Mostly the modern building structures are made of assorted types of materials. Regardless you are a builder, or an architect, an engineer, or a contractor, it is extremely important to become conversant thoroughly with the nuances of the popularly used building materials.
The knowledge of different types of building materials along with the details of their properties and their various uses for different purposes act as an important resource in the hands of the builders in obtaining economy in cost of construction. In addition to material economy, the accurate use of materials results in better structural strength, aesthetic appearance, and functional efficiency. In this article we are going to discuss one such building material, which is popularly called as “GFRG”. Let us first know what GFRG is.
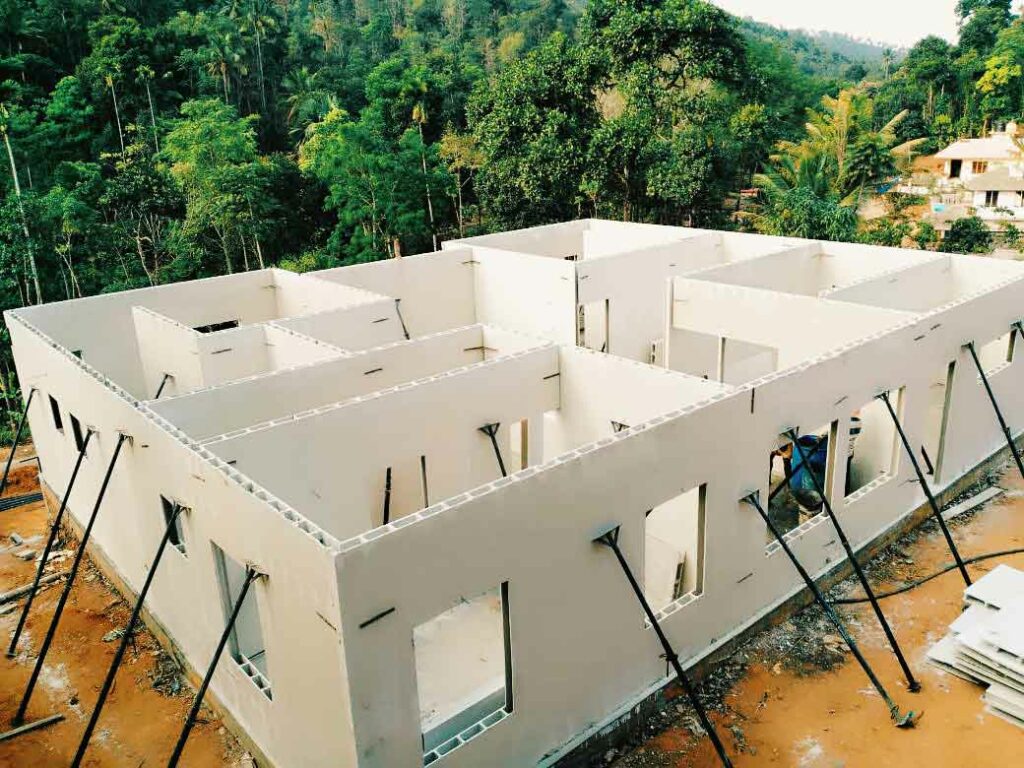
What is GFRG Panel?
GFRG stands for Glass Fibre Reinforced Gypsum. GFRG panels are also known as Rapid walls. These building panels are made-up of gypsum plaster, which is calcined and then later they get reinforced with glass fibres. It was first invented by the GFRG Building System Australia in 1990 for the purpose of mass scale building construction. Presently, these panels have found their application in India and other developing countries as well.
The typical dimension of GFRG Panel is usually 12 m in length, 3 m wide, and 0.124 m in depth. These panels are primarily constitute of gypsum, glass fibre, concrete slurry, and chemicals such as water repellent emulsion.
Currently there are two GFRG panel manufacturing units in India which are:
- FACT-RCF Building Products Ltd., which is located in Kochi (Kerala).
- Rashtriya Chemicals and Fertilizers Limited, located in Mumbai.
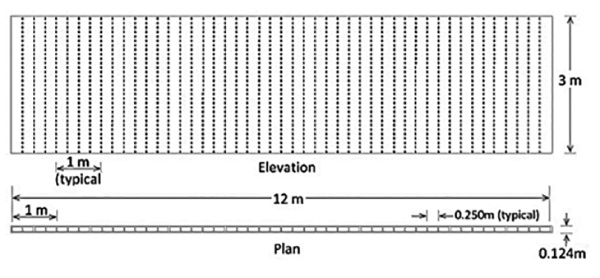
Typical View of a GFRG Panel
Also Read: Types of Gypsum Board | All you Need to Know
Classification of GFRG Panel
Class-1: Water Resistant Grade
Water resistant grade type of GFRG panels are used for the construction of external walls in damp areas where water resistance is of prime importance. Also, this variety of GFRG panel is used in floor or wall formwork for concrete filling.
Class-2: General Grade
General Grade GFRG panels can be used for both structural and non-structural applications in dry areas. These types of panels are mostly not suitable when it comes to the construction of external or internal walls. They are not recommended for the construction of wall or floor formwork as well.
Class-3: Partition Grade
Partition grade GFRG panels are best suitable for the construction of non-structural internal partition walls. This type of GFRG panel is recommended only for the dry areas.
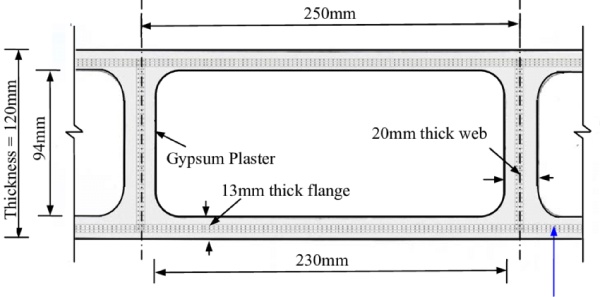
Enlarged View of a Typical Section of GFRG Panel
Applications of GFRG Panel in Building Construction
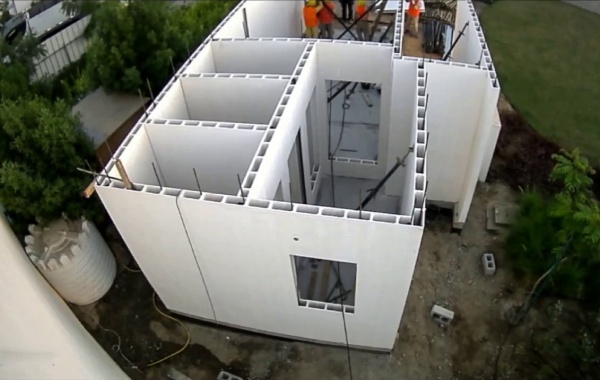
01. For Load Bearing Walls
One of the most common applications of GFRG panels is observed as load bearing structures in the buildings. When the cavities inside the GFRG panels are filled with concrete, the compressive strength of the panels gets enhanced. Additionally, when the reinforcing bars are introduced, the ability of the panel to resist the lateral loads also gets enhanced. Henceforth, using such load bearing structures in the construction are the most suitable option for multistoried buildings.
For single or two-storied building construction, the cavities may be filled with an alternative structural material such as quarry dust mixed with 5% cement. However, the filling protocol is recommended for every third or fourth cavity, and at every joint or an opening location. Preferably, the filling must be done with M20 concrete. Additionally, it shall be reinforced with one 8 mm reinforcing bars.
02. Horizontal Floor and Roof Slabs
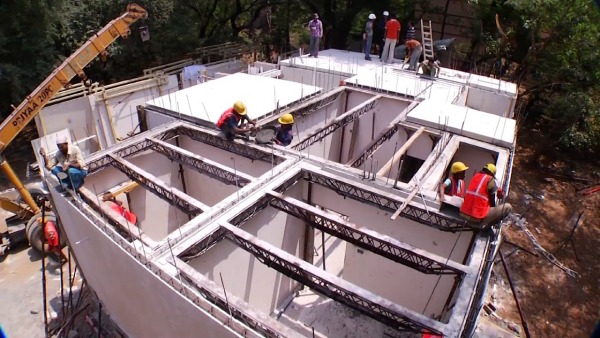
GFRG panels can also be used as intermediate floor or slab in combination with the reinforced concrete structures. The strength of such GFRG slabs can be significantly enhanced by incorporating it with reinforced concrete micro beams. In order to provide micro beams that are embedded, the top flange of the respective cavity is trimmed and removed in a way that the minimum of 25 mm flange remains protruded from both the ends.
GFRG panels for floor and slab are cut to a required size and marked with notations. Firstly, the wall joints, cavities, and the horizontal RCC tie beams are filled with concrete. Thereafter, a wooden plank of width 300 mm to 450 mm is provided to room span between the walls with support wherever the embedded micro beams are present. Finally, roof panels are to be lifted by the crane so that the panel can float perfectly horizontal.
Each of the GFRG roof panel is placed over the wall in such a way that a minimum gap of 40 mm is provided. This is done in order to enable vertical rods to be placed continuously from floor to floor and provide monolithic RCC frame within the rapid wall.
03. Partition Walls
GFRG panels can also be used as partition in-fill walls in single or multi storied buildings. The cavities of GFRG panels can be filled in suitably. Such panels are used as partition walls, whereas these panels can also be used for cladding in industrial buildings or sport facilities. Similarly, they can be used as compound walls or security walls.
Advantages of GFRG Panel Homes
01. Cooler Buildings
Conventional building materials like concrete possess high thermal conductivity and relatively low thermal resistance. The roofs and walls made of the conventional building materials tend to radiate heat inside the building. Henceforth, heavy electrical energy is required in order to maintain indoor comfort level. Additionally, there will be high electric energy consumption for heating the indoor during the winter season.
The GFRG panel offers low thermal conductivity and high thermal resistance in comparison to the conventional building materials. According to ‘Mohd Peter Davis’ (2000 in University Putra Malaysia, Selangor), during the summer season, indoor temperature of Glass Fiber Reinforced Gypsum Panel building gets cooler by 5 to 6 degrees Celsius in comparison to concrete made buildings.
02. Energy Efficient
Low energy consumption at the time of mass production of building material as well as minimal use of recurring energy for operational use is very critical in order to achieve carbon emission reduction. This helps indefinitely to save the environment and to fight global warming simultaneously.
The World Bank has approved GFRG as an eligible material for ‘carbon credits’ under the Kyoto Protocol.
The use of advanced low energy-based technology which is green & cleaner for reprocessing / recycling the raw material is the application of GFRG as GFRG panels consume significantly low level of energy and also it helps to protect the environment. This is the reason mass production GFRG Panel is considered suitable to meet the challenges of providing affordable housing/building for the budget friendly homes.
The United Nations Framework Convention on Climate Change (UNFCC) has also approved the use of GFRG panels as a green material under the Clean Development Mechanism (CDM) protocol.
03. Affordable Quality Housing
The cost of construction with GFRG material is more or less same or maybe slightly on lesser side as compared to the cost of building by the conventional brick homes. The total construction cost of the GFRG-panel homes come down to around Rs. 1700 per square feet which is very economical and pocket friendly. Since greater strength can be achieved with less thicker walls, Carpet area of the building can be increased up to 10%. It is eco-friendly as industrial waste gypsum is used as the constituent ingredient of GFRG. Homes built with GFRG panels are often referred as green buildings.
04. Time Efficient
With GFRG, the time of construction can be minimized greatly. Since the panels are already manufactured, the time consumed during the brick laying and curing can be abruptly eliminated. It saves up to 50% of the total building time. The use of GFRG panels increases the life span of a building. The life span of a conventional home is approximately 40 to 50 years whereas the life span of a house built with GFRG panel is around 80 to 90 years.
Disadvantages of GFRG Panel
- During the construction process, more space is required for the movement of crane.
- Since the design of GFRG panel is complicated, it may make the construction procedure less economical.
- For installing the GFRG panels, highly skilled and experienced labor is required.
- GFRG panels should be handled with great care during the transportation and erection process.
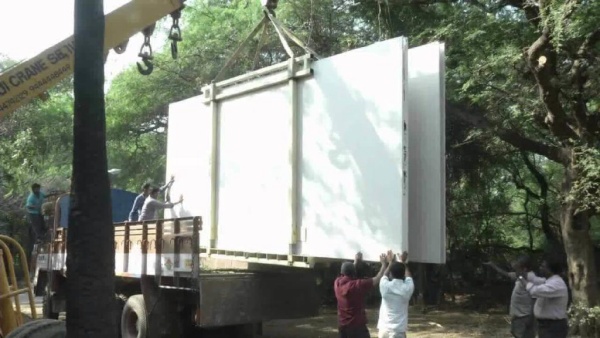
- The cutting of GFRG panels at site requires specific machinery.
- The entire procedure involved the erection and placing of GFRG panels is a little complicated and may difficult to follow.
- GFRG panels cannot be used for the construction of walls with circular or higher curvature.
Mechanical Properties of GFRG Panels
The following mechanical properties of GFRG building panels are determined from the tests conducted on the panels. The mechanical properties are as follows:
- Unit weight: 0.443 kN/m
- Modulus of Elasticity: 7500 N/mm2
- Uni-axial compressive strength: 160k N/m
- Uni-axial tensile strength: 34-37 kN/m
- Ultimate shear strength: 21.6 kN/m
- Water absorption capacity: 3.85 %
- Fire resistance: up to 140 minutes
Performance Requirements of GFRG Panels
01. Appearance
Both the external faces of GFRG panels must be free from all the defects such as ripples, pockmarks, corrugations, stains, cracks, loose corners, or any other defects which may have an adverse effect on the painted surface finishes.
It is necessary that paint has to be applied directly on to the A-side of a GFRG panel without any need for extensive rendering or plastering. The quality of the panel can be monitored by the operation of the final screeding during the manufacturing process.
The appearance requirements on the B-side are usually decided through negotiation between the manufacturer and its client. However, the minimum requirement for the other side is a 3.5mm texture coating or a trowelled-on coating that will cover all the possible defects.
02. Dimension Tolerance
The manufactured dimensional tolerances for a full sized GFRG panel shall satisfy the following:
- Length: ±3mm (Nominal length)
- Height: ±3mm (Nominal height)
- Thickness: +3 to 0 mm (Nominal thickness)
The flatness of the panel shall satisfy the following:
- The maximum local unevenness of protruding or recessing should be less than 1mm on the A side and 3mm on the B side and,
- For the entire curvature of the surface the deviation of any point on the panel face from a 2.5m straight edge shall not surpass k=3mm in any section of the panel and in both the orthogonal directions.
03. Water Content
The water content of panels is usually measured immediately after the drying process (without moisture intake after drying) shall be less than 1% when tested in accordance with Clause 10.4.3. of BMBA PC-3:2011.
04. Panel Weight
The nominal weight of the dried and empty hollow core GFRG panel of thickness 124 mm shall satisfy the following:
- Class 1: 40kg/m2 with a tolerance of ±6 %
- Class 2: 40kg/m2 with a tolerance of ±6 %
- Class 3: 40kg/m2 with a tolerance of ±15 %
05. Water Absorption Rate
The water absorption rate for the GFRG panels of water-resistant grade shall not be more than 5% by weight after 24-hour duration of immersion in water when tested in accordance with the Clause 10.4.5. No test is required for other grades of GFRG panels.
06. Vertical Load Bearing Capacity
When tested according to the Clause 10.4.6, the cross-sectional compression strength of the panel shall satisfy the minimum requirements as given below:
- Minimum compression strength for general or water-resistant grade: 160 kN/m
- Minimum compression strength for partition grade: 90 kN/m
Construction of Houses Using GFRG Panels
01. Excavation and Foundation
Excavation of soil is carried out the same way to lay the foundation. First step is the foundation. The three most commonly used types of foundation are Strip Footing, Isolated footing, and raft footing. Raft footing is generally used for multistoried buildings or in case if the soil is identified as weak. Isolated footing is generally used for small houses.
Once the foundation is laid, the waterproofing of the foundation is carried out by spraying the appropriate chemicals.
02. Placing of the Panels
The casting of reinforced concrete is laid down for the plinth beams. Then the starter bars are fixed inside the concrete casting so that the GFRG panels can be placed. The panels are transported from the manufacturing station to the construction site. They are placed on the starter bars according to the dimensions and the positions assigned to them. Once they are placed, waterproofing is provided for securing the joints.
03. Pouring of Concrete
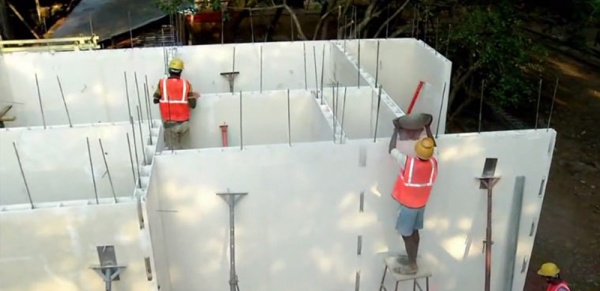
After fixing the GFRG panels, they must be held in place until the concrete mix is poured onto them. The support to these panels is provided by the support bars. Then the concrete mix is filled into each of the cavities of panels from the top.
04. Placing the Slabs
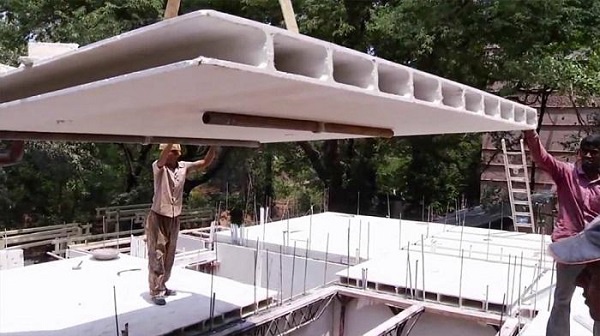
After finishing the walls, the panels are placed on the top as slabs. A reinforcement cage for the embedded beams are provided and concrete screed is provided by pouring concrete mix onto the slab. After concreting the roof slab, finishing and plastering is done to finish the building process. To know more about the construction of GFRG building, watch this video by IIT Madras.
Construction Procedure of GFRG Panel House
Construction Cost of GFRG Panel House
The net cost for a 1000 square feet house built with GFRG panel would be approximately Rs. 17 lakhs. This is a basic standard cost, and it may vary depending on the location, materials, floor plan, and design. At IIT Madras, under the pilot project, the low-cost house of 500 square feet cost was around Rs. 5,75,000. (Both prices at today’s market rates at September-2019).
Manufacturing Process of GFRG Panel
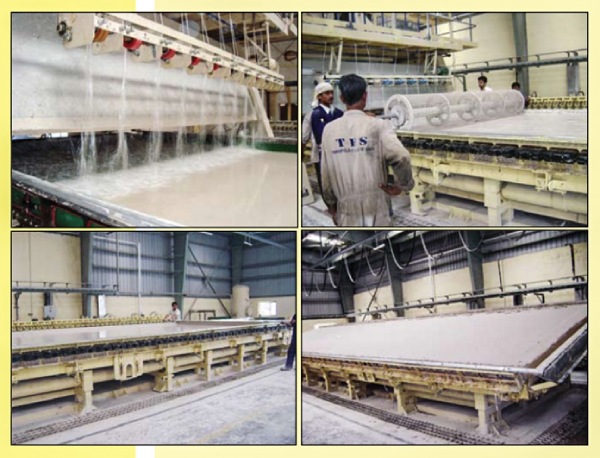
Manufacturing Process of GFRG Panels
The manufacturing process of a GFRG Panel is carried out in a semi-automatic plant by mixing the constituent ingredients together in adequate proportions. The waste product of the fertilizer industry is reprocessed to make gypsum plaster that serves as the raw material for producing the GFRG panels. The manufacturing process is basically carried out in three different and successive stages.
In the first stage, the calcined gypsum and other chemical additives are poured on a special table made for the manufacturing process of the panels. Then the glass fibers are spread evenly on the mix with the help of a screening and rolling process. Once a layer of mix is completed, aluminum plugs are inserted having a gap of 20mm between them. These aluminum plugs are introduced to hollow cavities within the panels. The second layer of mix is then poured on the aluminum plugs along with the cut glass fibers. Tamping is done to form ribs on the hollow panels. In the final stage, the same process as the first stage is repeated to complete the top layer of the panels.
This arrangement is left for setting, which is about 25 minutes. Then the casting table is rotated to reach a vertical position so that the panel can be taken out. It is then set aside for drying by means of a special forklift. The drying is carried out in a dry chamber, where hot air is continuously circulated to dry the panel evenly for approximately 20 minutes.
Once the panels are completely dried, they are cut to desired shapes and dimensions with the help of a computer aided automated process.
Conclusion
According to ‘Meher Prasad’ (Professor of Structural Engineering Division under the Department of Civil Engineering, IIT Madras), manufacturing of GFRG panels from the raw material gypsum, viz., natural gypsum, mineral gypsum, phospho-gypsum or chemical gypsum, with purity more than 90%, entails less energy in comparison to energy-intensive conventional building materials like, brick, concrete, etc. Increased thermal resistance of gypsum reduces the air conditioning load on the buildings: hence, it reduces the demand of operational energy in the GFRG buildings than in the buildings built with conventional building material. Further due to increased carpet area efficiency and less time for construction, ultimately helps in saving of cost.
Must Read:
Plaster of Paris (POP)| Uses, Advantages & Disadvantages
Cavity Wall: Its Purpose, Advantages & Disadvantages
10+ Types of Retaining Walls that can be used for Various Purpose in Construction!
Image Courtesy: Image 1 – rapidhomeskerala, Image 2, Image 3, Image 4, Image 5, Image 6 – Constructiontips, Image 7 – gfrgexpertsindia, Image 8 – industrychronicles, Image 9 – bmtpc
Author Bio
Arfa Falak – My name is Arfa Falak and I have my graduation in BE (civil). I live in Bangalore. I am an aspiring design Engineer.