If you travel in Mumbai or any other city in the vicinity of the sea, you will find that most of the RCC buildings built even 20-40 years ago are undergoing major structural repairs. Every building practically has a signboard showing that repairing work is in progress. As per the common man’s perspective, the life of a building is around 100 years then why the majority of Reinforced Concrete buildings are in a dire state. The reasons are not difficult to find out. The majors are:
- In the old days, the minimum grade of concrete allowed was M-15, which is not durable at all. Hence it is now revised to M-20.
- The cover to the reinforcement bars is not adequate. In most of the old buildings codal provision as far as covers are concerned were never followed strictly.
- The compaction must have been poor giving rise to porous concrete.
- The steel of poor quality or steel with higher carbon content.
As per one of the structural auditors on the panel of Mumbai Municipal Corporation stated; our company has observed that inadequate cover is a major cause of the corrosion, which has invited major repairs in RCC buildings, way before the end of the service life of the buildings. Usually cover does not involve any big cost, however, it is a classic example; as to, how the negligence can cost you a big fortune, sometimes, even the life of the building.
Concrete is a versatile material for modern construction which is prepared by mixing well-proportioned quantities of cement (even lime in some cases), crushed rock or gravel, sand and water. RCC is the concrete that comprise of steel bars, called reinforcements bars, or rebars. This combination of concrete and steel works very well, as concrete is strong in compression, easy to produce at site, and economical. Moreover, steel has a better capacity to resist the tension. This works as a great combination!
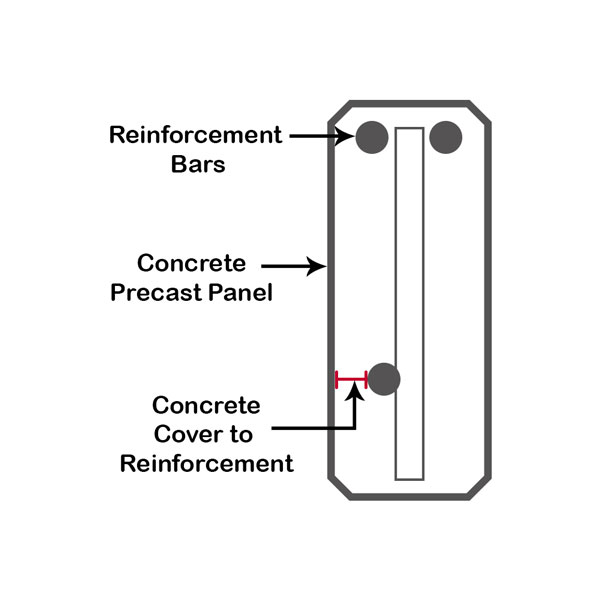
What is Concrete Cover?
According to a ‘Neville’ (Author of Concrete Technology) concrete cover to reinforcement is the shortest distance between the surface of a concrete member and the nearest surface of the reinforcing steel. In other words, the distance between the surface of implanted reinforcement and the exterior face of concrete of a RCC member is the concrete cover. It means that concrete cover to reinforced concrete member is the minimum thickness of concrete provided over the reinforcement steel measured from the exposed concrete surface to the closest reinforced steel surface.
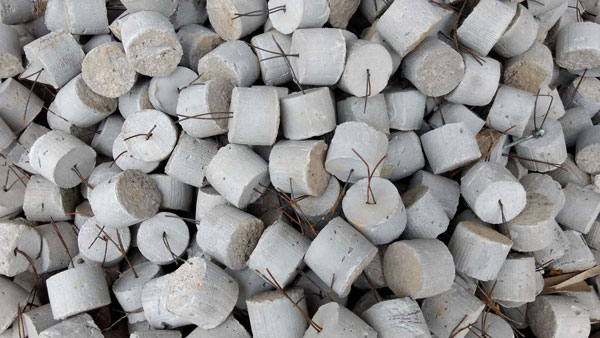
Concrete is required to cover and protect reinforcement steel within its body. The concrete cover is often subjected to impact, wear and ingress of moisture along with other chemicals. It has to also withstand against the bad effects of weather. The cover therefore should be dense, wear resistant, strong, and having low permeability. Concrete in the cover region plays a very important role in toughness and durability of the structure. The role of concrete in the cover region can be more or less similar to that of the role of human skin that plays a vital role in protecting the flesh and other parts of our body.
Why We Provide Concrete Cover?
According to ‘N. Subramanian and K. Geetha’ (1997) (Published in Indian Concrete Journal), for durable concrete structures, it is crucial that the steel embedded in concrete is protected adequately against corrosion. It is also essential that concrete should be dense, impenetrable, and uniform and free from deleterious components. For this, adequate cover to the steel should be provided on all faces of the concrete element.
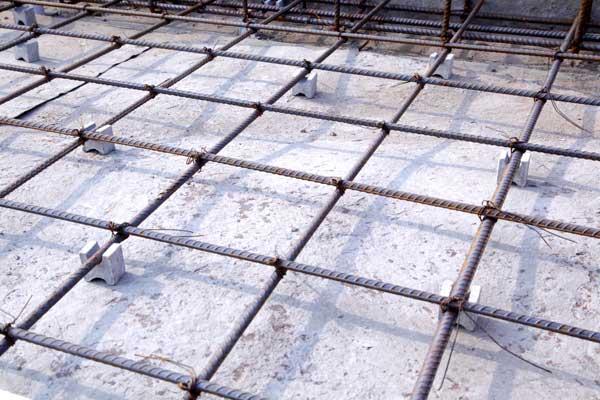
Concrete covering is provided to prevent corrosion of reinforcement bar in RCC. Reinforcement is prone to fire and corrosion due to atmospheric conditions. Hence, a proper covering is necessary in order to overcome such problems. In case of failing to provide a proper cover, there are acute chances of corrosion and crack development in the hardened RCC. Cover is provided to increase the structural integrity and coherence of the concrete in cover region.
Concrete covering is provided in every element of the building (Slabs, Beams, Columns Footings) wherever the reinforcement is used. In order to maintain the proper arrangement of reinforcement and to provide a cover to reinforcement, cover blocks are used.
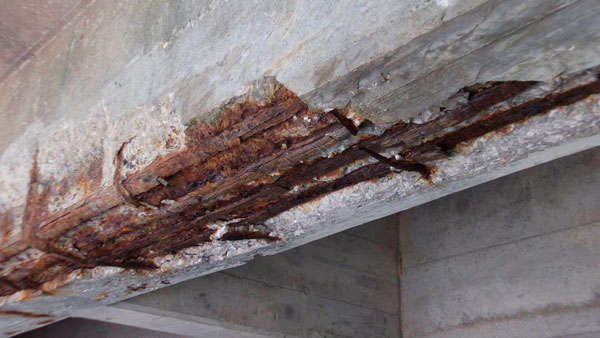
Requirements of Concrete Cover
To achieve good durability, it is utmost important to have the following requirements for concrete in the cover region.
- The concrete should be free from macro defects like honeycombs, entrapped air, cracks, voids, broken edges etc.
- The concrete should be strong and durable (low water to cement ratio)
- Concrete should be dense and free from micro defects.
- Concrete should be wear-resistant.
Need for Concrete Cover
Concrete in the cover region protects steel reinforcement in two ways.
- By providing a dense, strong and impermeable barrier against ingress of moisture, oxygen, chlorides, sulphates, carbon dioxide and other aggressive gases and chemicals.
- By providing a passive protective coating on steel surface. Due to alkaline nature of concrete this coating prevents corrosion of steel.
This protection remains effective as long as concrete is strongly alkaline in the cover region. This protection remains for a longer duration for concrete of high strengths and low water to cement ratios. Here, it is important to remember that concrete’s pH is 12 to 13. Now, this is because that the process of carbonation takes place where gradually it loses its alkalinity resulting into corrosion.
Construction Practice in Cover Region
Poor construction practices, methods, and supervision are largely responsible for poor quality of concrete cover resulting in loss of durability of the reinforced concrete structure, predominantly due to corrosion.
The following factors are responsible for poor cover.
- Improper selection of concrete materials, high water-cement ratio (w/c) and low concrete grade without giving consideration to the environment or climatic conditions in which concrete structure is to be raised.
- Improper batching of concrete, as well as the mixing of concrete causes lack of cohesiveness of the mix and resultant segregation, causes honeycombing and voids in concrete, especially in the cover region.
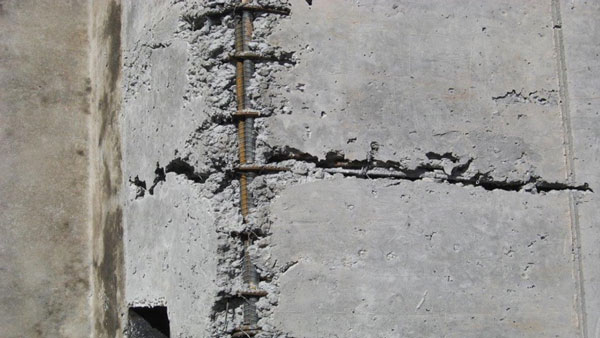
- Improper transportation and placement can also cause segregation of the concrete mix resulting in honeycombing and voids.
- Improper compaction of concrete leaves entrapped air voids. This results in porosity in concrete which becomes easily accessible to the moisture and chemicals. This can later react with steel or even concrete itself.
- Improper curing results mainly in drying and plastic shrinkage cracks on the concrete surface thereby allowing moisture and chemicals to easily enter through these cracks and attack steel and/or concrete.
- Defective planning, placing, bending and tying reinforcement steel often results in reduction in concrete thickness in the cover region thereby facilitating the passage of moisture and other chemicals to attack steel.
- Displacement of reinforcement steel during concrete placing operations results in considerable reduction of concrete thickness in the cover region.
- Inadequately made cover blocks used to maintain concrete cover are often so weak that they break during concreting operations resulting in reduction of cover. Sometimes the concrete cover blocks are made manually without proper proportioning, batching, mixing, compacting and curing. This results in cover blocks having high porosity and low strength. Instead of safe guarding the steel, they become a passage for moisture and chemicals to enter and cause corrosion thereby giving rise to durability problem.
- At many construction sites, stone chips are used to support steel reinforcement. These stone chips often get dislodged during concreting operations resulting in reinforcement steel resting directly on shuttering leaving little or no cover to the bars. Mosaic tiles or blue metal jali are also used as cover devices. But these are not recommended as their quality, strength and other properties can seriously cause porosity problems for concrete in the cover region.
- In doubly reinforced RC slabs, adequate spaced chairs should be provided so that adequate spacing between the top and bottom reinforcement is maintained during the concreting operations. Often chairs are not provided or the spacing between them is not adequate. This results in bars getting bent or distorted due to movement of work force during concreting. This also results in reduced strength of concrete element and can further result in reducing thickness of the cover.
Carbonation of Concrete Cover
Carbon dioxide, along with moisture and oxygen in the atmosphere forms carbonic acid which attacks the concrete surface and causes carbonation thus, resulting in drop in alkalinity of concrete at the surface. This carbonation process continues further and penetrates into the concrete. The depth of penetration of carbonated concrete mainly depends on the grade (strength) of concrete. Once this depth of carbonation goes beyond the concrete cover, the protection offered by concrete to reinforcement steel considerably reduces resulting in commencement of corrosion.
According to a ‘Neville’ (Author of Concrete Technology), Carbonation is progressive from the outer surface of the concrete. The progress is more rapid if the penetrability of the concrete is more. This process effectively decreases the protective cover. Hence, there arises the need for adequate cover.
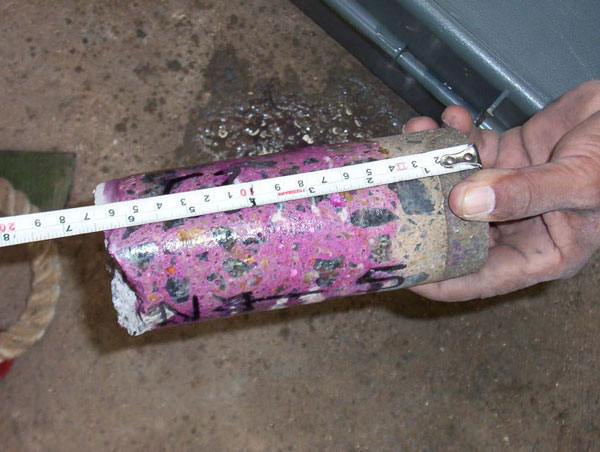
Factors Related to Minimum Cover Thickness
Before going into the various codal specifications for minimum cover, it is essential to note various factors which influence the specification of minimum cover. These factors are as follows:
- Exposure conditions (location of the structural member and presence of aggressive chemicals where the structure is proposed)
- Concrete grade (strength) specified or maximum w/c ratio specified. (Concrete with lower w/c ratio has less micro porosity hence cover can be reduced).
- Maximum aggregate size used in concrete manufacture (Concrete cover required will be more if higher maximum aggregate size is used).
- Diameter and spacing between reinforcement steel.
- Likely exposure to fire (Thicker cover gives better fire-resistance).
Covering for reinforcement in concrete is very important. The thickness of cover depends on type of structural member and environmental conditions. For the surfaces exposed to the harmful chemicals, acid, alkali, saline atmosphere, Sulphur, smoke etc.; the thickness of the cover needs to be increased. The correct cover shall be maintained by cement mortar cubes (blocks) or by other approved means. If the cover block is of cement/mortar, its strength should be same as that of basic concrete.
Minimum Thickness of Cover as per Codal Specification
Here, we have given minimum thickness of cover as per different codes.
01. Cover as Per Indian Standards
The existing code which specifies concrete cover requirements is IS:456-2000. The requirements are mentioned below in the table
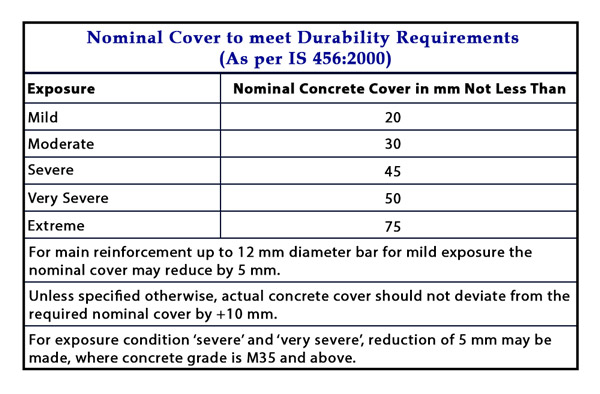
It is obvious from the table that the IS code does not take into account concrete quality. (Strength and/or water cement ratio)
02. Cover as Per American Concrete Institute
The requirement of cover as per ACI – 95 are given in table below. However, it is clear that the amount of concrete protection has to be suitably improved in corrosive or other severe environment while using this table.
The requirements for minimum concrete cover for reinforcement as per manual of concrete practice 1998 of American Concrete Institute given in table below.
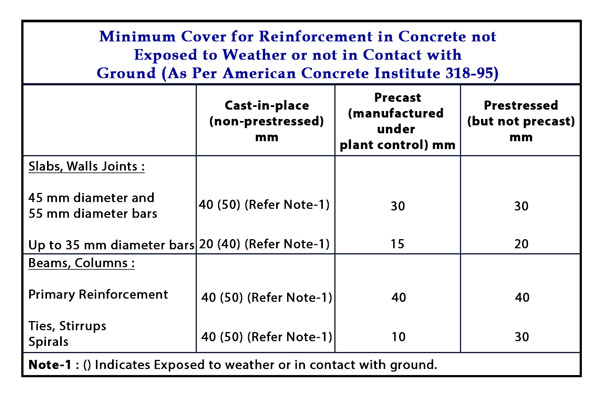
Minimum concrete cover for reinforcement, except for extremely corrosive atmospheres, other severe exposures, or fire protection, shall be as follows.
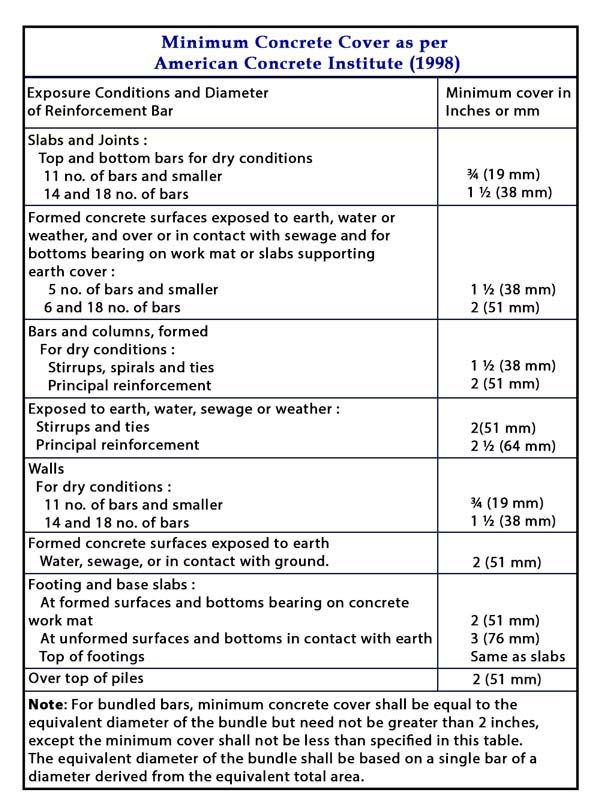
This should bring it to your notice that both the above tables do not consider the concrete strength, minimum cement content or w/c ratio while specifying the cover thickness.
03. Cover as Per Australian Standard
The minimum reinforcement cover as per AS 3600-1988 is as a given in table below.
Minimum reinforcement cover for protection of reinforcement, tendons or ducts from corrosion (as per AS 3600-1988)
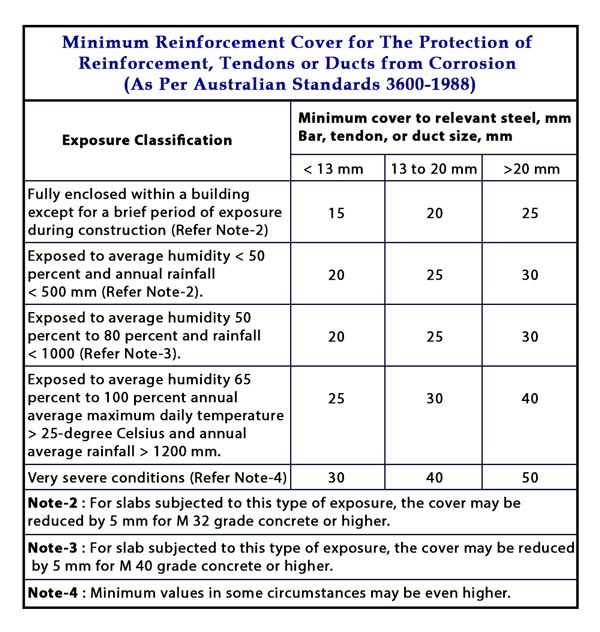
From the above table it is evident that, this standard lay stress on diameter of reinforcement, exposure conditions (rainfall/humidity) and location of the structural member. It reduces the cover requirement of higher grades concrete.
04. Cover as Per British Standard
The BS 8110 (Part I) 1997 specifies the nominal cover based on exposure conditions (mild to most severe), maximum free w/c ratio, minimum cement content and lowest grade of concrete. The table below gives nominal covers to all reinforcement for meeting durability requirements as per BS 8110 (Part I) 1997.

This BS has come up with recommendations which are to be followed in order to procure correct cover. There are also a couple of suggestions mentioned in the same, where primarily it emphasizes on checking the cover by using a cover meter so as to assure proper durability of the reinforced concrete structure. Some important recommendations are listed below.
Spacers & Chairs:
- Spacers and chairs should be used to maintain the specified nominal cover to reinforcement.
- Spacers or chairs should be placed at a maximum spacing of 1 meter.
- Material for spacers should be durable, and it should neither lead to corrosion of reinforcement nor cause spalling of concrete cover.
- Mix used for spacer blocks should be comparable in terms of strength, durability, porosity and appearance to the surrounding concrete.
- Nominal cover should be checked before and during concreting.
- The position of reinforcement in hardened concrete should also be checked with the help of a cover meter.
BS has also specified nominal cover to all reinforcements (including links) to meet specified period of fire resistances. The details are given in below table.
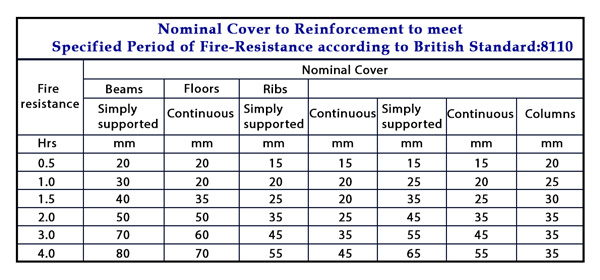
There are various types of cover blocks based on the type of material used
- Wooden cover Blocks
- Steel cover blocks
- PVC Blocks
- Cement Masonry cover blocks
- Aluminum cover Blocks
- Stone cover block
What will happen if Excessive Cover is Provided?
The use of cover more than required is undesirable due to following reason:
- In RCC structure, the size of crack is controlled by the distance of longitudinal bars to the point of section under consideration. The closer a bar is to this point, the smaller is the width of crack. Hence, closely spaced reinforcement bars with smaller cover will cause narrower cracks than compared to the widely spaced bars with larger cover. Therefore, with an increase in concrete cover, the crack width will increase too.
- The weight of the RCC structure increases due to increase in concrete cover. And this is a critical factor in some structure where self-weight is an important design criterion.
- For the same depth of concrete section, the increase in concrete cover results in the reduction of the lever arm of internal resisting force.
To encapsulate the whole thing, the emphasis is on the concrete covering and its importance. The article highlights on the indispensable role and significance of the concrete cover in the construction of any RCC structure. It is apparent from the article that Concrete cover provides protection to reinforcement steel from corrosion and fire. A concrete cover also contributes to the integrity, durability and soundness to the building. If it not done appropriately and satisfactorily, it will obviously reduce the durability of the structure due to onset of corrosion, loss of alkalinity resulting in brittle concrete, reduced elasticity and less resistance in case of fire. The cover, therefore, is essential and must be provided as per codal provisions.