Many times people fail to differentiate between cement and concrete. People normally use the word “Cement” when they mean “Concrete” in actual. They use the term cement and concrete as an alternative for each other. But in reality, cement and concrete are absolutely two different materials. Let us understand this with the help of a very common example. The relation between cement and concrete is similar to the relation between flour and a cake. Hence, one should know the basic difference between cement and concrete to overcome the misunderstanding. In this article, we have mentioned all the dissimilarities and disparities between cement and concrete. It will help you to identify and understand both the materials.
What is that Material?
Cement
Cement is a basic and core-building material used in the construction. It is a greenish-grey powder made from calcareous material like limestone or chalk and argillaceous material like clay or shale. Cement has an excellent adhesive property; hence it is used as a binding mortar. It is also used extensively in concrete and other construction works. It is thus used as one of the constituents of concrete.
Concrete
Concrete is a finished or derived product made from a heterogeneous mixture of a binder, i.e. cement, chemically inert aggregates (like coarse aggregates, fine aggregates or sand, crushed stone, brick chips, etc.), admixtures and water. It is the most widely used man-made material on the earth. When water is added into the raw materials, a stone-like structure is formed as water activates the cement to get hardened.
Ingredients of the Material
Cement
- Calcareous materials like,
01. Limestone
02. Chalk
- Argillaceous materials like,
01. Clay
02. Shale
Open this link to know various types of cement raw materials used in the cement manufacturing process. This article will comply with your inquisitiveness to understand everything in detail about cement i.e. its ingredients and their functions.
Concrete
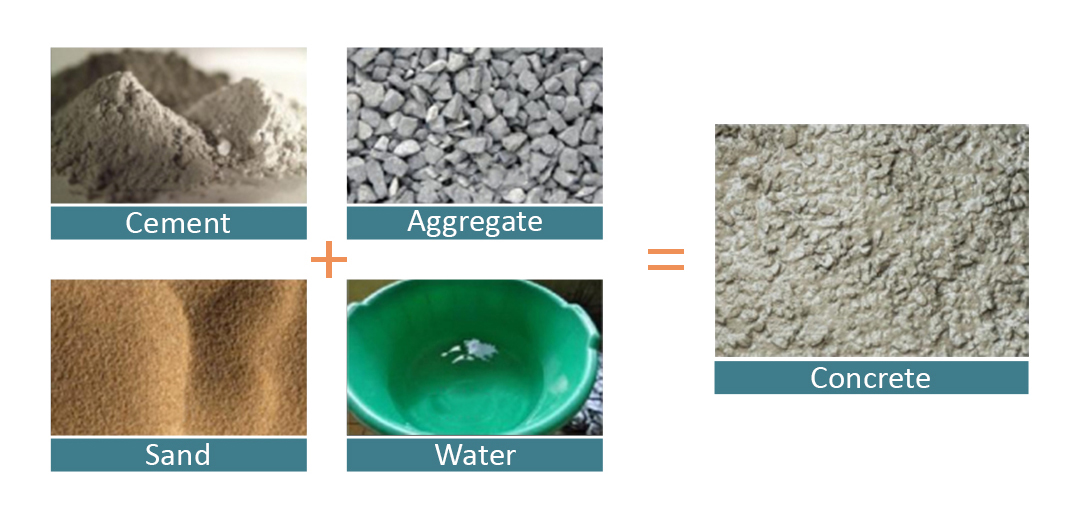
Ingredients of concrete
- Cement,
- Aggregates
01. Coarse aggregates
02. Fine aggregates or sand,
Crushed stones or brick chips also can be used as aggregates.
- Admixtures like Air entraining admixtures, plasticizers, retarders, accelerators,
- Water
Above mentioned ingredients are the most basic raw ingredients for making concrete. Still, other concrete ingredients such as reinforcement, polymers, fibers, Pozzolanic materials like fly ash, GGBS, Silica fume, pigments, recycled concrete aggregates etc. are also used as they help in modifying the properties of the fresh concrete as well as the hardened concrete.
How is this Material Made?
Cement
The cement manufacturing process consists of grinding the raw material and then burning it into a kiln at around 1400 °C. The raw material thus gets converted into clinker form.
After that, the clinker is cooled and ground to a fine powder thereby adding 3% to 5% of gypsum into it. This process is either a wet process or a dry process. If you want to gain additional information about the manufacturing process of cement, then read our articles on wet process and dry process.
Concrete
According to ‘A.M. Neville’[01] (Honorary Member of The American Concrete Institute), the hardened concrete is generally referred as concrete. Therefore, the process of manufacturing concrete refers to producing fresh concrete and placing it in different forms so that it can harden into structural or building material.
The following are the sequences of operations for the manufacturing of concrete.
01. Batching of Concrete
02. Mixing of Concrete
03. Transportation of Concrete
04. Placing of Concrete
05. Compaction of Concrete
06. Curing of Concrete
07. Finishing.
Production of good quality concrete requires thorough care exercised at every stage during the manufacturing process of concrete.
Above mentioned is the stepwise process of manufacturing concrete. In case you want to understand each process in detail, click on each of them to know further.
Uses
Cement
Cement is never used alone. Due to its crucial binding properties, it is used as a chief ingredient for preparing concrete, mortar, blocks, and other building materials in which it holds the other components together.
As we know, it has a unique adhesive property; hence it is used to hold together various construction materials like tiles, bricks, etc. Cement is also used as a sealant and grouting material.
Concrete
Concrete is one such building material which has become an integral part of construction industry. Its unique characteristics such as strength, low-maintenance, energy-efficient, durability, and sustainability make it even more popular. It is due to these properties, concrete is used in the construction industry.
Some of the uses of concrete are mentioned below:
01. It is used in construction of structural elements like footings, foundations, slabs, columns and walls for all types of buildings.
02. Culverts and Sewers
03. Concrete Roads or Driveways
04. Marine Construction
05. Concrete Dams
06. Concrete Bridges
07. etc.
Properties
Cement
Good quality cement gives overall a good resultant concrete or mortar. For that, cement must have following physical and chemical properties.
- Physical Properties of Cement:
01. Fineness
02. Soundness
03. Consistency
04. Strength
05. Setting time
06. Heat of hydration
07. Loss of ignition
08. Bulk density
09. Specific gravity, etc.
- Chemical Compounds of Cement:
01. Tricalcium aluminate
02. Tricalcium silicate
03. Dicalcium silicate
04. Ferrite
05. Magnesia
06. Sulphur trioxide
07. Iron Oxide
08. Alkalis
09. Free Lime
10. Alumina
Our article on Properties of Cement gives you detailed information regarding these properties.
Concrete
As concrete is the most extensively used construction material; it is essential to know about the important properties of concrete for designing a concrete structure. The following are the important properties of concrete.
- Properties of Fresh Concrete
01. Workability
02. Segregation
03. Bleeding
- Properties of Hardened Concrete
01. Compressive Strength
02. Tensile Strength
03. Modulus of Elasticity
04. Poisson Ratio
05. Shrinkage of Concrete
06. Creep in Concrete
07. Durability
08. Porosity
09. Density
10. Fire Resistance
11. Thermal and Acoustic Insulation Properties
Basics
Cement
- Cement consists of 10 to 15% of the total mass of concrete, but the precise proportion of cement varies from mixture to mixture. It also depends upon the type of concrete being made.
- In the ancient era, volcanic ash or tuff and lime was used as a binder in construction.
- Portland cement is not a brand name, but it is a general term for the most common cement type. As per ‘M. S. Shetty’[02] (Author of Concrete Technology), Joseph Aspdin founded the patent for Portland cement on 21st October 1824.
- Portland cement is a type of hydraulic cement; hence the hydration process starts after the water is added in it. The hydration process is most important for its strength gain.
- When cement comes in contact with water, chemical reaction called hydration takes place which causes the cement to set and harden so that it holds the aggregates and other materials together in a concrete mixture.
- Cement is an expensive building material hence; its solo usage can prove costly. Moreover, it is also prone to cracking.
Concrete
- In the fresh concrete, aggregates contribution is 60%-75%, cement is around 10%-15 %, and water is up to 15%-20%. But the exact proportion of all the ingredients varies according to the type of concrete being made.
- In the ancient era, the Greeks and Romans were the first to use such kind of material or mortar. The material was made up of volcanic ash or tuff, lime, and sand, which acquired superior strength and better durability in both fresh as well as saltwater.
- In the production of concrete, the water-cement ratio plays an important role as it influences the various properties of concrete like strength, workability, durability, porosity, etc. Hence, meticulous care must be taken while choosing it. If you want to know more about the w/c ratio and its effect on concrete, click the link to know more: Importance of Water-Cement Ratio in Concrete.
- There is a myth that higher-grade concrete needs more cement. But the fact is not so. Remember, as per Indian standards, cement content not including fly ash and ground granulated blast furnace slag in excess of 450 kg/m3 should not be used unless special consideration is there.
- Concrete can be moulded in any shape, but only when it is in plastic state. Later it gets hardened and stronger. In such state, concrete cannot be moulded. This hardening process of concrete continues for more than a year.
- Our mentor ‘Shree Mahadev Desai‘(CMD of Sthapati Designers & Consultant PVT LTD, the leading multidisciplinary consultancy organization of India since 40 Year), shares a vast and massive work experience in this industry. He holds expertise and has attained an authoritative proficiency in the construction industry over these years. Mr. Desai advices us to avoid using hand-mixed concrete for important structural elements like columns, shear walls etc., as the use of hand-mixed concrete is very risky for such important structural elements.
Grade
Cement
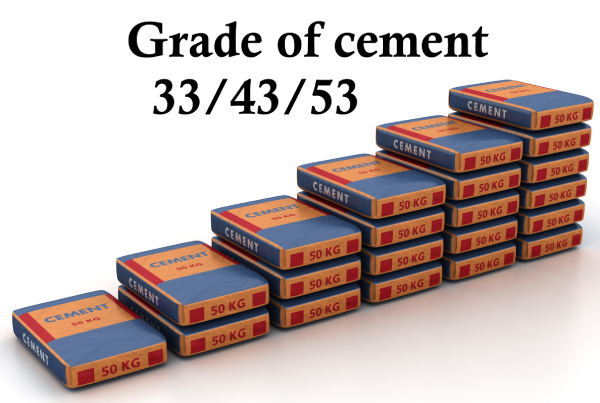
Nowadays, the following three grades of cement are available in the market.
01. 33 Grade
02. 43 Grade
03. 53 Grade
However the 33 and 43 grade of cement are not available freely. The grade of cement generally differs in terms of cement strength. Because the values of 33/43/53 specify the compressive strength of cement cube in N/mm2 (Mpa) after 28 days of curing, where cement mould size is 7.06 cm*7.06 cm*7.06 cm.
Concrete
The different grades of concrete are given below:
01. M5
02. M7.5
03. M10
04. M15
05. M20
06. M25
07. M30
08. M35
09. M40 etc.
Here, M denotes the mix and values like 5, 7.5, 10, 20, etc. denote the compressive strength of concrete cube after 28 days of curing in N/mm2 (Mpa).
As per the ‘Indian Standard- IS 456:2000’, grade M5 to M20 are the nominal mix concrete because its proportions are specified in the code, and those above M20, are the design mix concrete.
Read the following link to know the difference between Nominal Mix Concrete and Design Mix Concrete.
Types
Cement
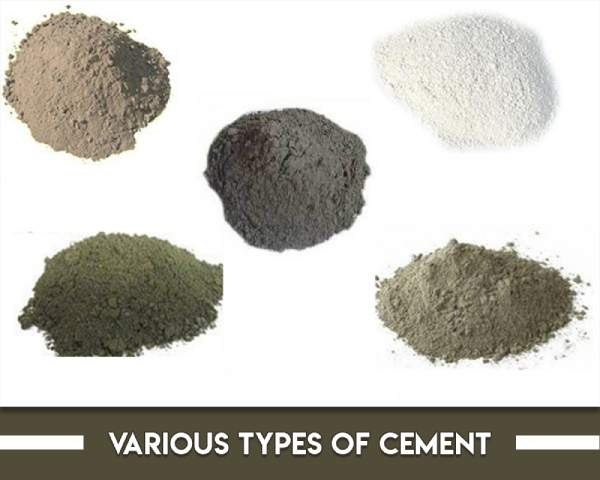
The cement types and quality have also developed and evolved with the development of manufacturing technology. The reason is, every special construction project requires something different than OPC (ordinary Portland cement). Different types of cement with different physical and chemical properties for various construction projects are available.
The following are 16 types of cement available which are used in construction.
01. Ordinary Portland Cement (OPC)
02. Portland Pozzolana Cement (PPC)
03. Rapid Hardening Cement
04. Extra Rapid Hardening Cement
05. Quick Setting Cement
06. Low Heat Cement
07. Sulphate-Resisting Cement
08. Portland Slag Cement
09. High-Alumina Cement
10. White Cement
11. Coloured Cement
12. Air Entraining Cement
13. Hydrophobic Cement
14. Masonry Cement
15. Expansive Cement
16. Oil Well Cement
Each type of cement differs from the other depending upon its properties, its uses and composition materials used in the manufacturing process.
15+ Types of Cement Used in Modern Construction gives you a detailed look at all the cement types mentioned above.
Concrete
The application of concrete is very vast. Thus, the need arises for concrete types to meet the demand for various challenges.
An example is Ready Mix Concrete (RMC). The name itself suggests that it is a ‘ready to use’ concrete on site. Hence, it is a great option to overcome the limitation of ordinary mixtures as it reduces the work on the construction site and avoids any sort of confusion taking place. It also helps in overcoming limitation particularly with reference to quality, especially when you are dealing with unskilled labour.
The following are the different types of concrete used in the field of civil engineering.
01. Plain Cement Concrete or Ordinary Concrete
02. Reinforced Concrete
03. Lightweight Concrete
04. Ready Mix Concrete
05. Polymer Concrete
06. Pervious Concrete
07. Transparent Concrete
08. Fiber Reinforced Concrete.
09. Precast Concrete
10. Self-Compacting Concrete
11. Bio Concrete or Self-Healing Concrete
12. Green Concrete
13. Plum Concrete
14. Ferro Cement Concrete
15. Fly Ash Concrete.
16. Pre-stressed Concrete
17. High-Density Concrete
18. High-Strength Concrete
19. Air Entrained Concrete
20. Shotcrete Concrete
21. Vacuum Concrete
22. Pumped Concrete
23. Stamped Concrete
24. Limecrete
25. Roller Compacted Concrete
26. Glass Concrete
27. Pre-packed Concrete etc.
Conclusion
To conclude this article – Both cement and concrete are different materials. The perceived difference between concrete and cement is the case of mistaken identities. Cement is one of the components of concrete, whereas concrete is the resultant product of mix of the cement, aggregates, admixtures, and water which hardens like a rock.
Cement is in powder form, whereas concrete is a dry mix which later becomes a semi-liquid flexible material which is able to form any shape or mould and ends up finally into a stone-like hard material. The properties of cement and concrete are also altogether different. You cannot cast slab, wall, or column with cement, but you can do it with concrete. The concrete has high strength, durability, low maintenance, excellent waterproofing properties, long service life, high thermal efficiency, etc.
We hope this article proves to be of help to our readers in clearing all their doubts regarding cement and concrete, their properties, composition, types and uses.