In this era concrete technology has developed in a big way. As you know concrete is the most essential material of construction. The basic components of concrete are cement, sand, aggregates and water. Concrete technology has advanced and several researches are being conducted to modify the properties of concrete. Nowadays, there are various additional materials found by many researches to modify the properties of concrete called concrete admixtures. Different concrete admixtures have different effects on the concrete mix and enhance various properties of the concrete in the different way.
Some of the concrete admixtures also have the cementitious properties and are used as a replacement of Portland cement. Such materials are also known as supplementary cementing materials or mineral admixtures or pozzolanic admixtures. Here, we have discussed one such cementitious material called ground granulated blast furnace slag. GGBS is a mineral admixture / pozzolanic admixture and it is basically a waste product from blast furnaces.
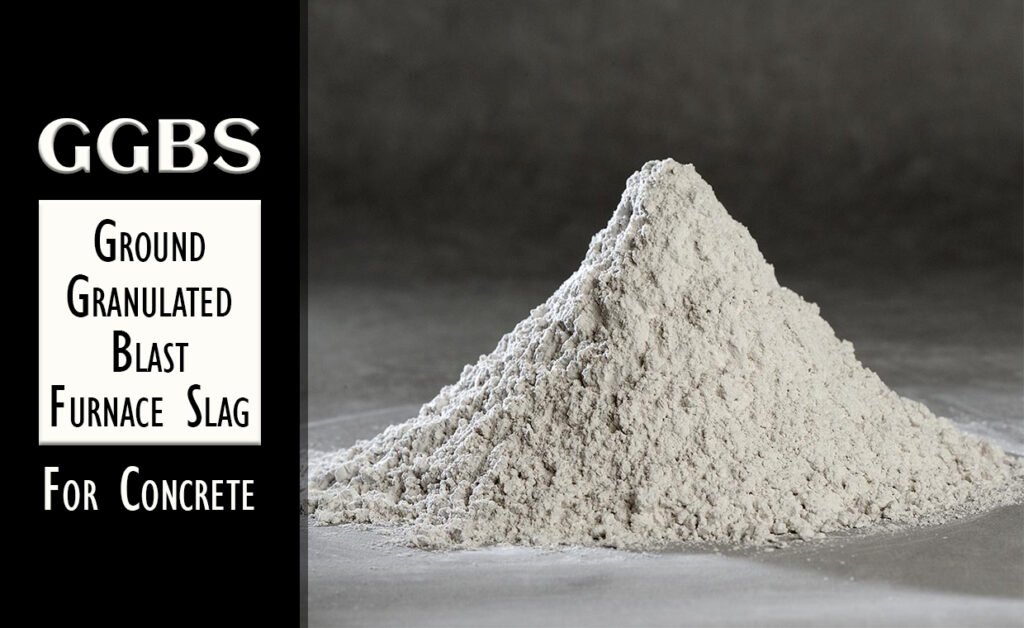
GGBS – Ground Granulated Blast Furnace Slag
Ground granulated blast furnace slag (GGBS) is a non-metallic product obtained as a byproduct from the blast furnaces used to make iron. Ground granulated blast furnace slag consists of silicates and aluminates of calcium and other bases. The size of its particles is less than 45 microns and specific surface area is about 400 to 600 m2/kg.
In simple words, ground granulated blast furnace slag is a waste product in the manufacture of pig iron. Approximately 300kg of slag is produced for each tonne of pig iron. Chemically, it’s a mixture of lime, silica and alumina which are also found in most of the cementitious substances. Blast furnace slag varies in composition and physical structure depending on the method of cooling of the slag.
Ground granulated blast furnace slag is usually designated as ‘GGBS’. It can also be referred as ‘GGBFS’ or ‘GGBS cement’ and the concrete which is made using GGBS is called ‘furnace concrete’ or ‘GGBS concrete’.
By-Product During Manufacturing
According to ‘D. Suresh and K. Nagaraju’ (2015) (Published in IOSR Journal of Mechanical and Civil Engineering (IOSR-JMCE)), blast-furnaces operate at temperatures of about 1,500°C and the furnaces are fed with a carefully controlled mixture mainly consisting of iron ore, coke and limestone. The iron ore is reduced to iron and the remaining materials form a slag that floats on top of the iron. This slag is periodically pumped off as a molten ash/liquid.

Manufacturing of GGBS
Granulated blast furnace slag is obtained by the rapid chilling of the molten ash/liquid with the help of water. During this process, the slag gets shattered and transformed into amorphous granules (glass). Granulated slag is then ground to desired fineness for producing ground granulated blast furnace slag.
- Concrete made with GGBS cement sets more slowly as compared to ordinary concrete and its setting time depends on the amount of GGBS in the cementitious material, but it endures to gain strength over a longer period.
- Use of GGBFS produces lower heat of hydration and lower temperature rise.
- It is very easy to avoid cold joints using GGBS.
- Furnace concrete gives better workability and makes placing and compaction easier.
- Use of Ground granulated blast furnace slag reduces the risk of thermal cracking in large pours due to low early age temperature rise,
- Furnace concrete reduces the risk of reinforcement corrosion improved slag cement, such improved slag cement, such improved slag cement, such because of high resistance to chloride ingress,
- It gives high resistance to the attack by sulphates and other chemicals. Furnace concrete thus ensures higher durability of the structure.
- GGBS concrete provides the resistance to internal reaction such as an alkali-aggregate reaction.
- Ground granulated blast furnace slag is not only used in concrete and other applications but is used in in-situ stabilization of soil too.
Disadvantages of GGBS
- Due to the delay in setting time, the use of ground granulated blast furnace slag may affect construction schedules where the quick setting is required and may not be right choice at such places.
- If the replacement of GGBFS with the cement is higher, then the early age strength development is slower
- Use of GGBS is not available or preferable for smaller-scale concrete production as it is generally supplied in bulk, and is economical only if the construction site is near to such sources.
Use of Ground Granulated Blast Furnace Slag:
There are two major uses of Ground granulated blast furnace slag,
- In the production of high quality-improved slag cement, such as Portland Blast furnace cement (PBFC) and high slag blast furnace cement (HSBFC). In such cements GGBS content ranges typically from 30 to 70%.
- In the production of ready-mixed concrete or site-batched durable concrete.

Portland Cement & Slag Cement
- Apart from the above, GGBFS is also preferred in following Furnace concrete is used in warm weather,
- GGBS cement is used in the precast concrete,
- GGBS concrete is used for the high-rise buildings,
- Furnace concrete is also used for marine works such as dams, shore protection construction etc
- In the waste and sewage treatment plants,
- It is used in the cement-based products like tiles, pipes, blocks, etc.]
Chemical and Physical Properties of GGBS
According to ‘Er. Kimmi Garg, Er. Kshipra Kapoor’ (Published in International Journal of Engineering Research and Management (IJERM)), the chemical composition of the slag varies significantly and depends on the composition of the raw materials in the iron production process. The typical chemical compositions of GGBS are as follows:
- Calcium Oxide: 40%
- Silica: 35%
- Alumina: 13%
- Magnesia: 8%
The physical properties of slag vary and depend on the method of cooling the slag. The typical physical properties of GGBS are as follows:
- Colour: Off white
- Specific Gravity: 9
- Bulk Density: 1200 kg/m3
- Specific Surface Area: 400 to 600 m2/kg
Effect of GGBS on the Properties of Concrete
01. Setting Time of Concrete
According to ‘A. M. Neville’ (Author of Properties of Concrete), with the use of GGBFS the setting time will be extended slightly, may be 30 to 60 minutes at normal temperatures. The effect will be more distinct in high levels of GGBS or at the low temperatures.
02. Workability
Concrete containing GGBS, improves the workability of the concrete and provides ease of placing and compaction of concrete, especially when required to pump or where using mechanical vibration.
03. No Early Age Temperature Rise
Replacing Portland cement with GGBS reduces the heat of hydration; hence it reduces the temperature rise in concrete during mixing and helps to avoid early age thermal cracking.
04. Strength
GGBS concrete may have lower strength at early ages but the ultimate strength after 28 days remains the same as the ordinary concrete. When the high amount of GGBS is used in the concrete the temperature is low and the reduction in strength during early age is noticeable. Hence, you cannot remove props early.
05. Permeability and Chemical Stability
The use of GGBFS in the concrete makes microstructure of the concrete matrix denser as compared with the ordinary concrete. This enhances the durability properties like lower permeability and imparts more stability against chemical attacks like chloride attack, sulphate attack, alkali-aggregate reaction etc.
According to ‘J. Daube and R. Bakker’ (1986) (Published in ASTM Special Technical Publication No. 897), when the GGBS content is at least 60% by mass of the cementitious material and the w/c ratio is 0.50, the diffusion coefficient of the concrete exposed to chloride ions is at least 10 times smaller than the concrete in which the cementitious material consists entirely of Portland cement.

Ground Granulated Blast Furnace Slag- GGBS
How to Use GGBS?
01. It can be used together with limestone as a raw material during conventional manufacture of Portland cement in the dry process.
02. According to the ‘‘Suresh and K. Nagaraju’ (2015) (Published in IOSR Journal of Mechanical and Civil Engineering (IOSR-JMCE)), ground granulated blast furnace slag is used in the concrete as a direct replacement of Portland cement by its weight. This replacement level of GGBS varies from 30% to 70% according to the location or purpose of concreting such as ground concreting or underground concreting, in mass concreting and concreting in special concrete structures etc.
- Commonly 40 to 50% is used in most instances.
- For concreting of on the ground concrete structures with high early-age strength is required than the GGBFS replacement ratio would usually be 20 to 30%.
- For concreting of the underground concrete structures where any average strength is required the GGBFS replacement ratio would usually be 30 to 50%.
- For the concreting of mass concrete or concrete structures with strict temperature rise requirement, the replacement ratio would usually be 50 to 65%.
- If concrete for the special concrete structures with higher durability requirement such as corrosion resistance for marine structures, sewage treatment plants , the replacement ratio would usually be 50 to 70%.
Summing up, ground granulated blast furnace slag is a byproduct and waste material hence the use of GGBS helps in achieving the green environment. The most important thing is that use of GGBFS doesn’t degrade the strength of concrete, but increases durability and serviceability of the concrete. Another thing is, you can use GGBS as partial replacement of cement as well as aggregates.