In this era, the construction industry is at its peak and one cannot imagine any construction without concrete. Concrete is the integral part of any construction. Concrete consists of cement, sand, aggregates and admixtures mixed with water. No doubt, concrete is the most important construction material for any structure’s serviceability and durability but it has also a darker side when it comes to environment safety.
Cement Production – Co2 Emission – Supplementary Materials
As we have discussed earlier, concrete is a supreme material for the construction and majorly used worldwide which has resulted in large scale manufacturing of cement. It is proven through various researchers that production of cement produces heavy environmental pollution because of the emission of CO2 gas. This is quite hazardous. Hence it became crucial and essential for the researchers to find a better alternative that can be eco-friendly and reasonable in every way. Hence, they have started working on the economical and eco-friendly substitute of cement which can partially supplement to cement minerals or raw materials without compromising the strength parameter. We can call such kind of material as supplementary cementing materials or a pozzolanic or mineral admixture.
There are various types of materials available like Metakaolin, fly ash, ground granulated blast furnace slag (GGBS), silica fume, rice husk ash, etc. Here we shall discuss about Metakaolin which is such a kind of supplementary cementing material that is used to make a high strength concrete and which simultaneously increases the durability of the concrete.

Metakaolin
Metakaolin is a high-quality pozzolanic material. Metakaolin is one of the most widely used mineral admixtures these days. It helps concrete obtain both higher performance and economy. Unlike others, it is neither the by-product of an industrial process (like GGBS) nor entirely a natural product. It is specially produced from high quality Kaolin. According to the ‘P.Muralinathan, A. Joshua Daniel & S. Sivakamasundari’(Published in International Journal of Pure and Applied Mathematics), Metakaolin is produced by the calcinations of pure or refined kaolinite clay at a temperature between 650℃ to 850℃. Once the burning process gets completed it is properly grinded to achieve desired fineness to improve various strengths and property parameters of cement mortar and concrete. Kaolin clay is the raw material for the Metakaolin. Kaolinite clay is a mineral which is fine and white in colour and it is used in the manufacturing of porcelain. Kaolinite clay is also known as china clay or kaolinclay.

Kaolin Clay
Metakaolin consist of silica and alumina in an active form and as other mineral admixtures, it reacts with the calcium hydroxide at room temperature and form calcium silicate hydrate (C-S-H)-gel which increases the density of concrete and reduces porosity. Thus, it decreases permeability and increase durability of the concrete. Now, when it is used in the concrete, it will act as filler penetrating into the voids (space) between cement particles thereby resulting into a more impermeable concrete.
Commercial Names of Metakaolin
Mentioned below are some commercial names of Metakaolin products which are popular in the market. The names of companies manufacturing them are also mentioned alongside.
01. Sikacrete® M-100 – Sika
02. Snow Cem Meta Kaolin – Kaolin Techniques Private Limited
03. Grade: Kao Cem Metakaolin- Kaomin Industries
04. Metakao- Carbo Industrial Technologies[vc_separator color=”black” border_width=”4″]
Advantages of Metakaolin
Use of Metakaolin gives the following various advantages,
01. Use of Metakaolin in concrete accelerates the initial setting time of concrete.
02. It helps in development of the early age strength of concrete which allows the early removal of formwork and thus enhances the production rate.
03. Metakaolin consumes calcium hydroxide thereby preventing the reaction of alkali-silica. Use of Metakaolin increases the resistance to sulphate attack, chemical attack and freeze and thaw action.
04. It reduces drying shrinkage and efflorescence.
05. It improves water-tightness and impermeability of concrete hence is safe for using in water retaining structure, off-shore structure etc.
06. It can increase the residual strength of refractory concrete after firing.
07. It increases the strength and durability of concrete.
08. It gives good spray-ability.
09. It is a green option, an ecofriendly building material.
10. It is cost effective as compared to its contemporaries.
11. Compared to other mineral admixtures, it is easily and abundantly available in the market.
Thus, if you take into consideration the above-mentioned advantages, you will find that it almost overcomes all the limitations of ordinary concrete and emerges as a better substitute.
Disadvantages of Metakaolin
01. Use of Metakaolin reduces the workability of the concrete due to its fineness; hence it becomes necessary to use water reducers or air entraining admixtures to achieve the desired workability.
02. However, the performance can be enhanced by taking into consideration the following:
- Increased quality control is essential in order to maintain the desired properties. High quality control must be consistent for it to be effective.
- Selection of material is equally important. Better quality may cost more than the lower ones.
Chemical and Physical Properties of Metakaolin
As per the ‘Sanjay N. Patil, Anil K. Gupta & Subhash S. Deshpande’ (Published in IOSR Journal of Mechanical and Civil Engineering (IOSR-JMCE)), followings are the properties of Metakaolin
Chemical properties of Metakaolin are as follows,
- Silica (SiO2): 51-53%
- Al2O3: 42-44%
- CaO: <20%
- Fe2O3: <2.20%
- SO4: <0.5%
- K2O: <40%
- Loss of Ignition: <0.50 %
Physical properties of Metakaolin are as follows,
- Physical Form: Powder
- Colour: Off white, Gray
- Specific Gravity: 2.40 to 2.60
- Fineness: 8000-15000m2/kg.
How can Metakaolin be Added in the Concrete?
Metakaolin can be blended with the ordinary Portland cement and can be used as partial replacement of cement by its weight.
‘M. Narmatha and Dr. T. Felixkala’ (Published in IOSR Journal of Mechanical and Civil Engineering (IOSR-JMCE)) conducted experimental program to investigate the use of Metakaolin as a partial replacement with cement. They casted the specimen with M60 grade of concrete with different replacement levels such as 5%, 10%, 15%, 20% of Metakaolin. And they concluded that 15% cement replacement by Metakaolin is superior to all other mixes.
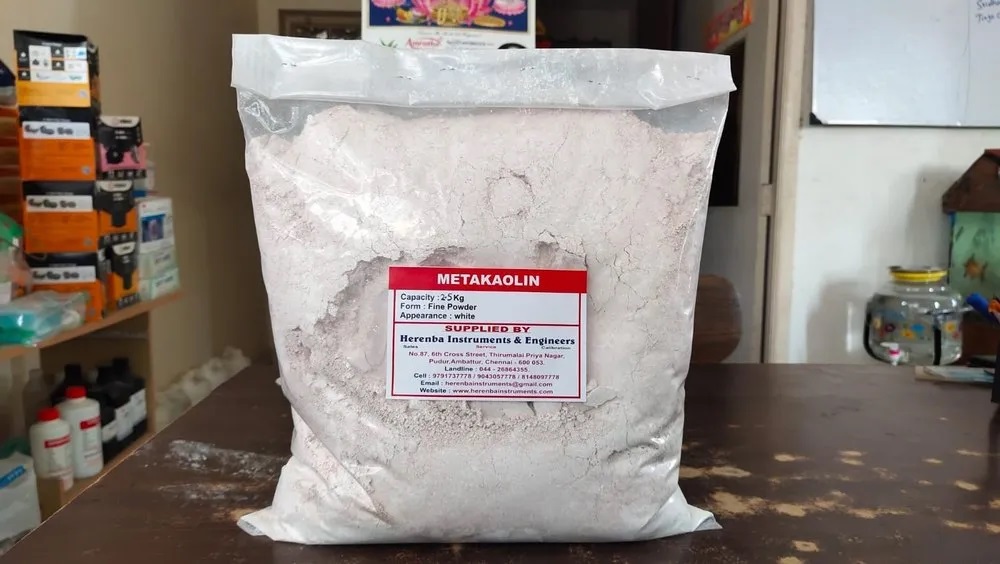
Metakaolin
Effect of Metakaolin on the Properties of Concrete
01. Slump/Workability of Concrete
According to the ‘Sunny A. Jagtap, Mohan N. Shirsath & Sambhaji L. Karpe’(Published in International Research Journal of Engineering and Technology- IRJET), slump of concrete or the workability of the concrete gets significantly reduced with the increased amount of the Metakaolin with the same water-cement ratio because of fineness of Metakaolin. But it can be compensated with the use of water reducing admixtures (plasticizers) or using combination with fly ash in mixes.
02. Strength
Use of Metakaolin in concrete gives the early age strength development because it has good filler effect as well as pozzolanic effect.
03. Permeability
Use of Metakaolin in concrete gives certain densification of the micro structure of the concrete due to the pozzolanic and hydraulic reaction and leads to greater impermeability.
04. Alkali-Silica Resistance
The partial replacement of the Metakaolin has higher resistance against the expansion due to alkali-silica reaction.
05. Chemical Diffusion
Use of Metakaolin in concrete decreases the chloride permeability. The more is the amount of the Metakaolin, less is the permeability. It also gives better resistance against the attack of sulphates and other aggressive substances such as mineral and organic acid.
Use of Metakaolin
01. Metakaolin is used while constructing dams, bridges and water retaining structures, off-shore structure etc.
02. It is also used in high rise buildings to achieve high strength concrete.
03. It is used in the manufacturing of high strength, high performance and lightweight concrete.
04. It is used in mass concreting,
05. It is also used in the construction of:
- Industrial flooring
- Warehouses
- Container Depots
- Roads
- Nuclear power stations etc.
Summing up, Metakaolin is utilized as pozzolanic material for partial cement replacement producing high strength concrete. High strength concrete withstands loads that a normal strength concrete can’t. Metakaolin increases the early age strength development of concrete. It provides long-term durability and increases the serviceability of the concrete. The use of this supplementary cementitious material in concrete can compensate indirect costs arising due to environmental, technical and economic issues caused by cement production.