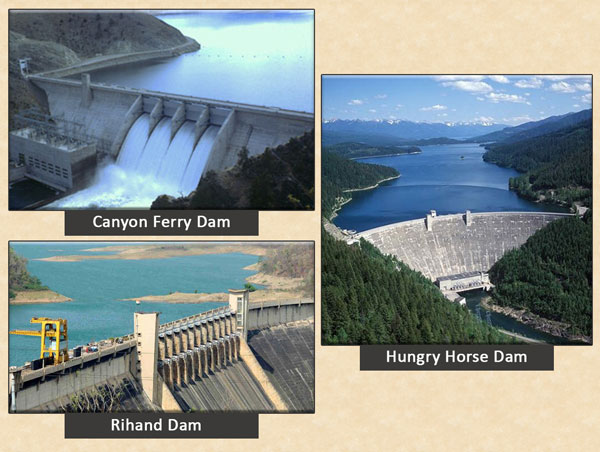
Use of Fly Ash in the Various Dam
Uses of Fly Ash
Fly ash is preferred for a wide variety of applications and it is used in:
- Manufacturing of Portland Pozzolana Cement. As per the ‘IS 1489 (Part 1): 1991’ (Portland-Pozzolana Cement Specification), the fly ash ingredient should be 10- 25 % by mass of Portland Pozzolana Cement.
- In mass concreting, such as dams, retaining walls, pavements etc.
- Manufacturing of bricks, blocks, asbestos sheets, asbestos pressure pipes etc.
- Flowable fill in embankments, approaches of flyover, bridges etc.
- Manufacturing of high-performance concrete.
- in cold weather concreting.
- Manufacturing of High Volume Fly Ash Concrete (HVFAC) which comprises of more than 40- 50% of fly ash content by mass of the total cementitious materials. It is generally used for making roads and pavements.
- In the preparation of Geopolymer concrete.
Geopolymer Concrete: Geopolymer concrete is an alternative to Portland cement concrete. It reduces the use of ordinary Portland cement responsible for high CO2 emission. it is prepared by the utilization of waste materials like fly ash and ground granulated blast furnace slag (GGBS) etc. Thus, it is innovative and eco-friendly.
Advantages of Fly Ash
- It is cost-effective substitute for Portland cement.
- Fly ash is a by-product or a waste product hence use of fly ash concrete reduces CO2 and is thus is environmentally friendly.
- It has good cold weather resistance.
- It is a non-shrink material.
- Pulverized fuel ash also produces dense concrete/brick with smooth surface and sharp detail.
- Fly ash concrete has great workability as well and allows for a lower water-cement ratiofor similar slumps compared to the ordinary concrete. According to ‘Davis et al.’ (1937), fly ash is different from other pozzolanic materials which usually increase the water requirement of concrete mix.
- It reduces the problems of cracks, permeability, bleeding etc.
- It also reduces the heat of hydration.
Disadvantages of Fly Ash
- Pulverized fuel ash may affect the colour of concrete. According to ‘A.M. Neville’ (Author of Properties of Concrete), colour of fly ash concrete to its carbon content. Usually ugly looking darker colour helps in identifying fly ash concrete with compared to lighter colour ordinary concrete, when two are placed side by side.
- Use of fly ash leads to slower strength gain.
- Class C fly ash is sensitive to temperature, hence in the mass concreting or when temperature rises to about 200℃ or 400℉, it does not give high strength.
- Use of Pulverized fuel ash reduces the water demand; therefore, the use of plasticizers/superplasticizers or air entraining admixtures becomes necessary to obtain good workability of fly ash concrete.
Physical and Chemical Properties of Fly Ash
Physical Properties
- Colour: Fly ash colour depends upon its constituent elements. In the fly ash, lime content imparts tan and light colours, iron content provides brownish colour and carbon & typically elevated un-burnt content attributes a dark grey to black colour.
- Specific Gravity: 90 to 2.96
- Specific Surface Area: 250 to 600 m2/kg while the specific surface area of cement is 225 m2/kg
Chemical Properties
As per the ‘ASTM C618-08a’ (American Society for Testing and Material), the chemical properties of Pulverised fuel ash are as follows:
70% silica, alumina, ferric oxide,
5% max.- SO3,
Max. loss on ignition- 12%,
How Fly Ash is Added in the Concrete?
There are two ways in which the fly ash can be used.
- Intergrind certain percentage of fly ash with cement clinker in the factory to produce Portland pozzolana cement (PPC)
- Use fly ash as an admixture at the time of making concrete at the site of work.
The addition of fly ash in both the ways are beneficial but the second method gives the freedom and flexibility to the engineer/user for changing the variation of percentage addition of fly ash.
According to ‘National Precast Concrete Association’ (Published in: Using Fly Ash in Concrete), for the normal concrete work,15 -35% of fly ash by weight of cement and for the mass concreting work like dams, retaining walls etc. up to 70% of fly ash by weight of cement can be added.
Classification of Fly Ash
There are two types of fly ash as per ‘ASTM C618-08a’ (American Society for Testing and Material), based on type of coal from which the ash originates.
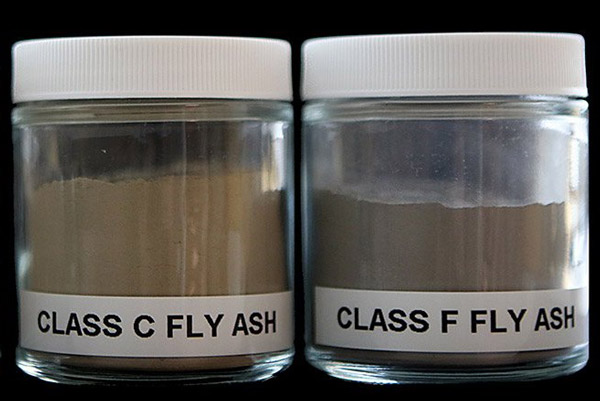
Class C Fly Ash & Class F Fly Ash
01. Class C Fly Ash
This type of fly ash is derived from sub-bituminous coal and lignite. Class C fly ash have a high percentage of calcium oxide a (more than 10%), about 35% silica and much lower carbon content less than 2%) than Portland cement. In addition to pozzolanic properties, Class C fly ash contains cementitious properties; hence it does not require an activator. It is resistant to expansion from chemical attack. Class C fly ash most commonly used for structural concrete, PCC pavements and also as a prime material in tiles, paving or bricks, blocks etc.
02. Class F Fly Ash
Derived from bituminous coal, Class F fly ash is more common than class C fly ash. It is generally low-calcium fly ash with carbon contents less than 5% but sometimes as high as 10%. Class F fly ash contains pozzolanic properties only, therefore, it requires a cementing agent such as Portland cement, quicklime, or hydrated lime – mixed with water to react and produce cementitious compounds. Class F fly ash particles are covered in a kind of melted glass. Hence, it greatly reduces the risk of expansion due to sulfate attack as may occur in fertilized soil or near coastal areas.
Effect of Fly Ash on the Properties of Concrete
01. Effect of Fly Ash on Fresh Concrete
Use of fly ash in the concrete can reduce,
- The demand for water for desired slump.
- Bleeding
- Drying shrinkage
- Heat of hydration
02. Effect of Fly Ash on Hardened Concrete
- The initial strength of fly ash concrete tends to be lower than the ordinary concrete.
- The pozzolanic reaction makes concrete of dense matrix which results in decrease of water and gas permeability
Finally, the use of fly ash in concrete can modify the properties of concrete in fresh state as well as in hardened state. Apart from it, fly ash uses gives the economic substitute of Portland cement and make concrete economical and it provides the most efficient way for disposal or recycling of byproducts. Hence, fly ash use as the concrete admixture is not only an extended technical advantage to the concrete properties, but it also contributes to the environmental pollution control.